Introduction
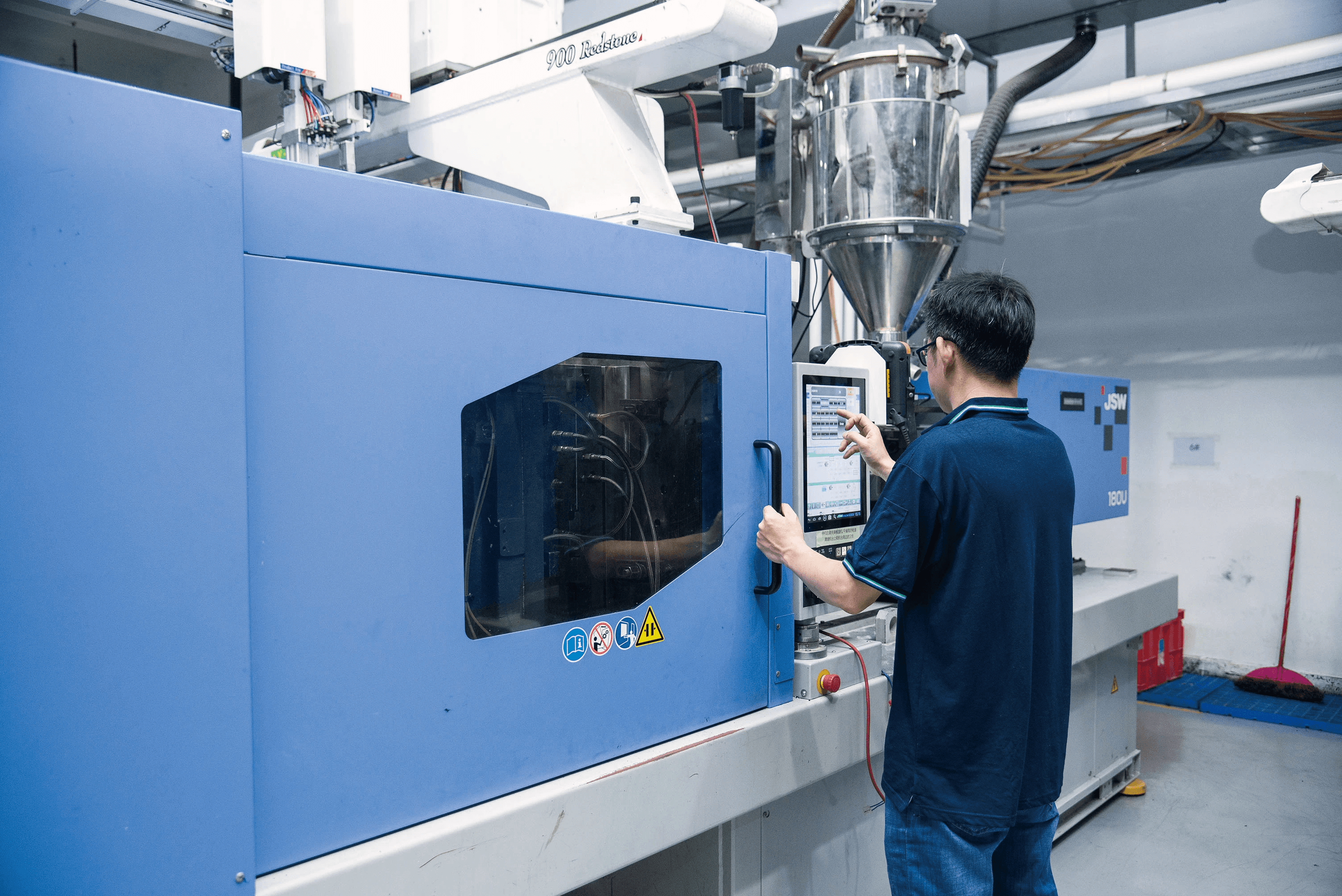
Injection molding is a marvel of modern manufacturing, allowing for the mass production of intricate plastic parts with impressive precision. However, one common issue that plagues this process is injection molding burn marks. These unsightly blemishes can compromise the aesthetic appeal and functionality of products, making it crucial to understand their causes and implications.
