Introduction
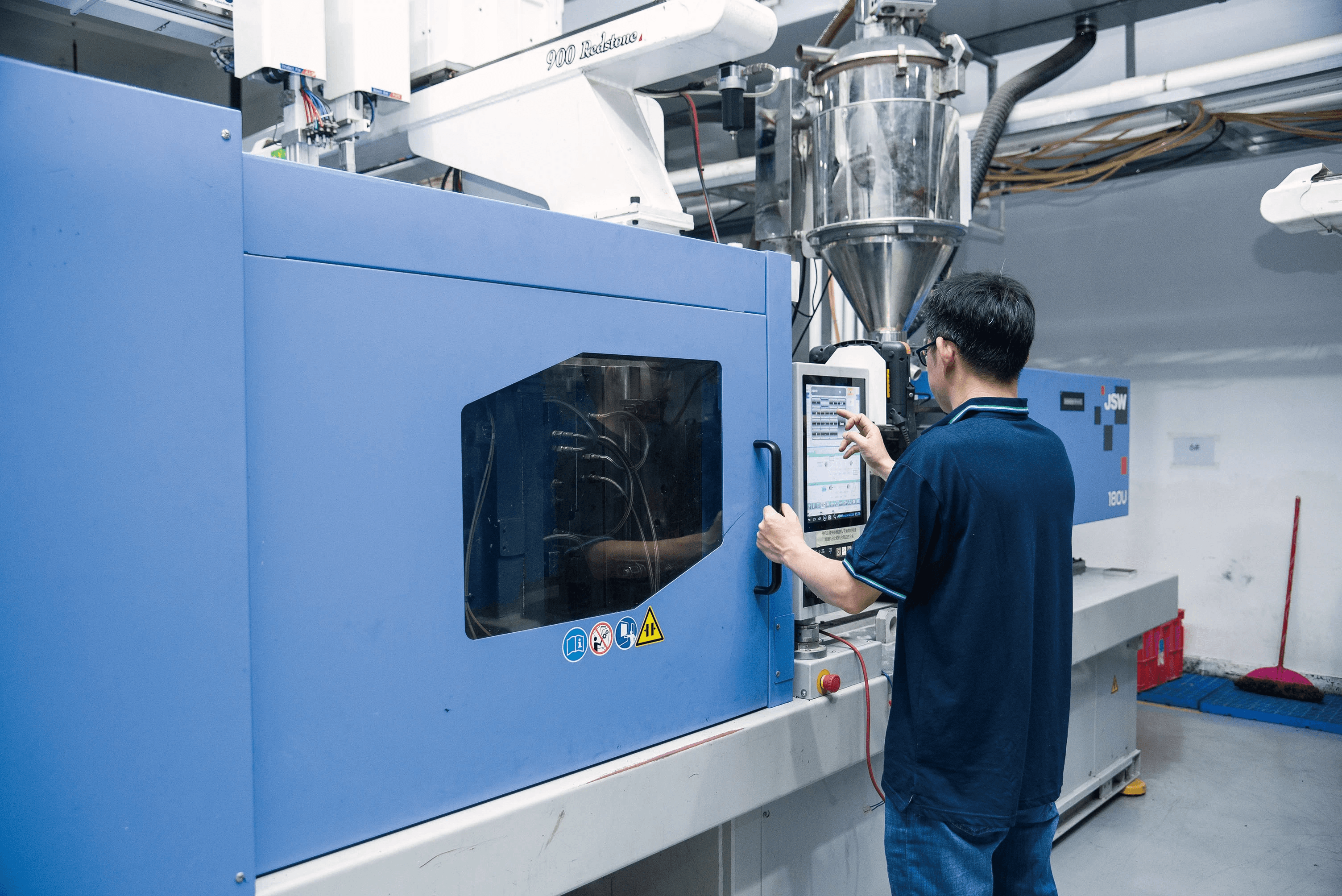
In the ever-evolving landscape of manufacturing, plastic molding stands out as a revolutionary process that has transformed how we produce everyday items. From intricate components in electronics to robust parts in automotive applications, the world of plastic injection molding is vast and versatile. As we delve into this fascinating realm, we'll uncover the myriad types of plastic injection molding and their significance in modern plastic manufacturing.
Discover the World of Plastic Molding
Plastic molding is not just a method; it's an art form that combines creativity with engineering precision. At its core, this process allows manufacturers to create complex shapes and designs from various types of plastic for molding, making it an essential technique across multiple industries. Whether you’re crafting toys or medical devices, understanding the nuances of injection molding can significantly enhance product quality and efficiency.
