Introduction
Injection molding is a fascinating process that has revolutionized plastic manufacturing, allowing for the mass production of intricate shapes and designs with remarkable efficiency. Understanding how to make an injection mold is crucial for anyone looking to dive into the world of mold plastic injection. This introduction will guide you through the essential concepts of injection molding, emphasizing the importance of precision in molds and providing a comprehensive overview of the entire process.
Understanding Injection Molding Basics
At its core, injection molding involves injecting molten plastic into a mold cavity, where it cools and solidifies into the desired shape. This method is widely used in various industries due to its ability to produce high-quality parts quickly and cost-effectively. Familiarity with different types of injection moldable plastics and their properties can significantly impact your success in creating effective molds.
The Importance of Precision in Molds
Precision is paramount in mold design because even minor deviations can lead to defects in the final product. A well-crafted injection machine mold ensures that every piece produced meets exact specifications, enhancing both functionality and aesthetic appeal. Investing time and resources into precise mold creation not only improves product quality but also reduces waste during production.
Overview of the Injection Molding Process
The injection molding process begins with designing a detailed mold using CAD software, followed by selecting appropriate materials for the job. Once you've designed your mold, it's essential to create it accurately through careful fabrication techniques while adhering to stringent quality control measures. Finally, after setting up your machine correctly, you'll engage in low volume plastic molding or mass production—each step critical for achieving successful outcomes.
Designing the Injection Mold
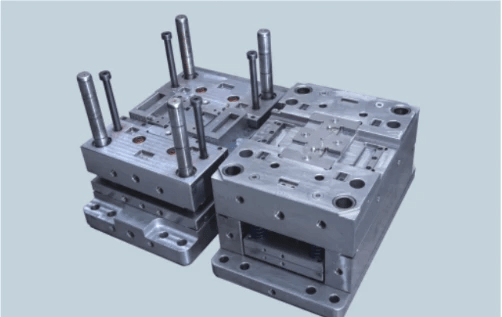
Designing an injection mold is a crucial step in the plastic manufacturing process, setting the stage for high-quality production. A well-designed mold ensures that the final products meet specifications while optimizing efficiency and reducing waste. The following sections delve into essential aspects of mold design, including CAD software, material selection, and prototyping.
CAD Software for Mold Design
When it comes to how to make an injection mold, Computer-Aided Design (CAD) software is your best friend. These powerful tools allow designers to create detailed 3D models of molds, enabling precise visualization before any physical work begins. Popular CAD programs like SolidWorks and AutoCAD provide features tailored specifically for injection molding, ensuring that every aspect from cooling channels to gate placement is meticulously planned.
Using CAD software not only streamlines the design process but also facilitates collaboration among team members. Designers can easily share files and make adjustments in real-time, which is invaluable when working on complex projects with tight deadlines. Ultimately, effective use of CAD can lead to better designs and fewer revisions during the actual production phase.
Selecting the Right Injection Moldable Plastics
Choosing the right injection moldable plastics is paramount for achieving desired characteristics in finished products. Factors such as mechanical strength, temperature resistance, and cost all play significant roles in this decision-making process. Common options include ABS for its toughness or polycarbonate for its clarity and heat resistance; each material has unique properties that suit different applications.
Understanding how different plastics behave during injection molding can help you avoid costly mistakes later on. For instance, some materials may require specific temperature settings or pressure adjustments during processing—critical details that can affect cycle times and overall quality. By selecting appropriate materials upfront, manufacturers can enhance their low volume plastic molding capabilities while ensuring product durability.
Importance of Prototyping
Prototyping serves as a vital step in designing an injection mold that meets production requirements effectively. Creating a prototype allows designers to test their concepts without committing significant resources to full-scale production—think of it as a dress rehearsal before opening night! This stage provides valuable insights into how well the design translates from digital model to physical object.
Additionally, prototypes help identify potential issues early on in the process; whether it's an alignment problem or inadequate cooling channels, catching these hiccups now saves time and money later on during mass production phases like plastic injection molding. Moreover, feedback from stakeholders regarding prototype performance can inform necessary modifications before finalizing designs for manufacturing.
