Introduction
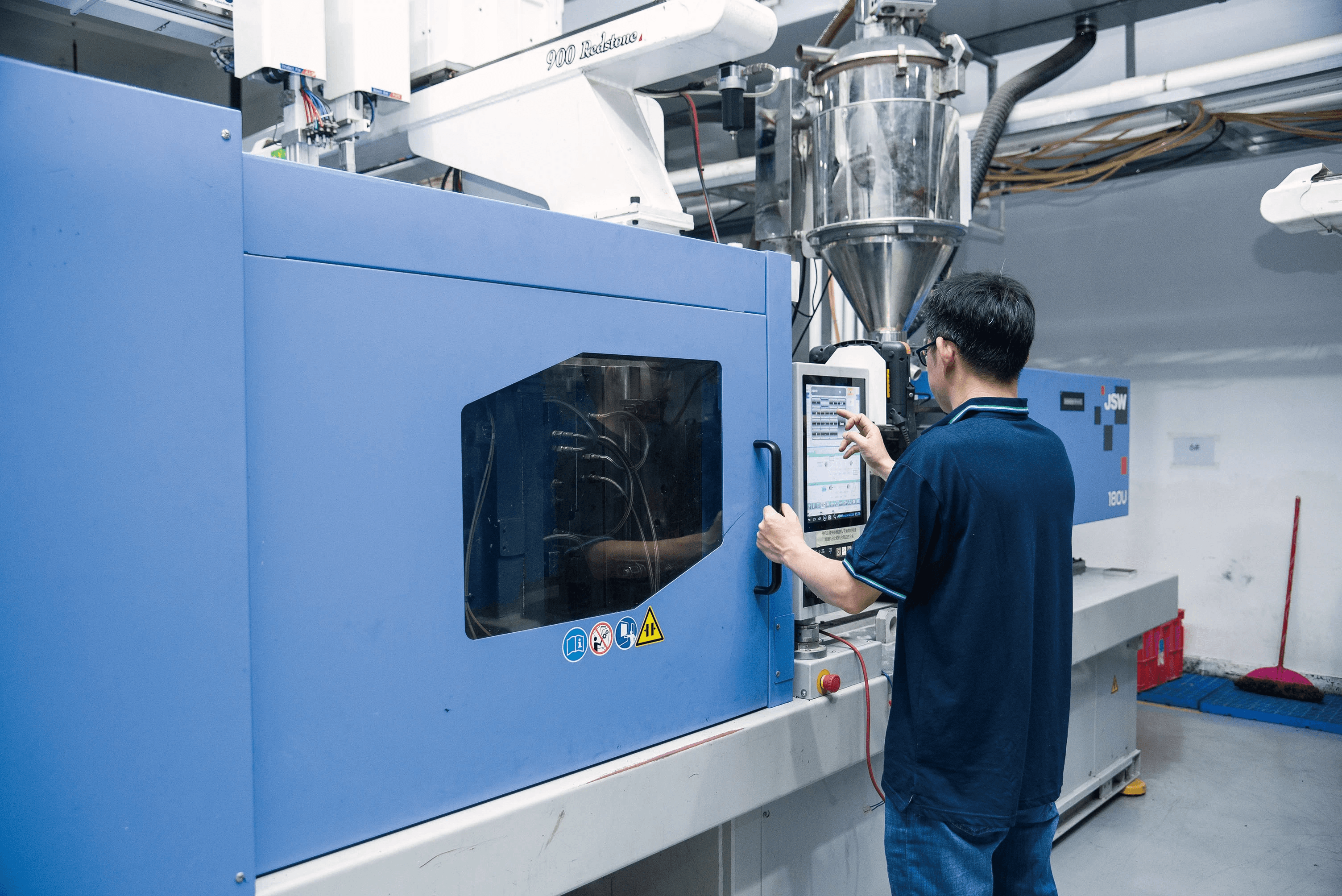
In today's fast-paced manufacturing landscape, the demand for small parts is surging. From electronics to automotive components, these tiny yet intricate pieces are essential in creating efficient and functional products. However, this growing demand brings with it an array of challenges that require innovative solutions in the realm of injection molding.
The Growing Demand for Small Parts
The miniaturization of technology has led to an increased reliance on injection molding small parts problem and solution approaches in various industries. As products become more compact, manufacturers must adapt their processes to ensure that even the smallest components meet stringent quality standards. This trend not only boosts production efficiency but also emphasizes the need for precision in mould injection moulding techniques.
