Introduction
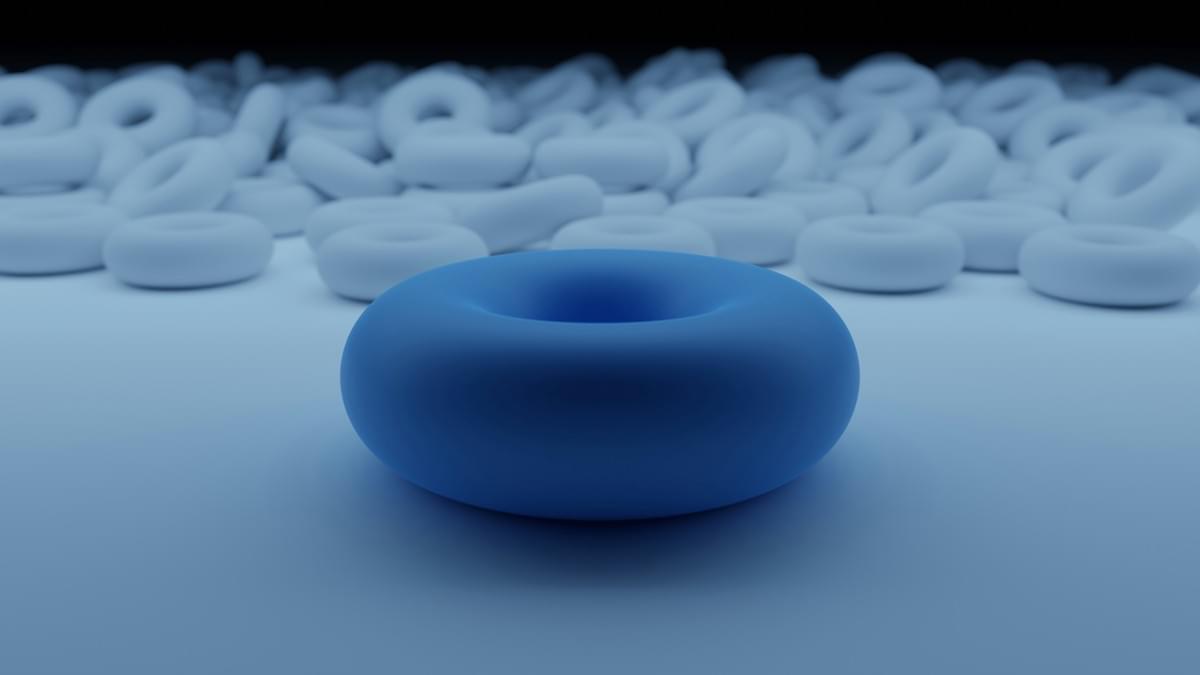
In the world of manufacturing, plastic injection moulding stands out as a revolutionary technique that has transformed how products are made. This process involves injecting molten material into a mould to create high-quality components with precision and efficiency. With the rising demand for durable products, understanding the nuances of hard plastic injection molding is crucial for manufacturers looking to optimize their operations.
Understanding Plastic Injection Moulding
Plastic injection moulding is not just about pouring plastic into a shape; it's about creating high-density plastics that can withstand wear and tear while maintaining structural integrity. The process utilizes various types of plastics, including high-density polyethylene, known for its strength and resistance to impact. By mastering this technique, manufacturers can produce everything from intricate parts to robust containers that meet diverse industry needs.
The Role of Tooling in Manufacturing
Tooling plays an essential role in the success of any manufacturing process, particularly in mould injection moulding. The right tooling determines the efficiency and quality of production runs, impacting everything from design flexibility to material usage. Whether utilizing hard or soft tooling, understanding their implications on production is key for businesses aiming to enhance their manufacturing capabilities.
A Dive into Hard vs Soft Tooling
Hard tooling typically involves robust materials designed for high-density plastic applications, offering durability but at a higher cost upfront. On the other hand, soft tooling provides flexibility and cost-effectiveness but may not be suitable for all production scenarios—each option has its place in the landscape of injection casting and mould plastic injection processes.
