Introduction
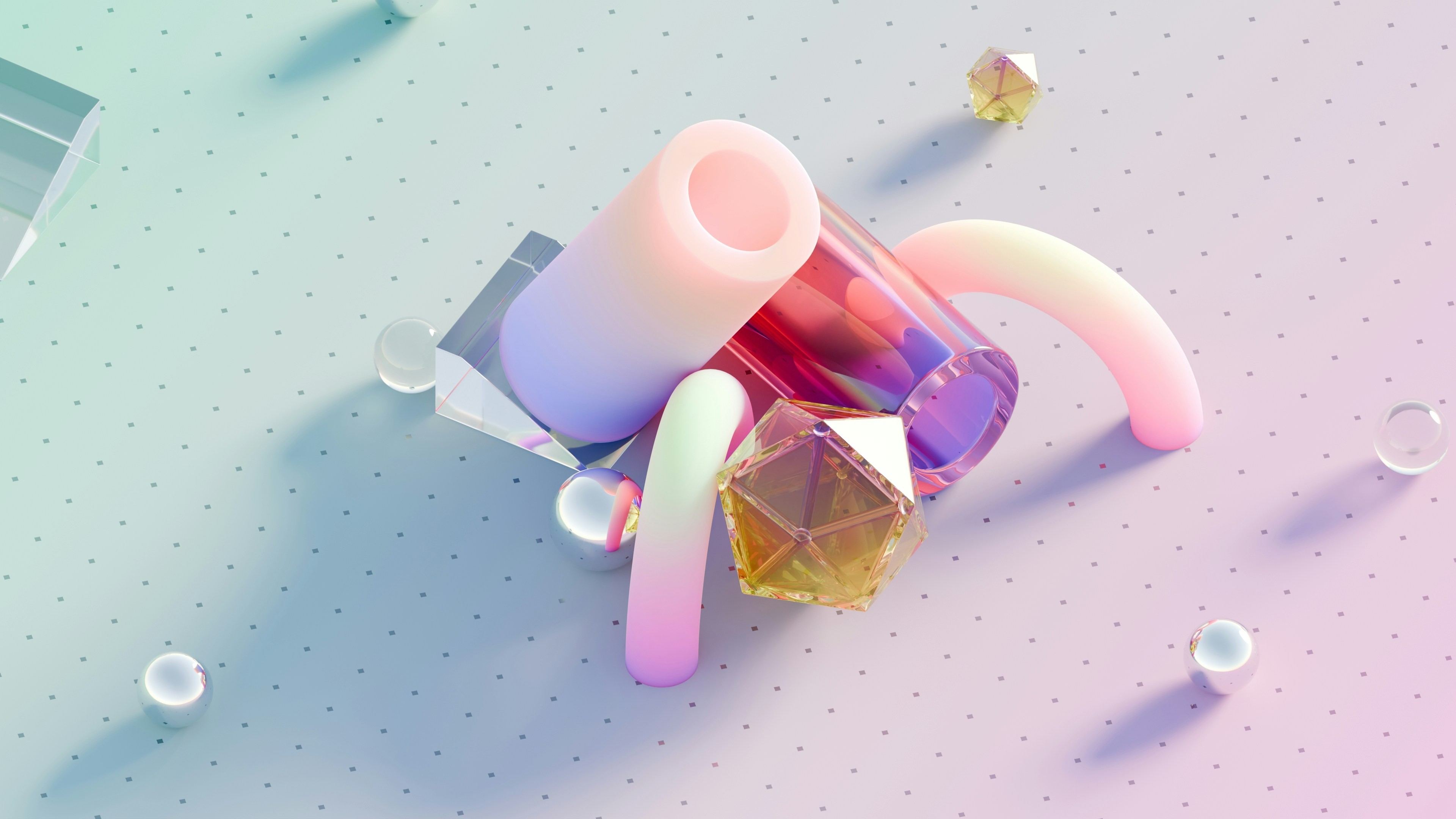
In the world of plastic manufacturing, injection molding polymers play a pivotal role in shaping the products we use daily. From household items to complex components in various industries, understanding these materials is essential for anyone involved in plastic injection molding. This introduction will explore the significance of injection moldable plastics and provide an overview of some of the most popular types used today.