Key Benefits of Plastic Injection Molding
One of the standout advantages of plastic injection molding is its ability to produce high volumes of consistent and precise plastic products with minimal waste. This efficiency not only reduces production costs but also supports sustainability efforts by maximizing material usage. Furthermore, the process allows for rapid prototyping and customization, enabling businesses to adapt quickly to market demands while maintaining high standards.
Overview of Injection Moldable Plastics
Injection moldable plastics come in various forms, each suited for specific applications within the manufacturing spectrum. Common materials include thermoplastics like ABS and polycarbonate, which are favored for their durability and flexibility during processing. Understanding these materials is crucial as they directly influence the performance characteristics and overall quality of the final product produced through injection molding.
What is Plastic Injection Molding?
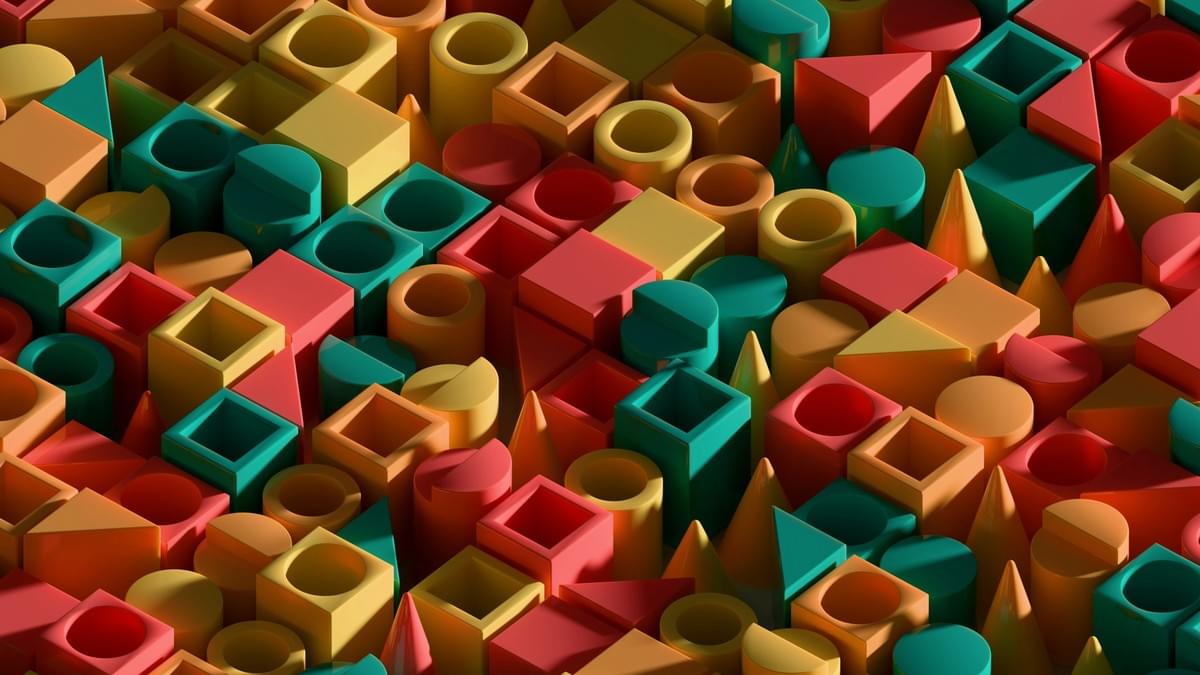
Plastic injection molding is a manufacturing process that transforms raw plastic into finished products through the use of specialized machinery. This technique is favored for its efficiency and ability to produce high volumes of identical plastic products with intricate designs. Understanding the fundamentals of this process can illuminate the vast potential it holds in plastic manufacturing.
The Basics Explained
At its core, plastic injection molding involves melting down plastic pellets, injecting them into a mold, and allowing them to cool and solidify into the desired shape. The process begins with an injection molding machine that heats the plastic until it becomes pliable, then forces it under high pressure into a mold cavity. This method enables manufacturers to create complex shapes and structures that would be challenging or impossible to achieve with other techniques.
The versatility of injection moldable plastics is one of its strongest suits; they can be engineered for various applications, from consumer goods to automotive parts. Additionally, this method allows for rapid production cycles, making it ideal for industries that require large quantities of uniform products quickly. Whether you're looking at single-color or specialty types of plastic injection molding, each method has unique advantages tailored to specific needs.
How Injection Molding Works
Injection molding starts with selecting the appropriate type of plastic for molding based on the final product's requirements—this could be anything from durability to flexibility. Once selected, the raw material is fed into an extruder where it's heated and melted before being injected into a pre-designed mold at high pressure. As the molten plastic fills the mold cavity, it takes on its shape and begins cooling almost immediately.
