Introduction
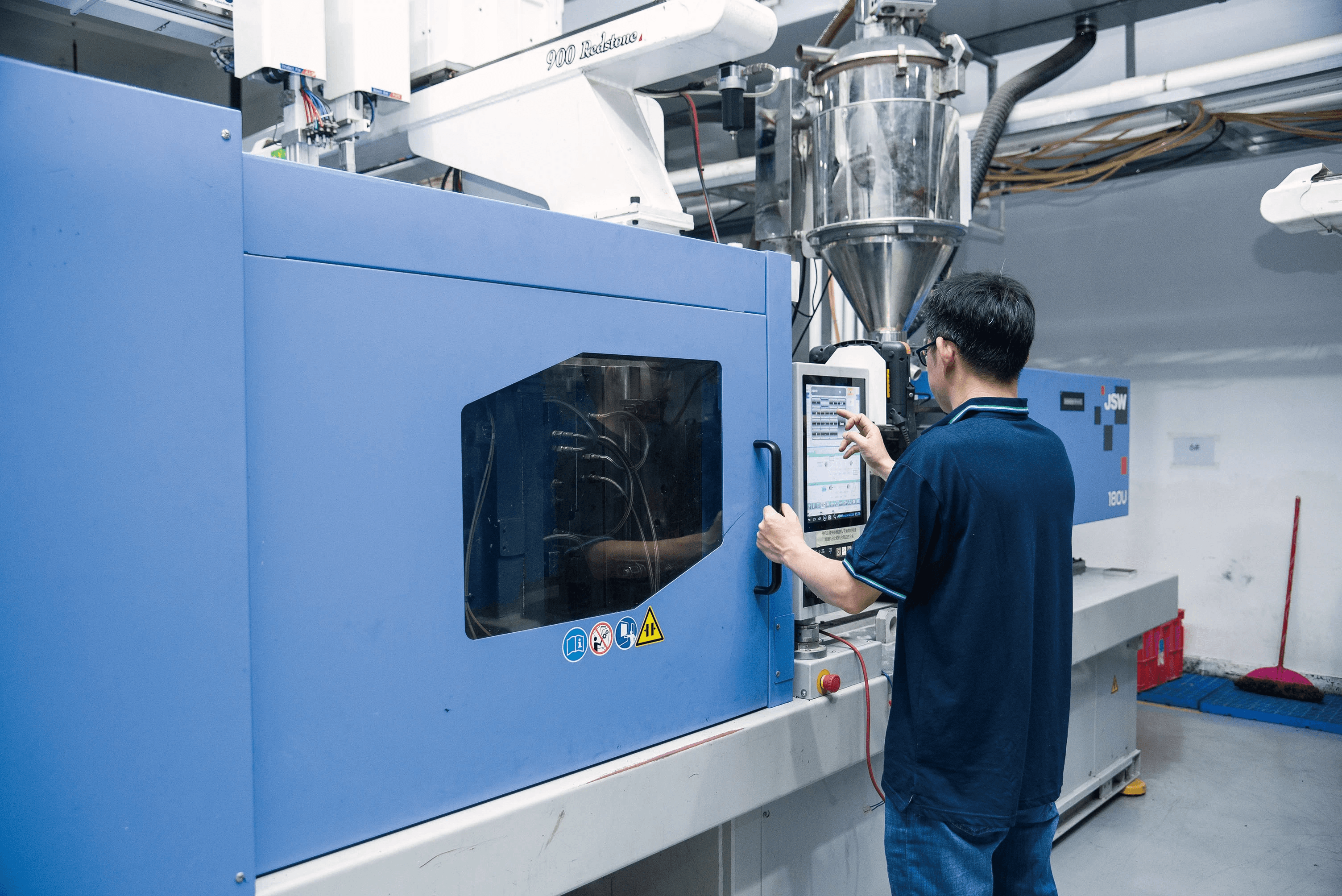
Injection molding is a cornerstone of modern manufacturing, allowing for the efficient production of complex plastic parts. However, within this seemingly seamless process lurks a host of injection molding defects that can compromise quality and efficiency. Understanding these defects is essential for anyone involved in plastic injection molding services, as they can significantly impact both production timelines and product integrity.
Understanding Injection Molding Defects
Injection molding defects come in various forms, each with its unique causes and implications. From air traps to sink marks, these issues can arise from improper mold design or inadequate processing conditions. By recognizing the different types of mold plastic injection defects early on, manufacturers can take proactive measures to mitigate their effects.
The Impact of Defects on Production
The presence of injection molding defects can lead to increased waste, reduced productivity, and ultimately higher costs for manufacturers. When defective parts are produced, it not only affects the immediate production run but also damages customer trust and brand reputation over time. Therefore, addressing these issues promptly is vital for maintaining a competitive edge in the market.
