Introduction
In the realm of manufacturing, polymer injection molding stands out as a transformative process that shapes the future of product design and production. Among various materials used in this method, polypropylene has gained significant traction due to its unique properties and versatility. Understanding the intricacies of injection molding, especially with polypropylene, is crucial for engineers and manufacturers aiming to optimize their production processes.
Understanding Polypropylene in Injection Molding
Polypropylene is a thermoplastic polymer widely utilized in injection molding due to its excellent balance of strength, flexibility, and chemical resistance. This material can be molded into complex shapes using an injection molding machine, making it ideal for a variety of applications. The adaptability of polypropylene allows for innovations such as over molding and multi-material designs that enhance product functionality.
The Significance of Polymer Injection Molding
The significance of polymer injection molding cannot be overstated; it revolutionizes how products are manufactured by enabling mass production with remarkable precision. This process not only reduces waste but also minimizes production time, leading to cost-effective solutions for manufacturers. With advancements in injection molding tooling and technology, industries can produce high-quality parts that meet stringent specifications while maintaining efficiency.
Applications of Injection Molding in Industry
Injection molding finds applications across diverse industries including automotive, consumer goods, medical devices, and packaging. The versatility offered by different injection molding materials—especially polypropylene—allows manufacturers to create everything from durable automotive components to intricate medical devices efficiently. As the demand for customized solutions grows, the role of advanced techniques like over molding becomes increasingly vital in addressing specific industry needs.
What is Polypropylene?
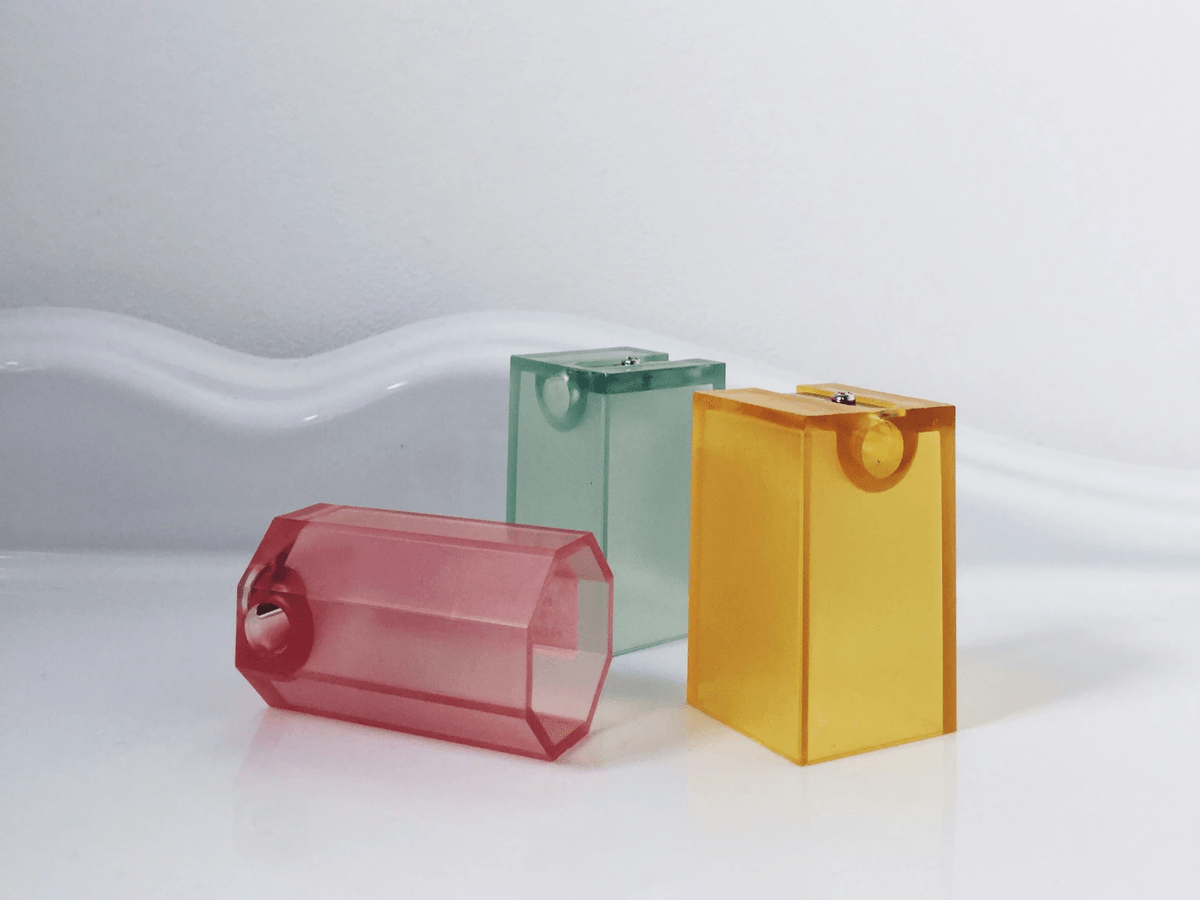
Polypropylene, often abbreviated as PP, is a thermoplastic polymer widely used in various industries due to its versatile properties. This polymer is known for its excellent chemical resistance, low density, and high tensile strength, making it ideal for injection molding applications. As a key player in the polymer injection molding arena, polypropylene's adaptability allows it to be molded into intricate shapes and designs with ease.
Characteristics of Polypropylene