Understanding Injection Molding Polymers
Injection molding polymers are specialized materials designed for use in injection molding processes, where molten plastic is injected into a mold to create specific shapes and forms. These polymers exhibit unique properties that make them suitable for diverse applications, including durability, flexibility, and resistance to chemicals. By grasping how these polymers function and their characteristics, manufacturers can optimize their production processes and enhance product quality.
Importance of Injection Moldable Plastics
The importance of injection moldable plastics cannot be overstated; they are integral to modern manufacturing practices across various sectors. These materials allow for efficient production methods that reduce waste while ensuring high-quality output through precision engineering with an injection molding machine or equipment. The ability to create complex shapes with minimal labor makes them invaluable in industries ranging from automotive to consumer goods.
Overview of Popular Plastic Types
Several types of plastics have gained popularity within the realm of injection molding due to their unique attributes and versatility. Polypropylene stands out as a versatile workhorse, while polyethylene is celebrated for its lightweight nature; acrylonitrile butadiene styrene (ABS) offers toughness that meets demanding standards, and polystyrene provides an economical choice for mass production needs. Each type has distinct advantages that cater to specific requirements in the ever-evolving landscape of plastic manufacturing.
Polypropylene: The Versatile Workhorse
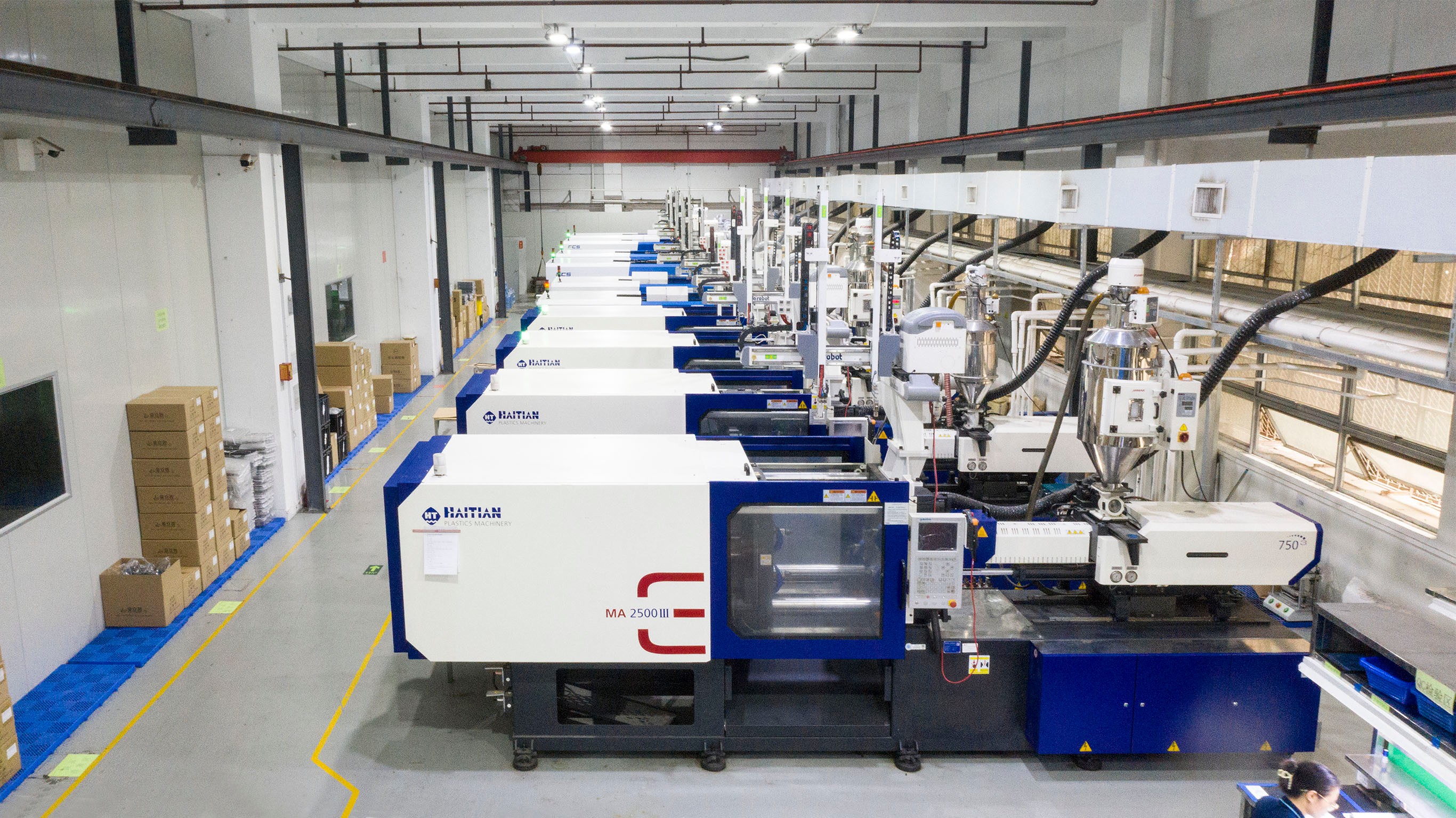
Polypropylene is often hailed as the unsung hero of injection molding polymers, thanks to its remarkable versatility and practicality in various applications. This thermoplastic polymer boasts a unique combination of properties that make it an ideal choice for plastic manufacturing processes. From automotive parts to consumer goods, polypropylene has established itself as a go-to material in the world of injection moldable plastics.