Understanding Injection Molding Burn Marks
Injection molding burn marks are dark spots or discolorations that appear on the surface of molded plastic parts due to trapped air or insufficient cooling during the injection process. They occur when gases are unable to escape from the mold cavity, leading to overheating and subsequent burning of the material. Recognizing these burn marks is essential for anyone involved in plastic injection molding services, as they can signify underlying problems in both design and execution.
The Impact of Burn Marks on Products
The presence of injection molding burn marks can significantly affect product quality and consumer perception. Not only do these blemishes detract from visual appeal, but they can also indicate compromised structural integrity, potentially leading to product failure under stress. For manufacturers relying on mould injection moulding techniques, maintaining high standards is vital; even minor defects like burn marks can tarnish a brand's reputation and result in costly recalls.
Why Quality Matters in Plastic Injection Molding
Quality in plastic injection molding isn't just about aesthetics; it's about ensuring that every component meets stringent performance standards. When businesses prioritize quality control measures, such as proper airflow management and optimal material selection, they minimize risks associated with issues like injection molding burn marks. By investing in expert plastic injection molding services that emphasize quality at every stage—from design to production—manufacturers can enhance their product offerings while safeguarding their reputation in a competitive market.
Insufficient Injection Speed
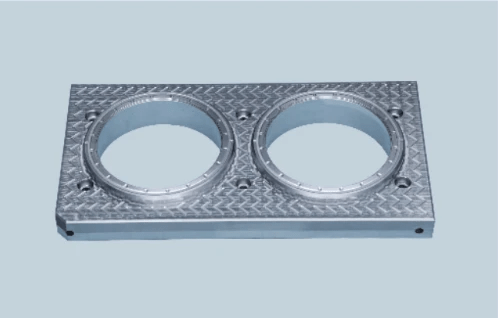
When it comes to injection molding, speed is of the essence. Insufficient injection speed can lead to a host of issues, including those pesky injection molding burn marks that can tarnish an otherwise perfect product. Understanding the role of injection speed is crucial for anyone involved in plastic injection molding services.
The Role of Injection Speed
Injection speed refers to how quickly molten plastic is injected into a mold during the mould injection moulding process. This speed significantly influences how well the material fills the cavities and ultimately affects the quality of the final product. When optimized, proper injection speeds help ensure a smooth flow, reducing the risk of defects like burn marks.
Consequences of Slow Injection
Slow injection speeds can have several negative consequences on your plastic injection molding projects. For starters, they may lead to incomplete filling of mold cavities, creating weak spots in your products or even causing them to fail entirely. Additionally, slower speeds increase residence time in the barrel, which can degrade materials and result in unsightly injection molding burn marks that are difficult to eliminate.
Tips for Optimizing Speed
To optimize your injection speed effectively, consider adjusting your machine settings based on material type and mold design specifics. Regularly monitor and maintain your equipment to ensure it operates at peak performance; this includes checking for any wear or tear that could slow down operations. Lastly, collaborating with experienced plastic injection molding services can provide valuable insights into best practices for managing and optimizing your mould injections.
