Introduction
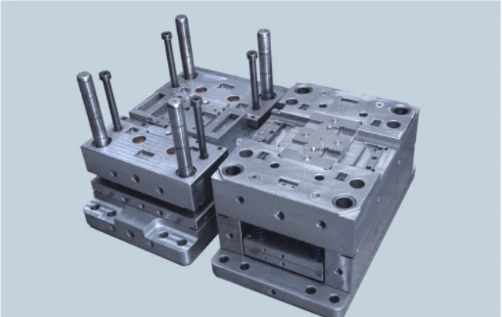
In the world of injection molding, sink marks can be a pesky issue that manufacturers often face. These unsightly depressions on the surface of molded parts not only compromise aesthetics but can also impact functionality and overall product quality. Understanding injection molding sink marks is crucial for anyone involved in the manufacturing process, as it lays the groundwork for effective solutions and preventive measures.
Understanding Injection Molding Sink Marks
Injection molding sink marks occur when there are inconsistencies in material cooling or packing during the injection process. They typically manifest as dimples or depressions on the surface of a finished product, often resulting from uneven shrinkage as the material solidifies. To tackle questions like What causes sink marks in injection molding? it’s essential to consider factors such as material selection, cooling rates, and injection pressure.
The Impact of Sink Marks on Quality
The presence of plastic injection molding sink marks can significantly diminish both aesthetic appeal and functional integrity of parts. Customers may perceive products with visible defects as lower quality, leading to dissatisfaction and potential loss of sales. Therefore, addressing how to get rid of sink marks in injection molding becomes not just a technical challenge but a vital component in maintaining brand reputation.
Why You Should Care About Sink Marks
Ignoring sink marks could lead to more than just visual flaws; they can also affect performance and longevity of molded parts. For businesses aiming for excellence in production, understanding how to prevent sink marks is essential for achieving consistency and reliability in their offerings. Ultimately, investing time into mastering this aspect of manufacturing will pay off by enhancing customer satisfaction and reducing costly rework or returns.
What Causes Sink Marks in Injection Molding?
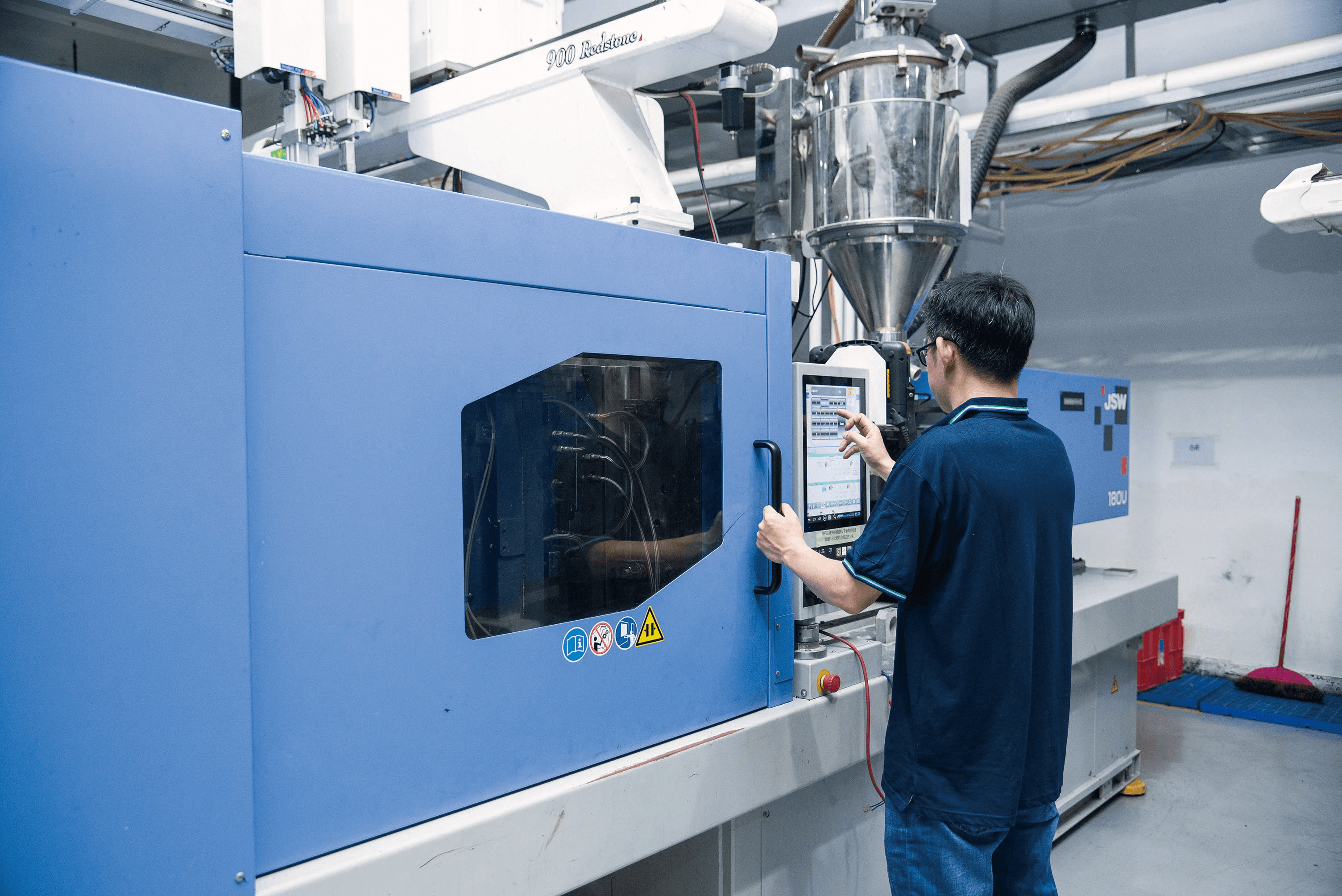
Understanding the causes of injection molding sink marks is essential for anyone involved in the manufacturing process. These pesky defects can mar an otherwise flawless product, leading to dissatisfaction and increased costs. Let’s dive into the primary culprits behind these unwanted blemishes.
Material Selection and Its Implications
The choice of material plays a critical role in determining whether injection molding sink marks will appear on your final product. Different plastics have varying shrinkage rates; for instance, some materials may contract more than others as they cool, leading to noticeable sink marks. Additionally, high-viscosity materials may not fill the mold completely during injection, causing uneven surfaces that contribute to these defects.
