Introduction
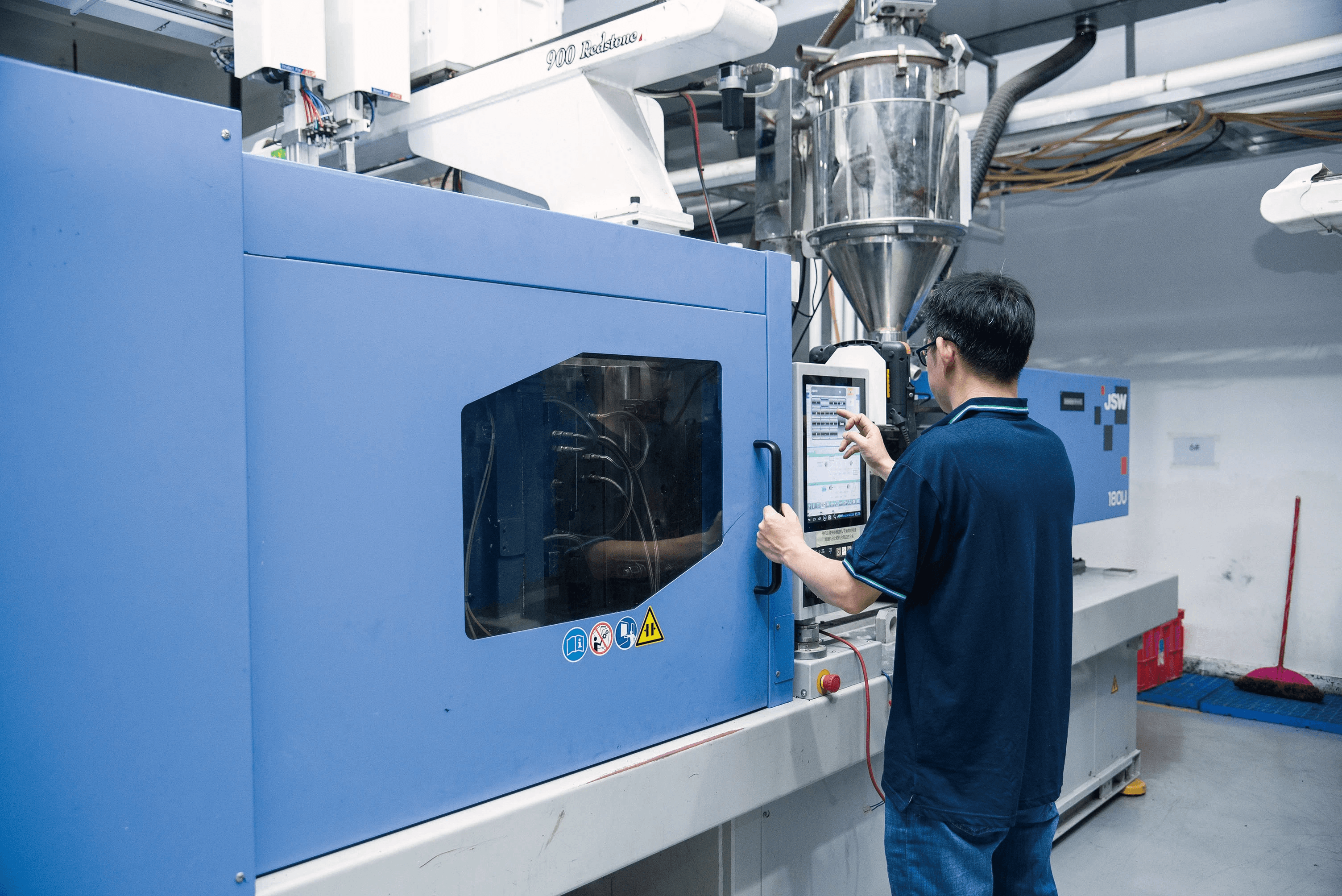
Injection molding has become a cornerstone of modern manufacturing, revolutionizing the way we produce plastic products. This process involves injecting molten plastic into a mold to create complex shapes with high precision and efficiency. As the demand for durable and versatile materials grows, understanding the advantages of injection moulding is essential for businesses looking to stay competitive in the ever-evolving landscape of plastic manufacturing.
