Introduction
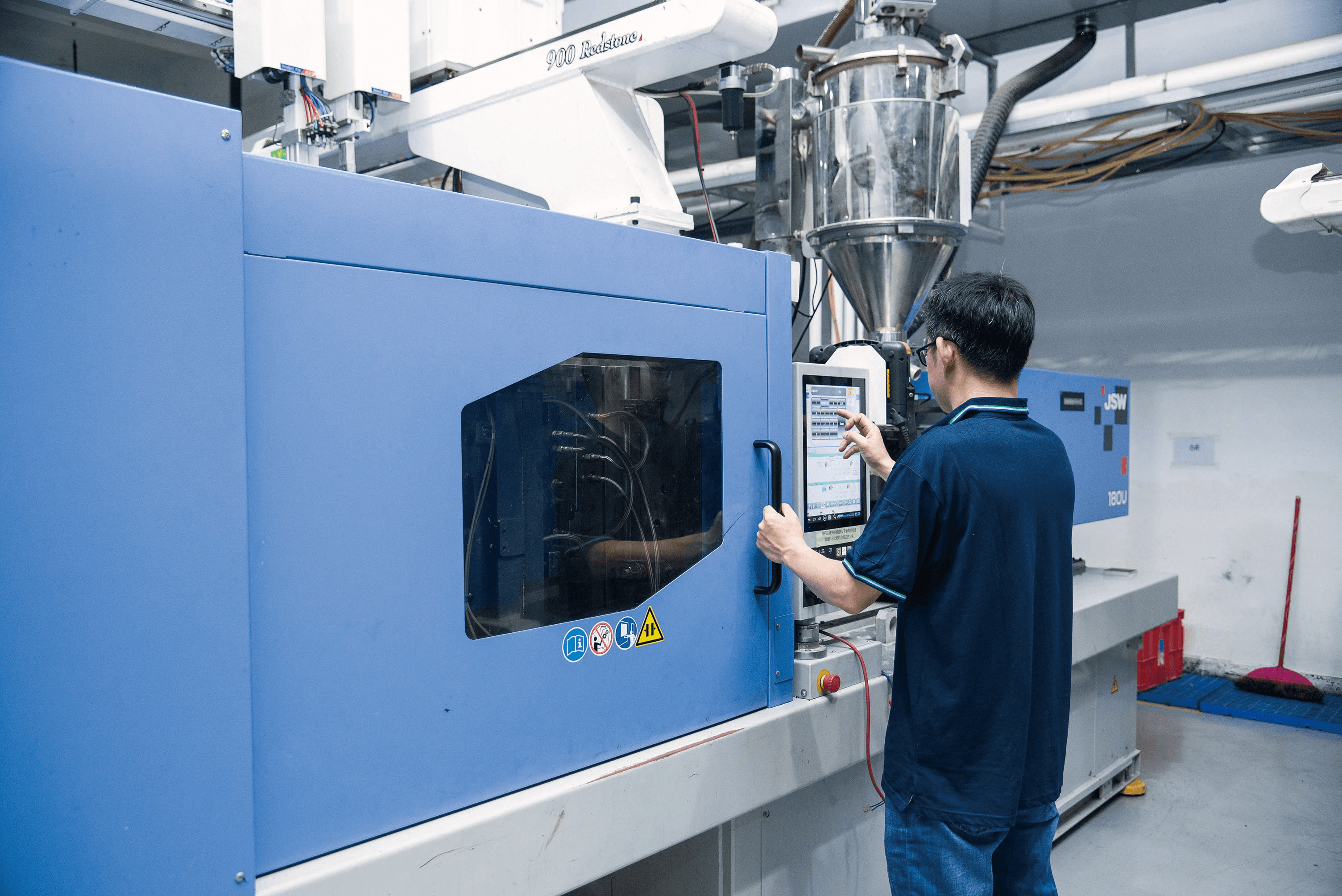
In the world of manufacturing, the quest for materials that combine strength, versatility, and cost-effectiveness is never-ending. One such material that has carved a niche for itself is ABS (Acrylonitrile Butadiene Styrene), known for its impressive properties and wide-ranging applications. Whether it’s in consumer electronics, automotive parts, or household goods, injection molded ABS stands out as a preferred choice due to its durability and adaptability.