Polypropylene boasts several characteristics that make it an attractive choice for manufacturers engaging in injection molding. It has a high melting point compared to other common thermoplastics, which enables it to withstand elevated temperatures without deforming. Additionally, its low moisture absorption rate ensures that products made from polypropylene maintain their integrity over time, even in humid environments.
Another notable characteristic of polypropylene is its excellent fatigue resistance and flexibility. This means that items produced through injection molding can endure repetitive bending or flexing without breaking down easily. Furthermore, the material can be easily colored and finished during the injection molding process, allowing for creative designs and branding opportunities.
Advantages of Using Polypropylene
Using polypropylene in polymer injection molding comes with numerous advantages that benefit manufacturers and end-users alike. One significant advantage is its cost-effectiveness; polypropylene is generally less expensive than many other plastics while still providing exceptional performance characteristics. This affordability makes it an appealing option for large-scale production runs where maintaining budgetary constraints is critical.
Another advantage lies in its recyclability; polypropylene can be recycled multiple times without significant degradation of its properties. This feature aligns well with growing sustainability trends within the manufacturing industry as companies increasingly seek eco-friendly materials and processes. Moreover, products made from polypropylene exhibit excellent durability and resistance to chemicals, which enhances their lifespan and reduces replacement costs.
Common Uses of Polypropylene in Injection Molding
Polypropylene finds widespread application across various sectors due to its unique properties tailored for diverse needs through injection molding techniques. In the automotive industry, it's commonly used for producing dashboard components, interior trims, and battery cases due to its lightweight nature coupled with strength and resilience under stress conditions.
In consumer goods manufacturing, polypropylene serves as a primary material for items such as containers, packaging solutions, and household goods like storage bins or kitchen utensils—thanks to its ability to be molded into intricate designs while remaining affordable. Additionally, medical devices often utilize this versatile polymer because it meets stringent hygiene standards while providing robust performance during sterilization processes.