Poor Ventilation in Molds
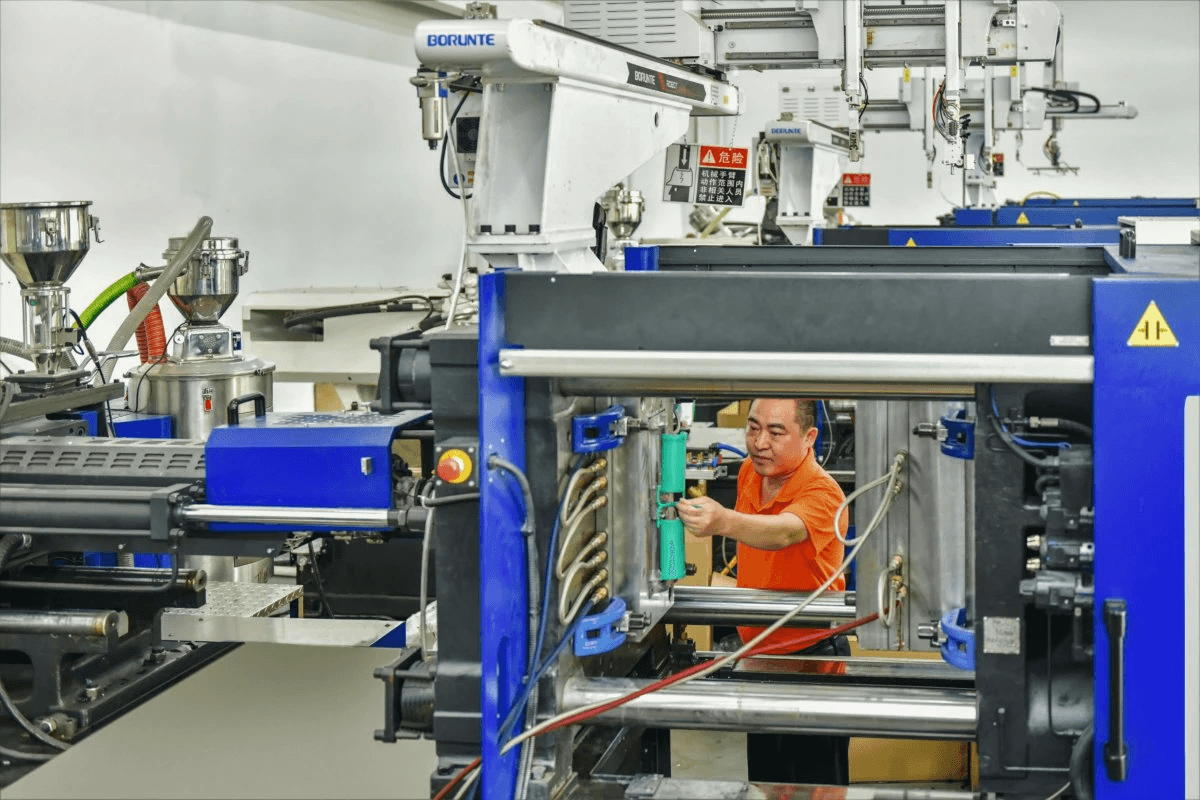
In the world of plastic injection molding, proper ventilation is often overlooked, yet it plays a crucial role in the quality of the final product. When air becomes trapped within the mold during the injection process, it can lead to unsightly injection molding burn marks that compromise both aesthetics and functionality. Ensuring adequate airflow not only enhances product quality but also optimizes production efficiency, making it a vital consideration for any serious manufacturer.
Importance of Proper Ventilation
Ventilation within molds is essential for allowing trapped gases to escape during the injection process. If these gases are not adequately vented, they can create pressure that leads to defects like burn marks on molded parts. Moreover, effective ventilation helps maintain consistent temperatures throughout the mold cavity, contributing to uniform cooling and reducing cycle times—a win-win situation for any plastic injection molding service.
How Ventilation Affects Burn Marks
When ventilation is insufficient in an injection mold, air pockets can form as molten plastic fills the cavity. These air pockets can heat up excessively and cause localized overheating, resulting in those dreaded injection molding burn marks on finished products. Additionally, poor airflow may lead to uneven material distribution during filling; this inconsistency exacerbates defects and undermines overall product integrity.
Solutions for Enhanced Airflow
To combat poor ventilation issues in mould injection moulding processes, several strategies can be employed. First and foremost, incorporating venting channels or grooves into the design of your plastic injection molding mold can significantly improve airflow and gas escape routes. Furthermore, utilizing advanced simulation software during the design phase allows manufacturers to predict potential ventilation problems before they arise—ensuring that only high-quality moldable plastics are used without compromising productivity.