Understanding ABS and Its Applications
ABS plastic is a type of thermoplastic polymer that boasts excellent impact resistance and toughness. Its unique composition allows it to be molded into complex shapes while maintaining structural integrity—a crucial factor in many industries. From toys to appliance housings, the applications of injection molded ABS are vast, making it an essential material in modern manufacturing.
What is Injection Molding?
Injection molding is a manufacturing process where molten plastic is injected into a mold to create specific shapes and designs. This method allows for high-volume production with remarkable precision and repeatability—two key factors that drive efficiency in manufacturing. By utilizing injection moldable plastics like ABS, manufacturers can produce intricate components quickly and economically.
Why Choose ABS for Your Products?
Choosing ABS for your products offers numerous advantages that can enhance both functionality and aesthetic appeal. Its ability to be easily colored and finished makes it ideal for consumer-facing products where visual impact matters. Additionally, the cost-effectiveness of using ABS in plastic injection molding ensures that businesses can maintain quality while keeping production costs low.
The Basics of Injection Molded ABS
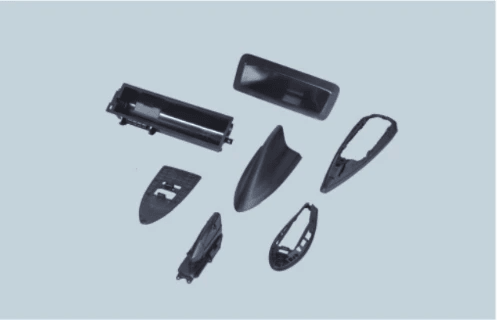
When diving into the world of injection molded ABS, it’s essential to grasp the fundamental aspects that make this material a popular choice in various industries. From its remarkable properties to the advantages offered by the injection molding process, understanding these basics can help you appreciate why ABS is often selected for product development. Let’s explore what makes ABS plastic stand out and how it benefits manufacturers and consumers alike.
Properties of ABS Plastic
ABS plastic, short for Acrylonitrile Butadiene Styrene, is renowned for its robust properties that lend themselves well to injection molding applications. One of its key characteristics is its excellent impact resistance, making it durable enough to withstand rough handling and environmental stressors. Additionally, injection molded ABS exhibits good thermal stability and chemical resistance, ensuring that products maintain their integrity over time.
Another significant property of ABS is its ease of processing through mould injection moulding techniques. This thermoplastic can be molded into intricate shapes with precision, allowing for complex designs in various applications. Furthermore, ABS plastic can be easily colored or finished to meet aesthetic requirements without compromising its structural integrity.
Benefits of Using Injection Molding
The benefits of using injection molding with ABS are numerous and compelling for manufacturers looking to optimize production processes. First off, plastic injection molding allows for high-volume production at a rapid pace, significantly reducing lead times compared to traditional manufacturing methods. This efficiency translates into cost savings and quicker time-to-market for new products.
Moreover, the versatility of injection moldable plastics like ABS enables designers to create parts with intricate geometries that might be challenging or impossible with other materials or methods. The ability to produce consistent quality across batches also enhances product reliability—an essential factor in maintaining customer satisfaction and brand reputation. Lastly, using mould plastic injection techniques minimizes waste material since excess plastic can often be recycled back into the process.
Common Applications of ABS
Injection molded ABS finds itself at home in a variety of applications across different sectors due to its favorable properties and processing advantages. In consumer electronics, it’s commonly used for housings and components because it can withstand impacts while maintaining a sleek appearance—think mobile phone cases or laptop shells! Similarly, automotive parts made from injection molded ABS contribute not only to vehicle aesthetics but also enhance durability against wear and tear.
Beyond electronics and automotive applications, this versatile material plays a crucial role in household goods such as kitchenware or toys where safety and durability are paramount considerations. Its ability to be easily colored allows manufacturers to create vibrant designs that appeal to consumers’ tastes while ensuring that products remain functional over time. Overall, the widespread use of abs plastic across diverse industries showcases its adaptability as an ideal choice for modern manufacturing needs.
