Introduction
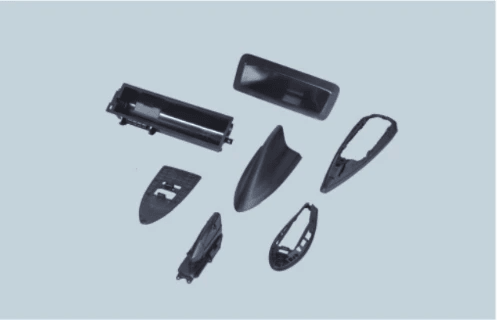
The world of automotive interior manufacturing is a fascinating blend of art and engineering, where aesthetics meet functionality to create spaces that enhance the driving experience. From the dashboard to the seats, every element is meticulously crafted, with automotive interior plastics playing a pivotal role in this intricate design process. As vehicles evolve towards smarter and more sustainable options, understanding the key processes behind plastic manufacturing becomes essential for anyone interested in the future of automotive interiors.
Overview of Automotive Interior Manufacturing
Automotive interior manufacturing encompasses a range of processes aimed at producing components that are not only visually appealing but also durable and comfortable. This sector has seen significant advancements over the years, with innovations leading to lighter materials and improved ergonomics. As consumers demand more from their vehicles, manufacturers are increasingly focused on integrating cutting-edge technologies into their designs while maintaining high standards in automotive interior plastics.
Importance of Plastics in the Industry
Plastics have become indispensable in automotive interiors due to their versatility, lightweight nature, and cost-effectiveness. They allow for complex shapes and finishes that can elevate an interior's look while also contributing to fuel efficiency by reducing overall vehicle weight. The importance of plastics is further underscored by their ability to be molded into various forms through techniques such as Slush Molding, Water-Assisted Injection Molding, and Low-Pressure Injection Molding—each offering unique advantages tailored to specific applications.
Key Processes to Know
To fully appreciate how automotive interior plastics are crafted, it's crucial to understand several key manufacturing processes that define the industry today. Slush Molding stands out for its ability to create soft-touch surfaces ideal for car interiors, while Water-Assisted Injection Molding offers enhanced design flexibility without compromising structural integrity. Low-Pressure Injection Molding rounds out this trio by providing efficient production methods that minimize waste—each technique plays a vital role in shaping modern automotive interiors.
Slush Molding in Interior Design
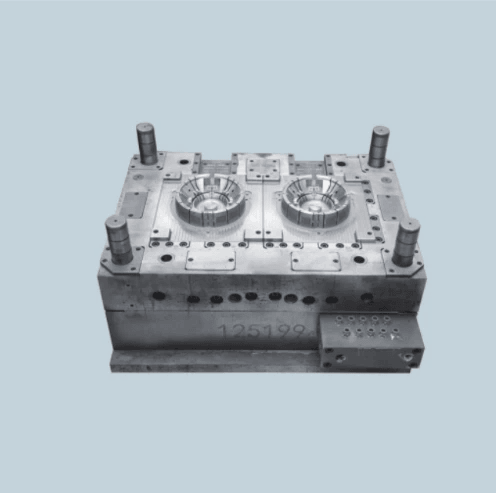
Slush molding is a fascinating process that plays a pivotal role in the realm of automotive interior plastics. This technique involves pouring a liquid polymer into a mold, allowing it to coat the interior surfaces before being rotated to create hollow parts. The result? Lightweight, durable components that are not only functional but also aesthetically pleasing, enhancing the overall design of modern vehicles.
Benefits of Slush Molding
The benefits of slush molding are numerous and impactful for automotive interior plastics. First off, this method allows for intricate designs and textures that can elevate the visual appeal of any vehicle's cabin. Additionally, slush molding produces lightweight components, which contribute to improved fuel efficiency—a win-win for manufacturers and eco-conscious consumers alike.
Another advantage is the ability to use various materials, including foams and elastomers, providing flexibility in design and functionality. This versatility means manufacturers can create soft-touch surfaces or hard-shell components as needed. Plus, slush molding offers excellent color retention and surface finish options, ensuring that automotive interiors remain vibrant and attractive over time.