After sufficient cooling time has passed—typically just a few seconds—the mold opens up to release the finished product. This quick turnaround is what makes injection molding such a popular choice in modern manufacturing processes; however, precision in temperature control and timing are crucial for achieving quality results consistently. The entire cycle—from melting to cooling—can often be repeated multiple times per hour depending on machine capabilities.
Common Applications in Various Industries
Plastic injection molding finds applications across numerous industries due to its adaptability and efficiency in producing custom parts at scale. For instance, in consumer goods manufacturing, everything from toy components to kitchen utensils often relies on this versatile process for mass production without compromising quality or design intricacies. Similarly, automotive manufacturers utilize injection molded plastics extensively for dashboard components, bumpers, and even internal mechanisms.
In medical device production as well as electronics sectors, precision becomes paramount; here too, types of plastic injection molding come into play by allowing engineers to create highly detailed components that meet stringent safety standards while remaining cost-effective. Additionally, packaging solutions benefit greatly from this method since it allows companies to produce lightweight yet durable containers quickly—perfect for fast-paced retail environments!
Overall, whether you’re crafting everyday items or specialized equipment parts using an injection molding machine ensures efficient production tailored precisely to market demands.
Types of Plastic Injection Molding
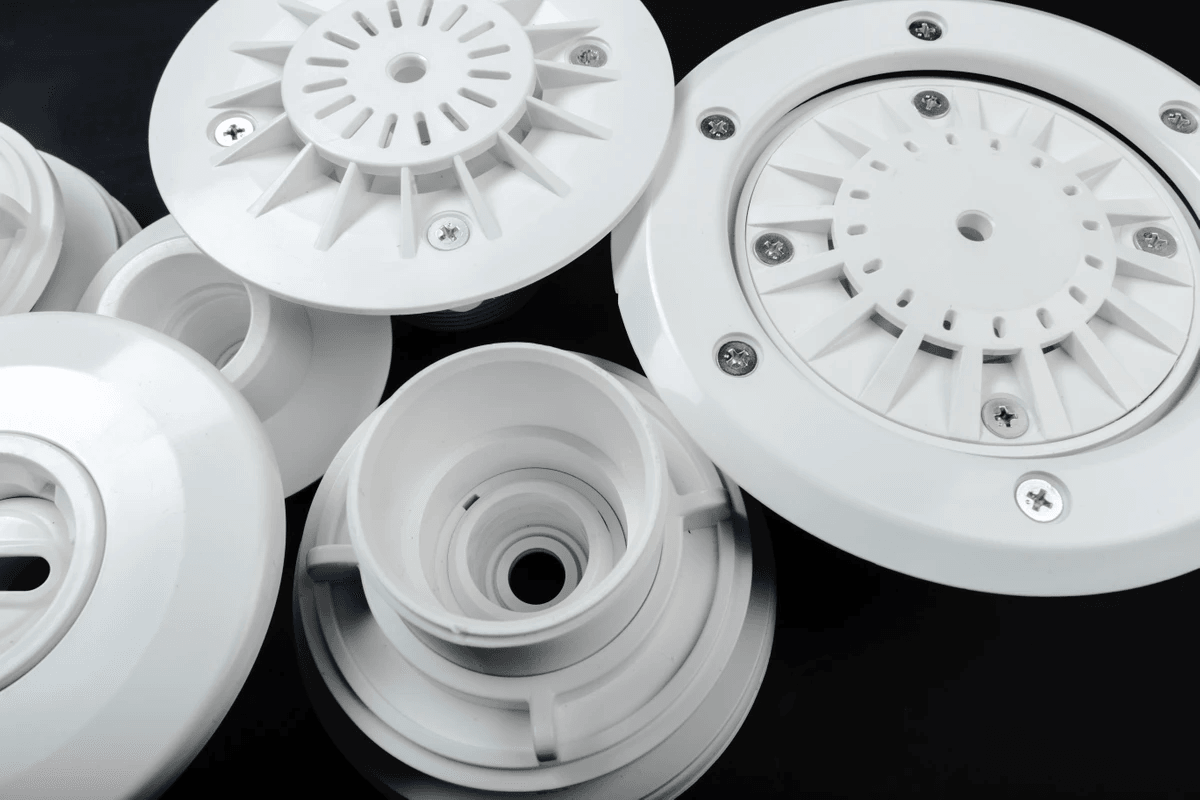
When it comes to plastic manufacturing, understanding the various types of plastic injection molding is essential for creating high-quality plastic products. Each technique offers unique advantages and caters to different needs in the production process. Whether you’re looking for single-color simplicity or intricate multi-color designs, there’s an injection molding method that fits the bill.