Selecting the right material can significantly impact not only the presence of sink marks but also overall product quality and durability. If you’re dealing with persistent plastic injection molding sink marks, it might be time to reassess your material choices. Remember: a little foresight in material selection can save you from hefty repair bills down the line.
Injection Speed and Pressure Factors
The speed at which plastic is injected into a mold and the pressure applied during this process are crucial factors that influence the formation of sink marks. High injection speeds can lead to turbulence within the melt flow, causing incomplete filling of intricate mold designs, which often results in unsightly surface imperfections. Conversely, low speeds might allow for better filling but could result in longer cycle times and increased production costs.
Pressure settings also play a pivotal role; inadequate pressure can prevent proper packing of material within the mold cavity, leaving voids that manifest as sink marks post-cooling. To mitigate these issues effectively, manufacturers must find a balance between speed and pressure while considering how these parameters affect cooling rates as well—an intricate dance that requires careful monitoring. If you're asking yourself What causes sink marks in injection molding?, look no further than your setup's speed and pressure settings.
Cooling Rate and Its Role
Cooling rate is another significant factor contributing to injection molding sink marks; it directly impacts how evenly materials solidify inside molds. Rapid cooling may lead to uneven contraction rates across different areas of a part—thicker sections tend to cool slower than thinner ones—and this disparity can create visible depressions or distortions on the surface once ejected from the mold.
Furthermore, if cooling occurs too slowly, excessive heat retention can cause warping or other defects alongside those pesky sink marks—definitely not what you want after investing time and resources into production! To avoid such issues, optimizing cooling channels within molds is essential for achieving consistent temperatures throughout each part during solidification.
How to Get Rid of Sink Marks in Injection Molding

Effective Post-Molding Techniques
When it comes to tackling injection molding sink marks, effective post-molding techniques can make all the difference. One common method is to employ heat treatment, which can help redistribute material and smooth out those unsightly depressions. Another approach is sanding or polishing the affected areas; while it may not eliminate the sink marks entirely, it can significantly improve the overall appearance of your plastic injection molding products.
Additionally, using fillers or surface coatings can also help mask minor sink marks and enhance aesthetic appeal. These techniques not only contribute to improving product quality but also extend the lifecycle of your molded parts by addressing defects early on. Remember that proactive measures are key; knowing how to get rid of sink marks in injection molding will save you time and resources down the line.