Injection Molding Process Steps
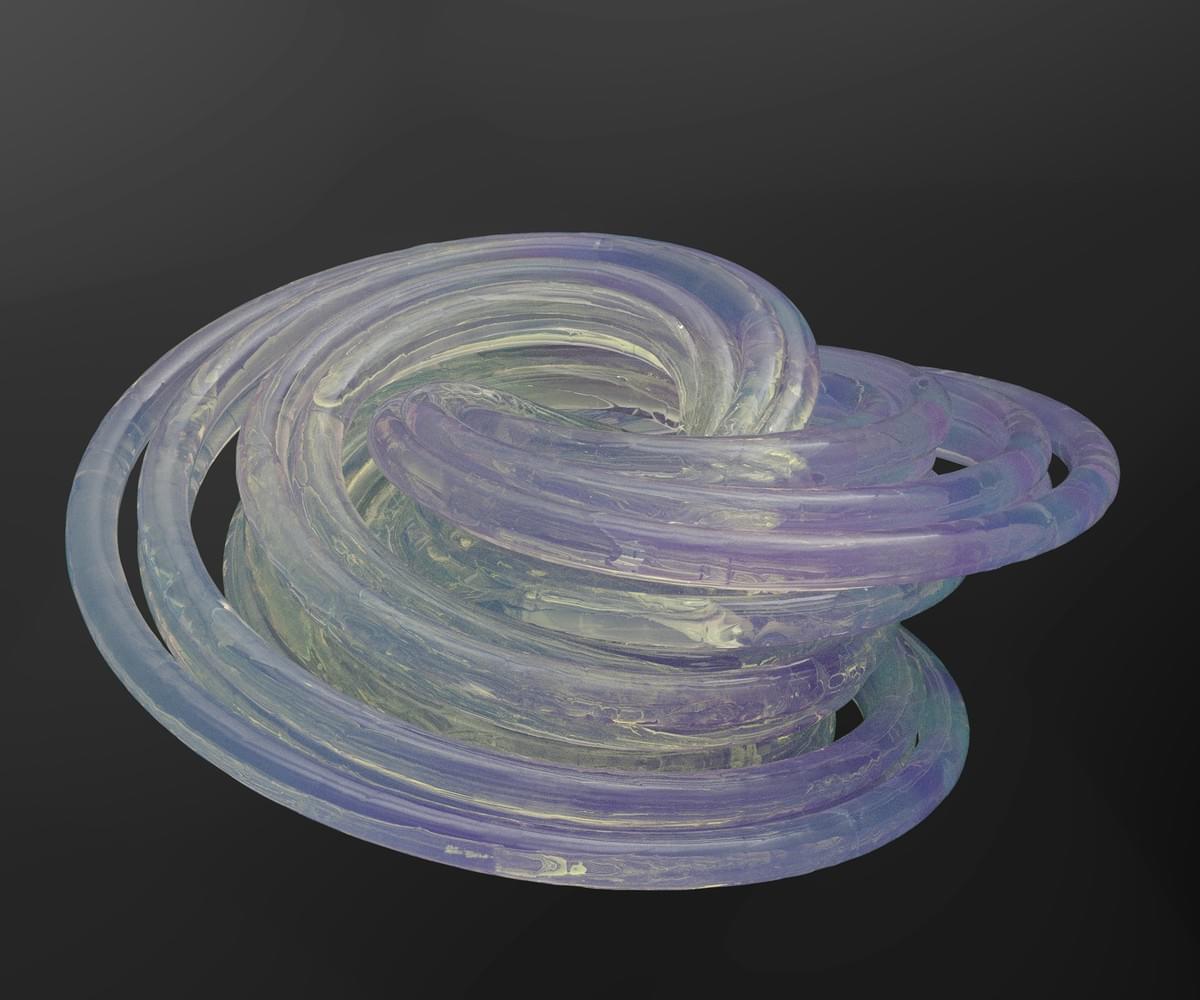
The injection molding process is a sophisticated sequence that transforms raw materials into finished products, particularly using ABS plastic. Understanding the steps involved can help you appreciate how injection molded ABS achieves its remarkable properties and versatility. Let's break down this process into three key components: designing the injection mold, preparing materials, and executing the injection molding cycle.
Designing the Injection Mold
The design of the injection mold is crucial as it dictates the final shape and quality of the product made from ABS plastic. Engineers use computer-aided design (CAD) software to create precise models that account for factors such as cooling channels, ejection systems, and parting lines. A well-designed mold ensures that every batch of injection molded ABS maintains consistency in quality while optimizing production efficiency.