Material Compatibility Issues
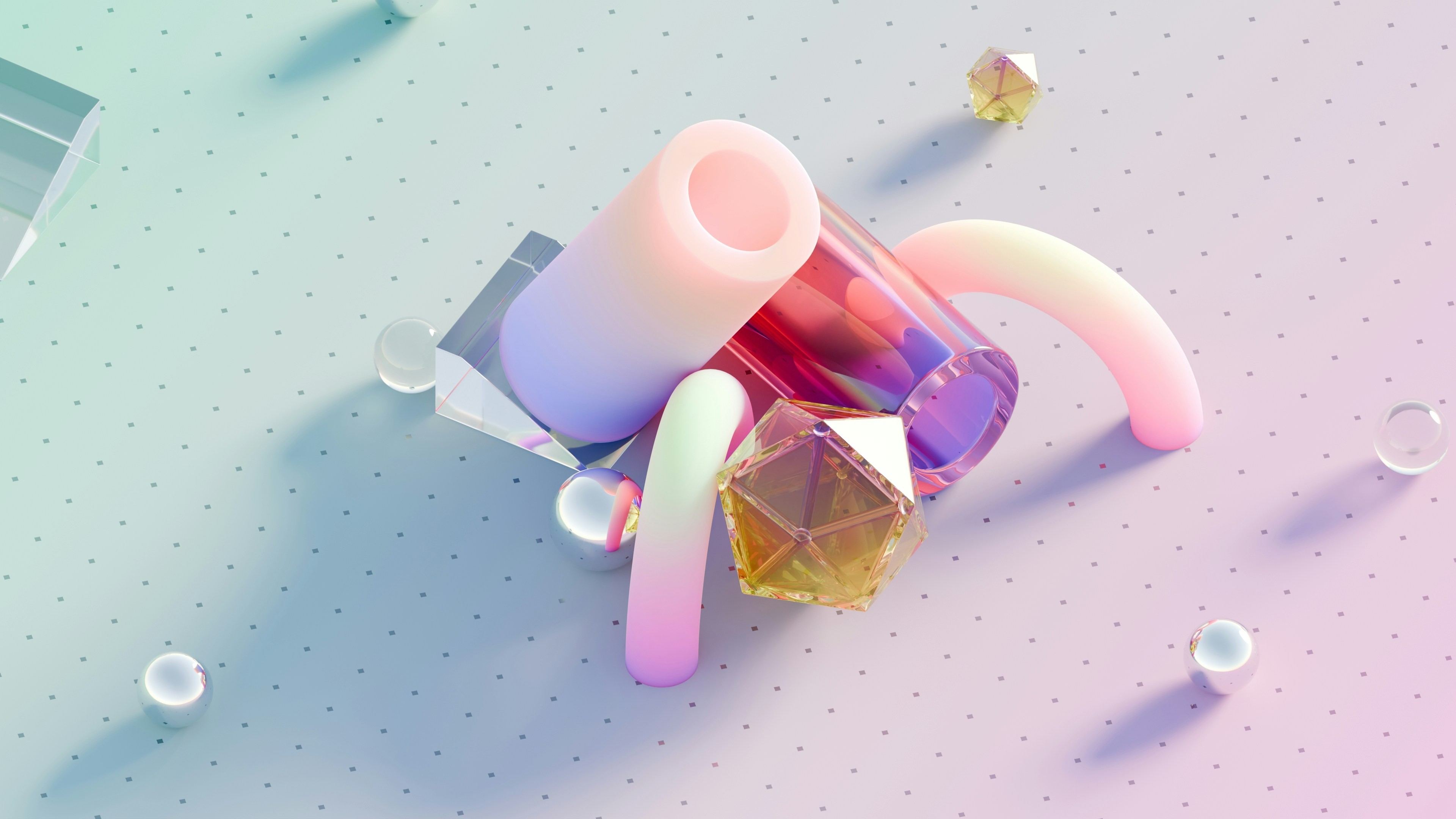
When it comes to injection molding, selecting the right materials is crucial for achieving high-quality results and avoiding defects like injection molding burn marks. The compatibility of plastics used in the process can significantly affect the final product's integrity and appearance. Understanding the properties of different injection moldable plastics is key to ensuring that your mould injection moulding process runs smoothly.