Utilizing Baoyuan's Expertise for Solutions
Navigating the world of injection molding sink marks can be daunting, but that's where Baoyuan shines! With years of experience under their belt, Baoyuan specializes in providing tailored solutions for reducing and eliminating sink marks effectively. Their team understands what causes sink marks in injection molding and offers insights into optimizing your processes for better results.
Baoyuan’s expertise extends beyond just identifying issues; they provide comprehensive support from material selection to mold design adjustments that directly address potential problems before they arise. By collaborating with professionals who know how to prevent sink marks effectively, you’ll be able to produce high-quality products consistently without compromising on aesthetics or functionality.
Repairing Surface Defects: Your Options
If you've already encountered those frustrating plastic injection molding sink marks and need a remedy, there are several repair options at your disposal. For minor defects, applying a high-quality filler or putty may suffice; once cured and sanded down smoothly, this method can yield impressive results without extensive rework.
For more severe cases where traditional methods fall short, consider utilizing advanced techniques like laser engraving or machining—these methods allow for precise corrections that restore surfaces back to their original glory while minimizing waste material. Understanding what is the difference between shrinkage and sink mark will further guide you in choosing appropriate repair strategies tailored specifically for each defect type.
How to Prevent Sink Marks?
Preventing injection molding sink marks is a crucial step in ensuring the quality and aesthetic appeal of molded parts. By understanding what causes sink marks in injection molding, manufacturers can implement effective strategies to minimize their occurrence. This section will explore design considerations, material selection, and process parameter adjustments that can help eliminate these pesky imperfections.
Design Considerations for Mold Creation
Another important aspect of mold design is ensuring adequate venting. Properly placed vents allow trapped air to escape during the injection process, reducing pressure build-up that could exacerbate sink mark formation. Moreover, considering draft angles in your designs ensures easier part removal from molds without compromising surface quality.
Lastly, taking into account the overall geometry of the part is vital; complex shapes may require more intricate molds that facilitate consistent filling and cooling rates. By addressing these design considerations upfront, you set the stage for minimizing injection molding sink marks effectively.
Selecting the Right Materials
Material selection is another key factor in tackling how to prevent sink marks in injection molding. Different plastics have varying shrinkage rates; choosing materials with lower shrinkage characteristics can significantly reduce the likelihood of sink marks appearing on your final product. For instance, engineering-grade thermoplastics often provide better performance compared to standard commodity resins when it comes to maintaining surface quality.
In addition to shrinkage properties, consider using additives or fillers that enhance dimensional stability during cooling processes. These materials can help mitigate shrinkage differentials that lead to unsightly defects like sink marks on molded parts. It’s also essential to evaluate material flow characteristics; those with better flowability tend to fill molds more uniformly and reduce pressure variations throughout the cavity.
Finally, always conduct thorough testing before full-scale production runs using your chosen materials. This practice helps ensure compatibility with your specific application while allowing you to identify any potential issues related to plastic injection molding sink marks early on.
Process Parameter Adjustments
Fine-tuning process parameters is crucial when aiming for effective injection molding sink marks removal and prevention strategies alike. Start by adjusting injection speed and pressure—higher speeds may improve filling but could also introduce turbulence that leads to defects if not managed properly. Striking a balance between sufficient pressure for complete mold filling without causing excess shear stress will yield smoother surfaces free from unwanted blemishes.
Cooling rate adjustments are equally important; too rapid cooling can cause excessive contraction leading directly to visible sink marks on finished products. Gradually controlling cooling rates allows for uniform solidification of materials while minimizing internal stresses within parts—an essential step toward achieving higher quality outputs without defects.
Finally, regularly monitoring temperature settings throughout both heating and cooling phases ensures optimal processing conditions are maintained consistently across production runs. Employing data logging tools or real-time monitoring systems provides valuable insights into how well parameters are performing against desired outcomes regarding prevention of plastic injection molding sink marks.
What Is the Difference Between Shrinkage and Sink Marks?
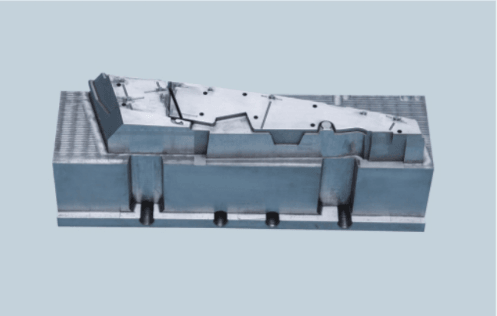
In the world of injection molding, it's crucial to understand the nuances between shrinkage and sink marks. Both phenomena can affect the quality of molded parts, but they stem from different causes and manifest in distinct ways. Recognizing these differences is essential for effective problem-solving and ensuring high-quality production.