Understanding Injection Molding Basics
At its core, injection molding is a method that transforms raw plastic into finished products through a series of steps involving heating, injecting, and cooling. The process begins with melting plastic pellets, which are then injected into a precisely designed mold under high pressure. Once cooled, the solidified product is ejected from the mold—this efficient cycle allows for rapid production rates that make it a popular choice among manufacturers.
The Rise of Plastic Manufacturing
The rise of plastic manufacturing can be attributed to the material's versatility and adaptability across various industries. From automotive components to consumer electronics, plastics have found their way into nearly every aspect of our daily lives due to their lightweight nature and resistance to corrosion. As technology advances, more innovative applications for injection moldable plastics emerge, driving further growth in this vital sector.
Why Explore Advantages and Disadvantages
While injection molding presents numerous advantages—such as cost-effectiveness and precision—it’s crucial to also consider its disadvantages before diving in headfirst. Understanding both sides helps businesses make informed decisions about whether this method aligns with their production needs and sustainability goals. By exploring the full spectrum of benefits and challenges associated with mould injection moulding, companies can strategically navigate their options in an increasingly complex market.
What is Injection Molding?
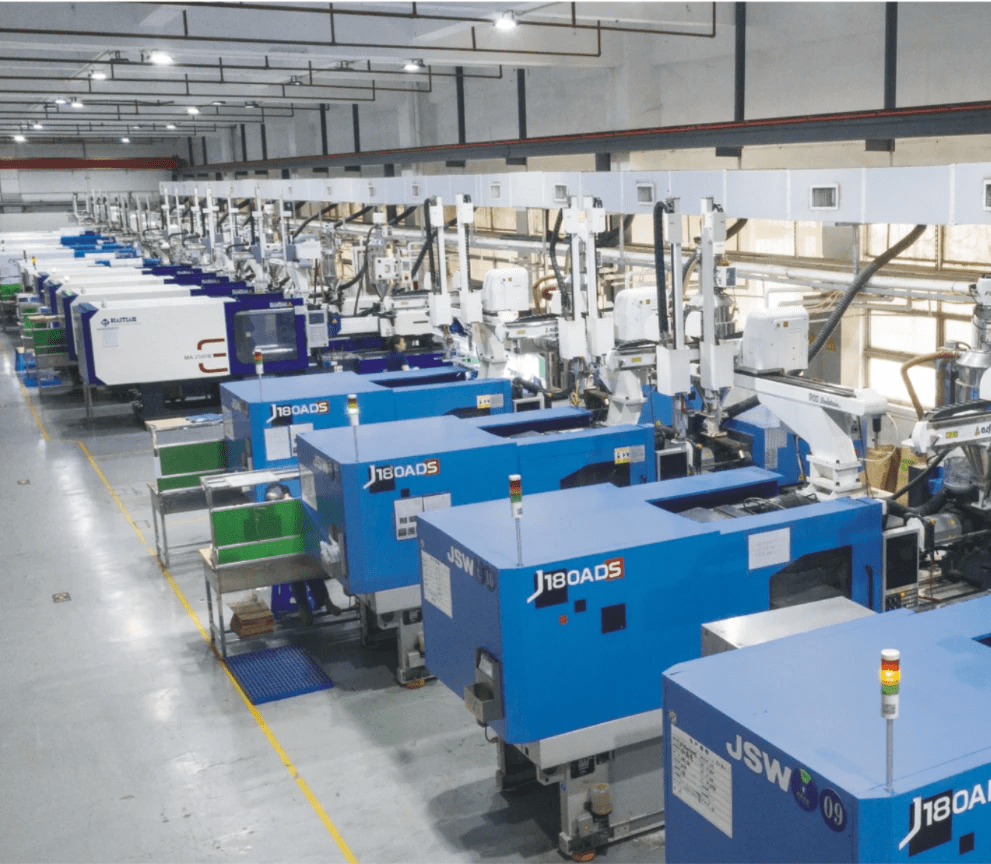
Injection molding is a widely used manufacturing process that transforms plastic materials into various shapes and products. This technique involves injecting molten plastic into a mold, where it cools and solidifies into the desired form. The efficiency and versatility of this method have made it a cornerstone of modern plastic manufacturing.