Single-Color Injection Molding
Single-color injection molding is the most straightforward and widely used method in plastic manufacturing. This technique involves injecting a single type of molten plastic into a mold to create uniform products with consistent quality. It's particularly popular for creating everyday items like containers, toys, and automotive parts where color variety isn’t a priority.
One major advantage of single-color injection molding is its efficiency; it simplifies the production process and reduces cycle times, which can lead to cost savings. Additionally, using one type of injection moldable plastics minimizes complexity in material handling and machine setup, making it ideal for mass production runs. However, while it may lack visual flair compared to other methods, its reliability makes it a staple in many industries.
Double-Color Injection Molding
Double-color injection molding takes things up a notch by allowing two different colors or types of plastic to be injected into a single mold during the same cycle. This technique not only enhances aesthetic appeal but also enables manufacturers to create more complex designs that can include functional features like soft-touch grips or integrated branding elements. It’s particularly useful for producing items like toothbrushes or automotive interior components where both form and function are crucial.
The beauty of double-color injection molding lies in its versatility; you can combine materials with different properties—like rigidity and flexibility—within one product, leading to innovative designs that stand out from competitors. However, this method requires specialized equipment such as dual-shot injection molding machines, which can increase initial investment costs but often pay off through higher-value products and reduced assembly time later on.
Specialty Molding Techniques
Specialty molding techniques encompass a range of advanced methods designed to meet specific requirements in plastic manufacturing beyond standard practices. These techniques include gas-assisted injection molding for hollow parts or insert molding that allows metal components to be encapsulated within plastic products seamlessly. Such innovations expand the possibilities for designers and engineers alike.
Using specialty techniques often results in lighter yet stronger products with enhanced functionality tailored precisely to user needs—think about ergonomic tools or intricate electronic housings! While these methods may require more sophisticated machinery and expertise (hello advanced injection molding machine), they ultimately offer solutions that traditional methods might struggle with achieving alone. The investment in these technologies pays dividends when considering performance improvements across various applications.
Materials Used in Plastic Manufacturing
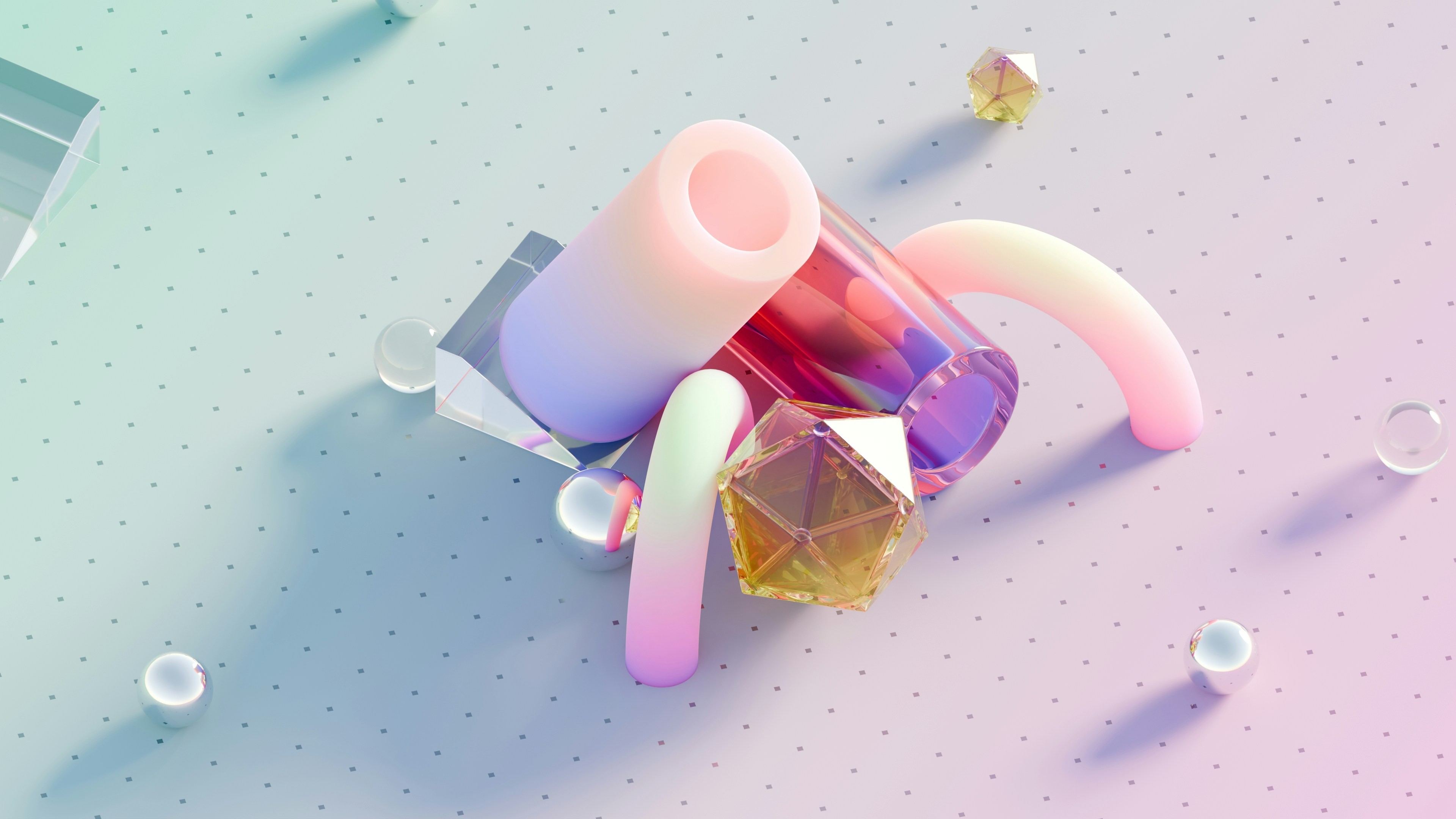
