Introduction
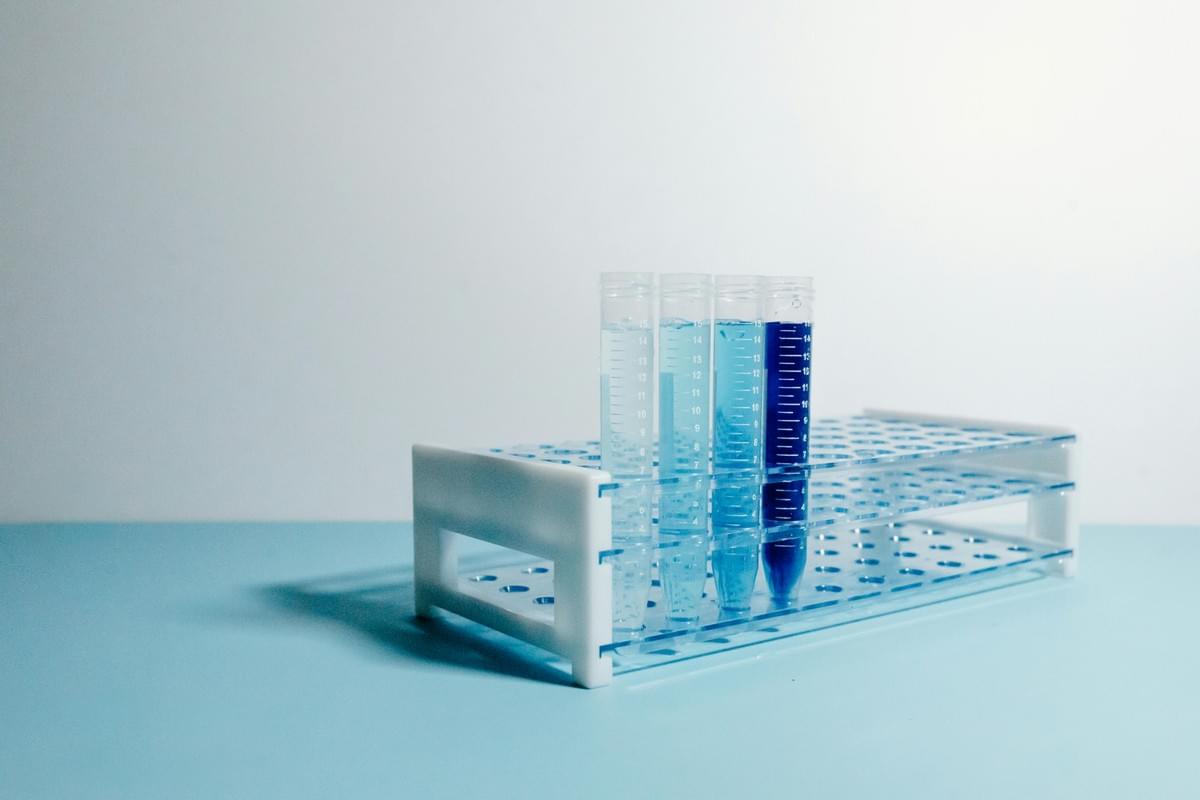
In the world of manufacturing, injection molding stands as a cornerstone technique, allowing for the efficient production of complex plastic parts. This method has revolutionized industries by enabling the creation of intricate designs with precision and speed. However, beneath this impressive process lies a crucial factor that can make or break the success of any project: the choice of plastic material.
Discover the World of Injection Molding
Injection molding is not just about pouring liquid plastic into a mold; it’s an art form that combines science and engineering to produce high-quality components. From automotive parts to household items, this versatile technique can cater to virtually any application imaginable. Understanding how injection moldable plastics work is essential for anyone looking to harness their potential in product design and manufacturing.
Why Material Choice Matters in Molding
The properties of different plastics vary widely; some offer exceptional strength while others excel in flexibility or heat resistance. By understanding these differences, manufacturers can optimize their processes and ensure that they are using the strongest plastic for injection molding suited for their specific needs.
The Strongest Plastics for Injection Molding
Among various options available, certain plastics stand out due to their superior strength and durability characteristics. High-performance polymers are often preferred in demanding applications where resilience is key, such as aerospace or medical devices. In this discussion, we will explore what makes these materials exceptional choices for those seeking reliable solutions in plastic injection processes.