Defining Hard Tooling
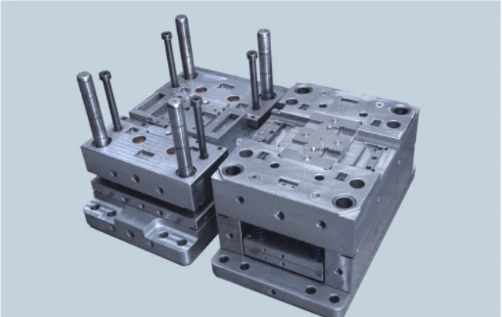
Characteristics of Hard Tooling
Hard tooling is characterized by its robust construction and longevity, making it ideal for high-density plastic applications. These molds are typically machined with high precision, allowing for intricate designs and features in products made from materials like high-density polyethylene (HDPE). Additionally, hard tooling can endure higher temperatures and pressures during the injection casting process, ensuring minimal wear over time.
Another notable feature is the ability to produce parts with superior surface finishes. This characteristic is particularly advantageous when working with hard plastic injection molding, where aesthetics and functionality need to coexist seamlessly. In essence, hard tooling combines durability with precision to deliver top-notch results in plastic manufacturing.
Applications in Plastic Manufacturing
Hard tooling finds its niche across a wide range of applications within the plastic manufacturing sector. From automotive components to consumer goods, this method is crucial for producing parts that require both strength and durability. Industries such as aerospace and electronics also benefit from hard plastic injection molding due to its ability to create complex geometries while maintaining structural integrity.
High-density polyethylene products are especially popular in sectors requiring resistance to impact and chemicals—think packaging solutions or industrial containers. The versatility of hard tooling allows manufacturers to cater to specific requirements while ensuring efficiency in production processes through mould plastic injection techniques.
Benefits of High Density Plastic
One of the standout advantages of utilizing high-density plastics in conjunction with hard tooling is their impressive strength-to-weight ratio. This means that products made from HDPE can be lightweight yet incredibly tough—perfect for applications where durability matters most without adding unnecessary bulk. Furthermore, high-density plastics exhibit excellent resistance to moisture and chemicals, making them ideal for a variety of environments.
The use of high polyethylene not only enhances product performance but also contributes positively to sustainability efforts; many HDPE materials are recyclable after their lifecycle ends. This eco-friendly aspect aligns well with modern manufacturing trends focused on reducing waste while maintaining quality standards through efficient processes like injection casting.
In summary, hard tooling plays a pivotal role in shaping the landscape of plastic manufacturing by offering unparalleled characteristics suited for producing high-density plastics that meet diverse industry needs effectively.
Exploring Soft Tooling
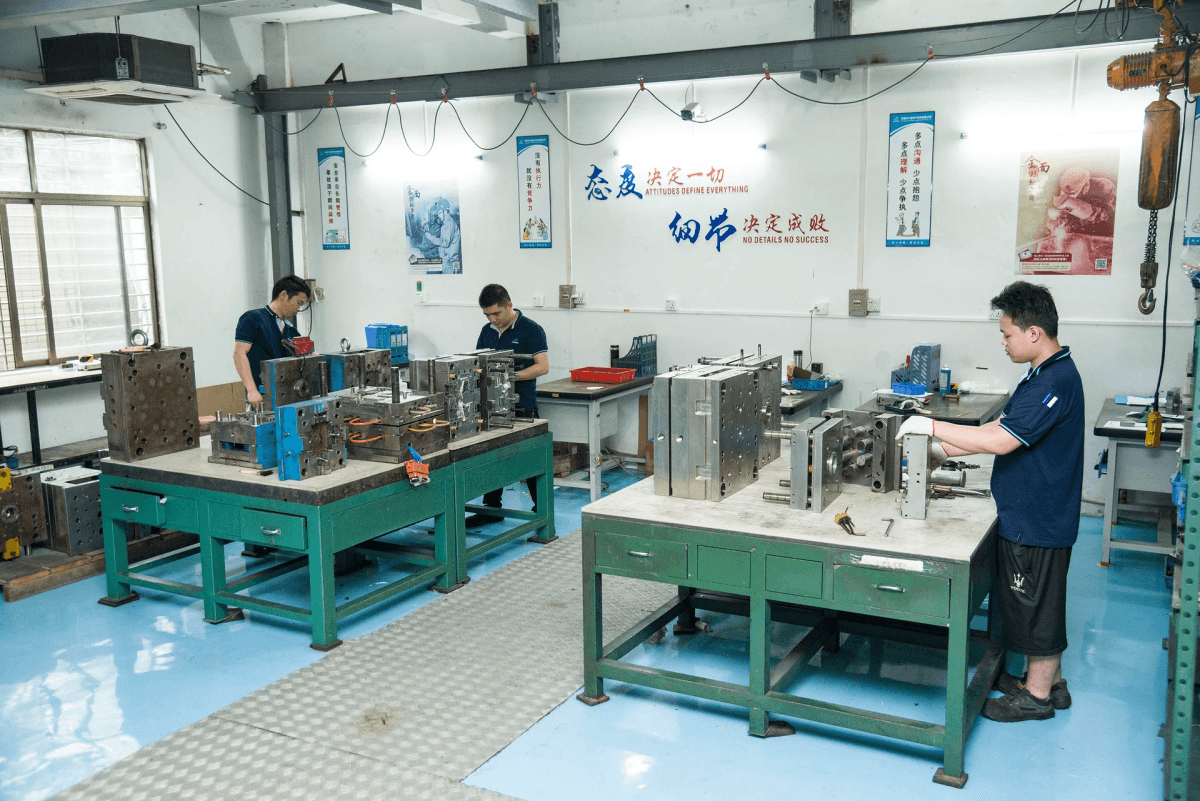
Soft tooling is a fascinating approach in the realm of plastic manufacturing, offering a flexible alternative to its hard counterpart. Unlike hard tooling, which typically involves the creation of durable steel molds, soft tooling often utilizes materials such as aluminum or even silicone for mold production. This flexibility allows manufacturers to adapt quickly to design changes and produce lower volumes of parts without the hefty investment typically associated with hard plastic injection molding.