When it comes to plastic manufacturing, the choice of materials is paramount. The right injection moldable plastics can significantly impact the performance and durability of the final product. Understanding the various types of plastic injection molding materials available helps manufacturers select the best options for their specific needs.
Popular Injection Moldable Plastics
Among the most popular injection moldable plastics are Polypropylene (PP), Acrylonitrile Butadiene Styrene (ABS), and Polyethylene Terephthalate (PET). Each of these materials offers unique properties that make them suitable for different applications in plastic manufacturing. For instance, PP is known for its excellent chemical resistance and flexibility, while ABS is favored for its toughness and impact resistance—ideal for making durable plastic products.
Moreover, PET stands out due to its excellent clarity and strength, making it a go-to choice for packaging applications. Other notable mentions include Polystyrene (PS) for lightweight applications and Nylon for high-strength components. Selecting the right type of plastic injection molding material ensures that manufacturers meet both functional requirements and aesthetic considerations.
Comparing Thermoplastics and Thermosets
In the world of plastic manufacturing, understanding the difference between thermoplastics and thermosets is crucial when choosing materials for injection molding. Thermoplastics are characterized by their ability to be melted down and reshaped multiple times without losing structural integrity; this versatility makes them ideal for a variety of types of plastic injection molding processes. Examples include PVC, which is widely used in construction due to its durability.
On the other hand, thermosets undergo a chemical change when heated, resulting in a rigid structure that cannot be remelted or reshaped once set—making them perfect for applications requiring high heat resistance or structural stability. This fundamental difference impacts how each type behaves during processing with an injection molding machine as well as their end-use characteristics in various industries like automotive or electronics.
The Role of Fillers and Additives
Fillers and additives play a significant role in enhancing the properties of injection moldable plastics used in various types of plastic injection molding processes. Fillers such as talc or calcium carbonate can improve strength while reducing costs by replacing some resin content without compromising quality—a win-win situation for manufacturers seeking efficiency! Meanwhile, additives like UV stabilizers or flame retardants help tailor performance characteristics to meet specific application requirements.
Additionally, colorants can be added to provide aesthetic appeal without affecting functionality—perfectly blending form with function in your finished plastic products! Ultimately, understanding how fillers and additives interact with base polymers allows manufacturers to optimize their formulations effectively during production processes involving an injection molding machine.