Overview of Injection Moldable Plastics
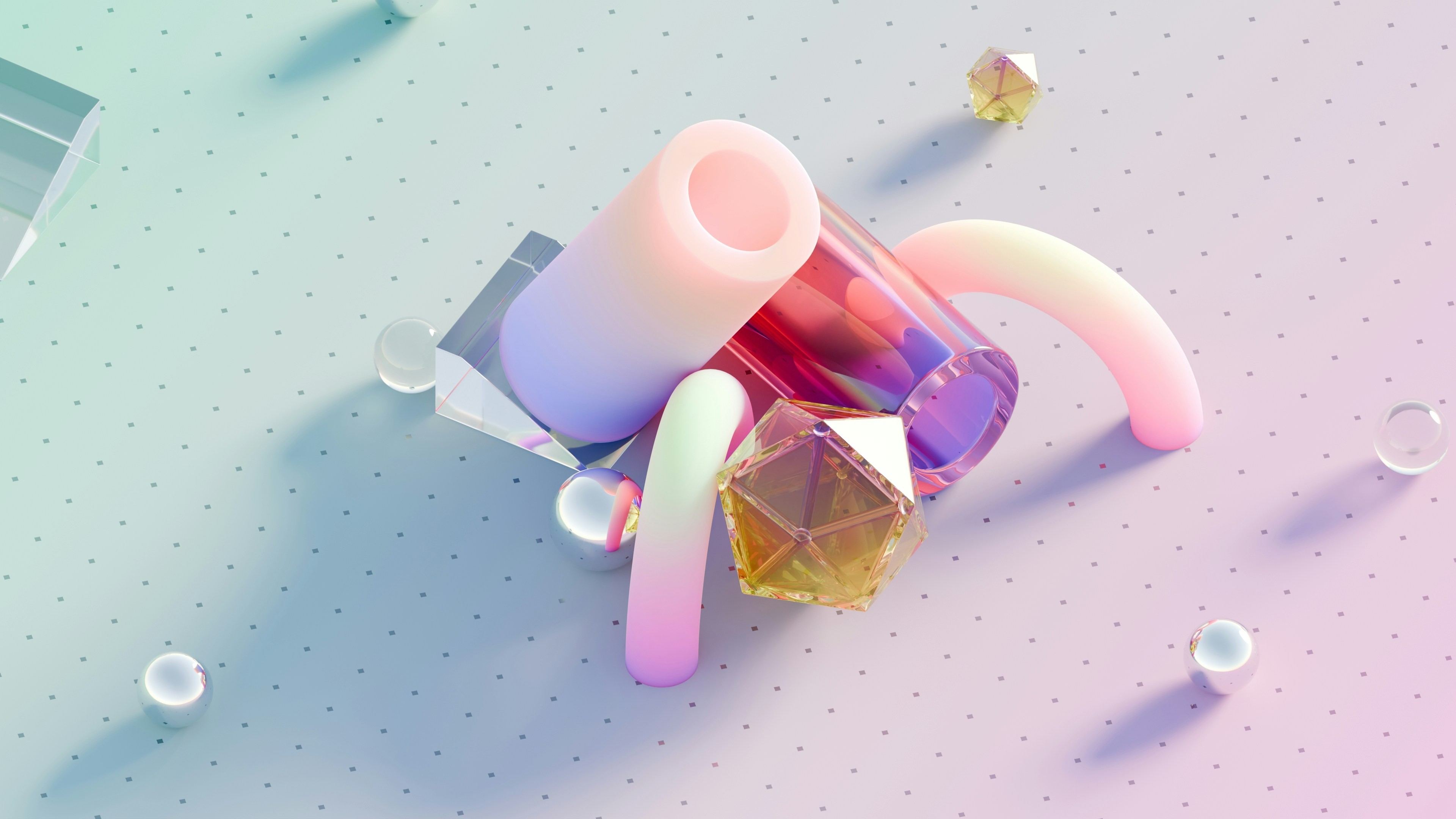
Injection moldable plastics are the unsung heroes of modern manufacturing, forming the backbone of countless products we use daily. Defined as thermoplastic or thermosetting polymers that can be shaped and solidified through injection molding processes, these materials offer an incredible balance between versatility and performance. Their importance cannot be overstated, as they allow for complex shapes and designs that are both lightweight and durable.
