Introduction
In the world of injection molding, one term that often raises eyebrows is the short shot. This phenomenon occurs when a mold fails to fill completely, leaving behind incomplete parts that can lead to significant production issues. Understanding what a short shot in injection molding is and how it manifests is crucial for anyone involved in manufacturing processes.
Understanding the Short Shot Phenomenon
So, what is a short shot in injection molding? It's essentially a defect where the injected material doesn’t fully occupy the mold cavity. This can happen due to various factors, such as inadequate material flow or insufficient injection pressure, resulting in parts that are not only unsightly but also functionally compromised. Recognizing these defects early on can save time and resources, making it essential for manufacturers to grasp this concept thoroughly.
The Importance of Resolving Short Shots
Addressing short shots is vital for maintaining product quality and operational efficiency. If left unresolved, these defects can lead to increased scrap rates and customer dissatisfaction—neither of which any manufacturer wants on their record! Moreover, understanding how to fix short shot injection molding issues ensures smoother production runs and enhances overall profitability.
Your Go-To Guide for Solutions
This guide serves as your comprehensive roadmap to tackling the challenges posed by short shots in injection molding. From exploring effective strategies on how to avoid short shots in injection molding to offering practical solutions for fixing them when they occur, we've got you covered! Additionally, we'll delve into related topics like short mold defects and provide valuable insights from industry experts along the way.
What is a Short Shot in Injection Molding?
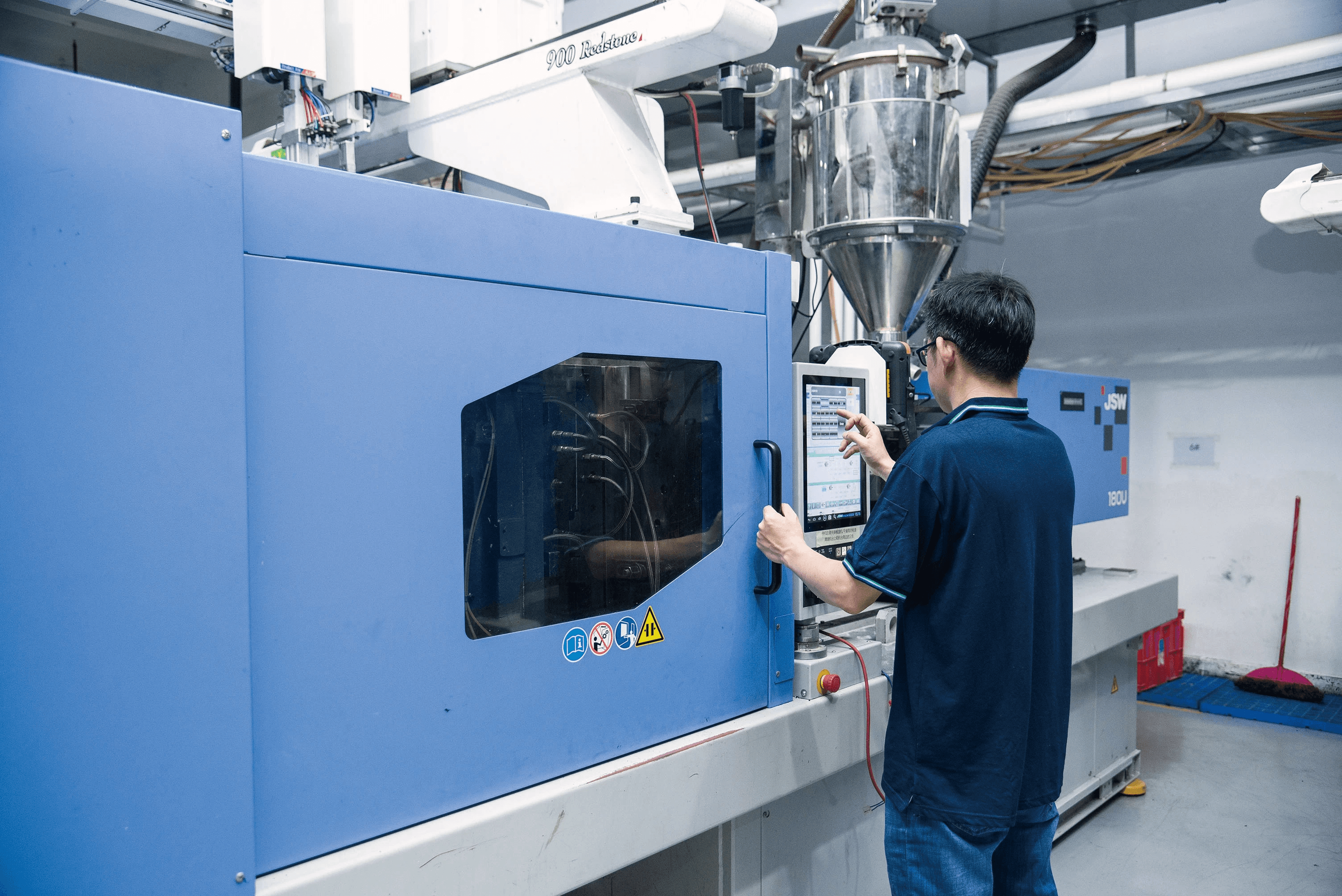