Characteristics of Polypropylene
Polypropylene stands out due to its excellent chemical resistance, lightweight nature, and high melting point, making it suitable for a variety of environments and applications. Its semi-crystalline structure provides good strength while maintaining flexibility, which is crucial for many mold plastic injection processes. Additionally, polypropylene is available in various grades and colors, allowing manufacturers to tailor their products according to specific requirements.
Applications in Plastic Manufacturing
In the realm of plastic manufacturing, polypropylene is widely used across numerous sectors including automotive, healthcare, and packaging industries. Its durability makes it perfect for producing everything from car bumpers to medical containers that require sterilization. Furthermore, its ability to be easily molded using injection molding machines means that complex shapes can be achieved with high precision and efficiency.
Benefits in Injection Molding
The benefits of using polypropylene in injection molding are manifold; first and foremost is its cost-effectiveness compared to other materials like polyethylene or nylon. This polymer's quick cycle times during the plastic injection molding process enhance productivity while minimizing waste—an essential factor for manufacturers looking to optimize their operations with efficient injection molding equipment. Moreover, polypropylene's recyclability contributes positively toward sustainable practices within the industry.
Polyethylene: The Lightweight Champion
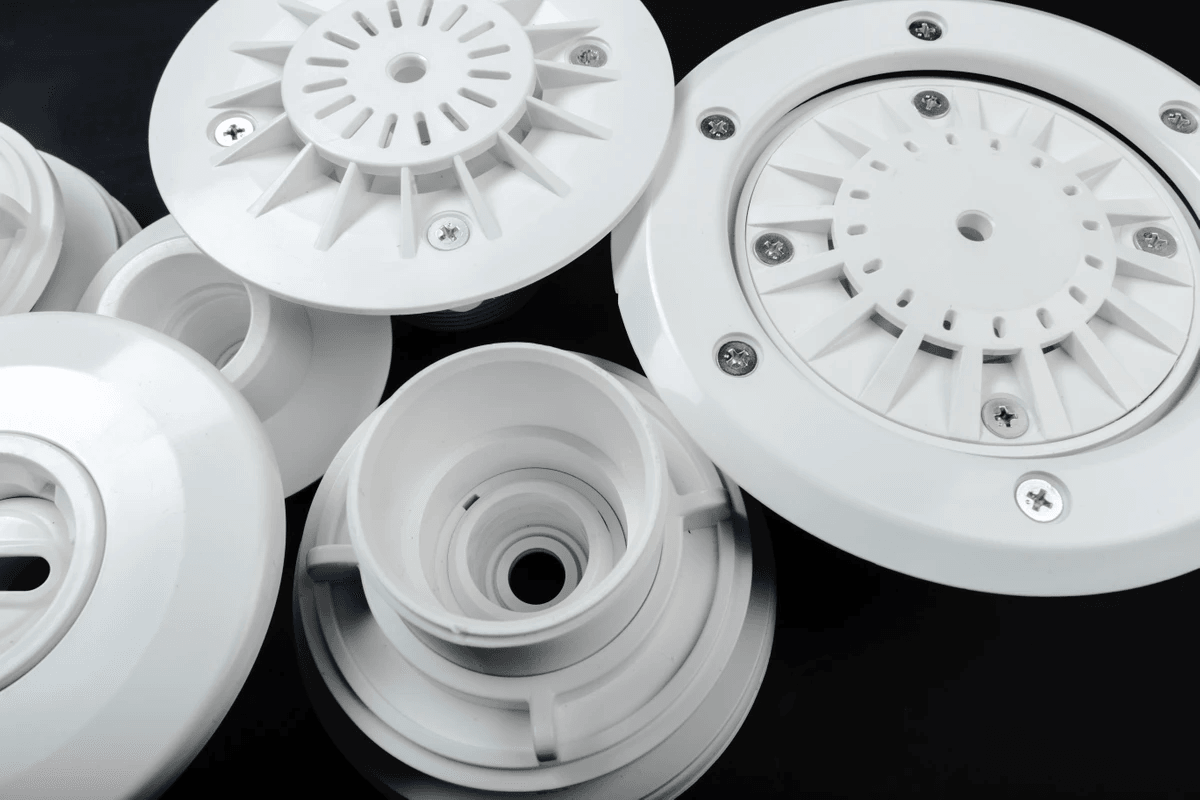
Polyethylene, often hailed as the lightweight champion of injection molding polymers, is a versatile thermoplastic that comes in various forms. Its unique properties make it an ideal candidate for plastic manufacturing processes, particularly in plastic injection molding. With its ability to be molded into intricate shapes and structures, polyethylene has secured its place as a favorite among manufacturers looking for reliable injection moldable plastics.
Different Types of Polyethylene