Defining Shrinkage in Injection Molding
Shrinkage in injection molding refers to the reduction in size that occurs as a plastic part cools down after being injected into a mold. This process is largely influenced by material properties, as different plastics have varying shrink rates during cooling. While some degree of shrinkage is expected, excessive shrinkage can lead to dimensional inaccuracies that compromise part functionality.
Identifying Sink Marks Specifically
Sink marks are surface depressions that appear on molded parts due to uneven cooling or insufficient material flow during injection molding. These imperfections often occur in thicker sections of a part where the interior cools more slowly than the outer surface, leading to a noticeable indentation. Unlike general shrinkage, which affects overall dimensions, sink marks are localized defects that can detract from both aesthetics and performance.
Importance of Distinguishing Both
Understanding what sets apart shrinkage from sink marks is vital for manufacturers aiming to optimize their processes and minimize defects like injection molding sink marks. Misidentifying these issues could lead to ineffective solutions; for instance, addressing sink marks with techniques designed for managing general shrinkage may yield unsatisfactory results. By accurately distinguishing between these two phenomena—shrinkage affecting overall size and sink marks impacting surface quality—manufacturers can implement targeted strategies for prevention and remediation.
The Role of Quality Control in Managing Sink Marks
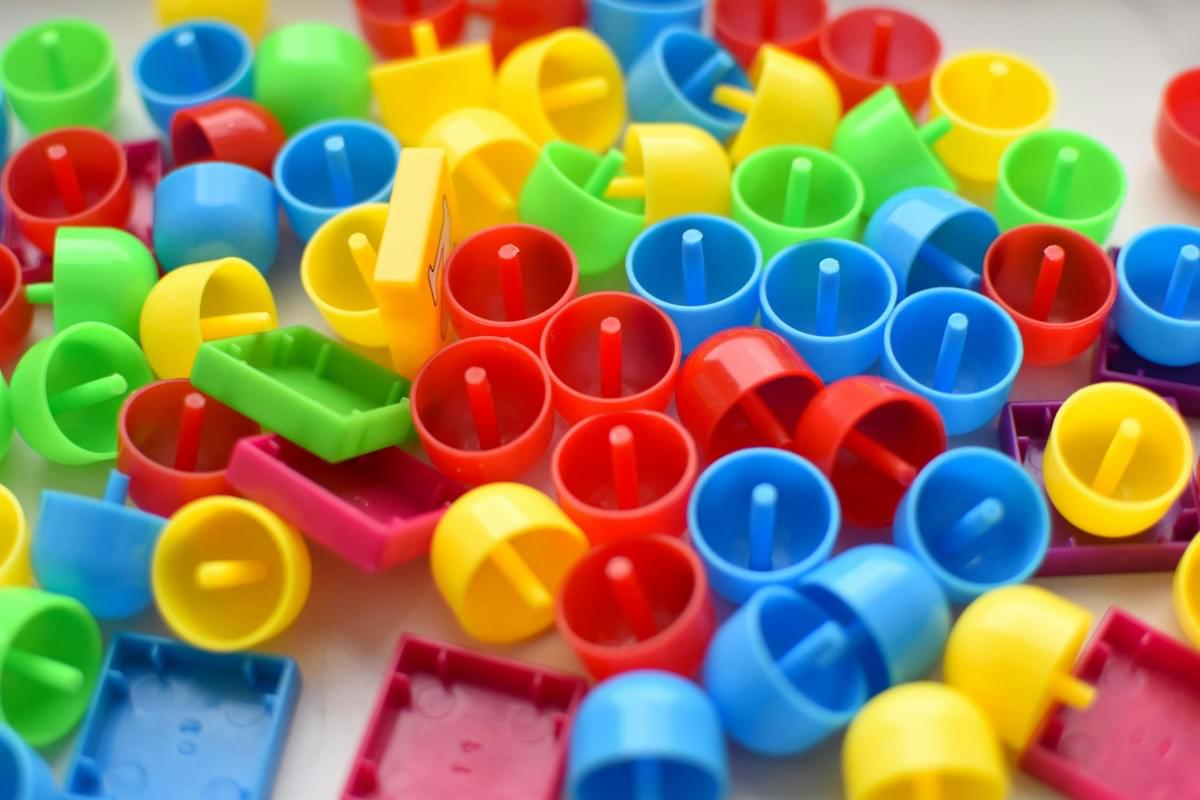
Inspection Techniques to Identify Issues
To effectively manage injection molding sink marks, it’s crucial to have robust inspection techniques in place. Visual inspections are often the first line of defense; however, they may not catch every subtle defect. Advanced methods such as ultrasonic testing or 3D scanning can provide deeper insights into surface integrity and help identify what causes sink marks in injection molding.