Creating the Mold
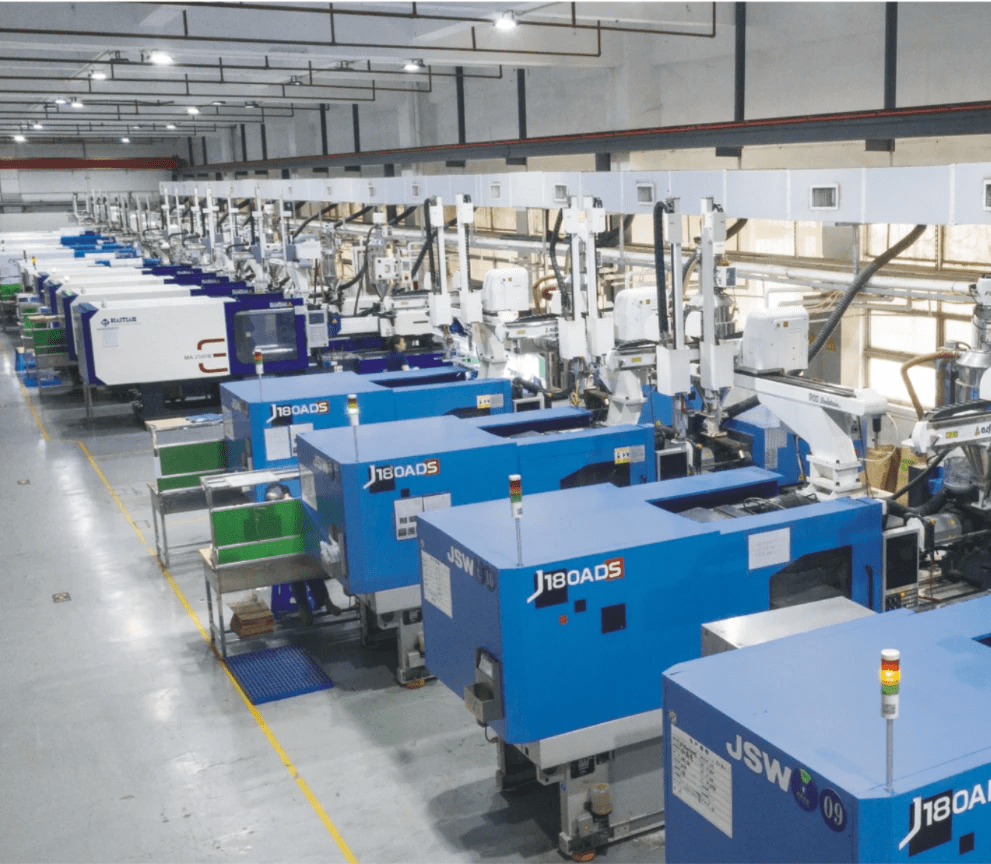
Creating an injection mold is a critical step in the injection molding process, where precision and quality are paramount. This section will guide you through the essential aspects of choosing an appropriate injection machine mold, detailing the step-by-step fabrication process, and emphasizing quality control measures that ensure your molds meet industry standards. Understanding how to make an injection mold effectively can significantly enhance your plastic manufacturing capabilities.
Choosing an Injection Machine Mold
Selecting the right injection machine mold is crucial for successful plastic injection molding. The choice depends on various factors, including the complexity of the part design, production volume, and material compatibility with different injection moldable plastics. For low volume plastic molding projects, a well-chosen mold can save time and reduce costs while still delivering high-quality results.
When determining how to make an injection mold that meets your needs, consider both standard and custom molds based on your production requirements. Custom molds can be tailored to unique specifications but may require more investment upfront compared to standard options. Ultimately, understanding your project’s demands will guide you in choosing between a simple or complex design for your injection machine mold.
