Introduction
In the world of manufacturing, insert injection molding has emerged as a game-changer, seamlessly combining the strengths of plastic and metal components into one cohesive product. This innovative process allows for the creation of complex designs that are both functional and aesthetically pleasing, making it a popular choice across various industries. As we delve deeper into the intricacies of this molding technique, it's essential to understand not just how it works but also why it has become a preferred option for many manufacturers.
Understanding Insert Molding
Insert molding is a specialized form of injection molding where pre-formed components—often made from metal—are placed into a mold before plastic is injected around them. This method results in strong, durable products that benefit from the unique properties of both materials, creating what we call injection molded plastic components. By understanding this process, manufacturers can leverage its advantages to produce high-quality products that meet demanding performance standards.
Why Choose Insert Injection Molding
Choosing insert injection molding over traditional methods can significantly enhance production efficiency and product quality. The ability to integrate multiple materials in one step reduces assembly time and labor costs while ensuring superior bonding between parts. Moreover, with advancements in mold design and technology, manufacturers can achieve intricate shapes and functionalities that were once deemed impossible with standard plastic for molding techniques.
Key Benefits of Insert Molding
The benefits of insert molding extend far beyond mere convenience; they encompass durability, cost-effectiveness, and design flexibility. Products created through this process often exhibit enhanced longevity due to the robust combination of materials used in their construction. Additionally, because injection moldable plastics allow for complex designs without compromising on strength or integrity, companies find themselves better equipped to meet evolving market demands while keeping production costs manageable.
The Insert Molding Process
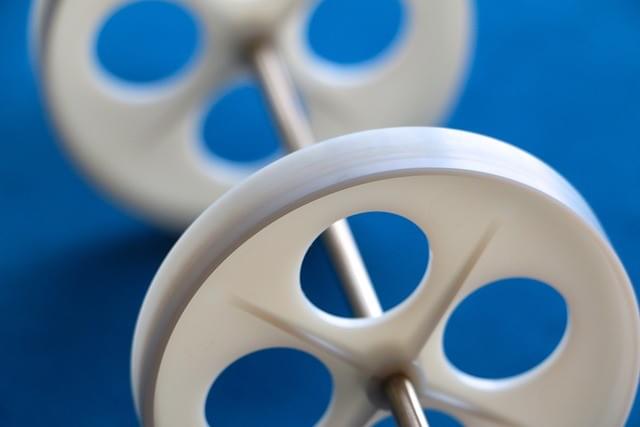
Insert injection molding is a fascinating technique that combines the benefits of traditional injection molding with the added functionality of embedding components within molded plastic parts. This process allows for the creation of complex, multi-functional parts in a single step, streamlining production and enhancing product performance. Understanding the steps involved, the materials used, and the machinery required can help businesses make informed decisions about utilizing insert molding.
Steps in Insert Injection Molding
The insert injection molding process begins with designing a mold that accommodates both the plastic component and any inserts to be embedded. Once the mold is created, it undergoes several stages: first, the inserts are placed into their designated positions within the mold cavity. Next, molten plastic is injected into the mold under high pressure, enveloping and bonding with these inserts to form a cohesive unit when cooled.
After cooling, the molded part is ejected from the mold cavity as an integrated piece featuring both plastic and embedded components. This streamlined process significantly reduces assembly time and potential errors associated with separate manufacturing steps. By mastering these steps in the injection molding process, manufacturers can produce high-quality injection molded plastic components that meet various industry standards.
Materials Used in Insert Molding
Common choices include thermoplastics like ABS (Acrylonitrile Butadiene Styrene), polycarbonate, nylon, and polypropylene due to their excellent mechanical properties and resistance to impact or heat. Each material offers unique benefits tailored to specific applications while ensuring compatibility with various insert types.
Moreover, selecting appropriate materials for both inserts and molds is crucial for achieving optimal performance in finished products. For instance, metal inserts may require different considerations compared to plastic ones regarding thermal expansion or adhesion properties during the injection molding process. Ultimately, understanding which plastics work best for your project will lead to more effective use of resources while enhancing product quality.
Common Machinery for the Process
The machinery used in insert injection molding plays a pivotal role in determining efficiency and precision during production runs. Standard equipment includes an injection molding machine equipped with specialized features such as heated barrels for melting plastics and precise control systems for monitoring pressure and temperature throughout each cycle. Additionally, custom molds are often fabricated from durable metals like steel or aluminum to withstand repeated use over time.
Automation has also made significant strides within this field; many manufacturers now incorporate robotic arms or automated loaders into their operations to streamline handling of inserts before they enter molds—reducing labor costs while increasing consistency across production batches. Investing in advanced technology not only enhances productivity but also ensures that every aspect of producing quality molded components aligns seamlessly with modern manufacturing standards.