The Injection Molding Process
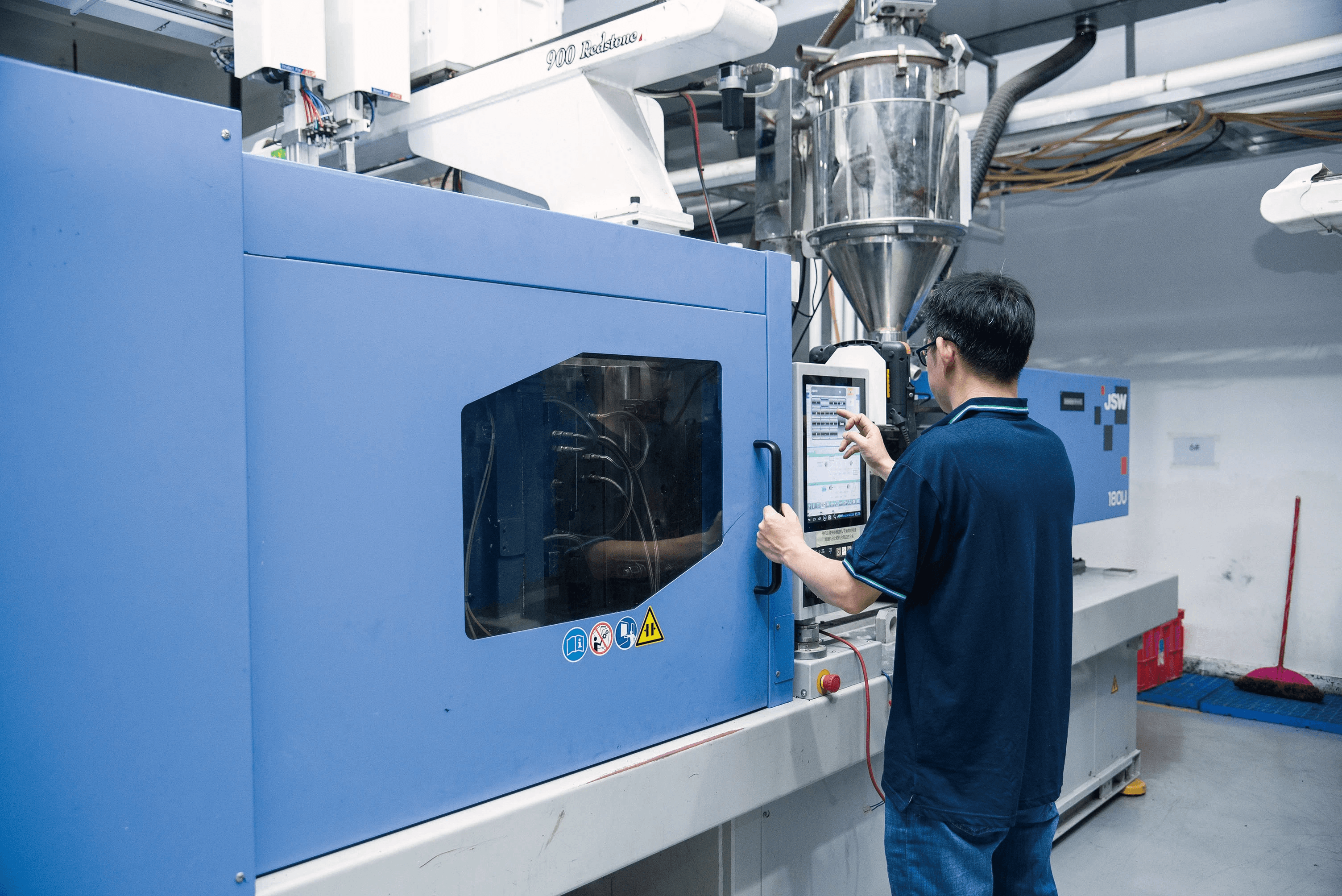
Injection molding is a fascinating blend of art and science, where molten polymer is transformed into intricate shapes with precision and efficiency. This process plays a pivotal role in manufacturing, especially when it comes to creating high-quality products from materials like polypropylene. Understanding the key steps involved in injection molding helps demystify this complex procedure and highlights its significance in molding manufacturing.
Key Steps in the Injection Molding Procedure
The injection molding procedure consists of several critical steps that ensure the final product meets desired specifications. First, raw polymer materials are fed into an injection molding machine, where they are heated until they reach a molten state. Next, this molten polymer is injected into an injection molding mold parts that have been designed to create specific shapes; once cooled and solidified, the mold opens to reveal the finished product.
After demolding, any excess material is trimmed away, and quality checks are conducted to ensure every piece meets stringent standards. Repeatability is crucial in this process; therefore, the machinery must be finely tuned for consistent results across multiple runs. Thus, mastering these steps not only optimizes production but also enhances overall efficiency in polymer injection molding.