Features of Soft Tooling
One of the standout features of soft tooling is its relatively quick turnaround time from design to production. The materials used for soft tools are generally easier to work with and can be machined or cast rapidly, allowing for faster prototyping in high-density polyethylene applications. Additionally, soft tooling can accommodate intricate designs that may be challenging with traditional hard molds, making it an attractive option for complex projects in mould injection moulding.
Another appealing aspect is that soft tooling can often be produced at a fraction of the cost compared to hard tooling. This cost efficiency stems from both reduced material expenses and shorter machining times involved in creating these molds. Furthermore, while they may not withstand the same level of wear as their hard counterparts, advancements in material science have led to improved durability in some soft tool applications.
Ideal Use Cases for Soft Tooling
Soft tooling shines brightest in scenarios where speed and flexibility are paramount—perfectly suited for short-run production or prototyping phases before transitioning into high-density plastic mass production. For instance, industries like automotive or consumer electronics often rely on this approach when developing new products that require rapid testing and iteration cycles before finalizing designs with more robust hard tools.
Additionally, soft tooling is ideal for products made from high-density polyethylene where precision isn’t compromised by lower volume demands; it allows manufacturers to explore various designs without committing significant resources upfront. Companies looking to test market viability through small batches can leverage this method effectively while keeping costs manageable.
Cost-Effectiveness of Soft Tooling
The financial implications of choosing soft tooling over hard tooling cannot be overstated—especially when considering initial investments versus long-term returns in plastic manufacturing processes like injection casting and mould plastic injection projects. With lower upfront costs due to cheaper materials and simpler manufacturing processes, companies can allocate funds toward other critical areas like marketing or research and development.
Moreover, while the lifespan of a soft tool may not match that of a steel mold used in hard plastic injection molding applications, it compensates through its ability to pivot quickly based on project needs without incurring prohibitive costs related to re-tooling or redesigns. In many cases, businesses find themselves saving money overall by utilizing soft tools during early product lifecycles before committing fully developed products into high-density plastic markets.
In summary, exploring soft tooling reveals a world where flexibility meets cost-effectiveness—a necessary balance as industries evolve at breakneck speeds demanding innovative solutions without sacrificing quality.