Considerations Before Choosing Insert Molding
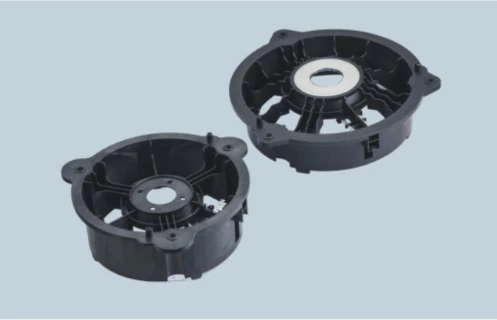
When considering insert molding, several factors come into play that can significantly influence the outcome of your project. Understanding these elements ensures that you select the best approach for your specific needs. From mold design to quality control measures, each consideration plays a vital role in the success of the insert injection molding process.
Factors Influencing Mold Design
The design of the mold is paramount in the insert injection molding process and is influenced by various factors, including part geometry and material selection. The complexity of the injection molded plastic components often dictates how intricate or straightforward your mold needs to be. Additionally, considerations such as cooling times and ejection mechanisms can affect both efficiency and product quality.
Choosing suitable plastic for molding is another critical aspect; different materials have unique properties that may require specialized mold designs. For instance, thermoplastics might necessitate different cooling channels than thermosets due to their varying thermal properties. Ultimately, a well-thought-out mold design can enhance production efficiency while ensuring high-quality end products.
Cost Implications of Insert Molding
Cost is always a crucial factor when deciding on manufacturing methods like insert injection molding. The initial investment in mold creation can be substantial but should be weighed against long-term production costs and efficiencies gained through automation and precision in manufacturing processes. Moreover, utilizing injection moldable plastics effectively can lead to significant savings over time as they offer durability and reduced waste during production.
Another cost consideration revolves around material selection; some plastics may have higher upfront costs but provide better performance or longevity in applications that justify their price tag. It's essential to conduct a thorough cost analysis before committing to an insert molding project to ensure it aligns with your budgetary constraints without compromising quality or performance standards.
Quality Control Measures
Implementing stringent testing protocols throughout the injection molding process helps identify defects early on, minimizing waste and rework costs associated with faulty products. Regular inspections at various stages—from raw material evaluation to final product testing—are crucial for maintaining high standards.
Additionally, leveraging technology such as automated inspection systems can help streamline quality assurance efforts by providing real-time data on product consistency and compliance with specifications. This proactive approach not only enhances overall product reliability but also builds trust with customers who expect nothing less than excellence from their suppliers of injection molded plastic components.
Applications of Insert Molding
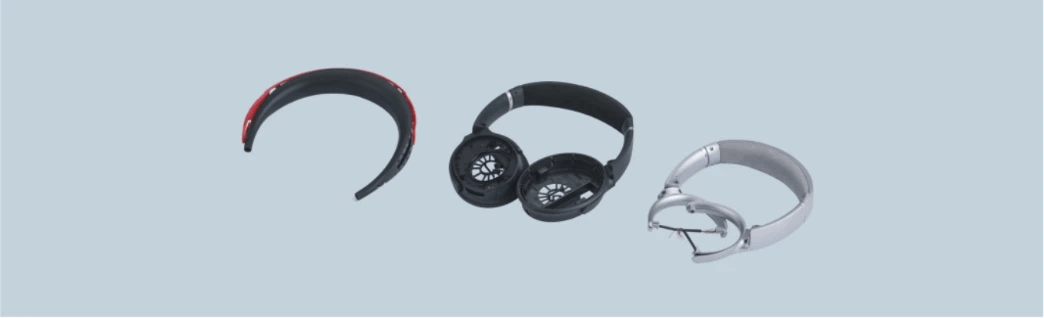
Insert injection molding is a versatile manufacturing technique that finds applications across various industries. From creating robust industrial components to designing consumer products, the benefits of this process are vast. In this section, we will explore the diverse applications of insert molding and highlight its significance in modern manufacturing.
Industrial Uses of Molding
In the industrial sector, insert injection molding plays a crucial role in producing reliable and durable components. Industries such as electronics, aerospace, and medical devices utilize injection molded plastic components for their ability to withstand harsh environments while maintaining precision. The versatility of mold plastic injection allows for the integration of metal parts into plastic assemblies, enhancing functionality and reducing assembly time.
Moreover, the efficiency of the injection molding process ensures that large quantities can be produced quickly without compromising quality. This is particularly important for industries requiring high-volume production runs where consistency is key. By utilizing injection moldable plastics with superior mechanical properties, manufacturers can achieve both performance and longevity in their products.
Consumer Products Made with Insert Molding
Everyday items like kitchen utensils, electronic gadgets, and sporting equipment often incorporate insert molded components that enhance usability and aesthetics. For instance, ergonomic handles on tools or appliances frequently use this technique to combine comfort with strength through innovative design.