Importance of Precision in Injection Molding
Precision is paramount when it comes to plastic injection molding, especially for small parts where tolerances can be razor-thin. Any deviation from specifications can lead to significant issues down the line, affecting product performance and reliability. Therefore, understanding how to optimize the injection molding machine and mold plastic injection processes is crucial for achieving high-quality results consistently.
Overview of Challenges Faced
Despite advancements in technology, several challenges persist within the realm of injection molding small parts problem and solution strategies. Issues such as defects during production, suboptimal mold design, and material selection can hinder efficiency and lead to costly rework or scrap rates. By identifying these challenges early on, manufacturers can implement effective solutions that enhance productivity while maintaining quality standards.
Understanding the Injection Molding Process
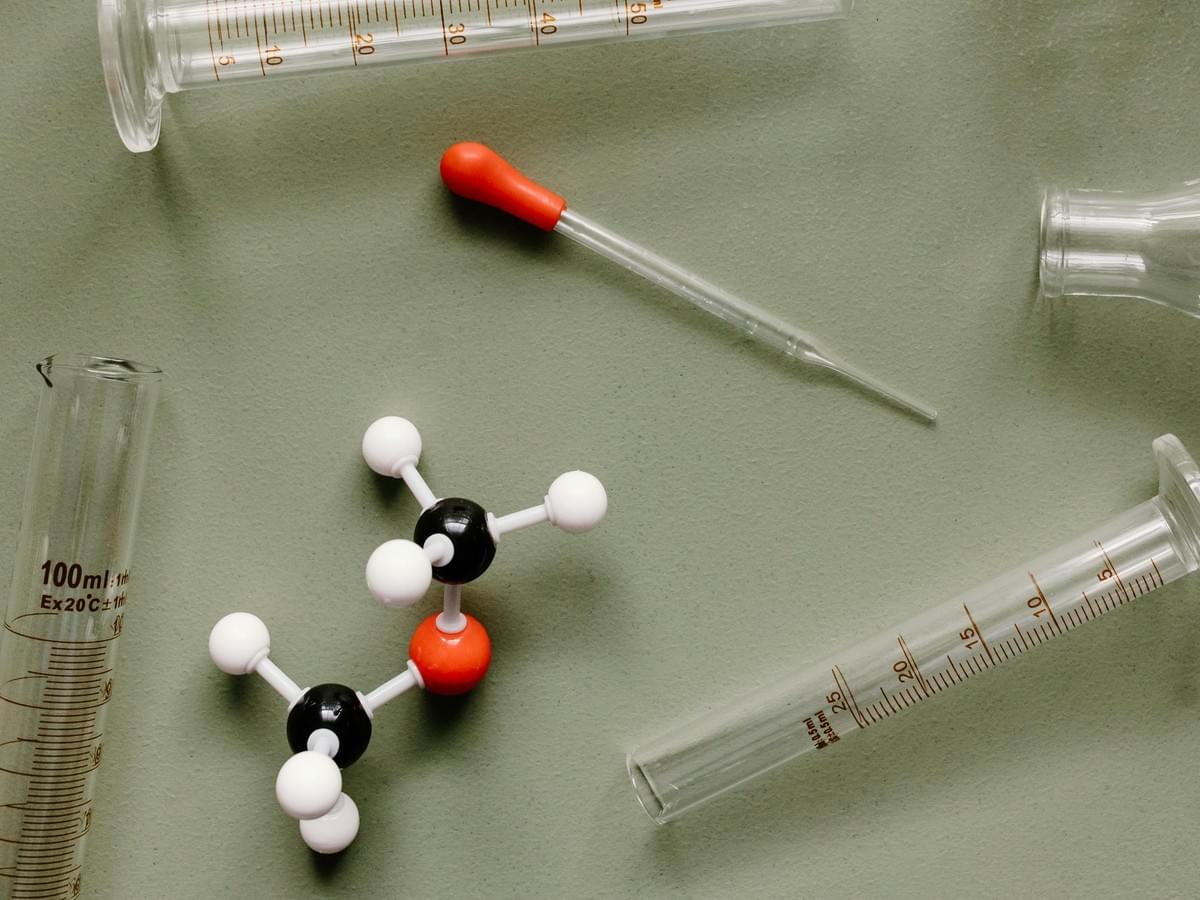
Injection molding is a fascinating and intricate process that has revolutionized the manufacturing of small parts. It combines precision engineering with innovative technology to create high-quality products from various plastics. To grasp this process fully, it's essential to break it down into key steps, understand the machinery involved, and explore the types of materials used.