Comparing Durability and Longevity
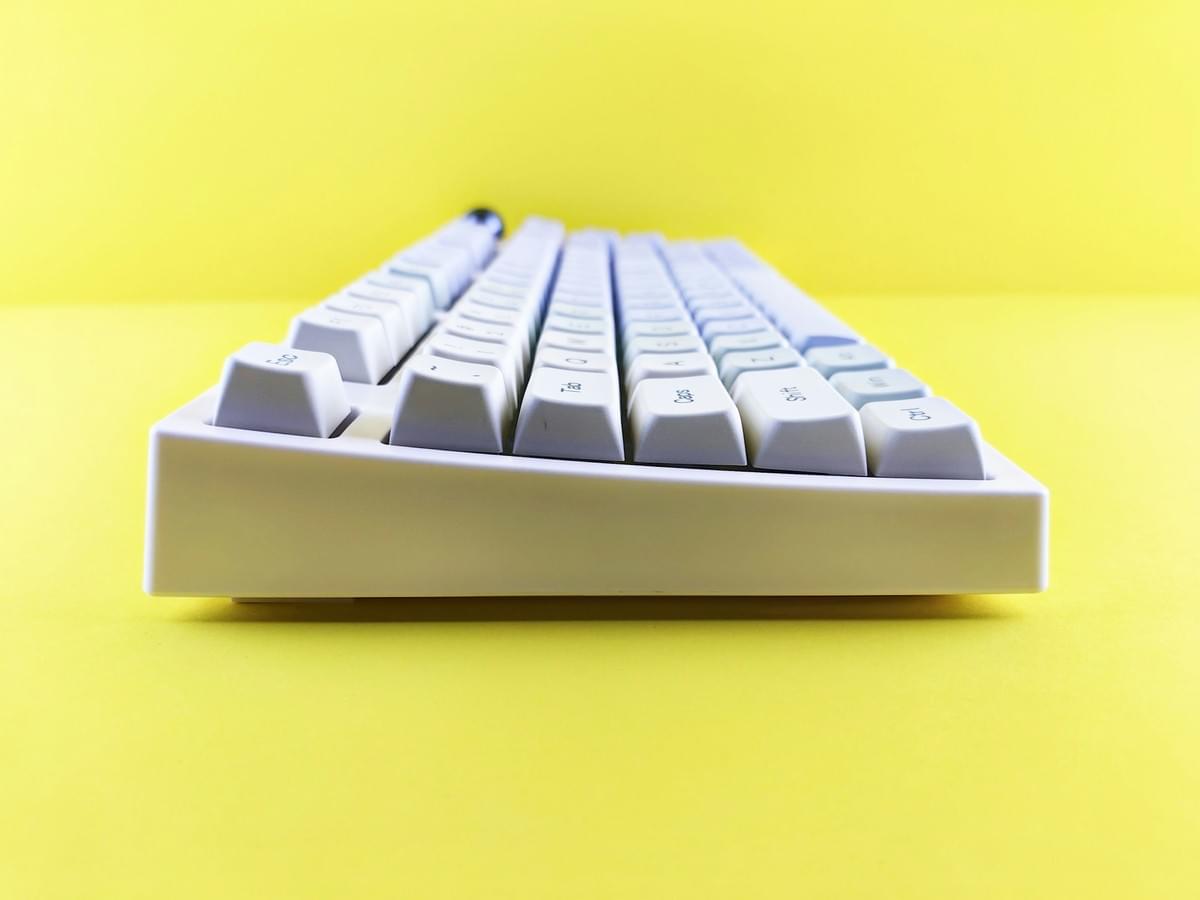
Hard Tooling vs Soft Tooling Durability
Hard tooling is crafted from robust materials like steel or aluminum, designed to endure the pressures of high-density plastic injection molding processes. This durability translates into longer tool life, especially when producing parts from high-density polyethylene (HDPE) or other tough materials. On the flip side, soft tooling often uses less durable materials such as silicone or lower-grade metals, which can lead to wear and tear after fewer cycles.
Factors Affecting Tool Life
Several factors come into play when determining the longevity of both hard and soft tooling in mould injection moulding processes. The type of material used—especially when dealing with high-density plastics—can influence how well a tool holds up over time. Additionally, environmental conditions such as temperature fluctuations and humidity levels can affect the performance of both hard polyethylene and soft materials during production runs.
Real-World Examples of Tool Performance
In practical applications, real-world examples illustrate how hard plastic injection molding outperforms in terms of longevity compared to soft tooling scenarios. For instance, manufacturers using hard tools for creating parts from high-density polyethylene have reported significantly fewer failures than those relying on softer tools for similar tasks. These performance metrics highlight that while initial costs may be higher for hard tooling, the long-term reliability makes it a worthy investment in many cases.
Production Speed and Efficiency

In the world of plastic manufacturing, speed and efficiency are key drivers of success. The choice between hard and soft tooling can significantly impact the production timeline and overall output. Understanding how these tooling types affect manufacturing processes is essential for making informed decisions.
Speed Comparisons Between Tooling Types
When it comes to speed, hard plastic injection molding typically outpaces soft tooling methods in terms of production rates. Hard tooling allows for rapid cycles due to its robust construction, which can withstand high-pressure conditions without deforming. On the other hand, while soft tooling may offer flexibility in design alterations, it often results in slower cycle times due to material limitations and potential wear.