Step-by-Step Mold Fabrication Process
The fabrication process of creating an injection mold involves several steps that transform raw ideas into functional tools ready for production. Initially, it begins with detailed design work using CAD software to create precise blueprints of the desired part geometry. Once finalized, these designs are translated into physical molds through machining processes such as milling or electrical discharge machining (EDM).
After machining is complete, assembly follows where components like cores and cavities are fitted together meticulously to ensure proper alignment during plastic manufacturing. Following assembly, surface treatments may be applied to enhance durability and reduce friction during the molding cycle—key factors when considering how to make an injection mold that lasts through multiple runs of plastic parts. Finally, testing prototypes ensures that everything functions flawlessly before moving onto full-scale production.
Quality Control Measures
Quality control measures are indispensable throughout the entire process of creating an injection mold; they ensure that every aspect meets stringent industry standards for safety and functionality. Implementing regular inspections at each stage—from initial design checks through final molded part evaluations—helps identify potential issues early on in low volume plastic molding scenarios where mistakes can be costly.
One effective method includes using statistical process control (SPC) techniques which monitor variations in production parameters like temperature and pressure settings during operation—critical factors in successful plastic injection molding outcomes. Additionally, employing advanced technologies such as 3D scanning allows for precise measurements of molded parts against their original specifications—a must when determining if you’ve mastered how to make an injection mold successfully.
Setting Up the Injection Molding Machine
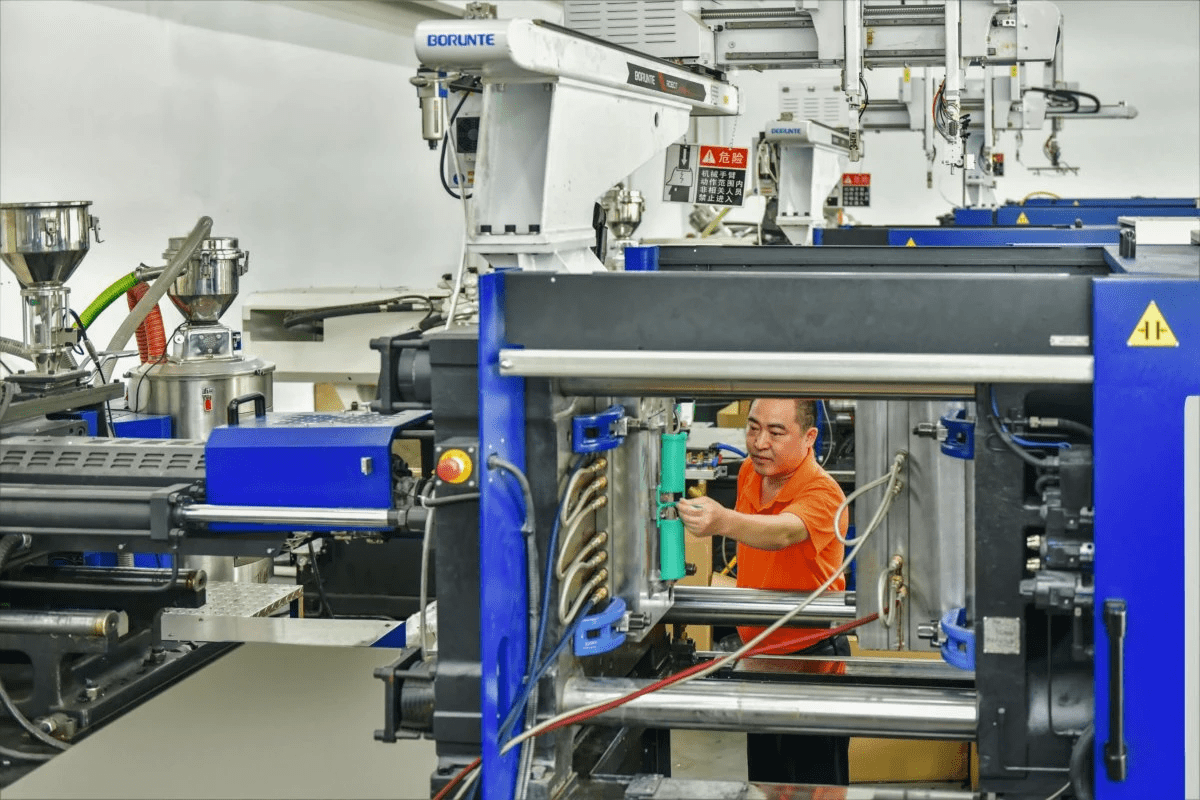
Setting up an injection molding machine is a crucial step in the plastic manufacturing process. Proper preparation ensures that you can produce high-quality parts efficiently, minimizing waste and maximizing output. This stage involves checking equipment, calibrating settings, and ensuring that all components are ready for operation.