Why Quality Control Matters
Quality control serves as the first line of defense against injection molding defects in any production environment. Implementing rigorous quality assurance practices ensures that potential issues are identified before they escalate into costly problems down the line. In an industry where precision is key—especially when working with injection moldable plastics—maintaining high standards through effective quality control cannot be overstated.
Air Traps
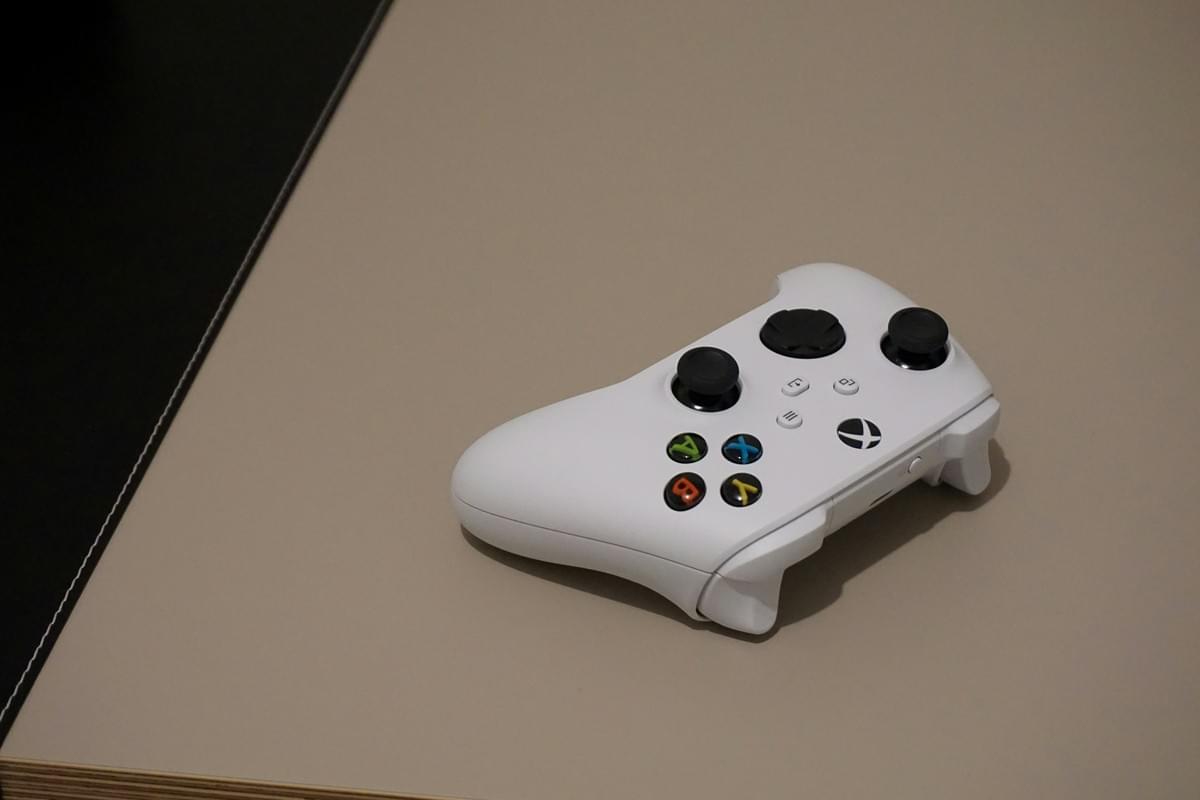
Air traps are a common issue in the world of injection molding defects, where pockets of air become trapped in the molded part during the injection process. This can lead to weak spots, unsightly blemishes, and compromised structural integrity in molded products. Understanding how these air traps form is essential for anyone involved in plastic injection molding services.
Causes of Air Traps in Molding
Air traps usually occur due to insufficient venting within the mold cavity, which prevents air from escaping as molten plastic flows into it. Additionally, incorrect material flow rates or temperatures can exacerbate this issue, leading to incomplete filling and trapping air pockets. Other contributing factors may include improper mold design or inadequate clamping pressure during the injection process.
Solutions to Prevent Air Traps
To prevent air traps, manufacturers must ensure that their mold designs incorporate adequate venting features that allow trapped air to escape efficiently. Adjusting material flow rates and temperatures can also help ensure a smooth filling process, minimizing the risk of trapping air bubbles. Regular maintenance and inspection of molds are crucial for identifying potential issues before they escalate into significant injection molding defects.
Importance of Venting in Mold Design
Venting is not just an afterthought; it's a critical aspect of effective mold design that directly impacts product quality in plastic injection molding. Properly designed vents facilitate the escape of air and other gases during the injection process, ensuring a complete fill without interruptions caused by trapped air pockets. Investing time and resources into effective venting strategies can significantly reduce defects like air traps while enhancing overall production efficiency.