High density polyethylene (HDPE) is frequently utilized with hard tooling because of its ability to maintain structural integrity during fast-paced production runs. This means that manufacturers can produce a larger volume of parts in a shorter timeframe using hard plastic injection molding techniques. In contrast, soft tooling might be better suited for smaller batches or prototypes where speed is less critical.
The Impact on Manufacturing Timelines
The choice between hard and soft tooling directly influences manufacturing timelines from project inception to delivery. Hard mould injection moulding tends to streamline processes as it requires fewer adjustments once set up, leading to more predictable lead times for high density plastic products. Conversely, soft tooling often necessitates multiple iterations before reaching an optimal design, extending project timelines.
When manufacturers opt for high polyethylene materials with hard tools, they often find that their production schedules become more efficient due to reduced downtime and maintenance needs associated with durable tools. Additionally, quicker turnaround times can enhance customer satisfaction by delivering products faster than competitors who rely on softer options. Thus, selecting the right type of tooling not only affects immediate output but also long-term business relationships.
Case Studies in Injection Casting
Examining real-world examples highlights how different tooling choices impact production efficiency in injection casting scenarios. For instance, a company specializing in automotive components switched from soft tooling to hard plastic injection molding for their high density polyethylene parts and reported a 30% increase in output within just three months. This transition allowed them not only to meet growing demand but also to reduce costs associated with frequent tool replacements.
Another case study involved a consumer goods manufacturer that initially used soft tools for prototype testing but later adopted hard mould injection moulding for mass production after validating designs through initial runs. The switch resulted in significant time savings and improved product quality since the rigid molds produced consistent results across large batches without sacrificing detail or durability.
In summary, when considering production speed and efficiency within plastic manufacturing contexts like injection casting or mould plastic injection processes, the differences between hard and soft tooling are substantial—favoring those who prioritize quick turnaround times without compromising quality or performance.
The Financial Implications of Tooling Choices
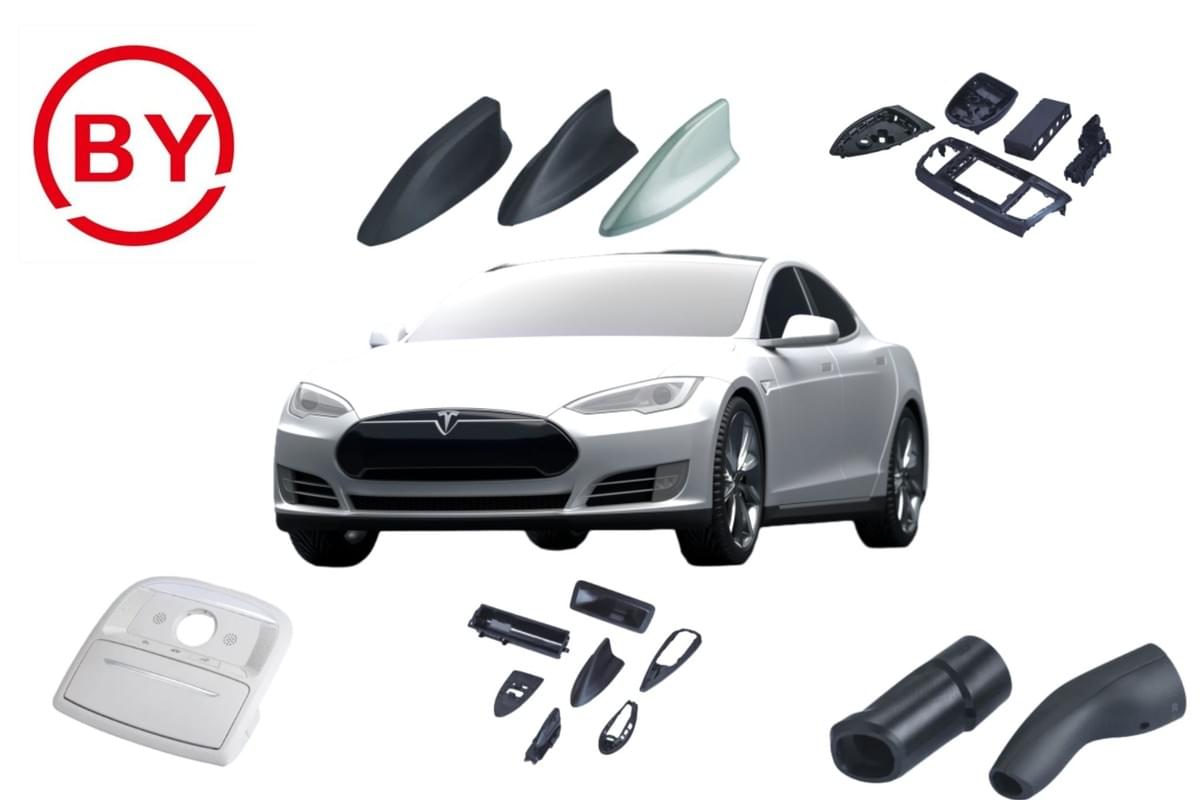
When it comes to plastic manufacturing, the financial implications of tooling choices can significantly impact a company's bottom line. The choice between hard plastic injection molding and soft tooling often boils down to an analysis of initial investments and long-term costs. Understanding these factors helps businesses make informed decisions that align with their production goals and budget constraints.