Applications in Automotive Interiors
When it comes to applications in automotive interiors, slush molding shines brightly across several components. Dashboard skins are one prominent example; they benefit from the process's ability to produce soft-touch finishes while maintaining structural integrity. Moreover, door panels crafted through slush molding provide both comfort and style—essential elements for any modern vehicle.
Beyond dashboards and door panels, slush molding is also utilized for center consoles and armrests where user interaction is frequent. These components require durability along with an appealing look—qualities that slush molded parts effortlessly deliver. The flexibility inherent in slush molding allows manufacturers to experiment with textures and colors that align perfectly with evolving consumer preferences.
Leading Companies Using Slush Molding
Several leading companies have embraced slush molding as a cornerstone technique in producing high-quality automotive interior plastics. For instance, Johnson Controls has made significant strides by integrating this method into their production lines—resulting in innovative designs that captivate consumers' attention while meeting stringent safety standards. Another key player is Grupo Antolin; they focus on creating sophisticated interior solutions through advanced manufacturing techniques like slush molding.
Furthermore, Faurecia has also recognized the potential of this process by leveraging it to enhance their product offerings within the automotive sector significantly. Their commitment to sustainability aligns well with the lightweight nature of slush molded products—demonstrating how innovation can meet environmental goals effectively. As these companies continue pushing boundaries through advanced manufacturing processes like water-assisted injection molding or low-pressure injection molding alongside traditional methods like slush molding, we can expect even more exciting developments on the horizon.
Water-Assisted Injection Molding Techniques
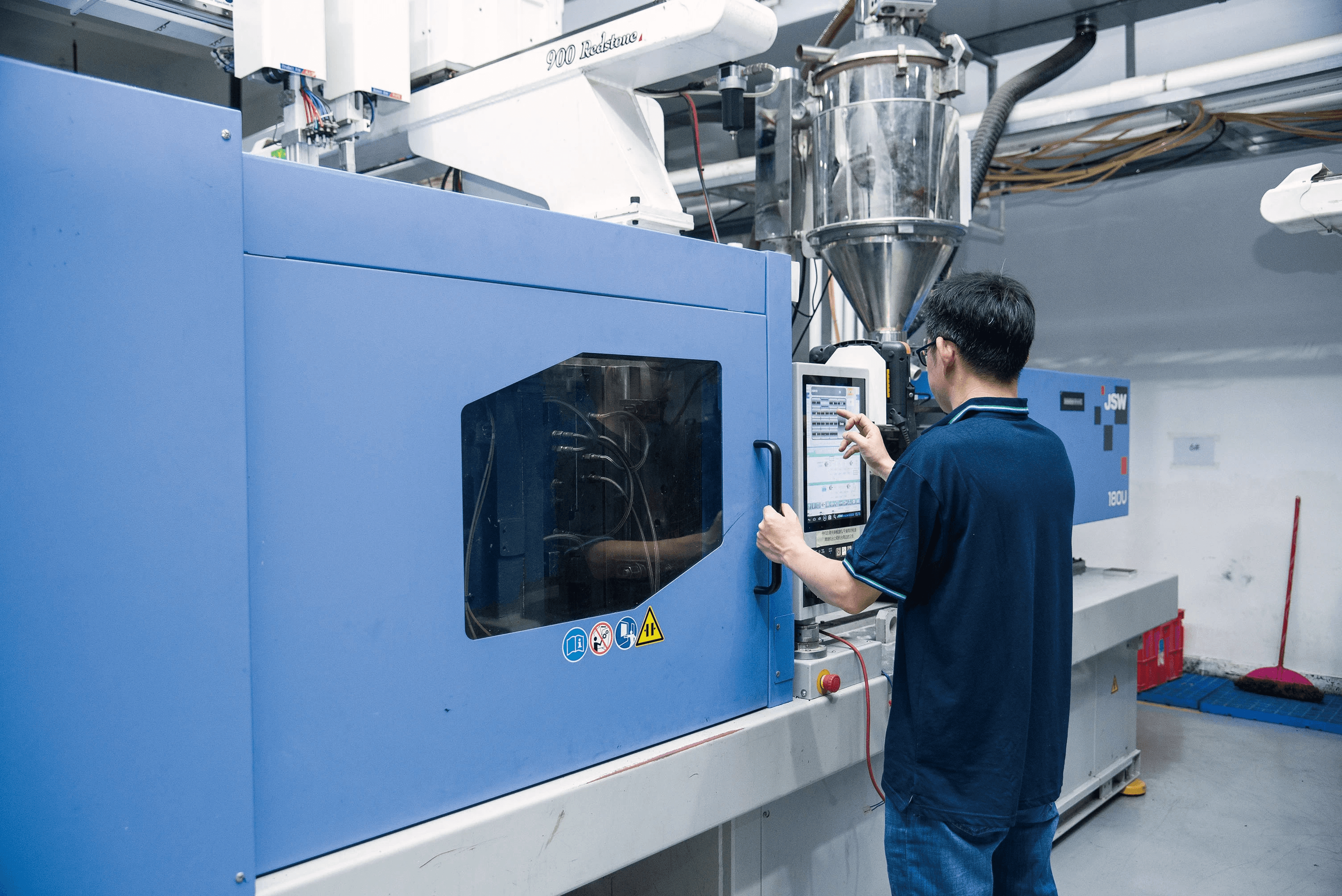
Water-assisted injection molding is revolutionizing the world of automotive interior plastics, offering innovative solutions that enhance both production efficiency and product quality. This technique leverages water as a cooling agent during the molding process, allowing for more intricate designs and lighter components. As manufacturers strive to meet the growing demand for high-performance automotive interiors, water-assisted injection molding stands out as a game-changer.
How Water-Assisted Molding Works