Regular audits should also include dimensional checks and surface roughness measurements to pinpoint deviations that might indicate potential sink marks. Employing statistical process control (SPC) can further enhance detection capabilities by monitoring variations in production processes over time. By utilizing these inspection techniques, manufacturers can quickly address plastic injection molding sink marks before they impact product quality.
Continuous Improvement Practices
Continuous improvement practices are essential for refining processes related to managing injection molding sink marks effectively. Implementing methodologies like Lean manufacturing or Six Sigma can help streamline operations and reduce waste associated with defects such as sink marks. Regular training sessions for staff on how to prevent sink marks through better material handling and operational techniques will empower teams to take ownership of quality outcomes.
Data-driven decision-making plays a pivotal role in identifying trends related to what causes sink marks in injection molding, allowing organizations to adjust processes proactively rather than reactively. Additionally, fostering a culture where feedback is encouraged ensures that everyone is on board with striving for excellence in minimizing defects like plastic injection molding sink marks. This proactive approach leads not only to improved product consistency but also enhances overall operational efficiency.
Baoyuan's Approach to Quality Assurance
Baoyuan takes a comprehensive approach toward quality assurance that specifically addresses the challenges posed by injection molding sink marks removal and prevention strategies alike. Their commitment begins with rigorous supplier evaluations ensuring that only high-quality materials are used—this directly impacts how to get rid of sink marks in injection molding effectively from the start of the process. Furthermore, Baoyuan invests heavily in state-of-the-art technology that allows for real-time monitoring during production runs.
The company employs a dedicated team focused on continuous improvement practices aimed at minimizing defects while maximizing output efficiency—a win-win scenario for both Baoyuan and its clients! Regular training programs ensure that all employees are well-versed in identifying issues early on while understanding what is the difference between shrinkage and sink mark occurrences during production cycles. With this holistic strategy, Baoyuan stands out as an industry leader committed not only to excellence but also innovation when dealing with common challenges like plastic injection molding sink marks.
Conclusion
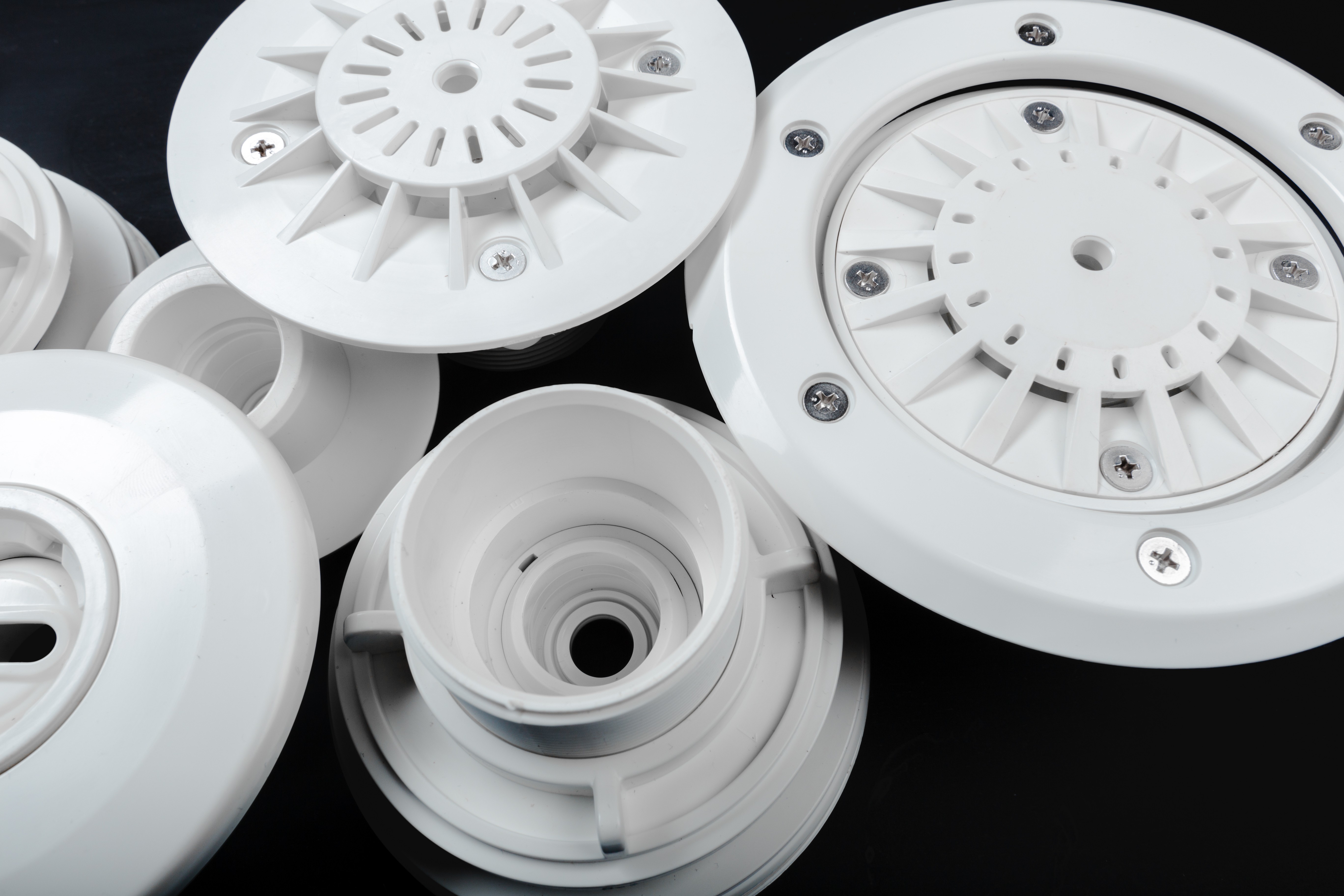