Short Shots
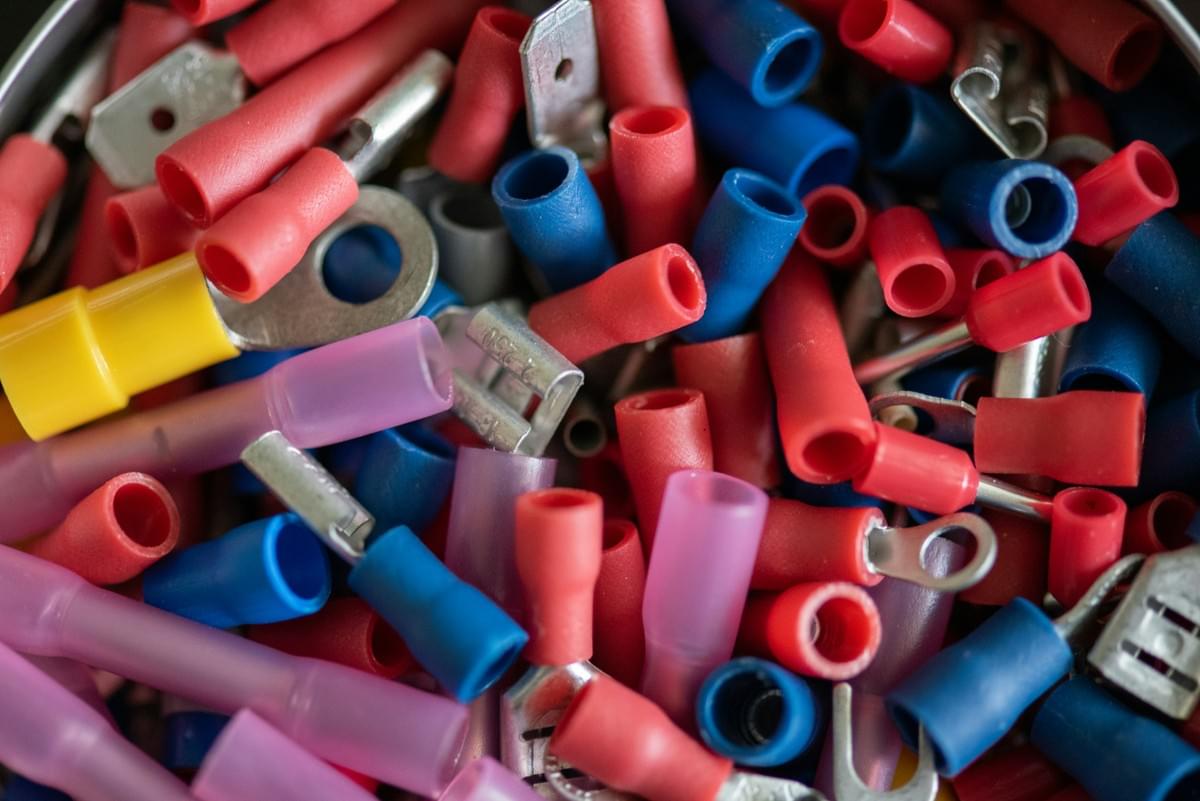
Short shots are a common issue in the world of injection molding, where incomplete filling of the mold results in defective parts. This defect not only compromises the integrity of the final product but can also lead to increased production costs and waste. Understanding what causes short shots is crucial for anyone involved in plastic injection molding services.
What Causes Short Shots?
Several factors contribute to short shots in injection molding. One primary cause is insufficient material being injected into the mold, which can occur due to low injection pressure or inadequate material feed. Additionally, issues with the design of the mold plastic injection system, such as poorly placed gates or vents, can hinder proper filling and lead to these pesky short shots.
Another factor could be related to the properties of injection moldable plastics themselves; if a material has high viscosity or poor flow characteristics, it may not fill the mold effectively. Temperature fluctuations during processing can also play a role by affecting how well materials flow and fill molds. Recognizing these causes is essential for manufacturers aiming to improve their production quality and minimize defects.
Techniques to Avoid Short Shots
Preventing short shots involves several strategic techniques that ensure smooth operation throughout the injection molding process. First and foremost, optimizing machine settings—such as increasing injection pressure or adjusting speed—can greatly enhance material flow into molds. Regular maintenance checks on equipment can also help identify any mechanical issues that might be contributing to incomplete fills.
Another effective technique includes reevaluating mold design; ensuring that gates are appropriately sized and strategically placed enhances material distribution throughout the cavity during filling. Utilizing high-quality plastic injection molding materials that have better flow characteristics will also reduce instances of short shots significantly. By combining these approaches, manufacturers can streamline their processes and produce higher quality products with fewer defects.