When diving into the world of injection molding, one term that often surfaces is the short shot. This defect occurs when the injected material fails to completely fill the mold cavity, leading to incomplete or defective parts. Understanding what a short shot in injection molding entails is crucial for manufacturers aiming to produce high-quality products consistently.
Defining Short Shot Defects
A short shot defect can be characterized as a failure in the injection molding process where insufficient material enters the mold, resulting in an unfinished or poorly formed part. Essentially, it's like trying to bake a cake without enough batter—some parts are missing, and it just doesn't rise to the occasion! Recognizing this defect early on can save time and resources while ensuring production efficiency.
Common Causes of Short Shots
Several factors contribute to short shots in injection molding, making it essential for operators to be vigilant. One common cause is inadequate injection pressure; if the pressure isn’t high enough, it won’t push the molten plastic into all areas of the mold effectively. Other culprits include improper temperature settings and poor material flow characteristics—think of it as trying to pour syrup from a bottle that's not wide enough; it just won't flow freely!
Real-World Examples of Short Shots
To illustrate how short shots manifest in real-world scenarios, consider an automotive manufacturer producing dashboard components. If certain sections of these dashboards appear incomplete or have visible gaps due to insufficient filling during molding, that’s a classic short shot scenario! Another example could be consumer electronics where casing parts are crucial; any short shot defects could lead to malfunctioning devices or aesthetic issues that deter customers.
How to Avoid Short Shots in Injection Molding?