In the world of plastic injection molding, managing injection molding sink marks is crucial for producing high-quality parts. Understanding what causes sink marks in injection molding and how to effectively address them can greatly enhance product integrity and customer satisfaction. By implementing best practices and leveraging modern technologies, manufacturers can significantly reduce the occurrence of these pesky imperfections.
Best Practices for Sink Marks Management
To combat injection molding sink marks effectively, adopting best practices is essential. Start by ensuring that your design considers material flow, thickness, and cooling patterns to minimize potential sink marks. Additionally, regular inspections and adjustments during the manufacturing process can help identify issues early on, allowing for timely interventions that prevent further complications.
Implementing consistent quality control measures is another critical step in managing plastic injection molding sink marks. This includes using precise monitoring tools to track parameters like temperature and pressure throughout the injection cycle. By staying proactive and refining processes continuously, manufacturers can significantly enhance their ability to avoid or reduce sink mark occurrences.
Leveraging Technology and Expertise
In today's fast-paced manufacturing environment, leveraging technology is key to tackling challenges like sink marks in injection molding. Advanced simulation software allows engineers to visualize potential issues before production begins, providing insights into how design changes might affect the final product's appearance. Furthermore, utilizing data analytics can help identify trends associated with sink mark occurrences over time.
Collaborating with industry experts also plays a vital role in overcoming challenges related to injection molding sink marks removal. Companies like Baoyuan offer specialized knowledge in optimizing processes tailored specifically to your needs—from material selection to machine settings—ensuring you have the best shot at achieving flawless results. Their expertise allows you not only to address existing problems but also to prevent future ones from arising.
Final Thoughts on Injection Molding Challenges
Navigating the complexities of plastic injection molding requires a keen understanding of various factors influencing product quality—including distinguishing between shrinkage and sink mark phenomena effectively. Recognizing what causes sink marks in injection molding enables manufacturers to implement targeted solutions while also fostering an environment conducive to continuous improvement.
As we move forward into an era where precision engineering becomes increasingly vital, embracing innovative strategies will be paramount for success in managing challenges like these. Remember that knowledge is power; by staying informed about how to get rid of sink marks in injection molding and preventing them from occurring altogether, you'll be well-equipped for whatever comes next in this dynamic industry.