In addition to functionality, aesthetics play a role in mold design; after all, no one wants a product that looks like it was made in a rush! The complexity of the design can also impact costs—more intricate molds typically require more time and resources to produce. Ultimately, investing time in designing an effective plastic injection molding mold pays off in terms of reduced waste and enhanced product integrity.
Materials Preparation for Mould Injection Moulding
Before diving into mould injection moulding, preparing your materials is essential to ensure optimal performance during production. For ABS plastic, this means selecting high-quality resin pellets that meet specific requirements for your application—after all, not all plastics are created equal! These pellets must be dried properly to eliminate moisture content which could lead to defects during molding.
Once prepared, these resin pellets are fed into an extruder where they’re heated until they reach a molten state suitable for injection molding. This stage requires careful temperature control since overheating can degrade the material properties of ABS plastic while underheating may result in poor flow characteristics during filling. Properly prepared materials lead to smooth operations throughout the entire process of plastic injection molding.
The Injection Molding Cycle
The heart of the operation lies within the injection molding cycle itself—a series of steps designed to transform molten material into solid forms efficiently. Initially, molten ABS is injected at high pressure into a pre-designed mold cavity through a nozzle connected to an extruder unit. Once filled, cooling begins as temperature-controlled water circulates around the mold; this stage solidifies your product while keeping its dimensions accurate.
After sufficient cooling time has elapsed—typically measured in seconds—the mold opens up to eject your newly formed piece from its confines via ejection pins or plates designed specifically for this purpose. It's worth noting that maintaining precision throughout this cycle is vital since even minor deviations can affect overall quality and performance characteristics of your final product made with injection molded ABS.
With these steps completed successfully, you have transformed raw materials into functional products ready for market use!
Advantages of Using ABS in Injection Molding

When it comes to injection molded ABS, the advantages are numerous and compelling. This thermoplastic is not just a favorite among manufacturers but also a reliable choice for a variety of applications. Let's dive into why ABS shines in the realm of plastic injection molding.
Durability and Impact Resistance
One of the standout features of ABS plastic is its exceptional durability and impact resistance. This makes injection molded ABS products ideal for use in environments where they may face rough handling or stress. Whether it's automotive parts or consumer electronics, the ability to withstand impacts without cracking ensures longevity and reliability.
Furthermore, this material maintains its integrity over time, resisting wear and tear better than many other injection moldable plastics. The combination of toughness and resilience means that products made from ABS can endure challenging conditions, making them a smart choice for businesses aiming to produce high-quality goods. With such durability, manufacturers often find that their investment in mould injection moulding pays off through reduced replacement costs.
Cost-Effectiveness in Production
Cost-effectiveness is a significant factor driving the popularity of ABS in plastic injection molding processes. The efficiency of mould plastic injection techniques allows for high-volume production without sacrificing quality—resulting in lower per-unit costs. Manufacturers can produce intricate designs at scale while keeping overhead expenses manageable.
Moreover, ABS's relatively low material cost contributes to overall savings during production runs. When combined with its ease of processing through various plastic injection molding molds, it becomes clear why many companies choose this material over others that may require more expensive processing or raw materials. Ultimately, using injection molded ABS helps businesses maximize their profitability while maintaining product excellence.
Versatility in Design
The versatility inherent in using ABS for mould injection moulding cannot be overstated; it opens up endless design possibilities for engineers and designers alike. With excellent flow characteristics during the melting process, this material allows for complex shapes and detailed features that would be challenging with other plastics. From sleek consumer gadgets to robust industrial components, the design options are virtually limitless when working with this adaptable thermoplastic.
Additionally, ABS can be easily colored or textured during manufacturing processes, providing further customization options that appeal to various markets and consumer preferences. This adaptability not only enhances aesthetic appeal but also enables manufacturers to cater to specific industry needs effectively—be it automotive parts requiring specific finishes or household items needing vibrant colors. In short, when it comes to versatility in design within plastic injection molding projects, few materials rival what injection molded ABS can offer.