Water-assisted injection molding operates on a straightforward yet effective principle: it uses water to create hollow sections within molded parts. During the injection phase, plastic is injected into a mold, while water is simultaneously introduced into the cavity to displace some of the molten plastic. This method not only facilitates complex shapes but also reduces cycle times significantly compared to traditional methods like slush molding or low-pressure injection molding, making it an attractive option for producing automotive interior plastics.
The process begins with injecting molten thermoplastic into a mold cavity where water is strategically introduced under pressure. As the plastic cools and solidifies around the water-filled core, it creates lightweight components with enhanced structural integrity. This dual approach allows manufacturers to produce intricate designs without compromising on strength or durability—a critical factor in automotive interiors.
Advantages for Automotive Interior Plastics
One of the standout advantages of water-assisted injection molding in automotive interior plastics is its ability to reduce weight without sacrificing performance. Lighter components contribute directly to improved fuel efficiency and overall vehicle performance, aligning perfectly with industry trends towards sustainability and eco-friendliness. Additionally, this technique allows for more complex geometries that can enhance aesthetics and functionality in vehicle interiors.
Another significant benefit is reduced cycle time—water-assisted techniques can cut production times by up to 30%. This efficiency not only boosts productivity but also lowers manufacturing costs, providing companies with a competitive edge in an ever-evolving market landscape dominated by innovation like slush molding and low-pressure injection molding techniques. Furthermore, the superior surface finish achieved through this method minimizes post-processing requirements, leading to even greater cost savings.
Lastly, water-assisted injection molding supports greater design flexibility compared to traditional methods used in producing automotive interior plastics. Designers can explore new shapes and forms that were previously unattainable due to limitations in material properties or production capabilities—opening up exciting possibilities for creativity and customization within vehicle interiors.
Companies Excelling in Water-Assisted Molding
Several forward-thinking companies are leading the charge in adopting water-assisted injection molding technologies for their automotive interior plastics needs. Industry giants such as BASF and Continental have integrated these advanced techniques into their manufacturing processes, reaping benefits from enhanced design capabilities and improved product performance. Their commitment not only highlights the effectiveness of this technology but also sets industry standards that others aspire to achieve.