Selecting the Right Materials
Choosing appropriate materials for plastic injection molding is not just a matter of preference; it's essential for preventing issues such as burn marks on your finished products. Each type of plastic has unique characteristics, including melting temperature, viscosity, and cooling rates that can influence how well it performs during the injection process. By carefully evaluating these properties, manufacturers can avoid potential pitfalls associated with using incompatible materials.
The selection process also involves considering factors like strength, flexibility, and environmental resistance based on the final application of the product. Using high-quality plastic injection molding services ensures that you have access to a wide range of suitable materials tailored to your specific needs. Ultimately, making informed material choices helps in reducing defects like burn marks while enhancing overall product quality.
Risks of Incompatible Plastics
Utilizing incompatible plastics in mould plastic injection can lead to various complications during production, one of which is the dreaded burn mark phenomenon. When two or more types of plastics are mixed improperly or not suited for each other, they may not melt uniformly or adhere correctly during the molding process. This lack of cohesion can create weak points in your products and lead to unsightly blemishes that compromise their aesthetic appeal.
Moreover, incompatible materials may react adversely under heat or pressure conditions typical in injection molding processes, resulting in further degradation and quality issues. Such risks highlight why thorough material compatibility assessments are essential before beginning production runs with any batch of plastic injection molded items. Ignoring these factors could lead to increased waste and costly rework due to defective parts.
How Baoyuan Ensures Material Quality
At Baoyuan, we understand that material quality directly impacts the success rate of our plastic injection molding services and ultimately influences customer satisfaction. We prioritize sourcing only top-tier injection moldable plastics from reputable suppliers who meet stringent industry standards—ensuring compatibility throughout our processes while minimizing risks associated with burn marks or other defects.