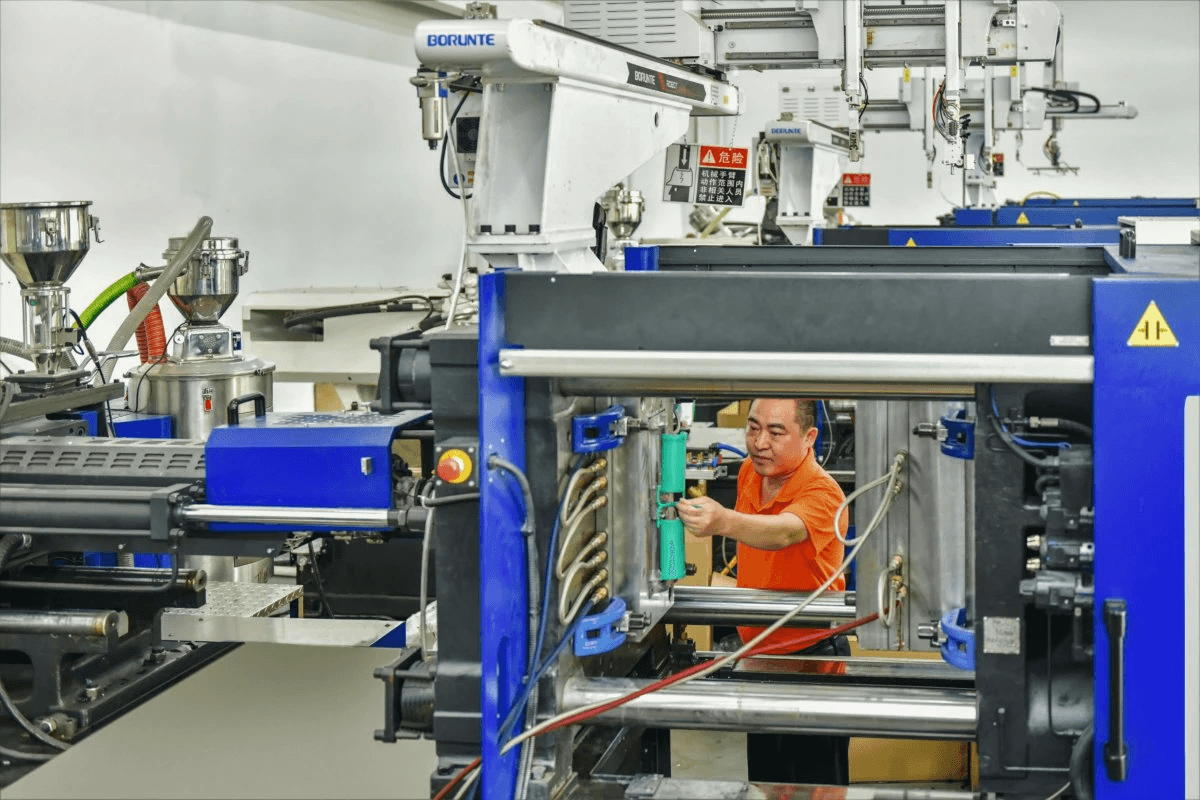
Preventing short shots in injection molding is crucial for maintaining production efficiency and product quality. By understanding the various factors that contribute to these defects, manufacturers can implement effective strategies to mitigate risks. Let's dive into some practical methods to avoid short shots and keep your molds running smoothly.
Design Considerations to Prevent Short Shots
When tackling the question of what is a short shot in injection molding, one of the first steps is to focus on design considerations. Effective mold design plays a pivotal role in ensuring that the molten material fills every nook and cranny of the mold cavity. Key elements include optimizing gate location, ensuring adequate venting, and maintaining uniform wall thickness throughout the part.
Additionally, incorporating features like flow channels or ribs can help guide the material more effectively during injection. Designers should also consider potential thermal issues, as inconsistent temperatures can lead to premature solidification and contribute to short shots. By prioritizing thoughtful design from the outset, manufacturers can significantly reduce their risk of encountering this common defect.
Material Selection and Its Impact
The choice of material is another critical factor when discussing how to avoid short shots in injection molding. Different polymers have varying flow characteristics; some may not fill complex molds efficiently if not selected carefully. Understanding these properties allows engineers to select materials that are compatible with their specific applications while minimizing risks associated with short shots.
Moreover, considering additives or fillers can enhance flowability without compromising mechanical properties. It's essential for manufacturers to conduct thorough testing before finalizing their material choices—this ensures that they won't face unexpected challenges during production runs due to inadequate fill rates or other related issues. Ultimately, informed material selection goes hand-in-hand with effective design strategies for preventing short shots.
Best Practices in Injection Molding Process
Implementing best practices during the injection molding process is vital for addressing how to fix short shot injection molding issues before they arise. Regularly monitoring key parameters such as temperature, pressure, and cycle times helps maintain optimal conditions throughout production runs. Operators should also be trained on recognizing early signs of potential defects so they can act swiftly if problems emerge.