Polyethylene is primarily categorized into several types based on density and branching: Low-Density Polyethylene (LDPE), High-Density Polyethylene (HDPE), Linear Low-Density Polyethylene (LLDPE), and Ultra-High Molecular Weight Polyethylene (UHMWPE). Each type offers distinct characteristics suited for specific applications; for instance, LDPE is known for its flexibility while HDPE boasts superior strength. Understanding these variations is crucial when selecting the appropriate type of polyethylene for specific projects in plastic injection molding.
Key Advantages for Injection Mold Plastic
One of the standout advantages of polyethylene in injection mold plastic applications is its excellent chemical resistance, making it suitable for products that may encounter harsh environments or substances. Additionally, polyethylene's low density allows manufacturers to produce lightweight components without compromising strength or durability—a significant benefit when using an injection molding machine. Furthermore, the ease with which polyethylene can be processed through various injection molding equipment enhances production efficiency and reduces costs.
Common Uses in Various Industries
Polyethylene finds itself at home across a multitude of industries due to its versatility and performance characteristics. In consumer goods, it's often used in packaging materials such as bags and containers due to its lightweight nature and resistance to moisture. Beyond that, construction materials like pipes and fittings frequently utilize HDPE because of its high tensile strength and ability to withstand environmental stressors—demonstrating how integral this polymer is within the realm of plastic manufacturing.
Acrylonitrile Butadiene Styrene: The Tough Polymer
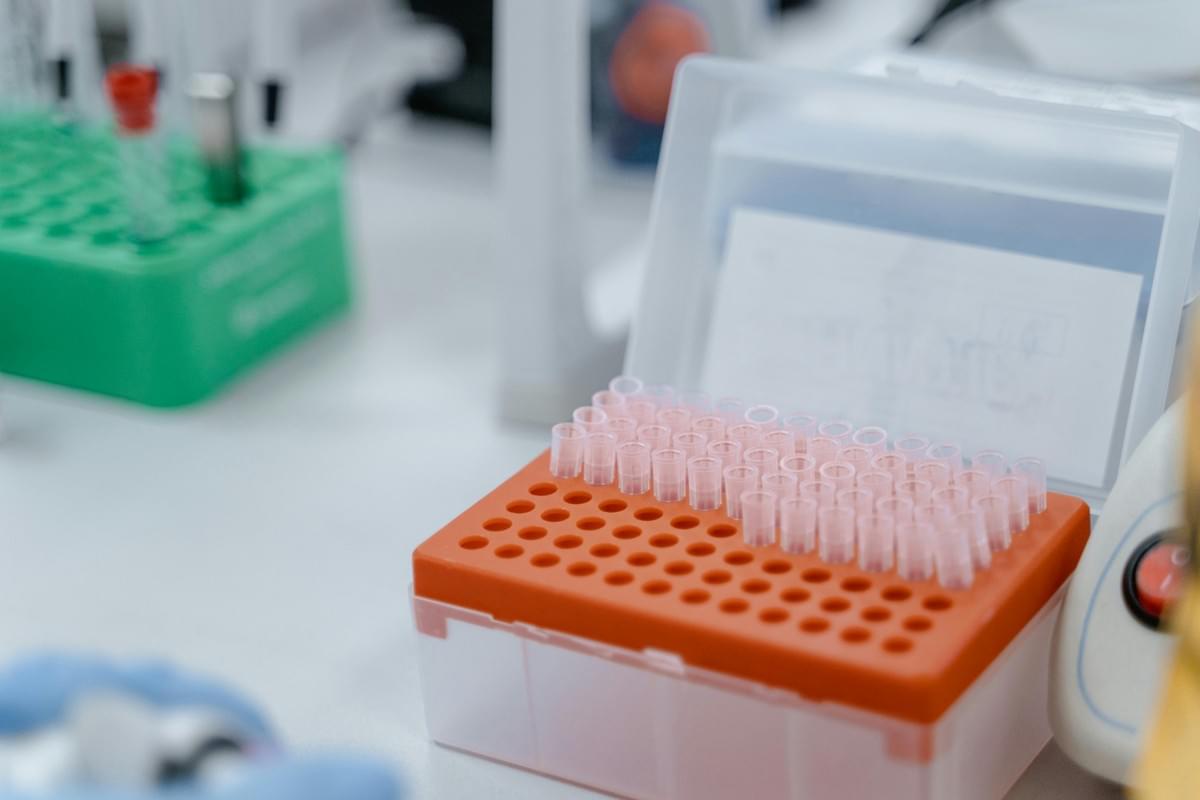
When it comes to toughness in the world of injection molding polymers, Acrylonitrile Butadiene Styrene (ABS) takes the crown. This remarkable plastic is known for its impressive impact resistance and durability, making it a popular choice in various sectors of plastic manufacturing. With its unique blend of properties, ABS stands out as a go-to material for creating robust and long-lasting products.
Properties that Make ABS Stand Out
The standout properties of ABS stem from its chemical composition, which combines acrylonitrile, butadiene, and styrene. This combination results in a material that exhibits excellent tensile strength and rigidity while maintaining flexibility—qualities that are crucial for many applications in injection molding. Additionally, ABS has great resistance to heat and chemicals, ensuring that items made from this polymer can withstand harsh environments without compromising their integrity.