Role of the Injection Molding Machine
At the heart of any successful injection molding operation lies the injection molding machine itself. This sophisticated piece of equipment performs several essential functions: heating the polymer materials, injecting them into molds at high pressure, and controlling cooling times for optimal solidification. The design and capabilities of these machines can significantly impact production speed and product quality.
Modern machines come equipped with advanced technology that allows for precise control over various parameters such as temperature and pressure during the injection process. This level of control ensures that even complex designs can be produced consistently without defects or variations in quality. In essence, an efficient injection molding machine serves as a vital cog in the wheel of effective polymer processing.
Importance of Injection Molding Tooling
Injection molding tooling is often underestimated but plays a crucial role in determining both cost-effectiveness and product quality within manufacturing processes. High-quality molds can lead to better surface finishes and tighter tolerances on finished products made from polypropylene or other polymers used in injection molding applications. Investing time and resources into developing robust tooling can yield significant long-term benefits for manufacturers.
Additionally, tooling allows for versatility within production; techniques such as over-molding enable manufacturers to combine different materials or colors seamlessly within one part creation cycle. Innovations in tooling design can further enhance productivity while reducing waste—a win-win situation for both manufacturers and consumers alike! Ultimately, understanding how critical proper tooling is will empower engineers to make informed decisions about their processes.
Molding Manufacturing Techniques
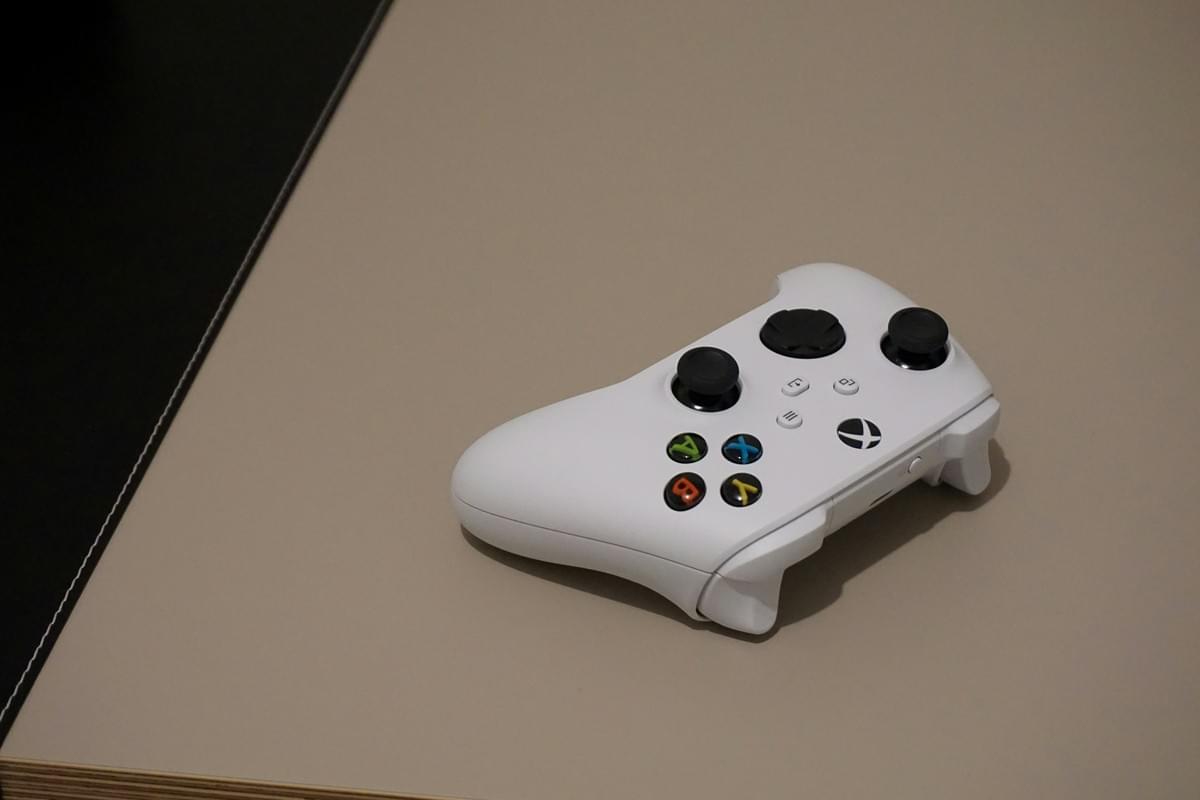
In the world of polymer injection molding, various techniques have emerged to enhance production efficiency and product quality. Understanding these molding manufacturing techniques is crucial for manufacturers looking to optimize their processes and remain competitive. This section delves into molding over molding, multi-material injection molding, and the latest innovations in injection molding tooling.