The Role of Material Flow in Injection Molding
Material flow plays a pivotal role in successful plastic molding processes, directly impacting both efficiency and product quality. Effective control over how materials move within molds ensures complete filling without leaving behind air pockets or unfilled areas—key contributors to injection molding defects like short shots. Properly designed runners and gates facilitate optimal flow paths for injected plastics, enhancing overall performance.
Moreover, understanding rheology—the study of how materials deform under stress—will help engineers select appropriate injection moldable plastics for specific applications based on their flow properties at various temperatures and pressures. This knowledge allows for better predictions regarding potential issues like short shots before they even occur during production runs. Ultimately, mastering material flow dynamics is essential for achieving consistent results in plastic injection molding while minimizing defects across all phases of manufacturing.
Sink Marks
Sink marks are a common concern in the world of injection molding, and they can significantly impact the aesthetic and functional qualities of a product. These defects occur when there are inconsistencies in the thickness of the molded part, leading to uneven cooling and shrinkage. Understanding how sink marks form is crucial for anyone involved in plastic injection molding services, as it helps manufacturers produce higher-quality mold plastic injection products.
Understanding Sink Marks in Products
Sink marks manifest as depressions or dimples on the surface of molded parts, often compromising their visual appeal. They typically arise when thicker sections of a part cool more slowly than thinner areas, resulting in uneven contraction during solidification. In plastic injection molding, recognizing the factors that contribute to sink marks—such as material selection and wall thickness—is essential for creating defect-free products.
How to Minimize Sink Marks
Minimizing sink marks requires a multi-faceted approach that includes optimizing design and process parameters during injection molding. One effective technique is to maintain uniform wall thickness throughout the product; this ensures even cooling and reduces the likelihood of sink marks forming. Additionally, using advanced plastic injection molding techniques like gas-assist or structural foam can help distribute material more evenly, further mitigating this common defect.
The Importance of Proper Cooling
Proper cooling plays a pivotal role in preventing sink marks from appearing on molded parts. Effective temperature control throughout the cooling phase allows for consistent shrinkage across all areas of a product, minimizing distortions caused by uneven temperatures. By investing time into designing an efficient cooling system within your plastic injection molding mold, you can significantly enhance product quality while reducing defects like sink marks.
Warping
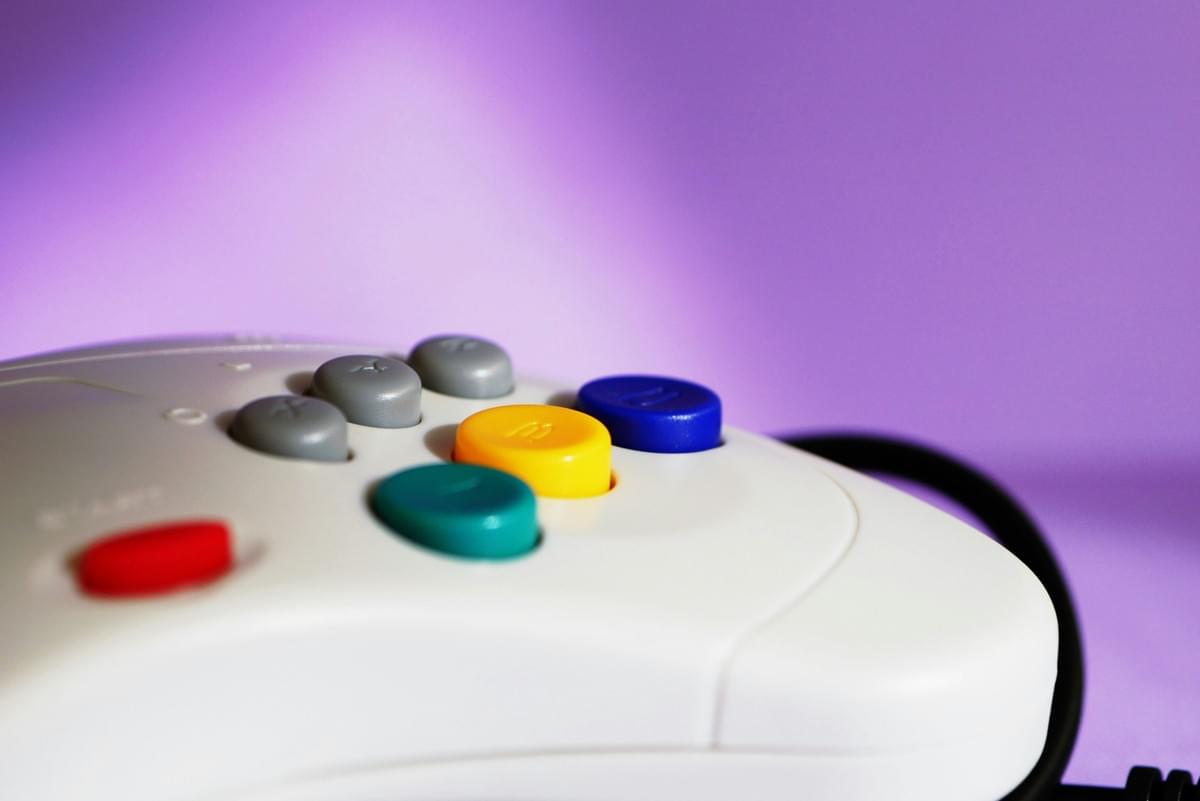
Warping is one of the more troublesome injection molding defects that can arise during the production process, causing significant issues in product quality and functionality. It refers to the deformation of a molded part, which can lead to misalignment and fit problems when components are assembled. Understanding the causes and prevention strategies for warping is crucial for manufacturers utilizing plastic injection molding services.