Key Steps in Mould Injection Moulding
The journey of creating small plastic parts through mould injection moulding begins with designing a detailed mold based on product specifications. Once the mold is ready, it is mounted onto an injection molding machine where raw plastic pellets are heated until they become molten. This molten plastic is then injected into the mold cavity under high pressure, allowing it to fill every nook and cranny before cooling and solidifying into the desired shape.
After cooling, the mold opens to release the finished product—voilà! However, this seemingly simple process can present several injection molding small parts problems if not executed correctly. Issues like incomplete filling or warping may arise if any step in this meticulous sequence is overlooked or poorly managed.
Role of Injection Molding Machine
The injection molding machine plays a pivotal role in ensuring that everything runs smoothly during production. It consists of two main components: the injection unit and the clamping unit. The injection unit melts and injects plastic into the mold, while the clamping unit secures the mold halves together during injection to prevent leakage.
Different machines are designed for different scales of production; some are tailored for high-volume manufacturing while others cater to more niche applications involving complex designs or smaller batches. Choosing the right type of injection molding machine can significantly impact both efficiency and quality when addressing any potential injection molding small parts problem and solution scenarios.
Overview of Injection Moldable Plastics
Understanding which materials can be used in plastic injection molding is crucial for successful production outcomes. Injection moldable plastics come in various types, including thermoplastics like ABS (Acrylonitrile Butadiene Styrene), polycarbonate, and nylon—each offering unique properties suited for specific applications. These materials not only need to have good flow characteristics but must also withstand post-molding processes such as painting or plating without losing their integrity.
Selecting appropriate plastics based on their mechanical properties ensures that final products meet performance standards while also reducing potential issues during production runs—thus tackling common challenges associated with small part manufacturing head-on! With advancements in material science continually emerging, manufacturers now have access to an even wider range of options that can help mitigate any existing problems related to plastic injection molding molds.
Common Problems in Injection Molding Small Parts
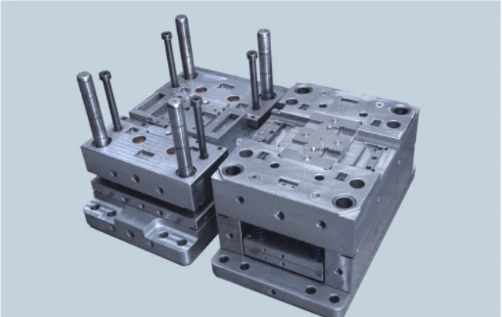
Injection molding small parts is a complex process fraught with potential pitfalls. Identifying defects early can save manufacturers time and money, but it requires a keen eye and an understanding of the intricacies involved. From surface blemishes to dimensional inaccuracies, recognizing these issues is critical for ensuring high-quality outcomes in plastic injection molding.
Identifying Defects in Plastic Injection Molding
Defects in plastic injection molding can manifest in various forms, including warping, sink marks, and short shots. Each of these issues not only affects the appearance but also compromises the functionality of the final product. To address these injection molding small parts problems effectively, manufacturers must implement rigorous inspection techniques at every stage of production.
Common methods for identifying defects include visual inspections and advanced technologies like ultrasonic testing or X-ray imaging. These techniques help catch issues before they escalate into larger problems that may require costly rework or scrapping of entire batches. By prioritizing defect identification, companies can enhance their overall quality assurance processes while minimizing waste.
Issues with Mould Design and Construction
Mould design plays a pivotal role in the success of injection molding small parts; an inadequate design can lead to numerous complications during production. Poorly designed molds may result in uneven flow rates or insufficient cooling times, which ultimately lead to defects such as warpage or incomplete filling of cavities. Therefore, investing time and resources into meticulous mold construction is essential for achieving optimal results in mould injection moulding.
Moreover, mold materials themselves need careful consideration; using subpar materials can compromise durability and lead to premature wear and tear on molds used for plastic injection molding processes. This not only increases maintenance costs but also impacts production timelines due to unexpected downtimes caused by mold failures. Addressing these mould design challenges early on ensures smoother operations down the line.