Process Overview of Mould Injection Moulding
The mould injection moulding process begins with the selection and preparation of raw plastic materials, which are typically in pellet form. These pellets are heated until they melt, creating a viscous liquid that can be injected into a pre-designed mold cavity under high pressure. Once the molten plastic fills the mold, it cools down to solidify before being ejected as a finished product, showcasing one of the key advantages of injection moulding: rapid production cycles.
This process allows for high-volume production while maintaining precision in each piece manufactured. Additionally, modern advancements have streamlined this process even further by incorporating automated systems for loading materials and removing finished products. As such, companies can produce intricate designs consistently, making injection molding an attractive option in various industries.
Key Components of Plastic Injection Molding
Understanding the key components involved in plastic injection molding is crucial for grasping how this method works effectively. The main components include the injection unit, which melts and injects the plastic; the clamping unit, which holds the mold closed during injection; and the mold itself, designed to shape the molten material into specific forms. Each component plays a vital role in ensuring that high-quality molded parts are produced efficiently.
The injection unit consists of several parts such as heaters to maintain optimal temperatures and screws for mixing materials thoroughly before injecting them into molds. The clamping unit not only secures the mold but also ensures that it withstands high pressures during production without leaking or deforming. Together, these components exemplify why many manufacturers favor using injection molding over other methods for creating complex shapes with minimal waste.
Types of Injection Moldable Plastics
A wide range of materials can be used in injection molding processes—each with its unique properties suited to different applications. Common types of injection moldable plastics include thermoplastics like polyethylene (PE), polypropylene (PP), polystyrene (PS), and polyvinyl chloride (PVC). These materials offer excellent durability and flexibility while being easy to shape through techniques like mould injection moulding.
Thermosetting plastics are another category often utilized; they harden permanently after being molded once heated—making them ideal for applications requiring stability under heat or pressure. Additionally, specialty plastics such as nylon or acrylonitrile butadiene styrene (ABS) provide enhanced strength or impact resistance for specific industrial needs. By selecting appropriate types of plastics based on their properties, manufacturers can fully leverage the advantages of injection moulding across diverse sectors.
Advantages of Injection Molding
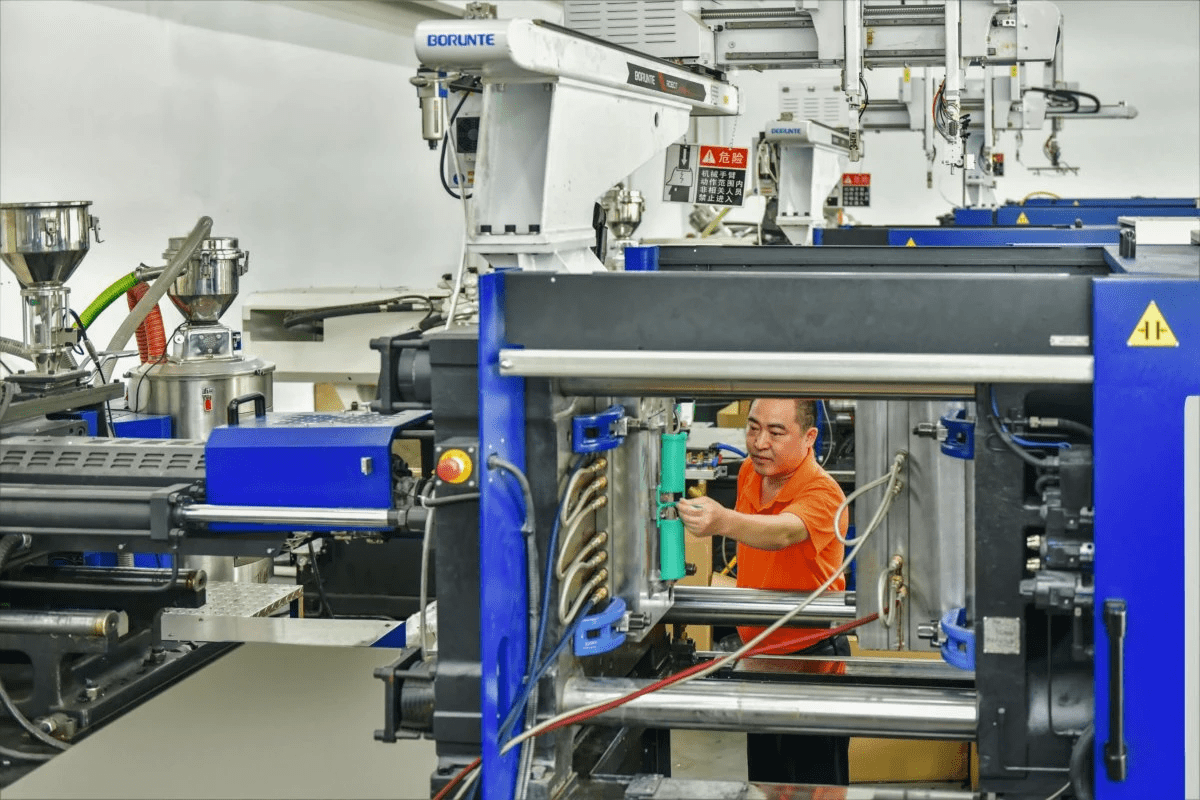
When it comes to the world of plastic manufacturing, injection molding stands out for its remarkable advantages. This process not only revolutionizes how products are made but also sets a high bar for efficiency and quality in production. Let’s dive into the specific benefits that make injection molding a go-to choice for manufacturers.