Preparing the Machine for Production
To successfully prepare the machine for production, start by conducting a thorough inspection of the injection machine mold and its components. This includes checking for any wear or damage, cleaning out any leftover materials from previous runs, and ensuring that all safety features are operational. Additionally, make sure to load the appropriate injection moldable plastics into the hopper to ensure compatibility with your design specifications.
Once everything looks good on a physical level, it’s time to set up your parameters based on your specific project requirements. This involves programming cycle times and adjusting settings tailored for low volume plastic molding if necessary. A well-prepared machine not only enhances efficiency but also contributes significantly to producing consistent quality in molded parts.
Importance of Temperature and Pressure Settings
Temperature and pressure settings are pivotal in achieving optimal results during plastic injection molding. Each type of injection moldable plastics has specific temperature thresholds that must be adhered to; exceeding these can lead to defects such as warping or incomplete fills. Similarly, maintaining proper pressure ensures that molten plastic flows evenly into every cavity of the mold without creating air pockets or voids.
Understanding how to make an injection mold requires knowledge about these critical parameters because they directly affect cycle times and overall product quality. For instance, too much pressure can cause flash—excess material seeping out from between mold halves—while too little may result in under-filled parts. Therefore, always refer back to material data sheets when setting these controls.
Troubleshooting Common Machine Issues
Even with careful setup, issues can arise during production that may hinder efficiency or compromise quality in plastic manufacturing processes like injection molding. Common problems include inconsistent flow rates, unexpected temperature fluctuations, or even mechanical failures within the injection machine mold itself. Knowing how to identify these issues quickly is essential for maintaining productivity.
For example, if you notice irregularities in part dimensions or surface finish quality during low volume plastic molding runs, it might indicate a problem with either temperature control or pressure settings needing adjustment. Regular maintenance checks can help preemptively address many common issues before they escalate into significant downtime concerns. Keeping detailed logs of past problems will also aid in identifying recurring issues over time.
The Injection Molding Process
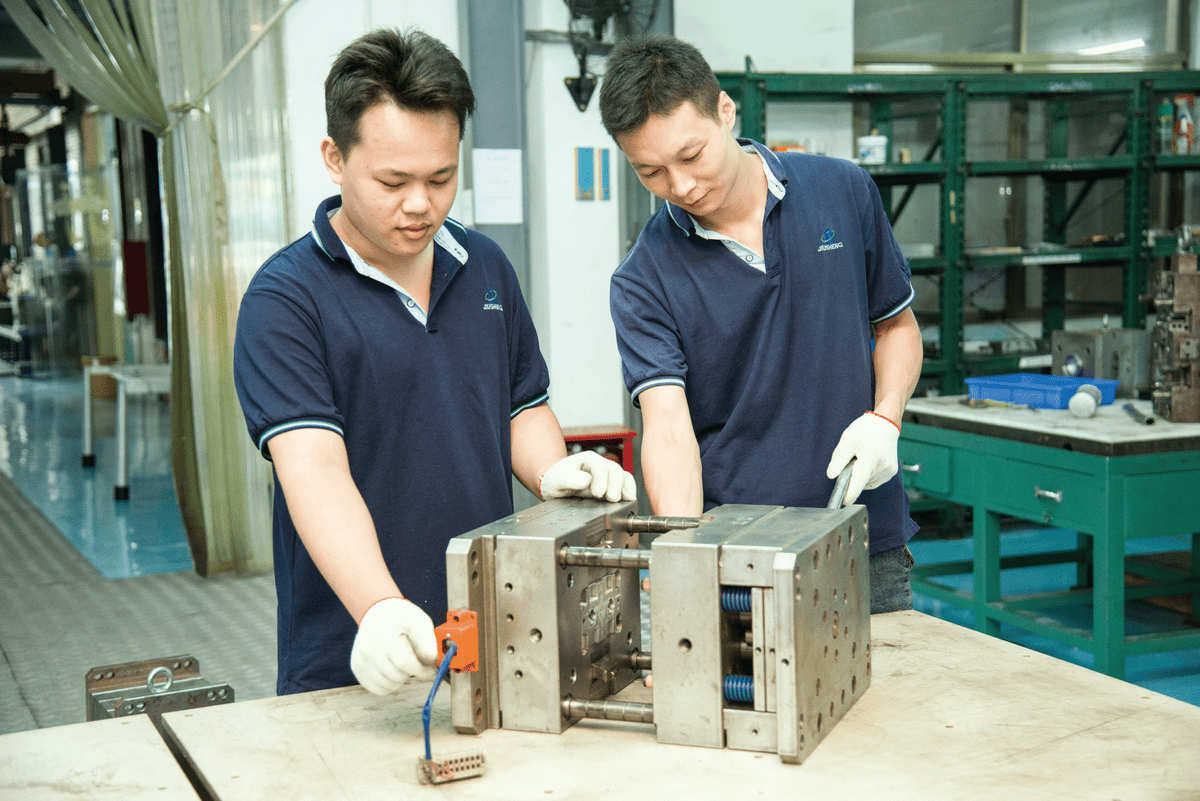