The flexibility offered by injection molded plastic allows designers to create complex shapes that would be challenging using traditional manufacturing methods. This design freedom not only enhances product appeal but also reduces material waste during production—a win-win for manufacturers focused on sustainability! As consumers increasingly demand high-quality products at competitive prices, the use of insert molding continues to grow in popularity among manufacturers aiming to meet these expectations.
Automotive Industry Innovations
The automotive industry has embraced insert injection molding as a game-changer for developing lightweight yet durable parts that improve vehicle efficiency and performance. With rising fuel costs and environmental concerns driving innovation, car manufacturers turn to advanced materials made through plastic for molding techniques like insert molding. This approach enables them to create intricate designs while maintaining structural integrity.
From dashboard components to exterior trim pieces, many automotive parts benefit from the precision offered by the injection molding process—resulting in improved fitment and reduced assembly time on production lines. Furthermore, integrating metal inserts into these molded parts enhances strength without adding significant weight—crucial factors when striving for better fuel economy! As electric vehicles gain traction globally, expect even more innovations stemming from insert injection molding as engineers seek ways to optimize performance while minimizing environmental impact.
Advantages of Using Injection Moldable Plastics
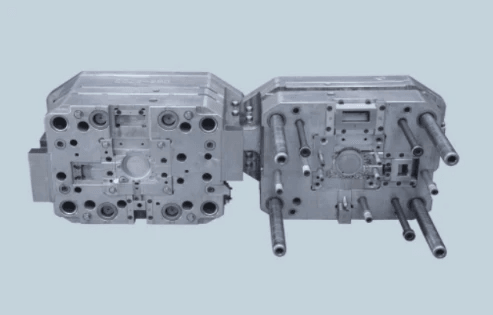
Longevity and Durability
One of the standout features of injection moldable plastics is their impressive longevity and durability. These materials are designed to withstand harsh conditions, making them ideal for various applications—from industrial components to consumer products. With insert molding, you not only get a robust final product but also reduce the risk of wear and tear over time, ensuring your investment stands the test of time.
Moreover, injection molded plastic components can be engineered to resist impacts, chemicals, and extreme temperatures. This resilience means fewer replacements over the lifespan of your product, leading to significant savings in maintenance costs. So when you choose plastic for molding through insert injection molding techniques, you're opting for long-lasting solutions that keep on giving.
Design Flexibility and Complexity
Insert injection molding shines brightly when it comes to design flexibility and complexity. The beauty of using injection moldable plastics lies in their ability to take on intricate shapes and detailed designs that might be challenging with other manufacturing methods. This versatility allows designers to innovate freely without being limited by material constraints.
Additionally, advancements in the injection molding process have made it easier than ever to create complex geometries while maintaining high precision levels. Whether you're looking at multi-material designs or integrating additional components into a single piece through insert molding techniques, the possibilities are virtually limitless! The result? Unique products that stand out in competitive markets.
Cost-Effectiveness for Production
Cost-effectiveness is often at the forefront of any production decision—and rightly so! When considering mold plastic injection processes like insert molding, manufacturers can achieve high-volume production with minimal waste and lower labor costs compared to traditional methods. This efficiency translates into significant savings that can boost your bottom line.
Moreover, once the initial investment in molds is made—often offset by bulk production capabilities—the ongoing costs per unit drop dramatically as more items are produced from each cycle. In essence, choosing injection molded plastic components means investing smartly for long-term gains rather than short-lived solutions that may lead you back to square one financially!
In conclusion, whether you're focused on durability or looking for design innovation at an economical price point—insert injection molding with its array of quality plastics has got your back!