Moreover, ABS is easy to process through standard injection molding equipment, allowing manufacturers to create intricate designs with precision. Its superior surface finish also means that products require less post-processing work compared to other plastics. These characteristics make ABS an ideal candidate for various mold plastic injection applications where both aesthetics and functionality are key.
Role in Plastic Injection Molding
In the realm of plastic injection molding, ABS plays a pivotal role due to its versatility and ease of use with injection molding machines. The ability to flow easily into molds allows for efficient production cycles while minimizing waste—a win-win for manufacturers looking to optimize their processes. Additionally, the consistent quality achieved during the mold plastic injection process ensures that each product meets high standards.
The adaptability of ABS also means it can be blended with other materials or modified with additives to enhance specific properties further—like UV resistance or flame retardance—tailoring it perfectly for diverse applications within different industries. Furthermore, because it can be recycled effectively after use, employing ABS aligns well with sustainable practices in modern plastic manufacturing.
Popular Applications in Consumer Goods
Acrylonitrile Butadiene Styrene finds itself at home across a wide array of consumer goods thanks to its unique attributes as an injection moldable plastic. From household appliances like vacuum cleaners and kitchen gadgets to electronic casings such as computer monitors and gaming consoles—ABS is everywhere! Its ability to maintain structural integrity while providing an aesthetically pleasing finish makes it a favorite among designers and engineers alike.
Additionally, you’ll find ABS used extensively in automotive parts like dashboard components and interior trim pieces due to its lightweight yet sturdy nature. Even toys benefit from this tough polymer; iconic building blocks are often made from high-quality ABS because they need durability while allowing vibrant colors through effective dyeing processes during production.