Challenges in Material Selection
Selecting the right materials for injection moldable plastics is another hurdle that manufacturers face when producing small parts. The choice of resin directly influences factors such as strength, flexibility, and thermal stability—attributes that are crucial depending on the intended application of the final product. A mismatch between material properties and product requirements can result in significant performance issues post-production.
Additionally, variations within material batches can introduce inconsistencies that further complicate production processes; this makes it vital to establish robust supplier relationships and perform thorough testing on incoming materials before use in mold plastic injection operations. With so many variables at play—ranging from environmental conditions to processing parameters—navigating material selection requires both experience and foresight from manufacturers aiming to solve common injection molding small parts problems effectively.
Quality Control in Small Part Injection Molding
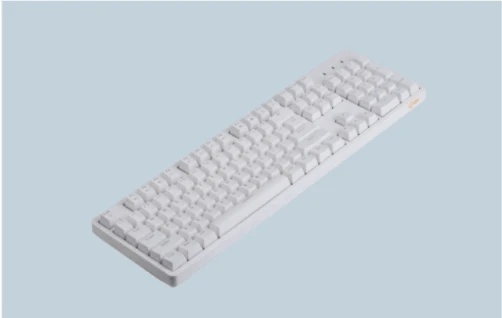
In the intricate world of injection molding, especially when dealing with small parts, quality control takes center stage. The precision required in plastic injection molding means that even the tiniest defect can lead to significant problems down the line. Therefore, implementing robust quality assurance measures is not just a good practice; it’s an absolute necessity for maintaining product integrity and customer satisfaction.
Importance of Quality Assurance
Quality assurance in injection molding small parts is crucial for several reasons. Firstly, it helps identify defects early in the production process, minimizing waste and reducing costs associated with rework or scrapping defective products. Secondly, ensuring high standards of quality fosters trust among clients and enhances a company’s reputation in a competitive market where precision is paramount.
Moreover, effective quality control can also streamline production processes by identifying bottlenecks and inefficiencies related to the injection molding machine or mould injection moulding design. By focusing on continuous improvement through rigorous testing and inspection protocols, manufacturers can ensure that their plastic injection molding molds meet both functional requirements and aesthetic expectations. Ultimately, this commitment to quality translates into better performance and reliability of the final products made from injection moldable plastics.
Techniques for Inspecting Mold Plastic Injection
To tackle the challenges associated with injection molding small parts problem and solution dynamics, various inspection techniques are employed throughout the production cycle. One common method involves visual inspections where operators closely examine each batch for any visible defects such as warping or surface imperfections that could compromise functionality. This initial step lays the groundwork for more advanced testing methods.
Another effective technique is dimensional analysis using precision measurement tools to ensure that each part meets specified tolerances—essential when working with small components where margins for error are minimal. Additionally, non-destructive testing methods such as ultrasonic or X-ray inspections can be utilized to assess internal structures without damaging the molded parts themselves.
Lastly, utilizing automated inspection systems integrated with machine vision technology has become increasingly popular in modern manufacturing settings. These systems provide real-time feedback during production runs of plastic injection molding molds to quickly identify deviations from established quality standards before they escalate into larger issues.
Case Study: Baoyuan's Approach to Quality
Baoyuan has become a leading name in tackling injection molding small parts problem and solution scenarios through its innovative approach to quality control. They employ a comprehensive strategy that combines traditional inspection techniques with cutting-edge technology like AI-driven analytics to monitor production processes continuously. This dual approach allows them not only to detect defects but also predict potential failures before they occur.
Their rigorous training programs for staff emphasize the importance of attention to detail during every phase of mould plastic injection—from design through final inspection—ensuring everyone understands their role in maintaining high-quality standards across all operations involving plastic injection molding molds. Furthermore, Baoyuan’s commitment to sustainability means they frequently revisit their practices to minimize waste while maximizing efficiency without compromising on quality.
By integrating these methodologies into their workflow, Baoyuan successfully reduces costs related to rework while enhancing overall product reliability—a true testament to how proactive measures in quality assurance can yield substantial benefits within the realm of small part manufacturing.