Factors Leading to Warping in Molds
Several factors contribute to warping in molds, primarily related to material properties and processing conditions. One major culprit is uneven cooling rates during the solidification of moldable plastics, which can create internal stresses that distort the final shape. Additionally, variations in wall thickness can exacerbate these stresses; thinner areas cool faster than thicker ones, leading to differential shrinkage that results in warped parts.
Prevention Strategies for Warping
To effectively minimize warping, manufacturers should prioritize uniform wall thicknesses when designing their mold plastic injection components. This design consideration allows for even cooling and reduces internal stress accumulation within the plastic injection molding mold. Moreover, optimizing cooling channel design helps ensure consistent temperature distribution throughout the mold, further mitigating potential warping issues.
The Role of Temperature Control
Temperature control plays a pivotal role in preventing warping during plastic molding processes. Maintaining a consistent temperature throughout both the melt phase and cooling phase ensures that materials behave predictably as they transition from liquid to solid states. By utilizing advanced temperature monitoring systems and adjusting parameters accordingly, manufacturers can significantly reduce instances of injection molding defects like warping while enhancing overall product quality.
Flashing
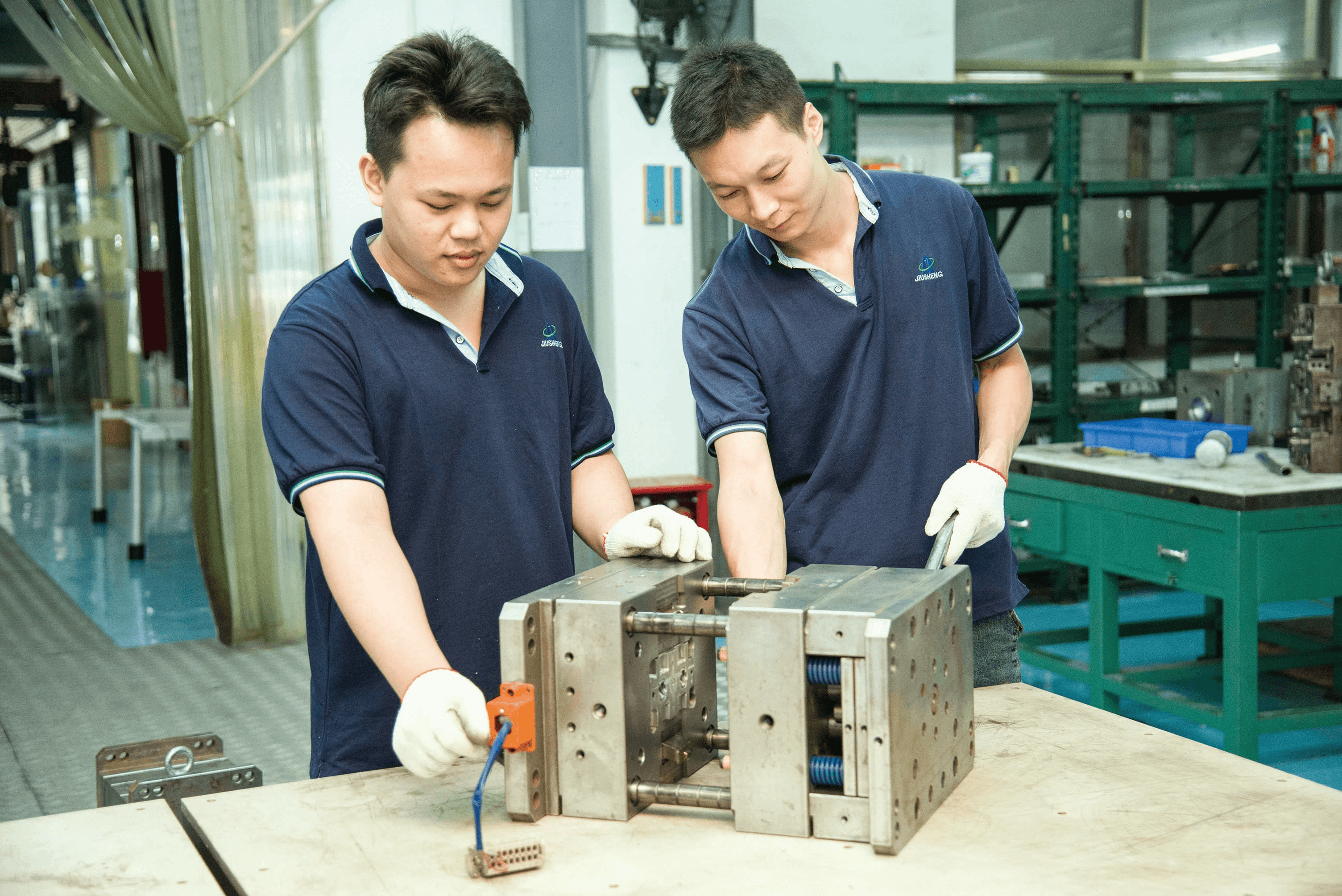
Flashing is a common issue in injection molding that occurs when excess plastic escapes from the mold cavity during the injection process. This defect manifests as thin, unwanted projections along the edges of molded parts, which can compromise both aesthetics and functionality. Understanding flashing is crucial for manufacturers utilizing plastic injection molding services, as it directly impacts production efficiency and product quality.