Polystyrene: The Economical Choice
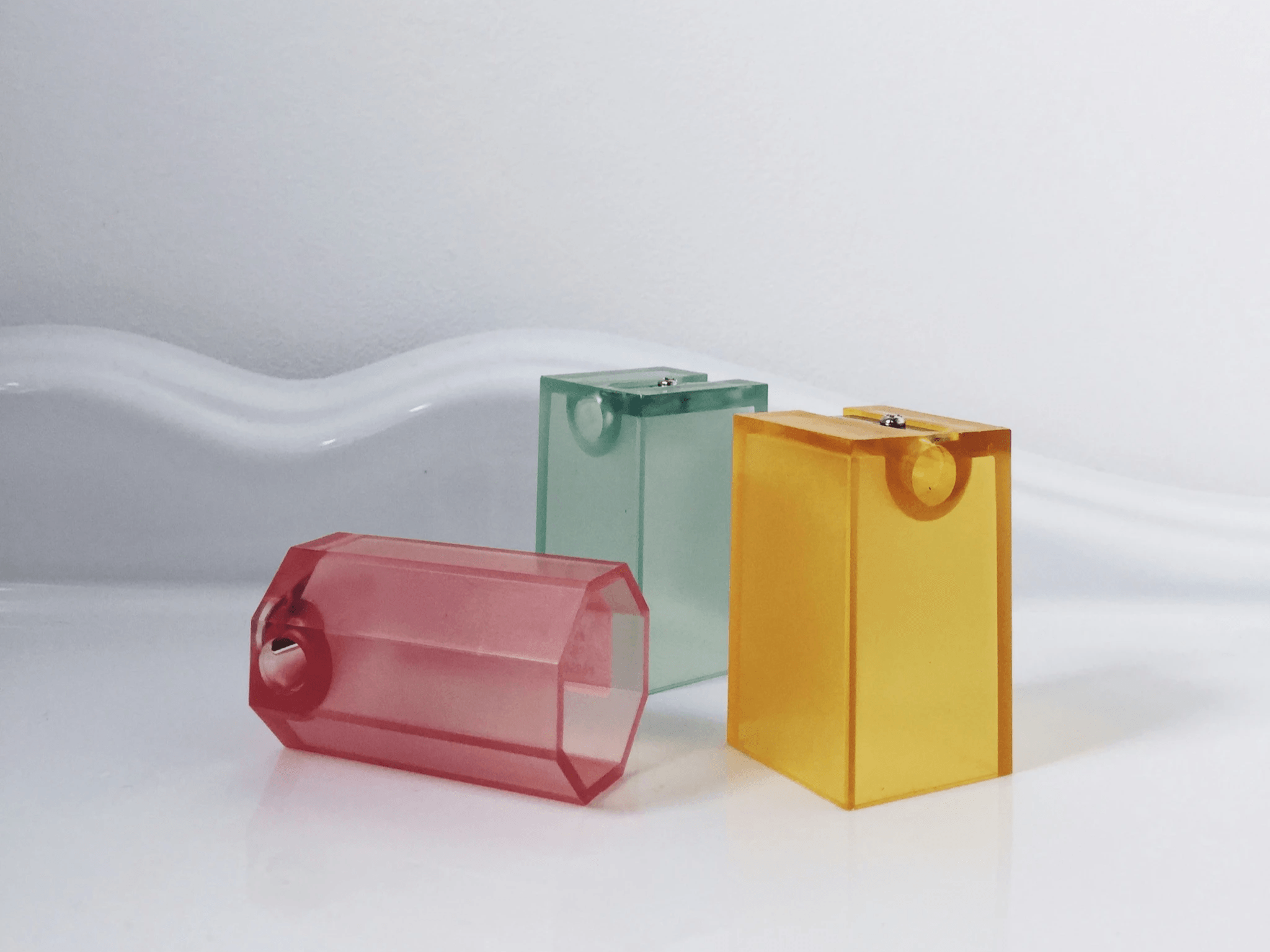
Polystyrene is often hailed as the economical choice among injection molding polymers, thanks to its affordability and versatility. This plastic is lightweight yet durable, making it a popular option in various plastic manufacturing processes. With its wide range of applications, polystyrene continues to be a staple in the world of mold plastic injection.