Innovative Solutions for Injection Molding Challenges
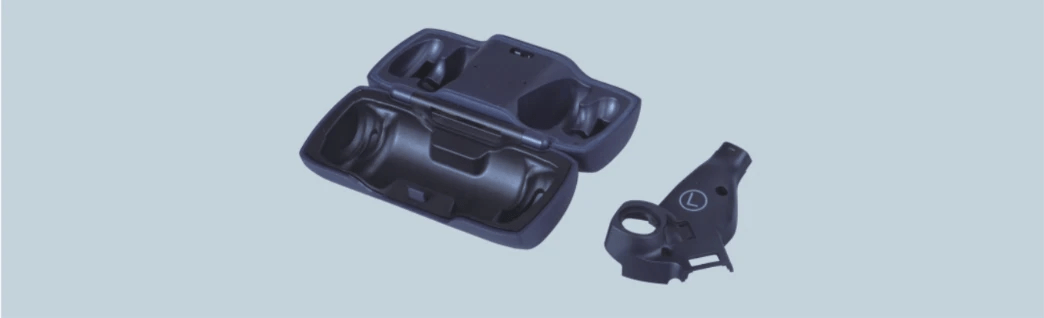
In the ever-evolving landscape of injection molding, innovative solutions are essential to overcoming the challenges associated with producing small parts. The integration of advanced technologies, thoughtful design considerations, and simulation software has led to significant improvements in efficiency and quality. By addressing the injection molding small parts problem and solution through these methods, manufacturers can enhance their production processes and outcomes.
Advanced Technologies in Mould Injection Moulding
The advent of advanced technologies in mould injection moulding has revolutionized how manufacturers approach the production of small plastic components. Techniques such as multi-material injection molding allow for greater flexibility in design and functionality, enabling the creation of complex geometries that were previously unattainable. Additionally, innovations like hot runner systems streamline material flow, reducing waste and improving cycle times—critical factors when tackling injection molding small parts problems.
Another notable advancement is the use of electric injection molding machines that provide precise control over temperature and pressure during the process. This precision is vital for achieving uniformity across batches of small parts, minimizing defects associated with traditional hydraulic systems. Moreover, advancements in sensor technology enhance real-time monitoring capabilities, allowing manufacturers to identify potential issues early on and implement corrective actions swiftly.
Furthermore, additive manufacturing techniques are increasingly being integrated into traditional plastic injection molding processes. By utilizing 3D printing for creating molds or prototypes, companies can significantly reduce lead times while maintaining high-quality standards in their final products. These advanced technologies collectively represent a robust arsenal against common challenges faced in producing small parts via plastic injection molding.
Design Considerations for Small Parts
Design plays a pivotal role in overcoming challenges related to injection molding small parts problems. When creating molds for tiny components, engineers must consider factors such as wall thickness consistency and draft angles to facilitate easy ejection from molds without compromising structural integrity. Failing to account for these elements can lead to defects that not only affect appearance but also functionality.
Additionally, utilizing design techniques like ribbing or integrating features directly into parts can enhance their strength without adding unnecessary weight or complexity. This optimization is crucial when working with injection moldable plastics that may have limitations regarding tensile strength or flexibility under stress conditions commonly encountered during use. By prioritizing smart design choices tailored specifically for small parts production within mold plastic injection frameworks, manufacturers can mitigate potential issues before they arise.
Collaboration between designers and engineers is also essential during this phase; feedback loops ensure that practical manufacturing considerations are incorporated into initial designs from the outset rather than being retrofitted later on—a common pitfall leading to increased costs and delays down the line.
Using Simulation Software in Design
Simulation software has become an indispensable tool for addressing many complexities involved in plastic injection molding processes—particularly when it comes to designing molds for intricate small parts. These programs allow engineers to model different scenarios virtually before committing resources to physical prototypes or production runs—saving both time and money while enhancing product quality overall.
By simulating various aspects such as material flow dynamics within molds or thermal profiles throughout cycles using advanced computational fluid dynamics (CFD) tools among others; teams gain insights into potential bottlenecks or defects long before they manifest physically on factory floors! This proactive approach enables informed decision-making regarding adjustments needed either at design stages—or even modifications required post-production if unexpected issues arise due too high pressures causing warping effects etc., ultimately leading towards achieving better results faster!
Moreover, simulation software facilitates collaboration across departments by providing visual representations easily understood by stakeholders from engineering through marketing teams alike—ensuring everyone remains aligned throughout development phases! Embracing this technology empowers companies not only solve existing challenges effectively but also stay ahead amidst rapid advancements shaping future landscapes surrounding manufacturing practices today!