Collaborating with Experts in the Field
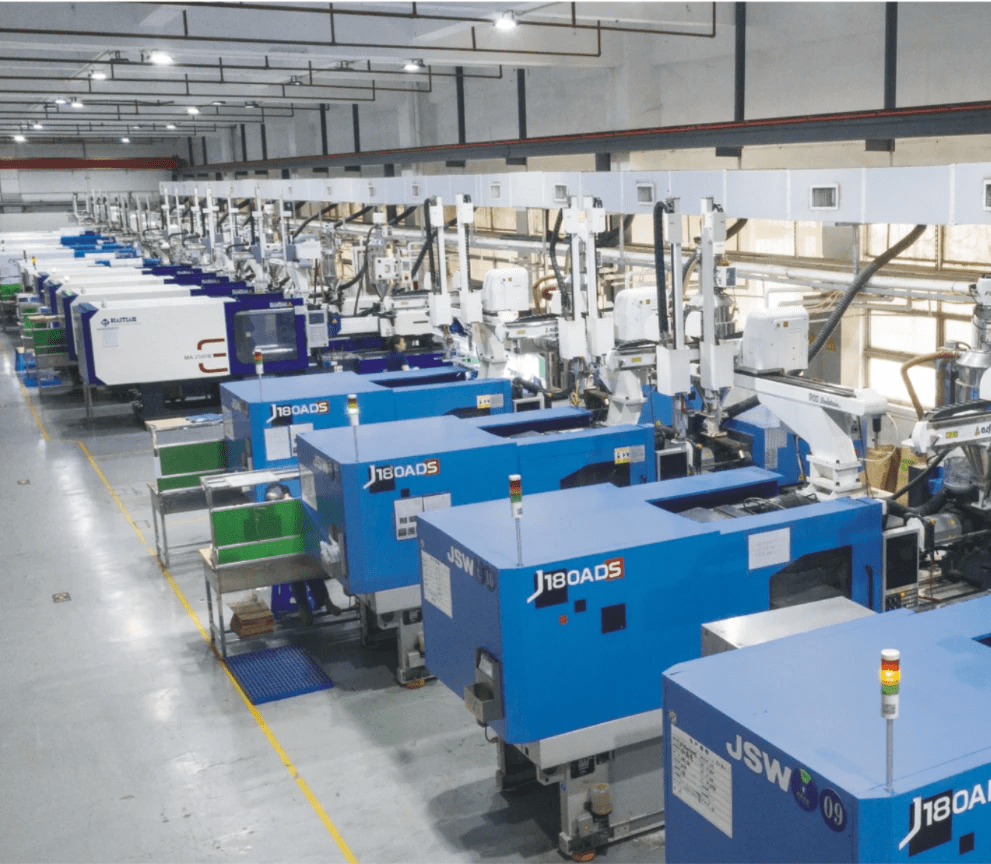
In the world of insert injection molding, collaboration with seasoned experts can significantly enhance the quality and efficiency of the process. Companies like Baoyuan have established themselves as leaders in this field, providing invaluable insights and support throughout the entire injection molding process. By leveraging their expertise, businesses can optimize their use of injection moldable plastics and achieve superior results.
Baoyuan's Role in Insert Molding
Baoyuan plays a pivotal role in advancing insert molding technologies, offering comprehensive solutions that cater to various industrial needs. Their state-of-the-art facilities are equipped with advanced machinery designed specifically for mold plastic injection, ensuring precision and reliability in producing injection molded plastic components. With a commitment to innovation, Baoyuan helps clients navigate the complexities of the insert molding process, ultimately enhancing product quality and reducing time-to-market.
Importance of Skilled Personnel
The success of any insert injection molding project hinges on having skilled personnel who understand both the technical aspects and creative opportunities presented by injection molded plastics. Experienced professionals bring a wealth of knowledge about material properties, mold design intricacies, and production techniques that can make or break a project. Investing in skilled workers not only ensures high-quality outcomes but also fosters an environment where innovative ideas can flourish.
Technology and Software in Molding Design
In today's fast-paced manufacturing landscape, technology plays an essential role in optimizing the design phase of plastic for molding projects. Advanced software tools enable engineers to simulate various scenarios within the injection molding process, allowing for precise adjustments before production begins. These technological advancements not only streamline workflows but also enhance collaboration among team members—ensuring everyone is on board when it comes to creating top-notch injection molded plastic components.
Conclusion
As we wrap up our exploration of insert injection molding, it's clear that this innovative process is poised for a bright future. With advancements in technology and materials, the potential applications for injection molded plastic components are expanding rapidly. The combination of efficiency and versatility makes insert molding an attractive option for various industries.
The Future of Insert Molding
The future of insert injection molding looks promising, driven by continuous innovations in mold design and material science. As manufacturers seek to reduce production costs while enhancing product quality, the use of advanced injection moldable plastics will become increasingly prevalent. Additionally, sustainability initiatives will likely push for more eco-friendly plastic options in the injection molding process, paving the way for greener practices.
Tips for Successful Insert Molding Projects
To ensure successful insert molding projects, meticulous planning is essential from the outset. First and foremost, selecting the right plastic for molding is crucial; it should align with your product's functional requirements and environmental considerations. Collaboration with skilled personnel who understand both the technical aspects and market demands can significantly enhance outcomes—after all, expertise in handling complex designs often leads to superior results in producing high-quality injection molded plastic components.
Final Thoughts on Injection Molding Benefits
In summary, the benefits of insert injection molding are hard to ignore: it offers durability, design flexibility, and cost-effectiveness that few other manufacturing processes can match. Whether you’re producing intricate automotive parts or everyday consumer products, this method stands out as a reliable choice. Embracing the advantages of mold plastic injection not only streamlines production but also opens doors to innovative designs that meet evolving market needs.