Definition and Importance
Injection moldable plastics encompass a wide range of synthetic materials specifically designed for use in plastic injection molding processes. These materials can be melted down and injected into molds, where they cool and solidify into precise shapes. The significance of these plastics lies in their ability to produce high volumes of consistent parts quickly, making them essential for industries ranging from automotive to consumer goods.
Key Properties of Injection Moldable Plastics
The strongest plastic for injection molding boasts several key properties that make it suitable for various applications. These properties include high tensile strength, excellent impact resistance, thermal stability, and chemical resistance. Furthermore, injection moldable plastics can be engineered to meet specific performance criteria, allowing manufacturers to choose the right plastic material based on the demands of their projects.
Applications in Various Industries
Plastic injection molding has become a go-to method across numerous industries due to its adaptability and efficiency. In automotive manufacturing, strong plastics are used for everything from dashboard components to exterior panels because they provide both strength and weight savings. Additionally, consumer electronics rely on injection moldable plastics for casings and internal components that require durability without sacrificing aesthetics—proving that plastic for molding is truly everywhere!
Common Types of Plastic for Molding
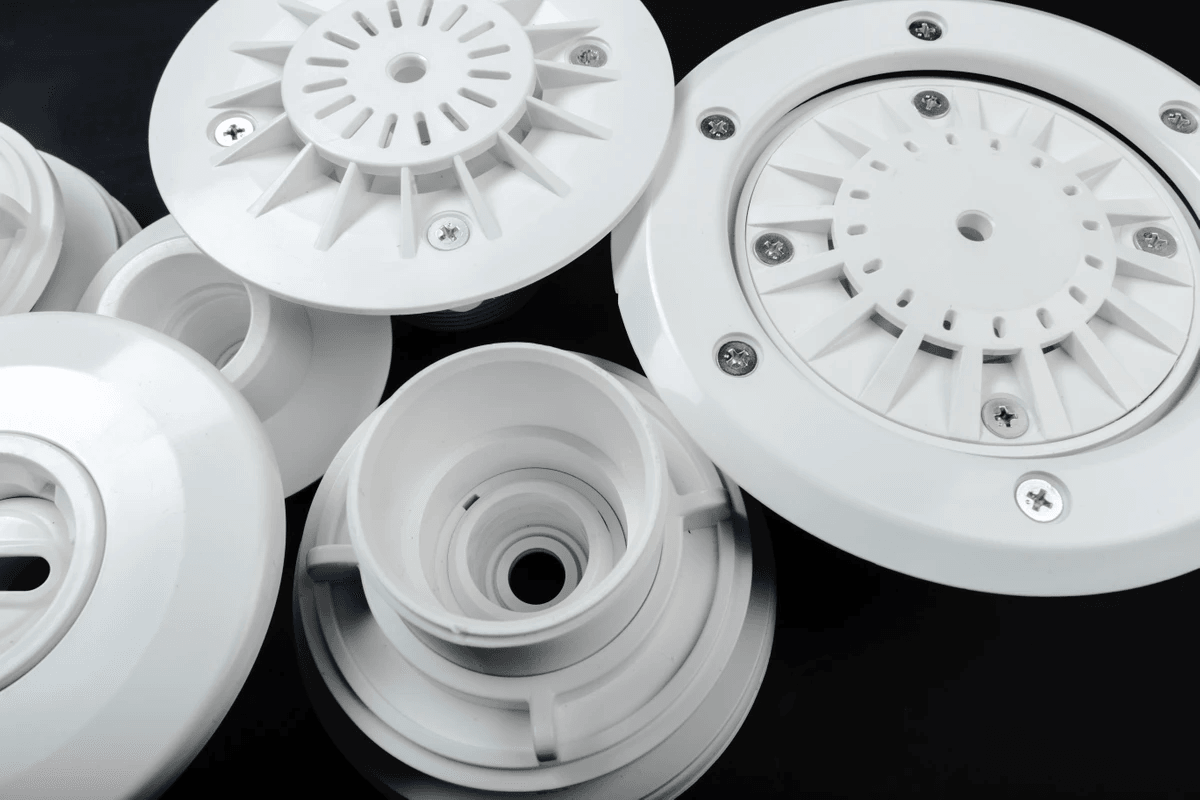
When it comes to plastic injection molding, the choice of material can make or break your project. Understanding the common types of plastic for molding is crucial, as each type offers unique properties and advantages. Let’s dive into some of the most popular options that dominate the injection moldable plastics landscape.