The Future of Injection Molding Small Parts
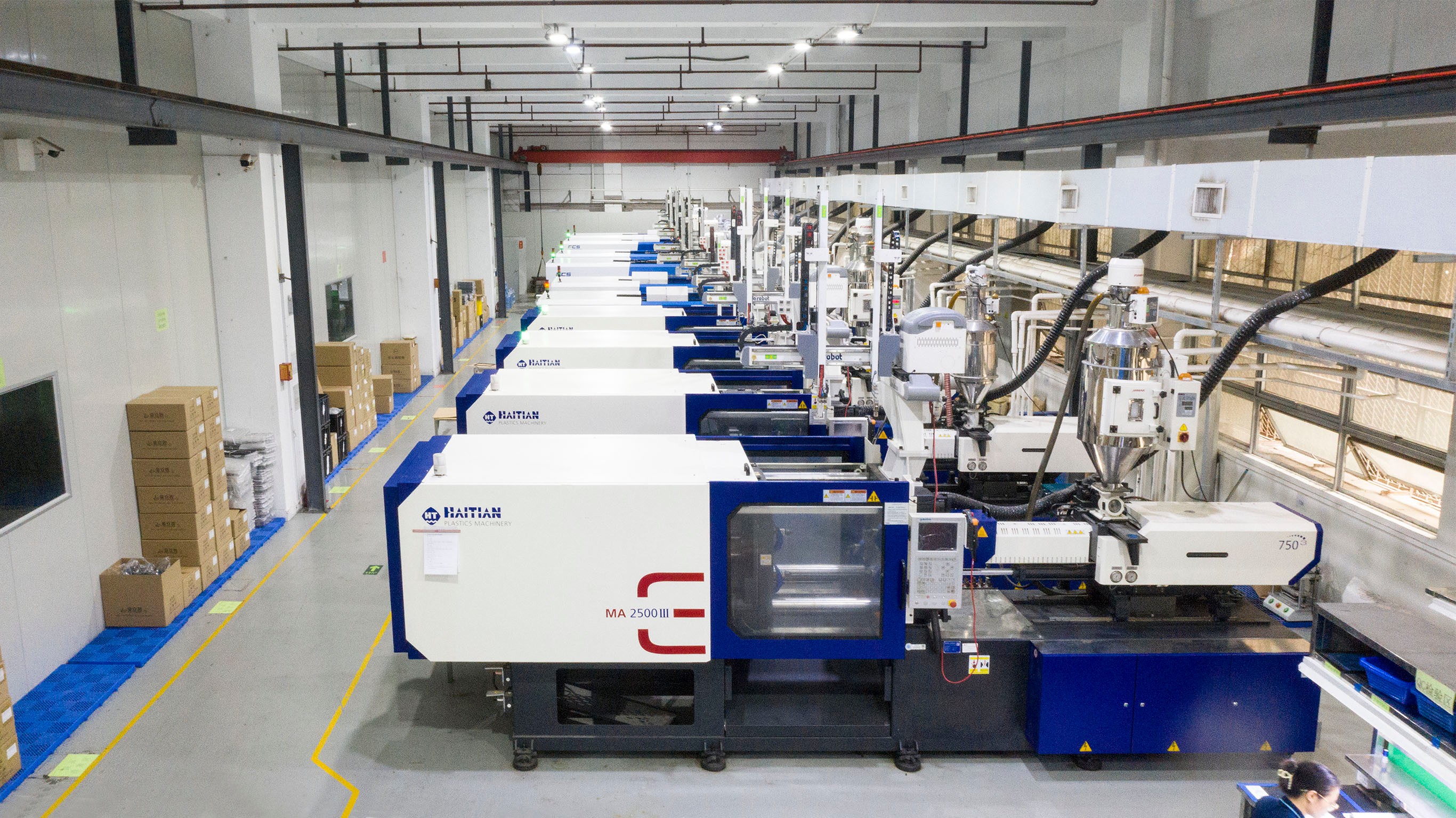
The future of injection molding small parts is brimming with potential as industries evolve and adapt to new technologies and consumer demands. With the continuous push for smaller, more intricate designs, the injection molding process must keep pace to address the unique challenges that arise. This section will explore emerging trends, the integration of automation and AI, and sustainable practices in mould plastic injection.