Choosing the Right Injection Molding Partner
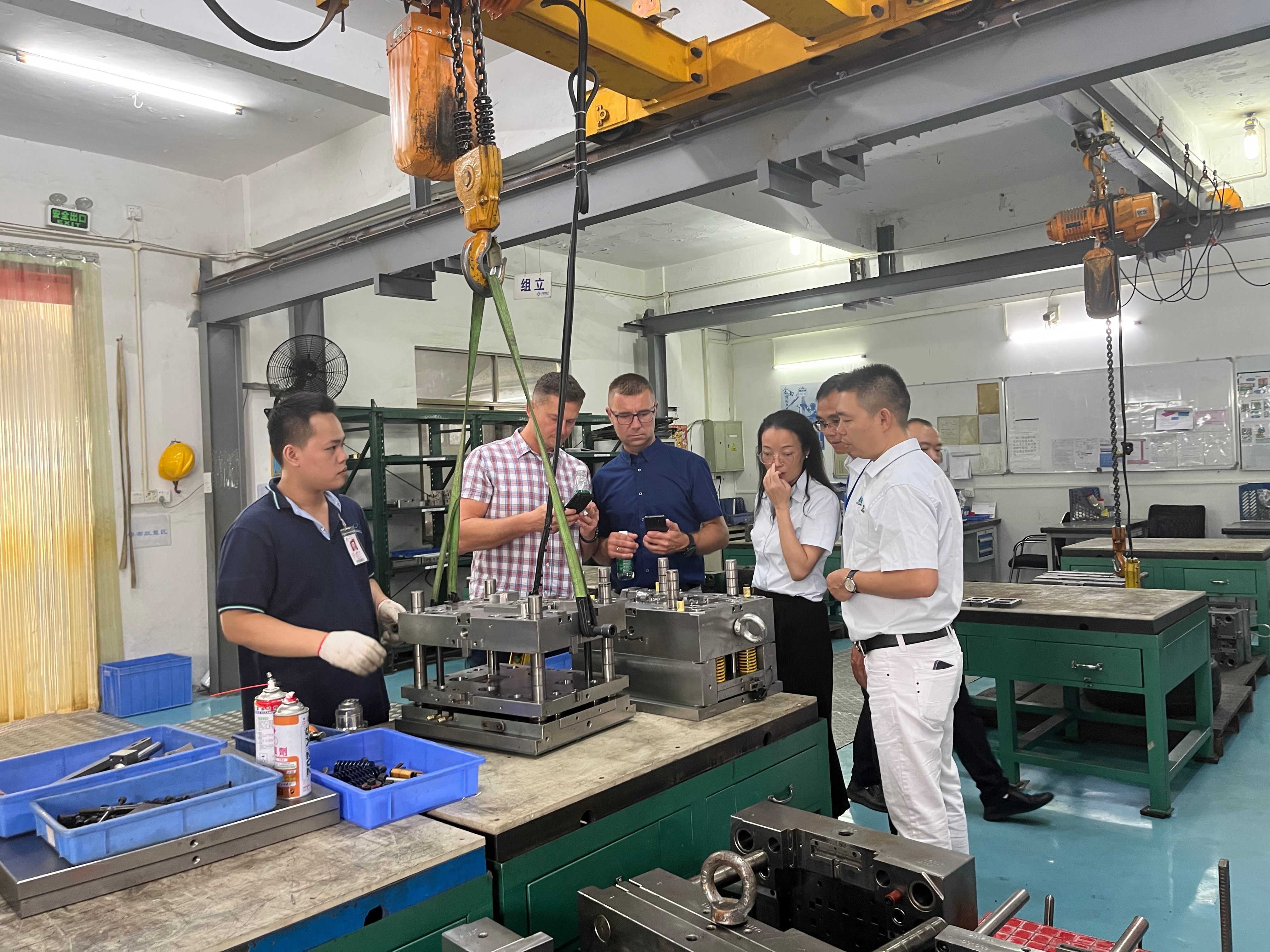
Selecting the right injection molding partner is crucial for ensuring high-quality products made from injection molded ABS. The right partner can make a significant difference in your production efficiency, cost-effectiveness, and overall product quality. With so many options available, it’s essential to evaluate potential partners carefully.