What is Flashing in Injection Molding?
In simple terms, flashing refers to the overflow of molten plastic that seeps out from between the mold halves during the injection process. This often happens when there’s excessive pressure or poor sealing between mold components, leading to a messy finish on what should be a sleek product. For those involved in mold plastic injection operations, recognizing this defect early can save time and resources by preventing further complications down the line.
How to Prevent Flashing During Production
Preventing flashing requires a multifaceted approach involving careful attention to several critical factors in the production process. First and foremost, ensuring proper clamping force can significantly reduce the chances of excess material escaping from the mold. Additionally, optimizing temperature settings for both material and mold can help maintain consistent flow rates while reducing pressure fluctuations that contribute to flashing.
Another effective strategy involves refining your choice of injection speed; slower speeds can sometimes minimize turbulence within the melt stream, thereby reducing flash occurrences. Regular maintenance of molds also plays a vital role—ensuring that they are clean and free from wear helps maintain their integrity during each cycle of plastic molding. By implementing these practices, manufacturers can enhance their overall quality control measures against common injection molding defects like flashing.
Quality Checks to Avoid Flashing
Quality checks are essential for catching potential issues before they escalate into significant problems during production runs involving plastic injection molding molds. Regular inspections should include visual assessments for any signs of flashing on completed parts; this proactive approach allows teams to address issues swiftly before they affect larger batches of products.
Moreover, utilizing precision measurement tools can help verify that molded parts meet specified tolerances—any deviations could indicate underlying issues with clamping or pressure settings that lead to flash formation. Finally, conducting routine audits on machinery involved in manufacturing processes ensures optimal performance levels are maintained over time; this diligence minimizes risks associated with various injection molding defects including flashing.
Color Mismatches
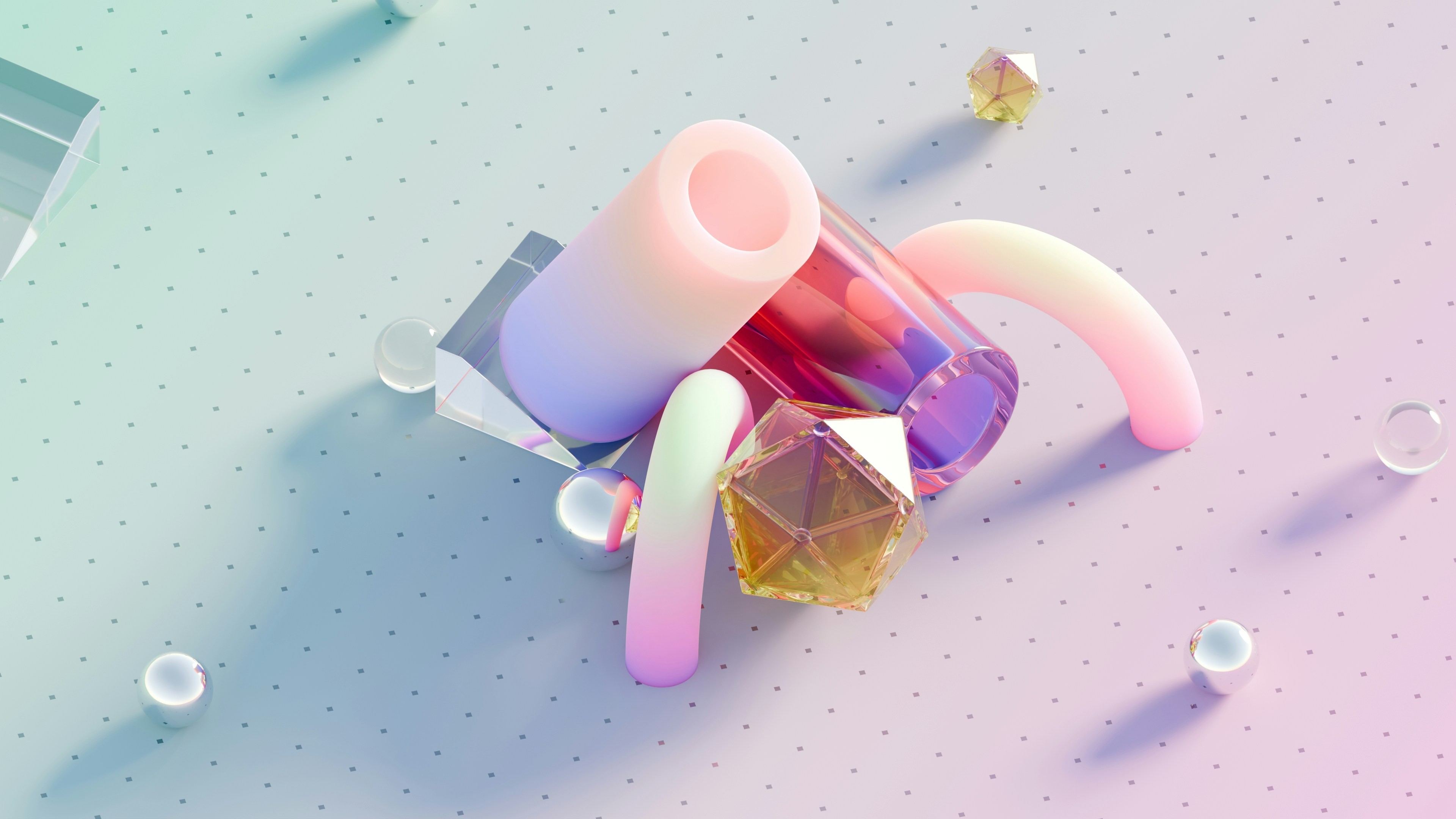
Color mismatches in plastic injection molding can be a real headache, impacting both aesthetics and customer satisfaction. These discrepancies often arise from variations in raw materials, inconsistent mixing processes, or even equipment calibration issues. Understanding the root causes of these mismatches is crucial for anyone involved in injection molding services aiming for high-quality results.
Causes of Color Mismatch in Plastics