Trends in Plastic Injection Molding
One notable trend in plastic injection molding is the shift toward lighter materials that enhance product performance while reducing manufacturing costs. Manufacturers are increasingly opting for advanced injection moldable plastics that offer superior strength-to-weight ratios, making them ideal for small parts applications across various sectors. Additionally, customization has become a focal point; as businesses seek tailored solutions, flexible production methods are being implemented to accommodate diverse design specifications.
Another trend shaping the future is rapid prototyping combined with traditional injection molding techniques. This approach allows for quicker iterations and refinements of designs, significantly shortening time-to-market for new products. Moreover, advancements in 3D printing technology are being integrated into mould design processes to create complex geometries that were once deemed impossible with standard methods.
Finally, there’s a growing emphasis on smart manufacturing systems within plastic injection molding facilities. These systems leverage data analytics to optimize production efficiency and minimize waste by predicting maintenance needs and adjusting processes in real-time. As companies embrace these trends, they will find innovative solutions to common injection molding small parts problems while enhancing overall productivity.
The Role of Automation and AI
Automation is revolutionizing the landscape of plastic injection molding by streamlining operations and reducing human error. Automated systems can handle repetitive tasks such as material handling or quality checks more efficiently than manual labor can manage them. The integration of AI further enhances this process by predicting potential issues before they escalate into significant defects during production runs.
Injection molding machines equipped with AI capabilities can analyze vast amounts of data from previous cycles to fine-tune parameters automatically—ensuring optimal conditions are maintained throughout the entire manufacturing process. This not only improves output quality but also reduces downtime caused by machine adjustments or repairs related to common problems encountered with small part production.
Additionally, robotics play a crucial role in increasing flexibility within manufacturing lines dedicated to mould plastic injection processes. By allowing quick changes between different product lines without extensive reconfiguration time or labor costs, manufacturers are better positioned to respond swiftly to market demands while maintaining high standards of quality assurance.
Sustainability in Mould Plastic Injection
Sustainability has become an essential consideration within the realm of plastic injection molding as environmental concerns grow among consumers and regulators alike. Companies are now prioritizing eco-friendly practices throughout their operations—from sourcing raw materials made from recycled content to adopting energy-efficient machinery designed specifically for lower emissions during production cycles involving small parts.
Moreover, sustainable mould design seeks not only to reduce waste but also improve recyclability post-consumer use through innovative strategies like using biodegradable plastics or developing multi-use molds that minimize material loss during fabrication processes such as mold plastic injection techniques employed today. By investing in these sustainable alternatives, manufacturers can address both their carbon footprint concerns while simultaneously tackling common problems associated with traditional plastics used in small part applications.
Lastly, collaborations between industry stakeholders—including suppliers focused on green materials—are becoming increasingly popular as companies work together toward shared sustainability goals within their supply chains related directly back into effective solutions addressing ongoing challenges faced by those involved with injecting molded components regularly produced worldwide.
Conclusion
In the world of manufacturing, the challenges associated with injection molding small parts are multifaceted and complex. From identifying defects to ensuring that mold design meets stringent specifications, companies face a myriad of hurdles in the quest for precision and efficiency. However, by understanding these challenges and implementing effective strategies, businesses can optimize their processes and enhance product quality.
Summarizing Key Injection Molding Challenges
The landscape of plastic injection molding presents several significant challenges, particularly when it comes to small parts. Issues such as dimensional accuracy, surface finish defects, and material selection can severely impact production efficiency. Additionally, problems in mould design and construction often lead to increased cycle times and waste—issues that can be detrimental in a competitive market focused on cost-effectiveness.
Effective Strategies for Problem Solving
To tackle the injection molding small parts problem and solution effectively, companies must adopt a proactive approach that includes rigorous quality control measures. Utilizing advanced technologies like simulation software can help identify potential issues before they arise during production. Furthermore, investing in high-quality injection molding machines specifically designed for small parts ensures precision while reducing the likelihood of defects during the mould injection moulding process.
Moving Forward in Small Parts Manufacturing
Looking ahead, the future of plastic injection molding will undoubtedly be shaped by innovation and sustainability practices. As industries increasingly prioritize eco-friendly solutions, manufacturers must adapt their processes to incorporate sustainable materials into their mold plastic injection practices. Embracing automation and artificial intelligence will also play a crucial role in enhancing productivity while addressing common challenges associated with small part production.