Another essential practice involves conducting routine maintenance on molds and machinery; this ensures that everything remains in tip-top shape and reduces wear-related defects over time. Additionally, conducting trial runs with new designs or materials can help identify any shortcomings before full-scale production begins—saving both time and resources down the line! By adhering strictly to these best practices within your operation, you’ll be well-equipped to minimize occurrences of short shots effectively.
How to Fix Short Shot Injection Molding?
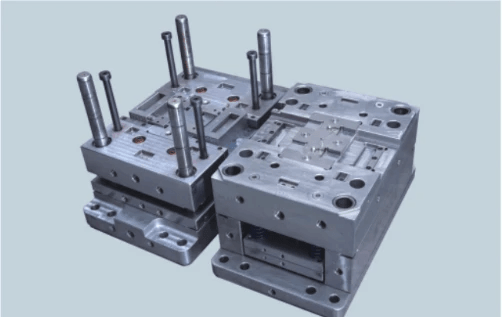
Addressing a short shot in injection molding can be a pressing concern for manufacturers, as it not only affects product quality but also production efficiency. Understanding how to fix short shot injection molding is essential for maintaining high standards and minimizing waste. In this section, we will explore both quick fixes for immediate issues and long-term solutions for persistent problems, while also sharing inspiring case studies that highlight successful resolutions.
Quick Fixes for Immediate Issues
When faced with a short shot in injection molding, the first step is to identify the problem quickly and implement immediate fixes. One effective approach is to increase the injection speed; this can help ensure that the molten material fills the mold cavity more completely. Additionally, checking and adjusting the temperature settings can also make a significant difference; higher temperatures can reduce viscosity and improve flow characteristics, effectively addressing what is a short shot in injection molding.
Another quick fix involves inspecting the mold itself for any obstructions or damage that could be hindering material flow. Cleaning out any debris or residue from previous runs can often resolve these issues promptly. Lastly, if you notice that specific areas of your mold consistently experience short shots, consider adding venting or modifying existing vents to allow trapped air to escape more efficiently.
Long-Term Solutions for Persistent Problems
While quick fixes can address immediate concerns about how to fix short shot injection molding, long-term solutions are crucial for preventing recurrence of these defects. One of the primary strategies involves revisiting your mold design; ensuring that it has adequate filling paths and appropriate gate sizes will significantly reduce instances of short shots in injection molding over time. Collaborating with experienced mold designers who understand how to avoid short shots in injection molding can yield invaluable insights.
Material selection plays a pivotal role as well; choosing high-flow materials may help mitigate issues related to low viscosity during processing. Furthermore, regularly scheduled maintenance on machinery ensures optimal performance and minimizes wear-and-tear-related defects that contribute to recurring problems like short shots.
Lastly, investing in comprehensive training programs for operators on best practices related to machine settings and monitoring processes will foster an environment focused on continuous improvement—essentially creating a culture where everyone understands how important it is to minimize defects like short shots.
Case Studies: Successful Resolutions
To illustrate effective strategies on how to fix short shot injection molding issues, let’s delve into some real-world case studies showcasing successful resolutions. In one notable instance, a manufacturer producing automotive components faced frequent occurrences of what is a short shot in injection molding due to inconsistent material flow rates caused by improper temperature control settings. By implementing precise temperature monitoring systems alongside regular operator training sessions focused on best practices in adjusting machine parameters, they reduced their defect rate by over 30% within just three months.
In another example from an electronics manufacturer grappling with similar challenges around how to avoid short shots in injection molding at their facility found success through redesigning their molds entirely based on simulation data analysis techniques—leading them not only towards reducing defects but also improving overall production efficiency by 20%.
These case studies highlight that while fixing existing issues with short shots requires swift action initially through quick fixes like adjusting speeds or temperatures; sustainable success hinges upon comprehensive long-term strategies encompassing everything from design modifications down through operator education—all aimed at cultivating expertise around identifying causes behind what constitutes both “short shots” and “short mold defects” in our industry today.