Our expert team conducts rigorous testing on all incoming materials to verify their suitability for specific applications within our moulding operations. Additionally, we maintain an extensive database outlining various plastics' properties so that we can make informed decisions tailored precisely to each project’s needs—effectively mitigating any chances of encountering issues related to material incompatibility.
By focusing on these critical aspects within our production workflow at Baoyuan, we deliver exceptional quality while preventing common problems like injection molding burn marks from derailing your projects—because when it comes down to it, nothing less than perfection will do!
Conclusion
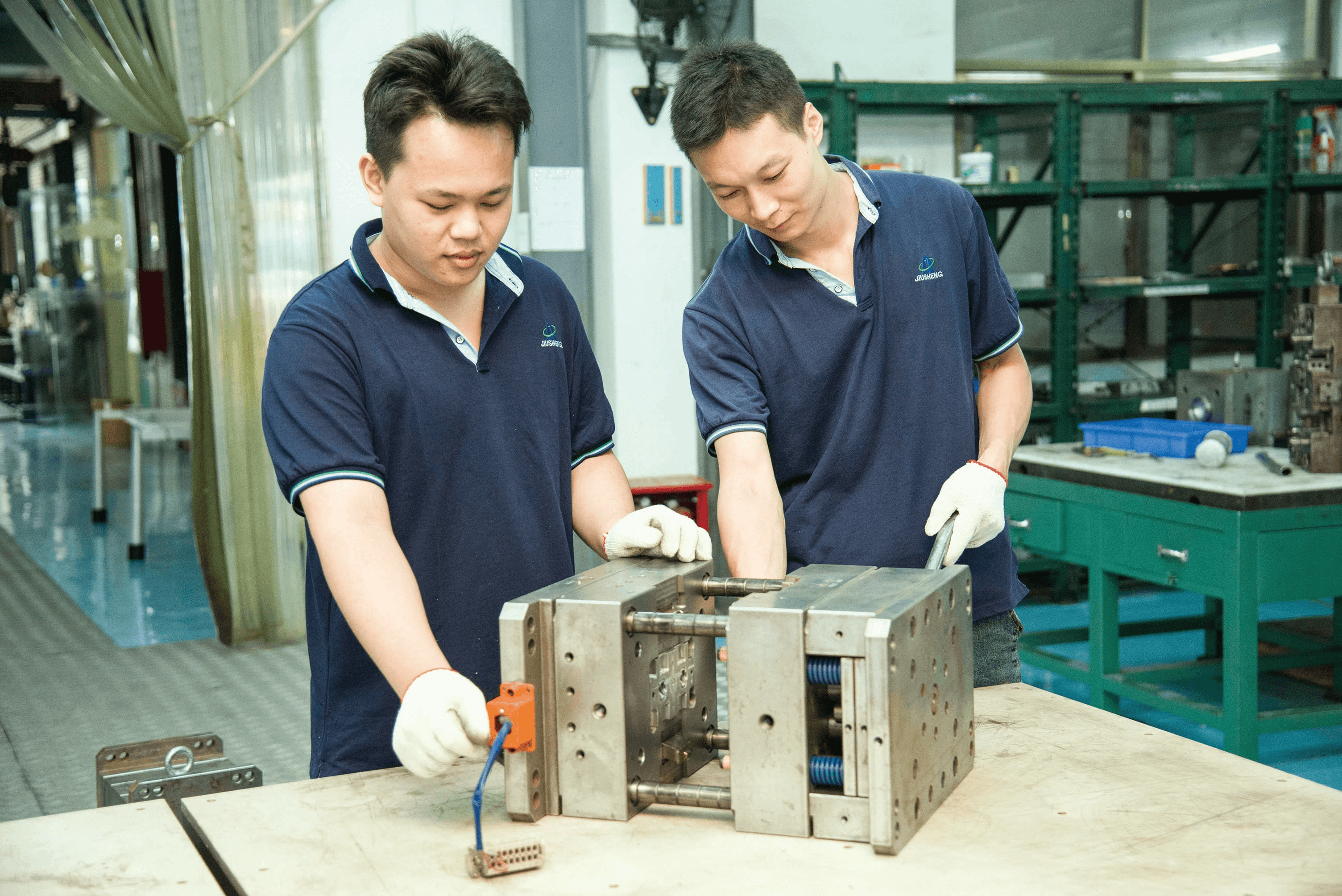
In summary, understanding the causes of injection molding burn marks is crucial for maintaining product quality in plastic injection molding. By addressing issues such as insufficient injection speed, poor ventilation, and material compatibility, manufacturers can significantly reduce the occurrence of these defects. Ultimately, investing in expert plastic injection molding services can lead to better outcomes and customer satisfaction.
Identifying Key Causes of Burn Marks
The most common culprits behind injection molding burn marks are slow injection speeds and inadequate mold ventilation. When the molten plastic takes too long to fill the mold cavity, it can lead to overheating and subsequent burn marks on the finished product. Additionally, poor airflow within the mold can trap gases that contribute to these unsightly blemishes, making it essential to identify these factors early in the production process.
Strategies to Mitigate Injection Molding Issues
To combat injection molding burn marks effectively, manufacturers should focus on optimizing their processes. This includes adjusting the injection speed for a more consistent flow and ensuring that molds are well-ventilated to allow trapped air to escape easily. Furthermore, selecting compatible injection moldable plastics can prevent chemical reactions that may exacerbate burn mark formation, ultimately enhancing overall product quality.
The Importance of Expert Plastic Injection Molding Services
Engaging with professional plastic injection molding services is key to achieving high-quality results while minimizing defects like burn marks. These experts possess in-depth knowledge of various moulding techniques and materials suited for specific applications—ensuring that every aspect of production meets stringent standards. By collaborating with seasoned professionals in mold plastic injection processes, companies not only enhance their product quality but also improve efficiency and reduce costs over time.