High Efficiency in Production
One of the standout advantages of injection moulding is its high efficiency in production. The mould injection moulding process allows for rapid cycle times, meaning that manufacturers can produce large quantities of items in a relatively short period. This efficiency is particularly beneficial when dealing with mold plastic injection, as it maximizes output while minimizing downtime between production runs.
Additionally, once the initial setup is complete, the process can be automated to run continuously without significant human intervention. This automation not only speeds up production but also reduces labor costs over time—another win for those leveraging injection molding techniques. Overall, high efficiency leads to quicker turnaround times and increased productivity, making it a preferred method in various industries.
Cost-Effectiveness for Large Volumes
Cost-effectiveness is another compelling reason why businesses opt for plastic injection molding mold processes, especially when producing large volumes of products. The initial investment may be higher due to tooling and machine costs; however, these expenses are quickly offset by the savings accrued during mass production runs. With lower per-unit costs achieved through economies of scale, companies can enjoy significant financial benefits as they ramp up their manufacturing efforts.
Moreover, because injection moldable plastics allow for intricate designs and complex shapes without sacrificing quality or increasing cost significantly, manufacturers can create diverse product lines efficiently. This flexibility means that companies can cater to market demands without incurring exorbitant expenses on design changes or new molds every time a slight adjustment is needed. Thus, businesses find themselves balancing initial investments with long-term savings—a classic win-win scenario.
Precision and Consistency in Manufacturing
Precision and consistency are paramount in today’s competitive market landscape; fortunately, injection molding excels in both areas. The technology behind mould injection moulding ensures that each item produced meets stringent specifications with remarkable accuracy—essential when dealing with components that require exact measurements or tolerances. Whether it's automotive parts or medical devices made from various types of injection moldable plastics, consistency remains key.
The ability to replicate designs flawlessly across thousands or even millions of units means that manufacturers can build trust with their customers regarding product quality and reliability. Furthermore, this level of precision minimizes waste during production since there’s less need for rework or adjustments after items come off the line—a crucial factor in maintaining cost-effectiveness throughout the manufacturing process. In summary, precision and consistency solidify plastic molding's reputation as an industry leader.
Common Applications in Industries
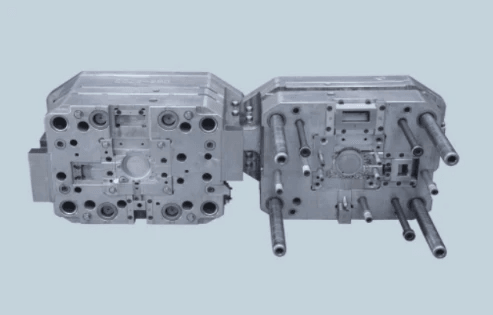
Injection molding is a powerhouse technique widely employed across various industries, thanks to its versatility and efficiency. From automotive components to consumer electronics and medical devices, the advantages of injection moulding make it an attractive choice for manufacturers seeking high-quality production solutions. Let's dive into some of the most common applications where plastic manufacturing truly shines.