Analyzing the Root Causes of Short Shots
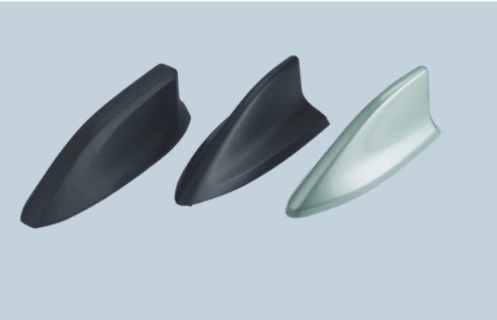
Understanding the root causes of short shots in injection molding is essential for any manufacturer aiming to produce high-quality parts. A short shot occurs when the molten plastic fails to fill the entire mold cavity, leading to incomplete parts and wasted materials. By dissecting the factors that contribute to this phenomenon, we can better strategize on how to avoid short shots in injection molding and enhance overall production efficiency.
Mold Design Flaws and Their Impact
Mold design flaws are often at the forefront when we talk about what is a short shot in injection molding. If a mold isn’t designed with appropriate flow paths or has inadequate venting, it can significantly hinder material flow, resulting in incomplete fills. Additionally, sharp corners or intricate geometries can trap air pockets, further exacerbating short shots by preventing the molten plastic from fully occupying the mold cavity.
When considering how to fix short shot injection molding issues related to mold design, it's crucial to prioritize simplicity and efficiency in your designs. Ensuring that molds are appropriately vented allows trapped air to escape easily while promoting smoother material flow. Ultimately, investing time upfront in robust mold design will pay off by reducing defects and improving product quality.
Injection Speed and Pressure Effects
The speed and pressure at which plastic is injected into the mold play a pivotal role in determining whether a short shot occurs or not. Low injection speeds may not provide enough force for the molten material to reach all areas of complex molds, leading directly to what is a short shot in injection molding situations. Conversely, excessively high speeds can cause turbulence within the melt stream, creating inconsistencies that also result in incomplete fills.
To avoid these pitfalls when considering how to avoid short shots in injection molding processes, manufacturers must carefully calibrate their machinery settings based on specific material characteristics and part designs. Monitoring pressure profiles throughout each cycle helps identify potential issues before they escalate into full-blown defects. By striking an optimal balance between speed and pressure, you can enhance fill consistency while mitigating risks associated with both underfilling and overpacking.
Recommendations from the Baoyuan Team
The Baoyuan Team has gathered invaluable insights on addressing root causes related to short shots through years of experience working with diverse clients across various industries. One key recommendation is conducting thorough simulations during the design phase using advanced software tools; this allows engineers to visualize potential filling issues before physical production begins—essentially providing answers for how to fix short shot injection molding concerns early on.
Additionally, regular training sessions for operators focusing on machine settings and maintenance best practices will help ensure everyone involved understands their role in preventing defects like short shots or even what is a short mold defect in injection molding situations as well! Continuous monitoring of production processes through data analytics helps identify trends that could signal impending problems—giving teams an opportunity for proactive intervention rather than reactive fixes later down the line.
In summary, understanding root causes such as mold design flaws or improper speed/pressure settings opens up avenues for improvement when tackling issues like how to avoid shorts shots effectively!
What is a Short Mold Defect in Injection Molding?
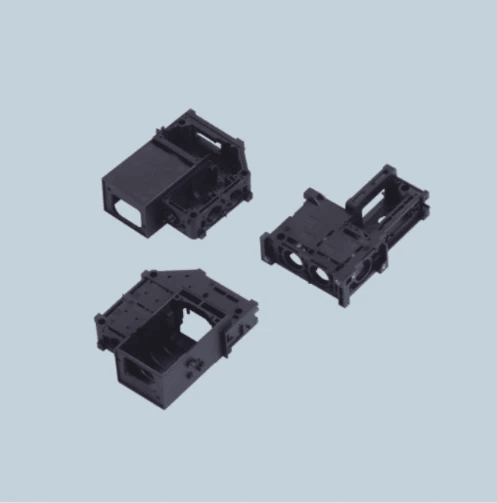
In the world of injection molding, understanding the intricacies of defects is crucial for maintaining quality and efficiency. One such defect that can wreak havoc on production is the short mold defect. This issue not only affects the aesthetics of the final product but also can lead to significant material waste and increased costs.