Overview of Molding Over Molding
Molding over molding is a fascinating technique that allows for the creation of complex parts by layering different materials during the injection molding process. This method involves injecting a base material into a mold, allowing it to cool slightly, and then injecting a second material over it, resulting in a bonded structure that combines properties from both polymers. The beauty of this approach lies in its ability to produce parts with enhanced functionality, such as improved grip or added durability, making it highly sought after in industries like automotive and consumer goods.
This technique not only showcases the versatility of injection molding but also highlights how manufacturers can leverage multiple materials to achieve specific performance characteristics. By using an injection molding machine equipped with specialized molds designed for this purpose, companies can streamline production while reducing waste associated with traditional assembly methods. Ultimately, this innovative approach contributes to more sustainable practices within polymer injection molding.
Multi-Material Injection Molding
Multi-material injection molding takes the concept of combining different polymers one step further by allowing for the simultaneous processing of multiple materials within a single cycle. This advanced technique enables manufacturers to create intricate designs that incorporate various colors or textures without compromising structural integrity. By utilizing an advanced injection molding machine capable of handling diverse materials simultaneously, businesses can significantly reduce production time and costs while increasing design flexibility.
The applications for multi-material injection molded products are vast; from sleek consumer electronics housings that require aesthetic appeal to durable industrial components needing specific mechanical properties, this method has proven invaluable across sectors. Furthermore, as industries increasingly demand customization and personalization in their products, multi-material capabilities will become even more essential in meeting these needs efficiently through polymer injection molding processes.
Innovations in Molding Tooling
The evolution of injection molding tooling has played a pivotal role in enhancing manufacturing efficiency and product quality within polymer injection molding operations. Recent innovations include advancements in mold design software that allow engineers to simulate flow patterns and thermal dynamics before actual production begins—saving both time and resources during setup phases. Additionally, new materials used for creating molds can withstand higher temperatures and pressures without warping or degrading over time.
Another exciting development is the integration of smart technology into tooling systems—such as sensors that monitor temperature changes or pressure fluctuations during the injection process—enabling real-time adjustments for optimal results. These cutting-edge improvements not only enhance productivity but also ensure consistency across batches by minimizing variations caused by human error or equipment limitations within traditional settings like conventional mold parts manufacturing lines.