Automotive Industry Uses
The automotive industry is one of the largest consumers of injection molded parts, utilizing this method for everything from dashboards to intricate engine components. The precision and consistency offered by plastic injection molding mold ensure that each part meets strict safety and performance standards, which is critical in this sector. Moreover, the ability to produce large volumes at a cost-effective rate makes mold plastic injection an ideal solution for automakers looking to streamline their production processes.
Consumer Goods and Electronics
Consumer goods and electronics also benefit significantly from the advantages of injection moulding. Items such as casings for smartphones, kitchen appliances, and toys are often produced using this method due to its capability to create complex shapes with high detail. With an array of injection moldable plastics available, manufacturers can choose materials that are not only durable but also aesthetically pleasing—perfect for attracting discerning consumers.
Medical Applications of Plastic Molding
In the medical field, plastic molding plays a crucial role in producing devices that require utmost precision and reliability. From surgical instruments to drug delivery systems, the advantages of injection moulding allow for the creation of components that meet stringent regulatory requirements while maintaining high levels of sterility and safety. Furthermore, advancements in technology have enabled manufacturers to develop specialized mold plastic injection techniques tailored specifically for medical applications.
Disadvantages to Consider
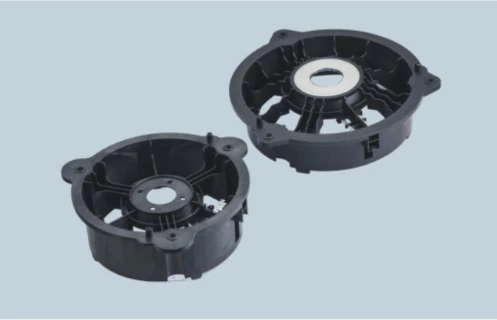
While injection molding offers numerous advantages, it's essential to address the drawbacks that can impact decision-making in plastic manufacturing. Understanding these disadvantages helps businesses and manufacturers weigh their options effectively. Let’s dive into some of the key challenges associated with this popular method of producing moldable plastics.
High Initial Setup Costs
One of the most significant hurdles in adopting injection molding is the high initial setup costs involved. Creating a custom plastic injection molding mold requires a substantial investment in both time and resources, including specialized machinery and skilled labor. This upfront expense can be daunting, especially for small businesses or startups looking to enter the plastic manufacturing market.
Moreover, once you commit to a particular design and mold, it can be challenging to justify these costs if production volumes do not meet expectations. The financial burden may deter companies from exploring the advantages of injection moulding despite its long-term cost-effectiveness for larger production runs. Therefore, careful financial planning and market analysis are crucial before jumping into this process.
Limited Flexibility in Design Changes
Another disadvantage of mold injection moulding is its limited flexibility when it comes to design changes after production has begun. Once a mold is created, altering its design can be both time-consuming and costly, often requiring entirely new molds for even minor adjustments. This rigidity can stifle innovation and adaptability within industries that demand rapid changes or customizations.
Additionally, if market trends shift or consumer preferences evolve, manufacturers may find themselves stuck with outdated designs that no longer resonate with their target audience. This limitation underscores the importance of thorough design planning before committing to plastic injection molding processes, as it can significantly affect future product iterations.
Environmental Concerns in Plastic Production
Environmental concerns are increasingly at the forefront of discussions surrounding plastic manufacturing practices like injection molding. The production of plastic materials contributes significantly to pollution and waste generation, raising eyebrows among environmentally conscious consumers and regulatory bodies alike. As awareness grows about sustainability issues related to plastic use, manufacturers must consider how their practices align with eco-friendly initiatives.
Moreover, while innovations in sustainable practices are emerging within the industry—such as using recycled materials—these solutions often come with their own set of challenges and costs associated with implementing them into existing processes like mold plastic injection systems. Companies must navigate these complexities while striving to maintain profitability without compromising environmental responsibility. Balancing economic viability with ecological impact remains a critical challenge for those involved in plastic injection molding.
Innovations in Injection Molding
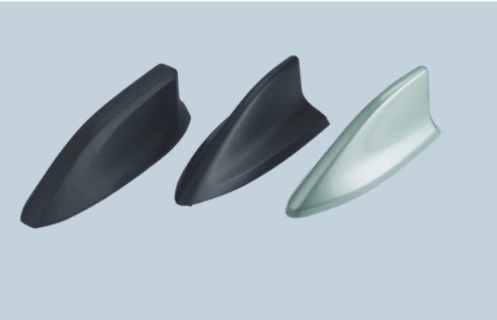
In the ever-evolving landscape of plastic manufacturing, innovations in injection molding are driving efficiency and sustainability. The rise of advanced technologies and software solutions has revolutionized the way mould injection moulding processes are designed and executed. By integrating smart systems, manufacturers can optimize production schedules, reduce waste, and enhance the overall quality of mold plastic injection products.