Types of Polystyrene Used in Molding
There are primarily two types of polystyrene used in injection molding: general-purpose polystyrene (GPPS) and high-impact polystyrene (HIPS). GPPS is transparent and rigid, making it ideal for applications requiring clarity and strength, while HIPS contains rubber additives that enhance its impact resistance. These variations allow manufacturers to choose the most suitable type for their specific needs in plastic injection molding.
Economic Benefits of Polystyrene in Production
One of the standout features of polystyrene is its cost-effectiveness, which significantly reduces production expenses for businesses using injection molding equipment. The material's easy processing characteristics enable faster cycle times on injection molding machines, leading to increased productivity and lower labor costs. Moreover, with less waste generated during production, companies can enjoy additional savings while maintaining quality standards.
Applications from Toys to Packaging
Polystyrene finds its way into an astonishing array of products—from children's toys to food packaging—demonstrating its adaptability across industries. In the realm of consumer goods, items like disposable cutlery and containers showcase polystyrene's practicality and convenience. Additionally, its use in packaging solutions ensures that products remain safe during transit while being lightweight enough to keep shipping costs down.
Nylon: The High-Performance Option
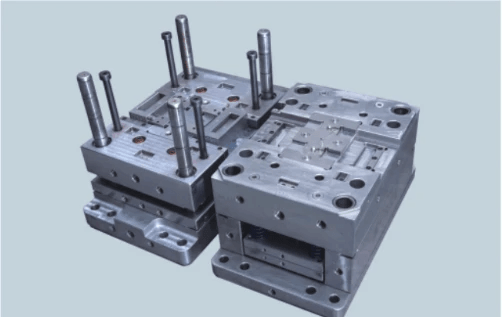
Nylon has carved a niche for itself in the realm of injection molding polymers, thanks to its unique combination of strength, flexibility, and resilience. This high-performance plastic is often the go-to choice for manufacturers looking to create durable products that can withstand rigorous use. When it comes to injection molding equipment, nylon's properties make it an ideal candidate for various applications in plastic manufacturing.
Benefits of Nylon in Injection Molding Equipment
One of the standout benefits of nylon in injection molding is its excellent thermal stability, which allows it to maintain structural integrity even at elevated temperatures. This characteristic makes it particularly suitable for use in injection molding machines that operate under high-stress conditions. Furthermore, nylon's resistance to wear and abrasion enhances the longevity of mold plastic injection components, reducing maintenance costs and downtime during production.
Another advantage is nylon's ability to absorb moisture without compromising its mechanical properties. This feature enables manufacturers to achieve precise tolerances and consistent quality in their products during the plastic injection molding process. Additionally, nylon can be easily modified with additives or fillers, allowing for tailored performance characteristics that meet specific industry requirements.
Strength and Flexibility Features
Nylon boasts impressive tensile strength and flexibility, making it a standout choice among injection moldable plastics. Its unique molecular structure provides excellent impact resistance while allowing for a degree of stretch without breaking—qualities that many other plastics simply cannot match. This balance between strength and flexibility ensures that products made from nylon can endure everyday wear and tear while maintaining their shape.
Moreover, the material's low friction coefficient makes it ideal for applications where parts must slide against one another or move within machinery smoothly. In plastic manufacturing processes like mold plastic injection, this property reduces energy consumption by decreasing resistance during operation. As a result, manufacturers benefit from enhanced efficiency while producing high-quality components.
Industries That Rely on Nylon Components
The versatility of nylon makes it indispensable across various industries that rely on injection molding polymers to create essential components. Automotive manufacturers frequently utilize nylon parts due to their lightweight nature combined with exceptional durability—perfect for everything from gears to fuel lines. Similarly, the electronics industry uses nylon extensively for connectors and housings because these components must withstand heat while ensuring reliable performance.
In addition to automotive and electronics sectors, consumer goods companies also leverage the benefits of nylon in their product designs—from kitchen utensils to sporting equipment—demonstrating its broad applicability across markets. The robust nature of this polymer allows designers and engineers alike the freedom to innovate without sacrificing quality or performance in their final products produced through plastic injection molding techniques.