Polyethylene: The Everyday Workhorse
Polyethylene is often hailed as the strongest plastic for injection molding due to its remarkable versatility and ease of processing. This thermoplastic is used in a myriad of applications, from packaging materials to household items, thanks to its excellent chemical resistance and durability. Its lightweight nature combined with cost-effectiveness makes polyethylene a go-to choice for manufacturers looking to optimize their plastic injection processes.
In the realm of plastic for molding, polyethylene comes in various densities—low-density (LDPE) and high-density (HDPE)—each catering to different needs. LDPE offers flexibility and softness, making it ideal for bags and films, while HDPE provides added strength and rigidity suitable for containers and bottles. With such diverse applications, polyethylene truly earns its title as the everyday workhorse in plastic injection molding.
Polypropylene: Versatile and Cost-Effective
Polypropylene stands out as another strong contender in the world of injection moldable plastics due to its impressive balance between performance and affordability. Known for its resistance to fatigue, chemicals, and moisture, polypropylene is often employed in products ranging from automotive parts to food containers. Its lightweight nature not only saves costs but also enhances efficiency during transportation—an essential factor in modern manufacturing.
The adaptability of polypropylene allows it to be molded into intricate shapes with high precision during plastic injection processes. Additionally, this material can be easily colored or modified with additives to enhance specific properties like UV resistance or impact strength. With such versatility at its disposal, polypropylene continues to be a staple choice among engineers seeking reliable materials for their projects.
Nylon: Strength Meets Flexibility
Nylon is celebrated as one of the strongest plastics available for injection molding, combining exceptional strength with remarkable flexibility—a true engineering marvel! This synthetic polymer boasts outstanding abrasion resistance and low friction properties, making it an ideal candidate for applications that require durability under stress or repeated use. From automotive components to consumer goods like zippers and textiles, nylon's robust characteristics are hard to overlook.
What sets nylon apart from other plastics is its ability to withstand elevated temperatures while maintaining structural integrity—a crucial feature in many industrial applications involving heat exposure during production processes. Furthermore, nylon can absorb moisture without compromising performance; this property allows it to adapt well across various environments where other plastics might fail. For those seeking high-performance materials in their plastic injection endeavors, nylon undoubtedly shines bright on the list!
The Strongest Plastic for Injection Molding
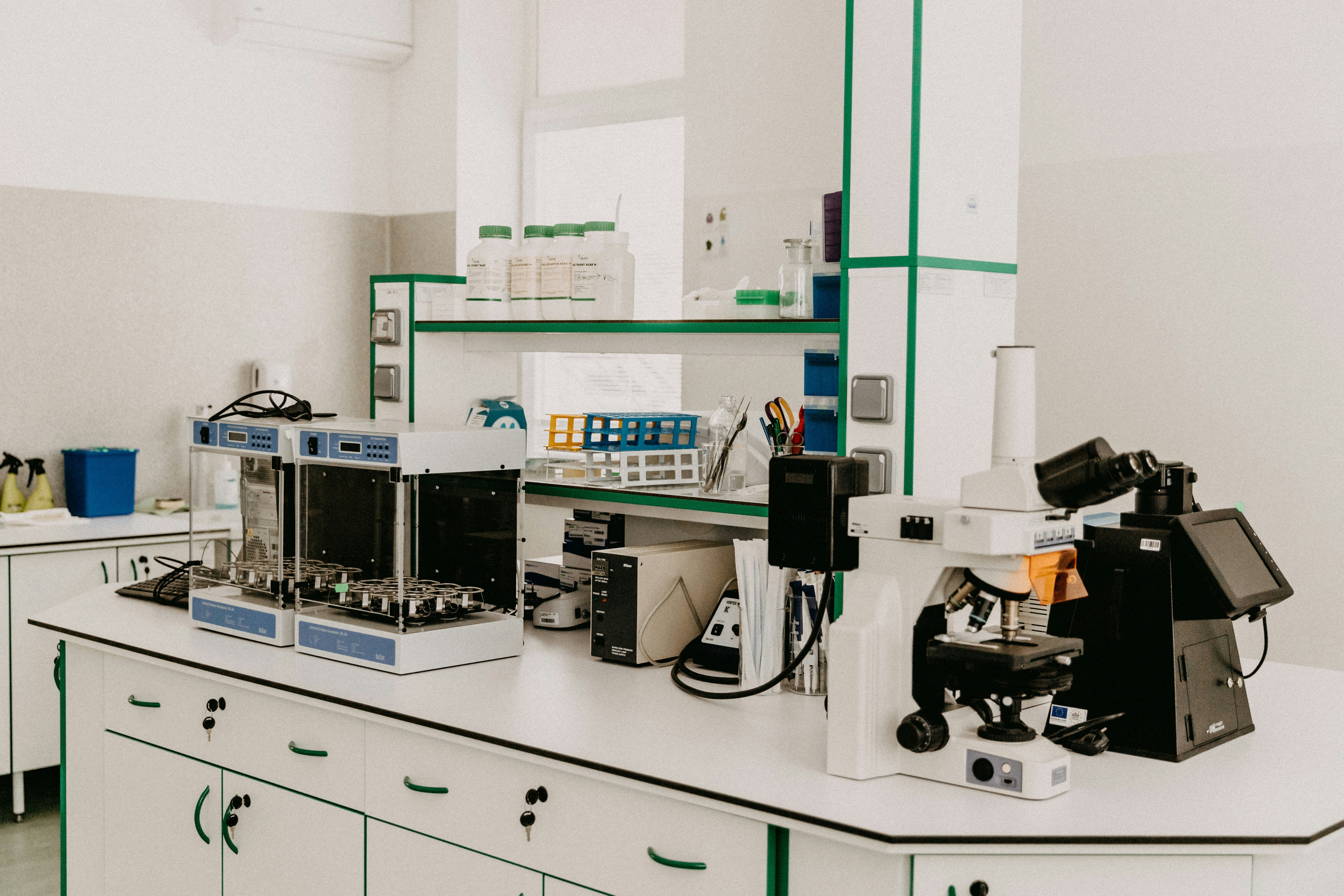