One primary cause of color mismatch in plastics is the inconsistency in the raw materials used during production. Variations in pigment concentration, moisture content, or even batch differences can lead to noticeable discrepancies in color across different production runs. Additionally, improper calibration of color mixing equipment or inadequate blending techniques can exacerbate these issues, resulting in injection molding defects that are hard to ignore.
Best Practices for Consistent Coloring
To achieve consistent coloring in plastic injection molding, several best practices should be implemented throughout the production process. First and foremost, it’s essential to establish a standardized procedure for measuring and mixing colors accurately before injecting them into molds. Regularly calibrating equipment and conducting thorough quality checks can also help maintain uniformity across batches—ensuring that your mold plastic injection produces identical shades every time.
The Importance of Material Selection
Material selection plays a pivotal role when it comes to minimizing color mismatches during the injection molding process. Opting for high-quality injection moldable plastics with well-defined specifications can significantly reduce variability and enhance color consistency throughout production runs. By choosing reliable suppliers who prioritize quality control measures, manufacturers can mitigate potential issues related to color mismatching and ultimately improve their product’s marketability.
Surface Defects
Surface defects in injection molding can be the bane of a manufacturer's existence. These imperfections not only detract from the visual appeal of a product but can also compromise its overall functionality. Understanding common surface defects is crucial for anyone involved in plastic injection molding services, as it directly impacts production quality and customer satisfaction.
Common Surface Defects in Molding
When discussing injection molding defects, several surface issues frequently arise, including scratches, blemishes, and uneven textures. Scratches often occur during handling or due to improper mold maintenance, while blemishes may result from contamination or moisture trapped in the mold plastic injection process. Uneven textures can stem from variations in cooling rates or inconsistent material flow during the injection molding process.
Techniques to Reduce Surface Defects
To combat these pesky surface defects, manufacturers can implement various techniques aimed at refining their plastic molding processes. Regular maintenance of molds is essential; keeping them clean and free from contaminants will significantly reduce the likelihood of scratches and blemishes. Additionally, optimizing cooling rates and ensuring uniform material flow during the injection process are critical steps for achieving a smooth finish on molded parts.