Baoyuan: A Trusted Industry Leader
When it comes to injection molding, Baoyuan stands out as a trusted industry leader known for its expertise in mould injection moulding and plastic injection molding. Their commitment to quality and innovation has made them a go-to choice for companies seeking reliable solutions for their ABS plastic needs. With advanced technology and skilled professionals, Baoyuan ensures that every piece of injection molded ABS meets rigorous standards.
Baoyuan's extensive experience with various industries allows them to tailor their services according to specific project requirements. They utilize state-of-the-art machinery that enhances precision and efficiency in the production of mold plastic injections. This dedication helps clients achieve optimal results while minimizing waste and production time.
Factors to Consider in Selecting a Partner
Choosing the right partner for your plastic injection molding needs involves several key factors that can influence your project's success. First, assess their expertise with injection moldable plastics like ABS; this knowledge is vital for achieving high-quality outcomes. Additionally, consider their capability to handle complex designs and large-scale productions without compromising on quality.
Another important factor is the availability of advanced technology and equipment for mould injection moulding processes. A partner with cutting-edge machinery can significantly enhance productivity while ensuring consistent quality across all products made from ABS plastic. Lastly, communication is paramount; ensure your chosen partner values transparency and keeps you informed throughout the production process.
Questions to Ask During Consultation
During your initial consultation with potential partners, asking the right questions can help you gauge their suitability for your project involving injection molded ABS. Start by inquiring about their experience with similar projects; understanding their track record will provide insight into their capabilities in handling specific challenges related to plastic injection molding molds.
Next, discuss their quality assurance practices; ask how they ensure consistency and reliability in every batch of injected molds produced from ABS plastic. Finally, don't hesitate to ask about lead times and flexibility; knowing how quickly they can adapt to changes or scale up production will be crucial as you navigate through market demands.
Quality Assurance in Plastic Injection Molding
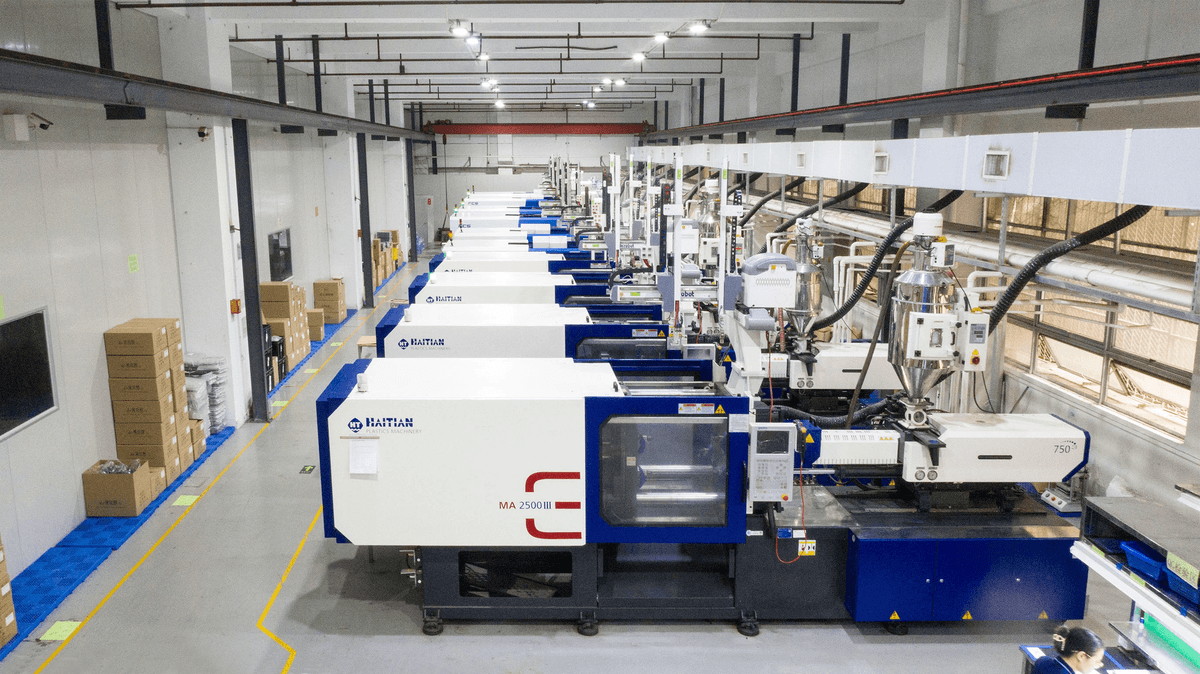
Quality assurance in plastic injection molding is not just a checkbox on the production list; it’s the foundation upon which successful products are built. When dealing with injection molded ABS, maintaining high-quality standards ensures that the final products meet customer expectations and industry regulations. A commitment to quality can significantly enhance brand reputation and customer loyalty.