Another notable player is Johnson Controls which has embraced this innovative approach to streamline their production lines while maintaining high-quality standards across various automotive interior components—from dashboards to door panels. By leveraging water-assisted techniques alongside established methods like slush molding or low-pressure injection molding, they have successfully optimized their operations while delivering products that meet consumer expectations for quality and durability.
In addition, smaller specialized firms are emerging as pioneers by focusing exclusively on niche markets within automotive interior plastics using water-assisted technologies. These companies often provide tailored solutions that cater specifically to unique client needs—demonstrating how versatile this method can be across different segments of the industry while pushing boundaries traditionally set by older manufacturing processes.
Low-Pressure Injection Molding Innovations
Low-pressure injection molding is revolutionizing the way automotive interior plastics are produced, offering a unique blend of efficiency and quality. This innovative process utilizes lower pressures compared to traditional methods, which helps in reducing stress on materials while ensuring superior surface finishes. As a result, manufacturers can create intricate designs that enhance both aesthetics and functionality in vehicle interiors.
Understanding Low-Pressure Molding
Low-pressure injection molding operates by injecting molten plastic into a mold at significantly reduced pressure levels, typically below 15 bar. This method allows for better control over the flow of plastic, minimizing defects such as warping or sink marks that can occur with higher pressure techniques. By utilizing specialized equipment and tailored mold designs, low-pressure molding opens up new possibilities for creating complex automotive interior plastics that meet rigorous industry standards.
Advantages for Interior Component Production
The advantages of low-pressure injection molding extend well beyond just reducing defects; it also enhances production efficiency and material usage. With lower energy consumption during the manufacturing process, companies can enjoy cost savings while being more environmentally friendly—an essential consideration in today’s automotive industry. Additionally, this technique allows for faster cycle times and improved flexibility in design changes, making it an ideal choice for producing a variety of automotive interior plastics.
Recognized Brands Using Low-Pressure Molding
Several leading brands have embraced low-pressure injection molding to elevate their production capabilities in the realm of automotive interior plastics. Companies like Faurecia and Lear Corporation have integrated this technology into their manufacturing processes to create high-quality components such as dashboards and door panels. By leveraging low-pressure techniques alongside other methods like slush molding and water-assisted injection molding, these brands are setting new benchmarks in the industry.
Conclusion
The automotive interior plastics industry is on the brink of exciting transformations, driven by innovation and sustainability. As manufacturers look to enhance vehicle aesthetics and functionality, processes like Slush Molding, Water-Assisted Injection Molding, and Low-Pressure Injection Molding are becoming increasingly vital. These methods not only improve production efficiency but also contribute to the overall quality of automotive interiors.
Future of Automotive Interior Plastics
Looking ahead, the future of automotive interior plastics appears bright with a strong emphasis on eco-friendly materials and advanced manufacturing techniques. Innovations in Slush Molding will allow for even greater design flexibility while reducing waste during production. Additionally, Water-Assisted Injection Molding is set to revolutionize how we think about material usage in automotive interiors, offering lighter components without sacrificing strength or durability.
The Role of Baoyuan in Innovation
Baoyuan has emerged as a key player in driving innovation within the realm of automotive interior plastics. By investing in cutting-edge technologies related to Slush Molding and Low-Pressure Injection Molding, Baoyuan continues to push boundaries and redefine industry standards. Their commitment to research and development ensures that they remain at the forefront of advancements that shape the future landscape of automotive interiors.
Final Thoughts on Manufacturing Processes
In conclusion, understanding manufacturing processes such as Slush Molding, Water-Assisted Injection Molding, and Low-Pressure Injection Molding is essential for anyone involved in the automotive sector today. These techniques not only enhance product performance but also align with growing consumer demands for sustainability and quality in vehicle interiors. As we move forward into this new era for automotive interior plastics, collaboration between manufacturers like Baoyuan will be crucial for driving further innovations that meet evolving market needs.