Initial Investment in Mould Injection Moulding
The initial investment in mould injection moulding can vary widely depending on the type of tooling selected. Hard tooling typically requires a higher upfront cost due to the materials used, such as high density plastic or high density polyethylene, which are essential for producing durable molds. Conversely, soft tooling offers a more budget-friendly entry point for manufacturers looking to minimize their starting expenses while still achieving quality results.
However, it's crucial to consider that while soft tooling may save money initially, it might necessitate more frequent replacements compared to hard plastic injection molding solutions. This could ultimately lead to higher cumulative costs over time if production runs require constant retooling or adjustments. Therefore, businesses must weigh the benefits of lower initial expenditures against potential future expenses when selecting their preferred method.
Long-Term Cost Analysis
In evaluating long-term costs associated with hard versus soft tooling, several key factors come into play that can influence overall expenditure in plastic manufacturing. Hard plastic injection molding tends to offer greater longevity and durability due to its robust construction from high density plastics like high polyethylene; this translates into fewer replacements and less downtime during production cycles. On the other hand, while soft tooling is less expensive upfront, its shorter lifespan could lead manufacturers back into the investment cycle sooner than anticipated.
Moreover, companies should also factor in operational efficiencies when conducting a long-term cost analysis; faster production times with hard tools can result in increased output and reduced labor costs over time. This efficiency is particularly relevant in industries where rapid turnaround is essential for maintaining competitive advantage. Ultimately, understanding these dynamics allows businesses to forecast their financial commitments more accurately based on their unique production needs.
Insights from Baoyuan on Cost-Effective Solutions
Baoyuan has positioned itself as a leader in providing cost-effective solutions within the realm of mould injection moulding technology tailored for both hard and soft tooling applications. Their expertise emphasizes utilizing high density polyethylene for hard plastic injection molding processes that maximize durability while minimizing waste—a crucial consideration for any manufacturer aiming for sustainability alongside profitability.
Additionally, Baoyuan's commitment to innovation ensures they stay ahead of industry trends by offering insights on optimizing tool performance without sacrificing quality or increasing costs unnecessarily—an essential balance for successful operations in today's competitive market landscape. By leveraging such expertise and understanding how different materials affect overall expenditure, companies can make strategic decisions that enhance both productivity and profitability over time.