Choosing Injection Molding Materials
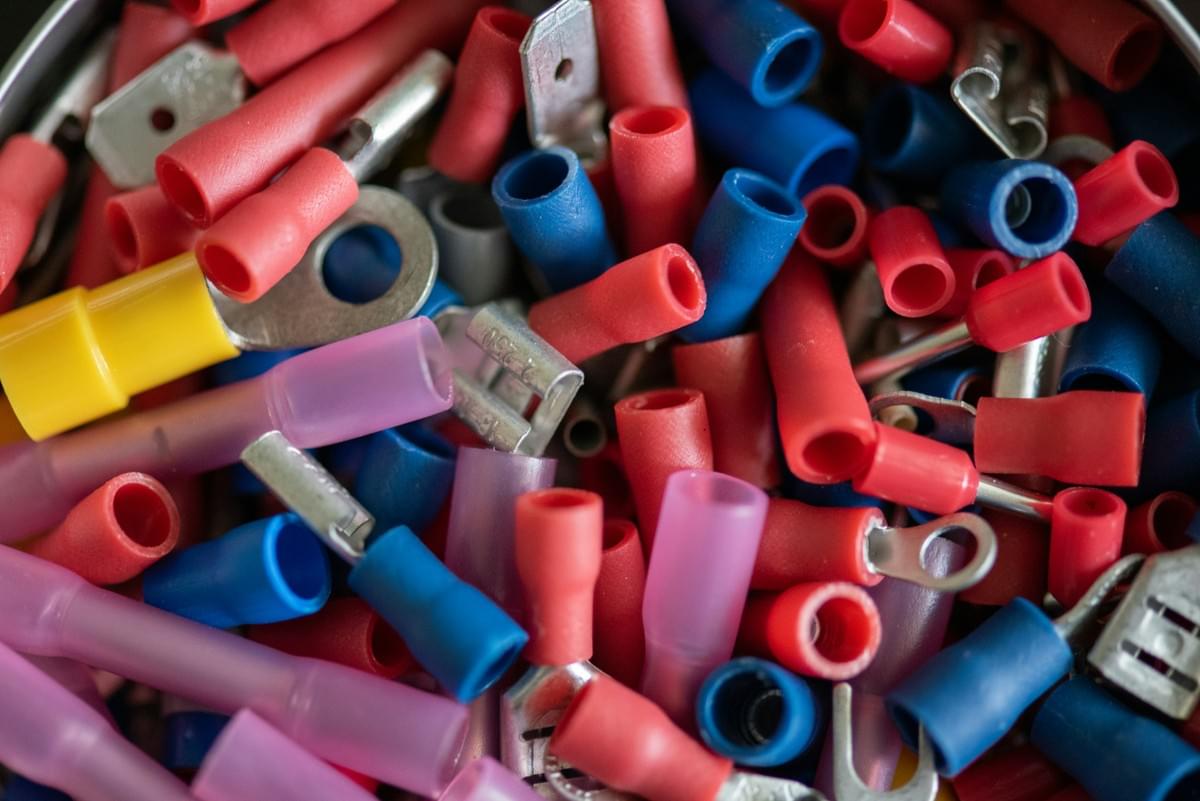
Selecting the right materials for polymer injection molding is a crucial step in the manufacturing process. The choice of injection molding materials can significantly influence product quality, production efficiency, and overall costs. Therefore, manufacturers must carefully evaluate various factors to ensure optimal performance and suitability for their specific applications.
Factors to Consider for Material Selection
When it comes to choosing materials for injection molding, several factors come into play. First and foremost, the mechanical properties of the material—such as strength, flexibility, and thermal resistance—must align with the intended use of the final product. Additionally, considerations like processing temperature compatibility with the injection molding machine and cost-effectiveness should also be part of the decision-making process.
Another important aspect is the environmental impact of materials used in polymer injection molding. Manufacturers are increasingly leaning towards sustainable options that minimize waste and reduce carbon footprints. This trend not only benefits our planet but can also enhance a company's reputation among eco-conscious consumers.
Benefits of Polypropylene Compared to Other Materials
Polypropylene stands out as a preferred choice among injection molding materials due to its impressive array of benefits. For starters, it offers excellent chemical resistance and durability while remaining lightweight—a combination that many other polymers struggle to achieve. This makes polypropylene particularly advantageous in industries such as automotive and consumer goods where strength-to-weight ratios are critical.
Additionally, polypropylene's versatility allows it to be easily molded into complex shapes during the injection molding process without compromising structural integrity. Its lower melting point compared to other plastics means that manufacturers can save on energy costs when operating their injection molding machines. Furthermore, polypropylene is recyclable, making it an environmentally friendly option that aligns with current sustainability trends.
Future Trends in Injection Molding Materials
The landscape of injection molding materials is continuously evolving as technology advances and market demands shift. One notable trend is the growing interest in bio-based polymers that offer similar performance characteristics as traditional plastics but with reduced environmental impact. These innovative materials are paving the way for greener manufacturing practices while still meeting rigorous industry standards.