When it comes to injection molding, the quest for the strongest plastic often leads engineers and manufacturers to high-performance polymers. These materials are designed to withstand extreme conditions and deliver exceptional mechanical properties, making them ideal for demanding applications. By harnessing the potential of these advanced plastics, industries can achieve superior results in their products.
High-Performance Polymers Unleashed
High-performance polymers represent a category of injection moldable plastics that stand out due to their remarkable strength and resilience. Among these, materials like polyether ether ketone (PEEK) and polyamide-imide (PAI) have gained popularity for their ability to maintain structural integrity under heat and stress. These polymers not only offer excellent chemical resistance but also provide outstanding dimensional stability, making them the go-to choice when seeking the strongest plastic for injection molding.
The versatility of high-performance polymers means they can be tailored for specific applications, whether it's aerospace components or medical devices requiring stringent safety standards. Their unique characteristics allow them to outperform traditional plastics in critical environments, ensuring reliability where it matters most. As industries continue to innovate, these cutting-edge materials are paving the way for advancements in plastic injection molding technology.
Comparing Strength and Durability
Strength alone doesn't paint a complete picture; durability is equally crucial when selecting a plastic material for molding. Various high-performance polymers exhibit different strengths under varying conditions—some excel at resisting impact while others shine in thermal stability tests. For instance, PEEK is renowned not only as one of the strongest plastics but also as one of the most durable options available today.
When comparing strength and durability among injection moldable plastics, it's essential to consider factors such as tensile strength, flexural modulus, and resistance to wear and tear over time. Testing these parameters helps manufacturers determine which material will best suit their specific needs while ensuring longevity in real-world applications. Ultimately, balancing strength with durability leads to better-performing products that can withstand rigorous use without compromising on quality.
Real-World Applications of Strong Plastics
The strongest plastic for injection molding finds its place across various industries where performance is non-negotiable. In aerospace engineering, high-performance polymers are used in components that must endure extreme temperatures and pressures without failing—think lightweight brackets or insulation parts that contribute significantly to overall aircraft efficiency. Similarly, medical devices benefit from these robust materials due to their biocompatibility and ability to maintain integrity under sterilization processes.