The Importance of Injection Molding Machines
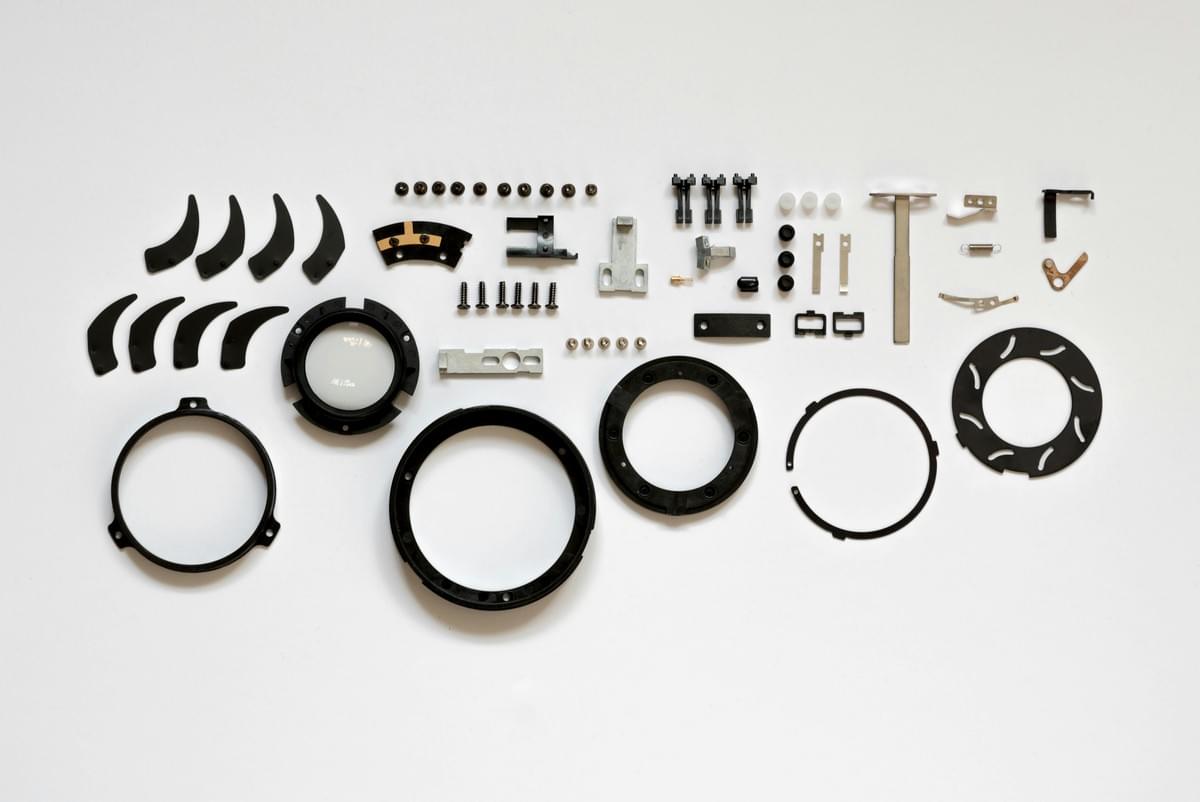
When it comes to plastic manufacturing, injection molding machines are the unsung heroes of the process. These machines are designed to inject molten plastic into molds, shaping it into various forms and sizes, which is essential for producing high-quality plastic products. Understanding how these machines function can significantly impact the efficiency and quality of your production line.
How They Function in the Process
Injection molding machines operate through a series of well-coordinated steps that begin with heating the plastic for molding until it reaches a molten state. This molten plastic is then injected into a mold cavity under high pressure, allowing it to take on the desired shape as it cools and solidifies. The precision and speed at which these machines work enable manufacturers to produce large volumes of consistent and intricate designs, making them vital in various industries that utilize injection moldable plastics.
Choosing the Right Machine for Your Needs
Selecting an injection molding machine isn't just about picking the biggest or most expensive option; it's about finding one that aligns with your specific requirements. Factors such as part size, material type, production volume, and cycle time all play critical roles in determining which machine is right for your project. Additionally, understanding different types of plastic injection molding—like single-color or double-color options—can help you choose machinery that best suits your product goals.
Maintenance Tips for Optimal Performance
To keep your injection molding machine running smoothly and efficiently, regular maintenance is key. This includes routine checks on hydraulic systems, ensuring proper lubrication of moving parts, and monitoring temperature controls to prevent overheating during operation. By following these maintenance tips diligently, you can extend the lifespan of your machine while minimizing downtime—a crucial factor in maintaining productivity in plastic manufacturing.