Moreover, developments in multi-material injection molding are gaining traction as manufacturers seek ways to enhance product functionality through diverse material combinations—think over-molding techniques that allow different polymers to be combined seamlessly within a single component. As these trends unfold, we can expect more sophisticated tooling solutions tailored specifically for complex polymer injection molding applications.
In summary, selecting appropriate injection molding materials requires careful consideration of numerous factors including mechanical properties, processing capabilities, sustainability concerns, and market trends—all pivotal for ensuring successful outcomes in today's competitive manufacturing landscape.
Quality Assurance in Injection Molding
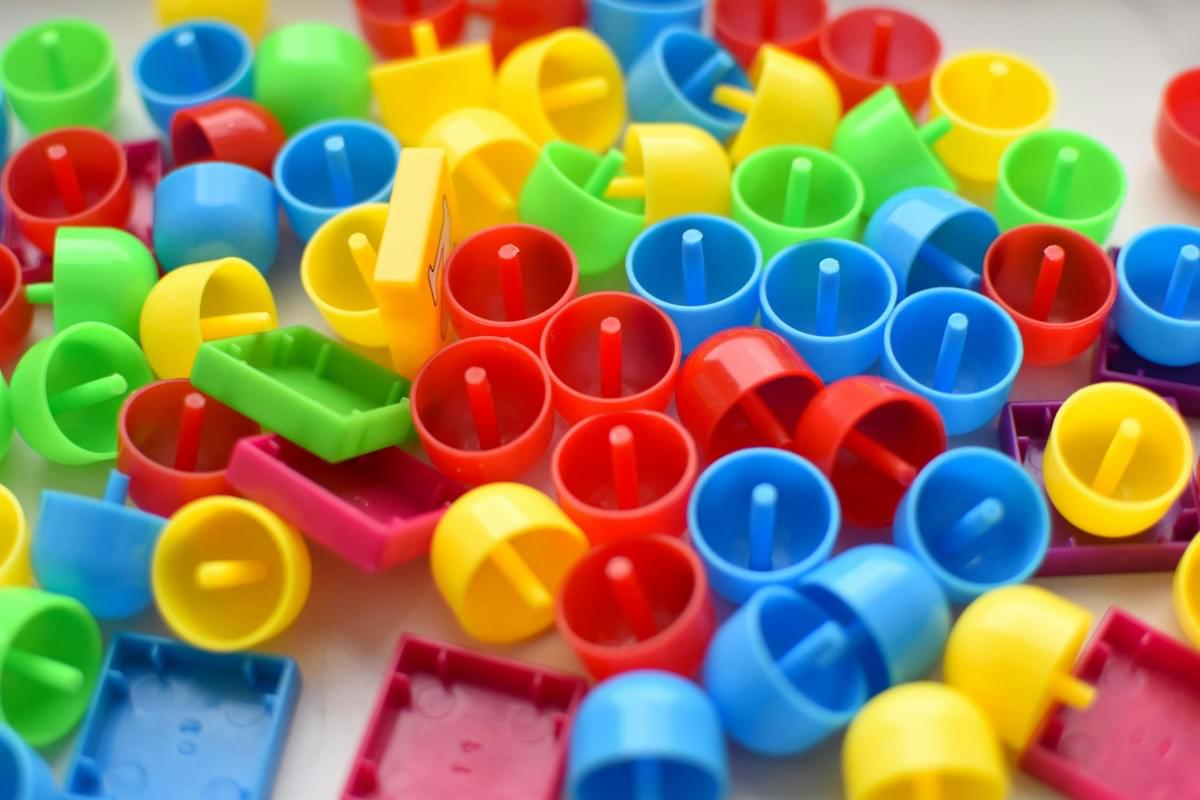
In the world of polymer injection molding, quality assurance is not just an option; it’s a necessity. The precision required in injection molding processes means that even the slightest deviation can result in defects, affecting the end product's functionality and aesthetic appeal. By implementing rigorous quality control measures, manufacturers can ensure that their injection molding machine operates efficiently and produces high-quality products consistently.