Importance of Quality in ABS Products
The importance of quality in ABS products cannot be overstated, especially when considering their applications across various industries. High-quality injection molded ABS components exhibit superior durability, impact resistance, and aesthetic appeal, making them ideal for consumer goods, automotive parts, and electronics. Poorly manufactured ABS products can lead to failures that not only affect performance but also pose safety risks to users.
In the realm of plastic injection molding, ensuring consistent quality helps manufacturers avoid costly recalls and rework processes. By investing in robust quality assurance practices, companies can minimize defects and enhance the overall reliability of their injection moldable plastics. Ultimately, a focus on quality translates into better product performance and a stronger market position.
Techniques for Ensuring Quality Control
To ensure quality control in mould injection moulding processes, several techniques are employed throughout production stages. One common method involves implementing statistical process control (SPC), which monitors production parameters to detect variations before they result in defects. Regular inspections during different phases of the plastic injection molding cycle help identify issues early on.
Another effective technique is utilizing advanced testing methods such as tensile strength testing or impact resistance tests for finished injection molded ABS components. These tests verify that the properties of ABS plastic meet specified standards and performance requirements before they reach consumers. Additionally, employing automated inspection systems can enhance accuracy by detecting flaws that may go unnoticed during manual checks.
Training personnel involved in the plastic injection molding process is equally vital for ensuring quality control. Skilled workers who understand best practices contribute significantly to maintaining high standards throughout production while minimizing human error.
Certification Standards for Mould Plastic Injection
Certification standards play a crucial role in establishing trust between manufacturers and customers regarding product quality in mould plastic injection processes. Various international standards exist—such as ISO 9001—that outline requirements for effective quality management systems within manufacturing environments where plastic injection molding occurs. Compliance with these standards reassures clients that their products are produced under stringent guidelines.
Moreover, specific certifications related to materials like ABS plastic ensure that manufacturers adhere to safety regulations applicable to their respective industries—be it automotive or medical devices. These certifications often involve thorough audits and assessments by third-party organizations dedicated to evaluating compliance with established criteria.
Staying updated with evolving certification requirements is essential for companies involved in injecting molded plastics since non-compliance can lead to significant consequences including legal penalties or loss of market access. Thus, investing time and resources into achieving these certifications not only enhances product credibility but also supports continuous improvement initiatives within organizations.
Conclusion
As we wrap up our exploration of injection molded ABS, it’s clear that this material is a powerhouse in the world of plastic manufacturing. From its impressive durability to its cost-effective nature, injection molded ABS stands out as a prime choice for various applications. Understanding the intricacies of injection molding and the advantages of ABS can empower businesses to create superior products that meet market demands.
Key Takeaways on Injection Molded ABS
When considering plastic injection molding, one must recognize the unique properties of ABS plastic that make it an ideal candidate for many projects. Its impact resistance and versatility in design are significant benefits that enhance product performance and aesthetic appeal. Additionally, the efficiency of mould injection moulding processes ensures that production can be scaled effectively without compromising quality.
Future Trends in Injection Molding
The future of injection molding is bright, with advancements in technology leading to more efficient processes and sustainable practices. Innovations such as 3D printing integration and smart manufacturing techniques are set to revolutionize how we approach mold plastic injection. Moreover, the demand for eco-friendly materials will likely influence the development of new types of injection moldable plastics, including bio-based alternatives to traditional ABS.
Making Informed Choices for Your Products
Choosing the right materials and processes is crucial when developing products using plastic injection molding. By understanding the strengths of injection molded ABS and collaborating with a reputable partner like Baoyuan, businesses can ensure high-quality outcomes tailored to their specific needs. Ultimately, informed choices lead to better products, satisfied customers, and a competitive edge in today’s fast-paced market.