Quality Assurance in Plastic Products
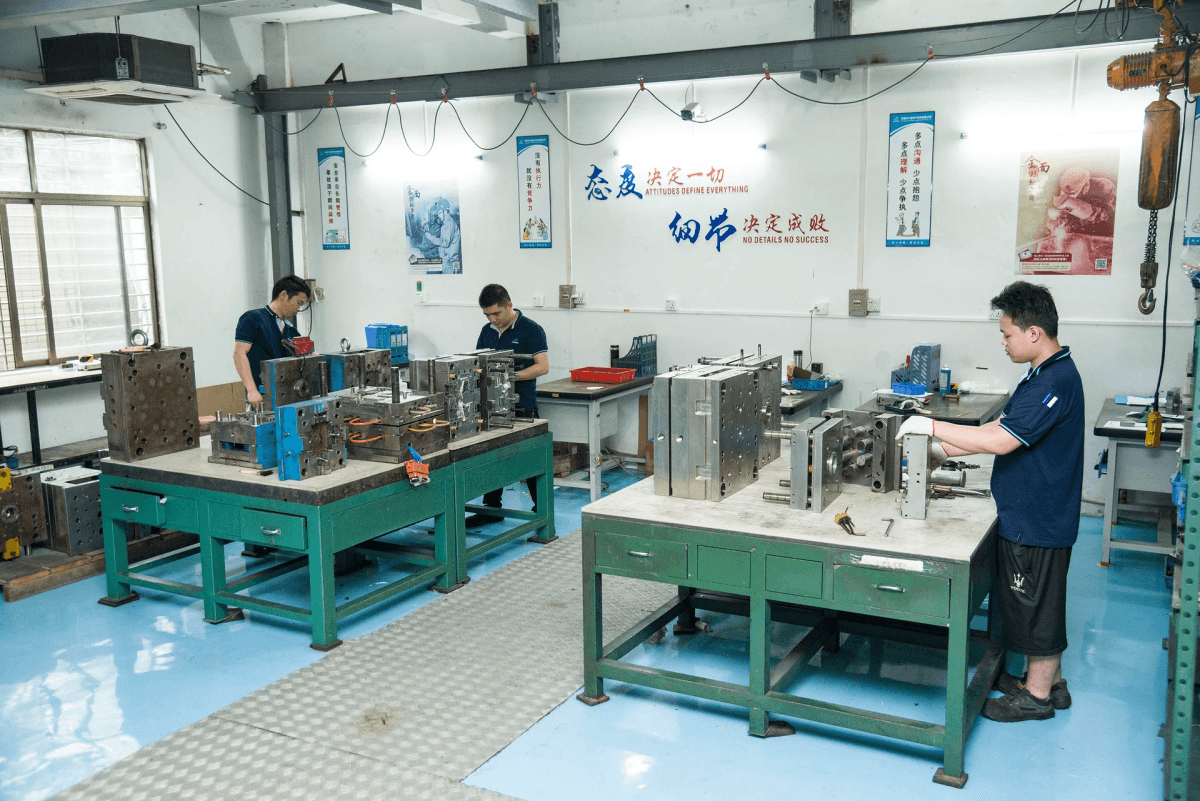
In the world of plastic manufacturing, quality assurance is paramount to ensure that the final products meet industry standards and customer expectations. This involves a rigorous process of monitoring and evaluating every stage of production, from the selection of injection moldable plastics to the final inspection of plastic products. By adhering to best practices, manufacturers can significantly reduce defects and enhance overall product reliability.
Best Practices for Production Quality
To achieve high production quality in plastic injection molding, several best practices should be implemented consistently. First and foremost, selecting appropriate types of plastic injection molding techniques is crucial; each method can yield different results based on material properties and desired outcomes. Additionally, regular calibration and maintenance of injection molding machines are essential to prevent mechanical failures that could compromise product integrity.
Another important aspect involves establishing a robust quality management system that includes documentation and traceability throughout the manufacturing process. This ensures that any issues can be quickly identified and rectified without impacting large batches of plastic for molding. Continuous training for staff involved in production also plays a vital role in maintaining quality standards, as knowledgeable employees are better equipped to spot potential problems before they escalate.
Role of the Baoyuan Team in Quality Control
The Baoyuan team plays an instrumental role in upholding stringent quality control measures within the realm of plastic manufacturing. Their expertise spans various aspects of production—from selecting the right materials for injection moldable plastics to overseeing each phase of the injection molding process with meticulous attention to detail. By employing experienced professionals who understand both technical specifications and market demands, Baoyuan ensures that all plastic products meet or exceed customer expectations.
Moreover, their proactive approach includes conducting regular audits and assessments throughout production runs, which helps identify areas for improvement before they become significant issues. The team utilizes advanced technologies alongside traditional methods to monitor processes closely—ensuring consistent output quality across different types of plastic injection molding projects. Their commitment not only enhances product reliability but also builds trust with clients seeking high-quality solutions.
Testing Methods for Ensuring Durability
Ensuring durability in plastic products requires a comprehensive suite of testing methods designed to evaluate performance under various conditions. Common testing techniques include tensile strength tests, impact resistance evaluations, and thermal stability assessments—each tailored specifically for different types of plastic injection molding applications. These tests help manufacturers ascertain how well their products will withstand real-world usage scenarios while identifying any weaknesses that may need addressing.
Additionally, non-destructive testing methods are employed to assess internal structures without compromising product integrity—a vital step when dealing with complex geometries often found in advanced injection moldable plastics designs. Regularly scheduled testing not only guarantees compliance with industry regulations but also reinforces consumer confidence in the durability and safety of finished goods produced through effective injection molding practices.
Ultimately, by combining best practices with dedicated teams like Baoyuan's and thorough testing protocols, manufacturers can deliver superior-quality plastic products that stand up to scrutiny while meeting diverse market needs.