Automotive manufacturing also leverages strong plastics like polyamide-imide (PAI) in engine components that require both heat resistance and mechanical strength. Electrical connectors made from high-performance thermoplastics ensure reliable operation even under challenging conditions such as moisture exposure or vibration stressors common in automotive settings. With an ever-growing list of applications ranging from industrial equipment to consumer goods, it's clear that strong plastics play an integral role in pushing boundaries within multiple sectors.
Special Purpose Injection Molding Materials
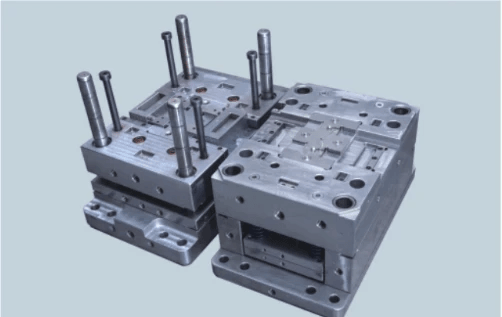
In the world of injection molding, not all plastics are created equal. Some materials are designed for specific applications, boasting unique characteristics that set them apart from standard injection moldable plastics. This section delves into special purpose injection molding materials, highlighting their benefits and applications in various industries.
Thermoplastic Elastomers: Flexibility Redefined
Thermoplastic elastomers (TPEs) combine the best of both worlds—flexibility and durability—making them an ideal choice for a variety of applications in plastic injection molding. These materials exhibit rubber-like properties while being processable like thermoplastics, allowing for easy shaping and forming during the injection process. TPEs are often utilized in products requiring soft-touch surfaces or enhanced grip, such as handles, seals, and gaskets.
One of the standout features of TPEs is their ability to withstand extreme temperatures without losing their flexibility or performance. This makes them suitable for outdoor applications where exposure to the elements is a concern. Additionally, TPEs can be blended with other plastics to enhance their performance further, making them a versatile option among plastic materials for molding.
In summary, thermoplastic elastomers redefine flexibility in injection molding by providing durable yet adaptable solutions across numerous industries—from automotive components to consumer goods. Their unique properties ensure they remain a go-to choice when designing products that demand both resilience and comfort.
Engineering Plastics: Toughness in Action
When it comes to strength and durability in plastic injection molding, engineering plastics take center stage as some of the strongest options available on the market today. These high-performance polymers are designed to endure rigorous conditions while maintaining structural integrity over time. Common types include polycarbonate (PC), acrylonitrile butadiene styrene (ABS), and polyamide (nylon), each offering distinct advantages depending on the application.
Engineering plastics excel in environments where mechanical stress is prevalent—think automotive parts or industrial machinery components that require exceptional toughness under pressure. The ability to withstand high temperatures without deforming adds another layer of appeal when selecting the strongest plastic for injection molding projects. Furthermore, these materials can be tailored with additives to enhance properties like UV resistance or flame retardancy.
With their impressive mechanical properties and versatility, engineering plastics have become indispensable across various sectors including automotive, aerospace, and electronics manufacturing. Their role as tough contenders in plastic for molding ensures they contribute significantly to creating reliable products built for longevity.
Biodegradable Plastics: Eco-Friendly Choices
As sustainability becomes increasingly important in manufacturing processes globally, biodegradable plastics are emerging as eco-friendly alternatives within the realm of plastic injection molding materials. These innovative substances break down more easily than traditional plastics when exposed to natural environmental conditions—reducing waste accumulation and promoting greener practices across industries.
Biodegradable options such as polylactic acid (PLA) offer similar processing capabilities found with conventional injection moldable plastics but with added environmental benefits that appeal to conscious consumers and manufacturers alike. While they may not always match the strength levels achieved by engineering plastics or thermoplastic elastomers, advancements continue pushing these green solutions closer toward performance parity with traditional options.
Choosing biodegradable plastics reflects a commitment to sustainability without sacrificing quality—a win-win scenario for businesses looking to innovate responsibly while meeting consumer demands for environmentally friendly products! By integrating these eco-conscious choices into your production line-up alongside stronger alternatives like TPEs or engineering-grade polymers offers an opportunity not just towards profitability but also towards social responsibility.