How Surface Quality Affects Product Performance
The surface quality of molded products plays an integral role in their overall performance and durability. Poorly finished surfaces can lead to increased friction or wear during use, which might ultimately shorten a product's lifespan—something no manufacturer wants to deal with! Moreover, aesthetic appeal is paramount; customers are drawn to products that look polished and professional, making attention to detail in surface quality an undeniable asset for any company involved in plastic injection molding.
Conclusion
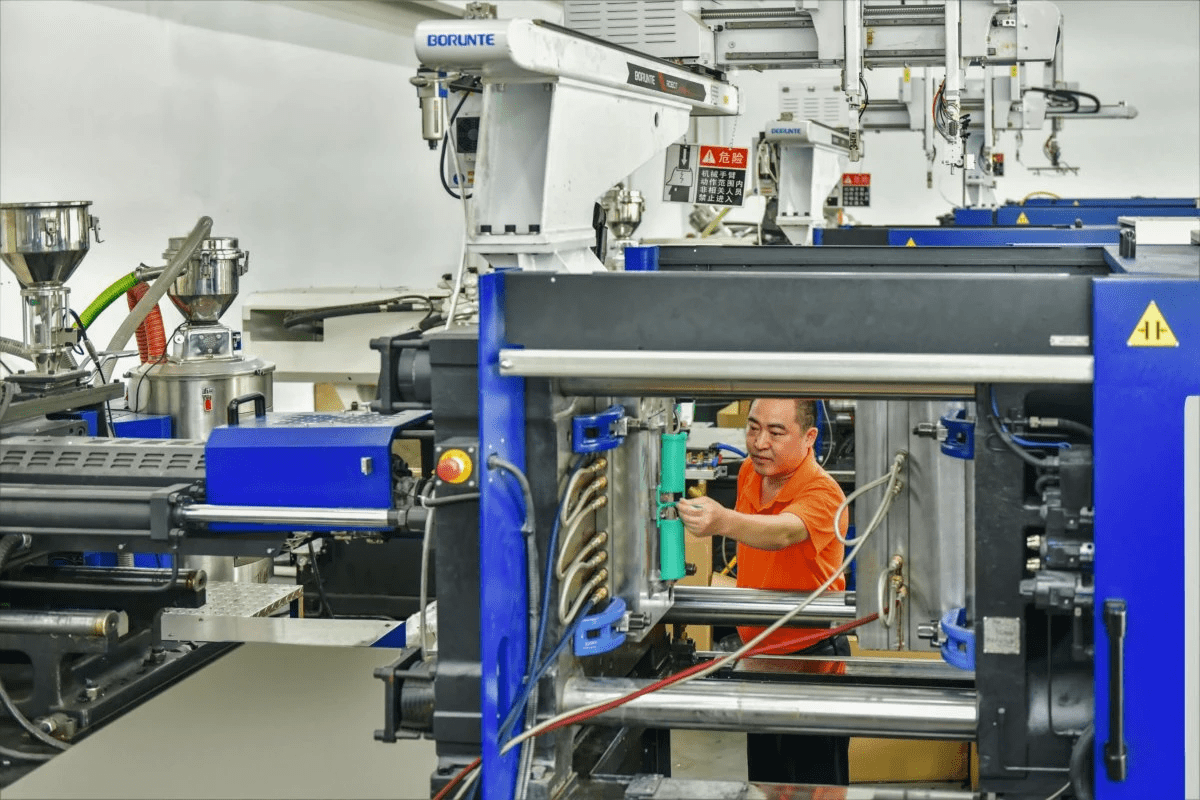
In the world of injection molding, understanding defects is crucial for maintaining quality and efficiency. Throughout this guide, we've explored various injection molding defects, their causes, and effective solutions to prevent them. By implementing these strategies, manufacturers can enhance their production processes and ensure high-quality plastic products.
Key Takeaways on Injection Molding Defects
Injection molding defects can significantly impact product quality and production timelines. From air traps to color mismatches, each defect has its own set of causes and solutions that must be understood for effective management. By recognizing these issues early on, companies can save time and resources while improving the overall quality of their plastic injection molding services.
The Role of Quality Assurance in Molding
Quality assurance plays a pivotal role in the injection molding process by ensuring that every step meets established standards. Regular checks during production help identify potential defects before they escalate into larger issues, safeguarding both product integrity and customer satisfaction. Investing in robust quality assurance practices not only minimizes injection molding defects but also enhances the reputation of manufacturers in the competitive landscape.
How Baoyuan Can Help You Avoid Defects
At Baoyuan, we specialize in delivering top-notch plastic injection molding solutions designed to minimize defects at every stage of production. Our expertise in mold plastic injection allows us to implement best practices tailored to your specific needs, ensuring consistent results with every batch. With our comprehensive approach to quality control and commitment to excellence, you can trust Baoyuan as your partner in achieving defect-free products.