Importance of Quality Control and Assurance
Quality control in injection molding is crucial for maintaining customer satisfaction and brand reputation. It involves systematic monitoring of various stages of the injection molding process to identify issues before they escalate into major problems. This proactive approach helps manufacturers avoid costly rework or recalls while ensuring that each component meets stringent industry standards.
Moreover, effective quality assurance practices contribute to operational efficiency by minimizing waste and optimizing resource utilization. By focusing on quality from the outset, companies can enhance their production capabilities while reducing lead times. In a competitive market where every detail counts, investing in robust quality control measures is essential for long-term success.
Techniques for Ensuring Product Quality
Ensuring product quality in polymer injection molding involves several techniques tailored to address potential challenges at different stages of production. One common method is statistical process control (SPC), which uses data analysis to monitor and control the injection molding process continuously. This technique helps identify trends or anomalies early on, allowing for timely adjustments to maintain consistent output quality.
Another effective approach is implementing thorough inspection protocols for injection molding mold parts throughout the manufacturing process. Regular inspections help detect defects such as warping or dimensional inaccuracies before they reach the final assembly stage. Additionally, employing advanced technologies like 3D scanning can further enhance accuracy by providing detailed feedback on mold integrity and part geometry.
Finally, investing in high-quality injection molding tooling is vital for achieving precise results consistently. Well-designed molds reduce variability during production runs, leading to improved overall product reliability and performance. By integrating these techniques into their workflow, manufacturers can significantly elevate their product quality standards.
Baoyuan’s Expertise in Quality Management
Baoyuan stands out as a leader in quality management within the polymer injection molding industry due to its commitment to excellence at every level of production. With years of experience under its belt, Baoyuan employs a comprehensive approach that combines state-of-the-art technology with skilled craftsmanship to ensure top-tier outcomes for clients across various sectors.
The company's focus on continuous improvement drives them to adopt innovative practices that enhance both product quality and operational efficiency. From meticulous selection of high-grade injection molding materials to rigorous testing protocols for finished products, Baoyuan leaves no stone unturned when it comes to delivering superior results. Their expertise extends beyond traditional methods; they also embrace cutting-edge developments like smart manufacturing technologies that further refine their processes.
Ultimately, Baoyuan's dedication to maintaining stringent quality assurance practices positions them as a trusted partner for businesses seeking reliable solutions in polymer injection molding and beyond.
Conclusion
In wrapping up our exploration of polypropylene in the realm of polymer injection molding, it's clear that this material and the processes surrounding it are evolving rapidly. As industries continue to seek innovative solutions, the future of polypropylene injection molding appears bright, with advancements promising enhanced efficiency and sustainability. By embracing these changes, manufacturers can leverage polypropylene's unique properties to create high-quality products that meet market demands.
The Future of Polypropylene Injection Molding
The future of polypropylene injection molding is poised for transformative growth driven by technological advancements and an increasing focus on sustainability. Innovations in injection molding machine design and efficiency will allow for more precise control over the molding process, minimizing waste while maximizing output quality. Furthermore, as environmental concerns grow, we can expect a rise in biopolymer alternatives within traditional polymer injection molding applications, potentially revolutionizing how we think about material sourcing and usage.
Benefits of Advanced Injection Molding Techniques
Advanced injection molding techniques offer significant benefits that extend beyond mere production efficiency; they enhance product performance and customization options as well. Techniques like over molding and multi-material injection molding allow manufacturers to combine different materials seamlessly, resulting in products with improved functionality and aesthetic appeal. Additionally, leveraging cutting-edge injection molding tooling ensures that mold parts are designed for longevity and precision, further reducing costs associated with retooling or adjustments.
Key Takeaways for Manufacturers and Engineers
For manufacturers and engineers navigating the landscape of polymer injection molding, several key takeaways emerge from our discussion on polypropylene's role in this field. First, understanding the characteristics of various injection molding materials—including their advantages—can significantly influence production outcomes and product quality. Moreover, staying abreast of innovations in both tooling technology and manufacturing techniques will empower professionals to optimize their processes while ensuring compliance with evolving industry standards.