Defining Short Mold Defects
A short mold defect occurs when an injection molded part does not fill the entire cavity of the mold, resulting in incomplete or missing sections. This differs from a short shot in injection molding, where insufficient material flows into the mold due to various factors like pressure or temperature issues. Essentially, while both defects result in incomplete parts, a short mold defect specifically refers to problems related to the mold design itself.
How They Relate to Short Shots
Short shots and short mold defects are closely related; understanding one helps illuminate the other. A short shot in injection molding often stems from inadequate filling caused by design flaws or operational missteps that also lead to short mold defects. By identifying these connections, manufacturers can implement strategies that address both issues simultaneously, improving overall product quality.
Prevention Strategies for Short Mold Defects
Preventing short mold defects requires a proactive approach involving thorough planning and design considerations. Start with ensuring proper mold design by incorporating adequate venting systems and optimizing gate locations—this will help facilitate better flow of material into all areas of the cavity. Additionally, regular maintenance checks on molds can catch potential issues before they escalate into costly production errors; this ties back into how to avoid short shots in injection molding as well.
Conclusion
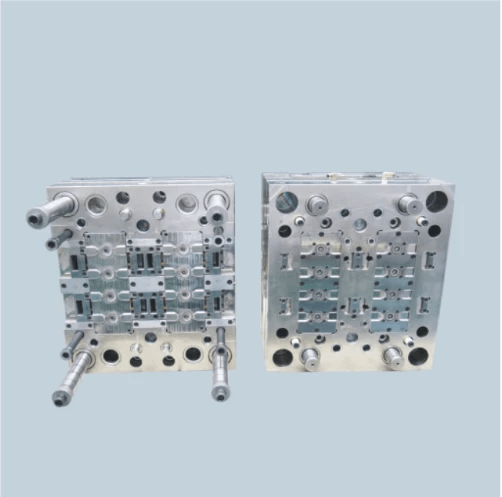
In wrapping up our exploration of the short shot phenomenon in injection molding, it's clear that understanding and addressing this issue is crucial for maintaining production quality. A short shot in injection molding not only impacts the final product but can also lead to increased costs and inefficiencies. By being aware of what a short shot is, how to avoid it, and how to fix it when it occurs, manufacturers can enhance their processes and outcomes.
Key Takeaways on Short Shots
To summarize, a short shot in injection molding occurs when the material does not completely fill the mold cavity, resulting in defects that can compromise product integrity. Common causes include inadequate injection pressure, poor material flow characteristics, and design flaws within the mold itself. Recognizing these factors allows you to take proactive measures against short shots and maintain high-quality production standards.
Strategies for Continuous Improvement
Improving your injection molding processes requires a commitment to ongoing evaluation and adaptation. To avoid short shots in injection molding, consider investing in advanced mold design techniques and optimizing your material selection based on specific project needs. Regular training sessions for your team on best practices can also foster a culture of quality awareness that helps prevent issues before they arise.
Resources for Further Learning on Injection Molding
For those eager to delve deeper into the intricacies of injection molding, numerous resources are available online and through industry publications. Websites like the Society of Plastics Engineers (SPE) offer valuable insights into best practices regarding what is a short shot in injection molding as well as comprehensive guides on troubleshooting techniques like how to fix short shot injection molding effectively. Additionally, engaging with professional forums or attending workshops can provide hands-on experiences that enhance your understanding of both preventing and resolving issues related to short mold defects.