Conclusion
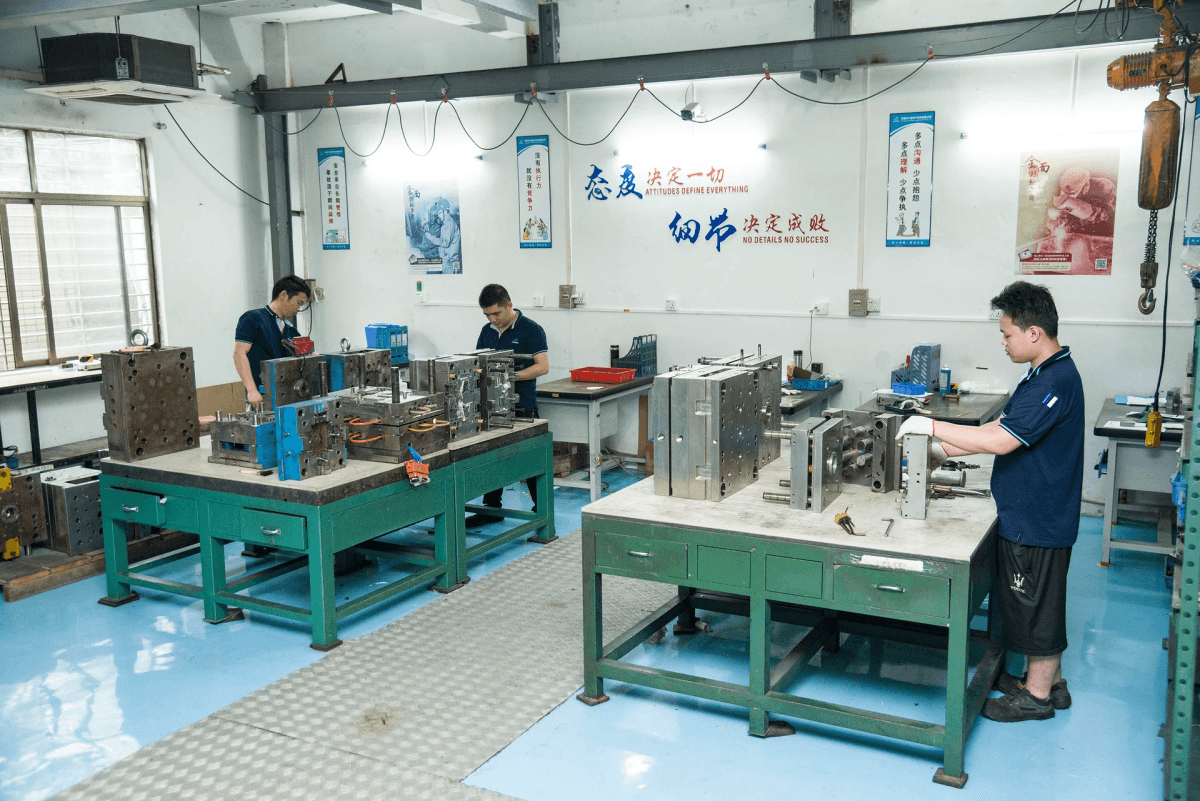
In the realm of plastic manufacturing, understanding injection molding polymers is crucial for selecting the right materials for various applications. From the versatile polypropylene to the lightweight polyethylene and tough ABS, each polymer brings unique characteristics that cater to specific needs in injection molding. As industries continue to evolve, so too will the innovations in injection moldable plastics, making it essential for manufacturers to stay informed.
Key Takeaways on Injection Molding Polymers
Injection molding polymers are foundational to modern plastic production, with each type offering distinct benefits that enhance efficiency and product quality. Polypropylene stands out for its versatility, while polyethylene excels in lightweight applications; both are indispensable in the world of plastic injection molding. Understanding these materials' properties ensures manufacturers can make informed choices that align with their production goals and market demands.
How to Choose the Right Plastic
Choosing the right plastic for mold plastic injection involves evaluating several factors such as mechanical properties, thermal stability, and cost-effectiveness. For instance, if durability is paramount, nylon may be your go-to option due to its high-performance features; conversely, polystyrene could be ideal for budget-conscious projects without compromising quality. Ultimately, aligning your selection with application requirements will enhance performance and optimize production processes using an efficient injection molding machine.
The Future of Plastic Injection Molding
The future of plastic injection molding promises exciting advancements driven by technology and sustainability trends. Innovations in injection molding equipment are likely to improve efficiency while reducing waste—an essential factor as industries face increasing environmental scrutiny. With ongoing research into bioplastics and recycling methods, we can expect a shift toward more sustainable practices within the realm of injection moldable plastics.