Advances in Technology and Software
Recent advancements in technology have significantly enhanced the capabilities of injection molding machinery. For instance, computer-aided design (CAD) software now allows for intricate designs that were once impossible to achieve with traditional methods. Additionally, automation and robotics streamline production lines, ensuring that the advantages of injection moulding—such as speed and consistency—are maximized while minimizing human error.
Moreover, simulation software plays a pivotal role in predicting how different materials will behave during the plastic injection molding process. This predictive capability helps manufacturers select suitable injection moldable plastics for specific applications while reducing costly trial-and-error phases. As a result, companies can produce high-quality products more efficiently than ever before.
The Role of Baoyuan in Modern Molding
Baoyuan has emerged as a key player in modern plastic manufacturing by providing innovative solutions tailored to the needs of diverse industries. Their advanced equipment is designed to enhance productivity while maintaining the high standards associated with quality mold plastic injection processes. By focusing on precision engineering and user-friendly interfaces, Baoyuan enables manufacturers to harness the full potential of their mould injection moulding operations.
Furthermore, Baoyuan's commitment to research and development ensures that they remain at the forefront of industry trends and technological advancements. Their state-of-the-art machinery often incorporates features such as energy-efficient designs and real-time monitoring systems that align with sustainable practices in plastic manufacturing. This focus not only improves operational efficiency but also addresses growing environmental concerns related to traditional production methods.
Sustainable Practices in Plastic Manufacturing
Sustainability is becoming an essential aspect of modern manufacturing practices, including those within plastic molding industries. Many companies are now exploring biodegradable materials or recycled plastics as alternatives for traditional injection moldable plastics. These sustainable options not only reduce environmental impact but also appeal to consumers who prioritize eco-friendly products.
Moreover, innovative recycling techniques are being developed within the realm of mould injection moulding to minimize waste generated during production processes. Technologies such as closed-loop systems enable manufacturers to reprocess scrap material back into usable pellets for future runs—essentially giving new life to what would otherwise be discarded waste from plastic manufacturing operations.
In conclusion, embracing these innovations allows businesses not only to benefit from the advantages of injection moulding but also aligns them with global sustainability goals—a win-win scenario for both industry players and our planet.
Conclusion
In summary, injection molding stands out as a pivotal process in modern plastic manufacturing, offering numerous advantages that make it the go-to method for producing high-quality plastic components. The efficiency and precision of mould injection moulding allow manufacturers to produce large volumes of consistent products at a cost-effective rate. With its ability to utilize various injection moldable plastics, this technique has become integral across multiple industries, from automotive to medical applications.
Recap of Injection Molding Advantages
The advantages of injection moulding are manifold and play a crucial role in its widespread adoption. High efficiency in production ensures that manufacturers can meet demand without sacrificing quality or speed, while cost-effectiveness becomes apparent when producing large quantities of parts—making it an attractive option for businesses looking to optimize their operations. Furthermore, the precision and consistency achieved through plastic injection molding mold technology guarantee that each component meets stringent specifications, which is vital for industries where quality cannot be compromised.
The Impact of Disadvantages on Choices
Despite the numerous benefits associated with this manufacturing method, there are also disadvantages that must be carefully considered before diving into production. High initial setup costs can deter smaller businesses from investing in this technology, especially if they do not have guaranteed high-volume orders on the horizon. Additionally, limited flexibility in design changes during production can pose challenges; once a mold is created for a specific part, altering it may require significant time and financial resources—factors that could impact decision-making processes.
Making an Informed Decision on Plastic Molding
When considering whether to engage in plastic molding through injection methods, it's essential to weigh both the advantages and disadvantages thoroughly. Understanding how the benefits align with your production needs versus potential drawbacks will help you make informed choices about your manufacturing strategy. Ultimately, successful implementation of injection molding hinges on evaluating not just immediate gains but also long-term sustainability within your business model.