Choosing the Right Plastic Material
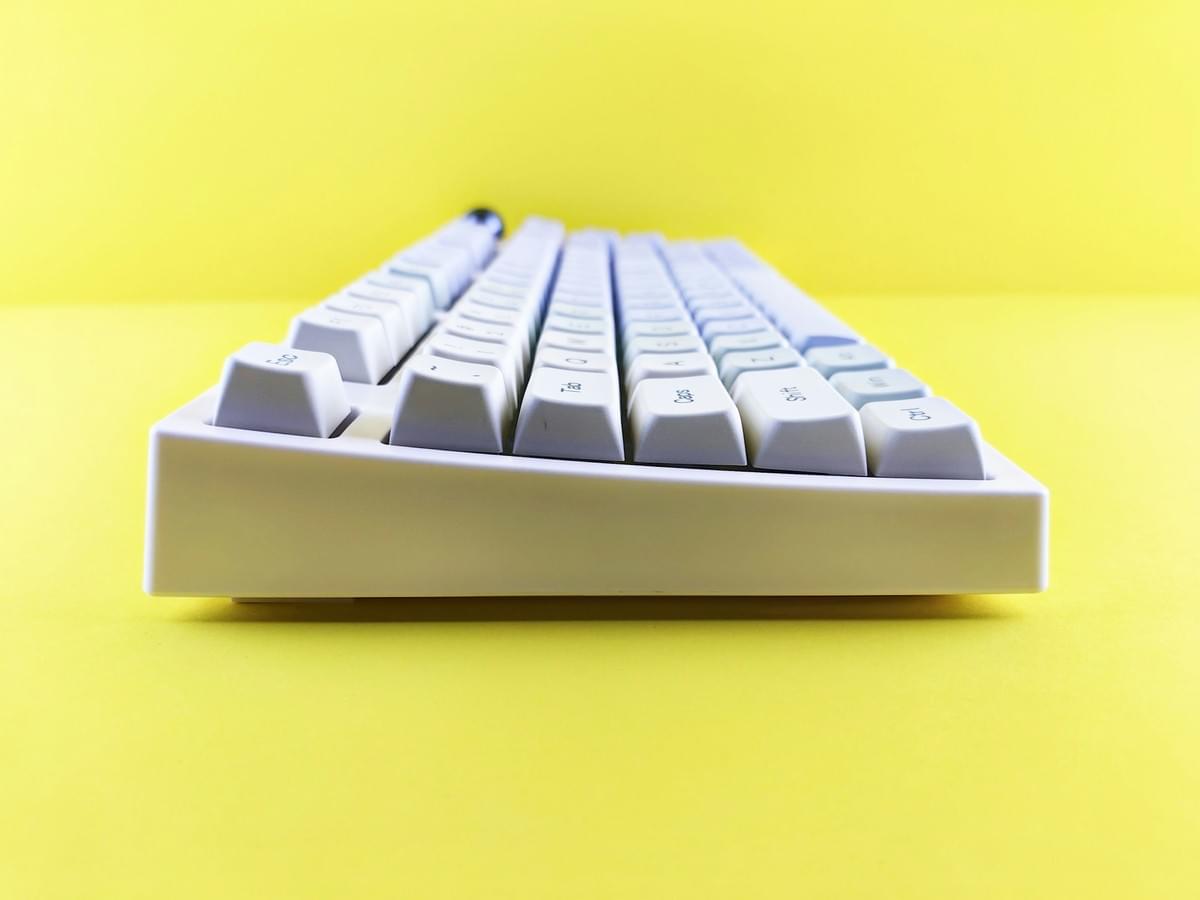
Selecting the right plastic material for injection molding can feel like navigating a maze, but it doesn't have to be overwhelming. The strongest plastic for injection molding can vary based on specific project needs, and understanding the options is key. By considering factors such as performance requirements, environmental conditions, and budget constraints, you can make informed decisions that lead to successful outcomes in your projects.
Factors Influencing Material Selection
When choosing an injection moldable plastic, several factors come into play that can significantly impact your final product. First and foremost is the mechanical properties of the plastic; tensile strength, impact resistance, and flexibility are crucial to ensure that your product meets its intended use. Additionally, thermal stability and chemical resistance must be considered to ensure longevity in various environments—after all, no one wants a melted or corroded product!