Conclusion
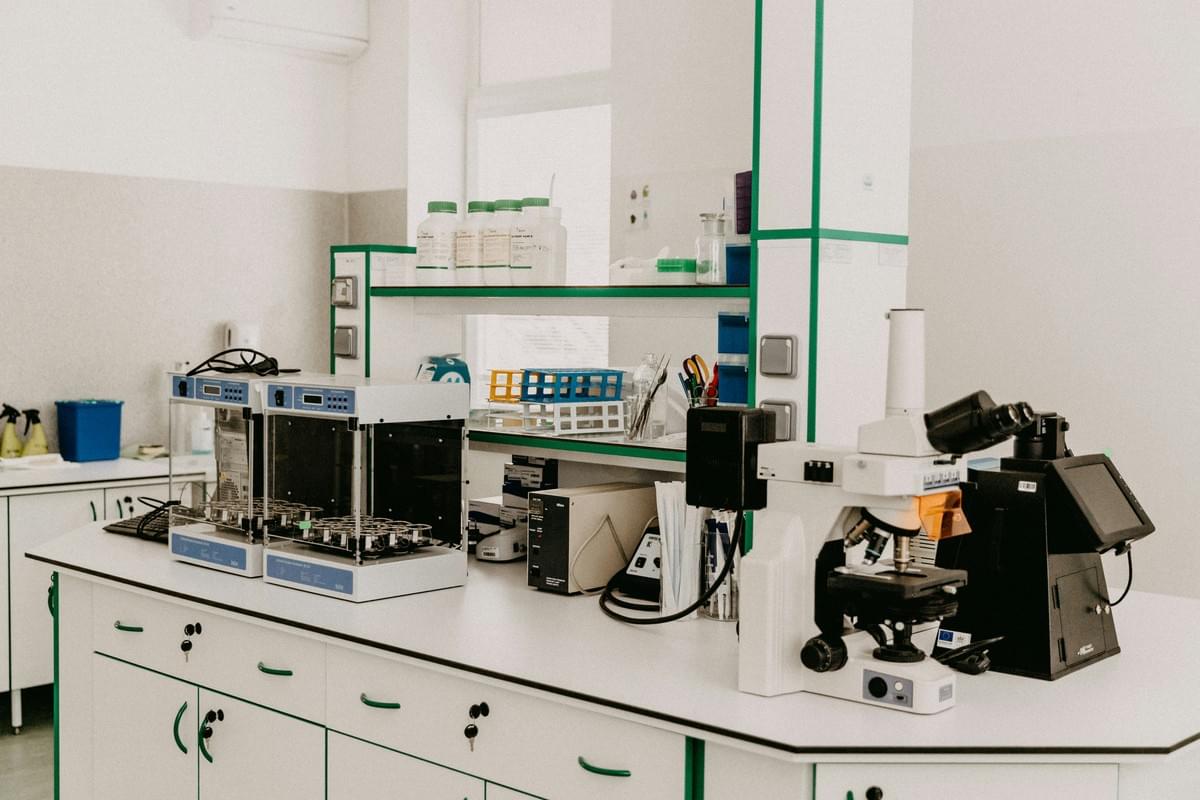
In the world of plastic manufacturing, understanding the various types of plastic injection molding is crucial for selecting the right methods and materials. From single-color to double-color and specialty techniques, each type offers unique benefits tailored to different applications. As we wrap up this exploration, it’s clear that injection molding stands as a cornerstone in producing high-quality plastic products efficiently.
Recap of Molding Types and Techniques
We’ve delved into several types of plastic injection molding, each designed to meet specific needs in diverse industries. Single-color injection molding is ideal for straightforward designs, while double-color options allow for more creativity and functionality in product design. Specialty molding techniques further expand possibilities by accommodating unique shapes and material combinations, making them invaluable in today’s competitive market.
Future Trends in Plastic Manufacturing
Looking ahead, the future of plastic manufacturing is poised for exciting advancements driven by sustainability and innovation. Biodegradable plastics and recycled materials are gaining traction as manufacturers seek eco-friendly alternatives to traditional plastics used in injection molding processes. Moreover, advancements in technology such as automation and smart manufacturing will streamline production processes, enhancing efficiency while maintaining high standards for quality assurance.
How to Choose the Right Injection Molding Method
Selecting the right injection molding method requires a careful evaluation of your project requirements and desired outcomes. Consider factors like material compatibility with your chosen types of plastic injection molding, production volume needs, and budget constraints when deciding on an approach. Consulting with experts or suppliers can provide valuable insights into which techniques—be it standard or specialty—will best suit your goals for creating durable plastic products.