Conclusion
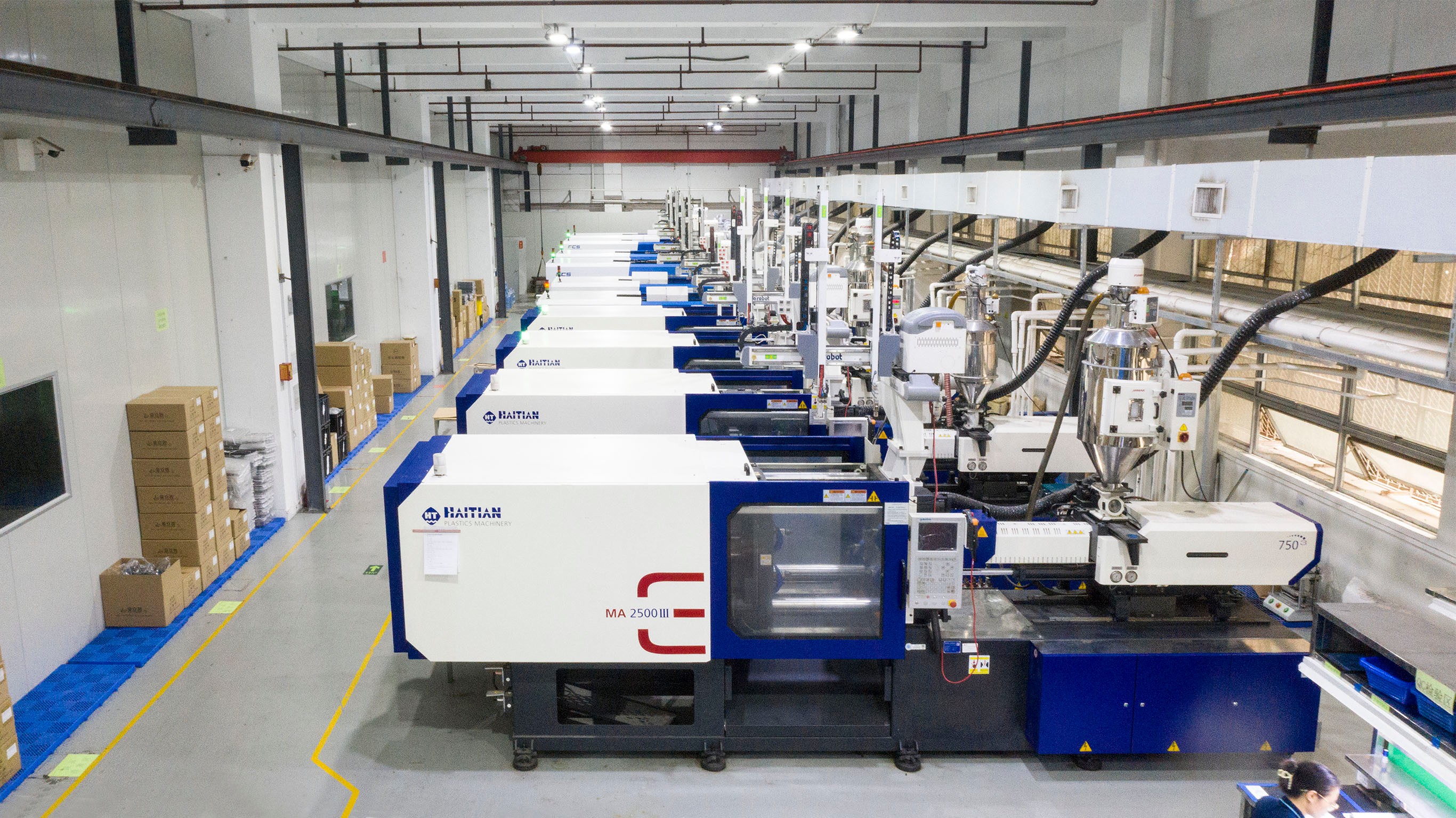
In the world of plastic manufacturing, making informed decisions about tooling is crucial for achieving optimal results. The choice between hard and soft tooling can significantly impact production efficiency, costs, and product quality. By understanding the nuances of each method, businesses can better align their tooling choices with their specific manufacturing needs.
Making Informed Decisions in Tooling
When it comes to hard plastic injection molding versus soft tooling, the decision should be driven by project requirements and expected production volume. Hard tooling is ideal for high-density plastic applications where durability is paramount, while soft tooling may offer flexibility for lower volume runs or prototyping phases. Ultimately, a thorough analysis of project goals will guide manufacturers toward the most suitable option.
Balancing Cost and Quality in Production
Cost-effectiveness is a key consideration in mould injection moulding processes, especially when weighing high density polyethylene against other materials. While hard tooling often requires a higher initial investment due to its robust nature and longevity, it frequently pays off in terms of quality and consistency for mass production runs. Conversely, soft tooling provides an attractive alternative for projects where budget constraints are tight but still demands careful consideration to ensure that quality is not compromised.
The Future of Plastic Manufacturing Techniques
As technology advances, the landscape of plastic manufacturing continues to evolve with innovative techniques enhancing both efficiency and sustainability in processes like injection casting. Future developments may see a blend of hard and soft tooling approaches that leverage the strengths of both methodologies while minimizing weaknesses—potentially leading to new materials like high polyethylene becoming more mainstream in various applications. Staying ahead means keeping an eye on these trends as they shape the future of mould plastic injection practices.