Another important factor is processing characteristics: some plastics are easier to mold than others due to their flow properties during plastic injection. This means that while one type of strong plastic may offer superior durability, it could also complicate production if it doesn’t flow well in the mold. Lastly, regulatory standards and environmental considerations are becoming increasingly significant; choosing biodegradable plastics or materials with lower carbon footprints may not only appeal to eco-conscious consumers but also comply with emerging regulations.
Cost vs. Performance: Finding the Balance
In any project involving plastic for molding, balancing cost against performance is often a tightrope walk—one misstep could mean budget overruns or compromised quality! While it's tempting to opt for cheaper materials when selecting injection molding materials, this approach can backfire if those materials fail in application or require costly redesigns later on. The strongest plastics for injection molding usually come with a higher price tag due to their enhanced properties; however, investing upfront can save time and money in the long run.
To strike this balance effectively, it's essential to conduct thorough research on different types of plastics available for injection molding applications. Consider not just the initial cost but also factors like durability over time and maintenance requirements—these elements contribute significantly to total lifecycle costs. Ultimately, finding a sweet spot between cost efficiency and high-performance material will lead you toward making smarter decisions for your projects.
Insights from the Baoyuan Team
The Baoyuan Team has amassed invaluable insights over years of experience in selecting suitable plastics for various applications in plastic injection molding. Their expertise emphasizes that understanding customer needs is paramount—what works beautifully for one client might not suit another’s specifications at all! They recommend conducting detailed consultations before settling on any specific type of plastic material so that all variables are taken into account.
Moreover, they advocate keeping abreast of industry trends regarding new innovations in strong plastics designed specifically for challenging environments or specialized applications—this knowledge could give you an edge over competitors who stick with traditional choices without exploring newer options available today! Finally, don’t underestimate the power of collaboration; working closely with suppliers who understand your unique challenges will ensure you receive tailored recommendations that fit perfectly into your production process.
Conclusion
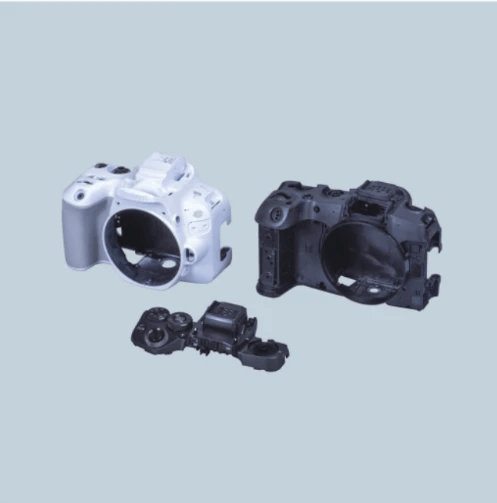
As we wrap up our exploration of injection molding and the materials that drive this innovative process, it's clear that selecting the right plastic is crucial. From everyday workhorses like polyethylene to high-performance polymers, each type of injection moldable plastic has its unique strengths and applications. Understanding these options empowers manufacturers to make informed decisions that enhance product quality and performance.
Recap of Key Injection Molding Plastics
Throughout this guide, we've delved into various types of plastics used in injection molding, highlighting their key properties and applications. Polyethylene stands out as a versatile choice for many everyday items, while polypropylene offers a cost-effective solution for diverse needs. Meanwhile, nylon emerges as the strongest plastic for injection molding when flexibility and durability are paramount, showcasing the range of options available in the ever-evolving landscape of plastic materials.
Future Trends in Injection Molding Materials
The future of injection molding materials is bright and brimming with possibilities. Innovations in biodegradable plastics are gaining traction as industries seek eco-friendly solutions without sacrificing quality or performance. Additionally, advancements in engineering plastics promise even tougher applications, ensuring that manufacturers can meet increasing demands while pushing the boundaries of what's possible with plastic injection.
Making Informed Choices for Your Projects
Choosing the right plastic material for your projects requires careful consideration of various factors such as strength, flexibility, cost, and environmental impact. By weighing these elements against your specific needs—whether you're focused on durability or budget constraints—you can make informed decisions that align with your project goals. With insights from industry experts like the Baoyuan team at your disposal, navigating the world of injection molding becomes a strategic advantage rather than a daunting task.