Injection molding is a fascinating blend of art and science, where the magic happens to transform raw materials into intricate plastic parts. This process is particularly advantageous for low volume plastic molding, allowing manufacturers to create high-quality components with precision and efficiency. Understanding the nuances of this process is crucial for anyone looking to delve into plastic manufacturing.
Understanding Low Volume Plastic Molding
Low volume plastic molding refers to producing smaller quantities of molded parts, typically ranging from a few dozen to several thousand units. This method is ideal for prototypes or specialized products that may not require large-scale production runs but still demand high-quality standards. Knowing how to make an injection mold for low volumes can save time and resources while ensuring that the final product meets desired specifications.
In low volume scenarios, selecting the right injection moldable plastics becomes even more critical since material costs can significantly impact overall production expenses. Additionally, manufacturers often utilize advanced techniques like rapid prototyping to streamline the design phase and minimize lead times. By mastering low volume plastic molding, businesses can effectively meet niche market demands without overcommitting resources.
Cycle Time Management
Cycle time management plays a vital role in maximizing efficiency during the injection molding process. The cycle time encompasses all stages from injection through cooling and ejection of the molded part, impacting overall productivity in plastic manufacturing operations. To optimize this cycle, it’s essential to understand how temperature and pressure settings on your injection machine mold affect material flow and cooling rates.
By fine-tuning these variables, manufacturers can reduce cycle times without compromising quality—leading to increased output and profitability in their operations. Implementing effective monitoring systems allows teams to identify bottlenecks quickly and adjust processes accordingly for continuous improvement in cycle times across various projects involving injection moldable plastics. Ultimately, efficient cycle time management contributes significantly towards achieving cost-effective production goals.
Post-Molding Finishing Techniques
Once the initial injection molding process is complete, post-molding finishing techniques come into play to enhance the final product's appearance and functionality. These techniques may include trimming excess material (flash removal), surface polishing, or applying coatings that improve aesthetic appeal or durability—crucial steps when working with injection moldable plastics intended for consumer use or specific applications.
It's essential not only to focus on how to make an injection mold but also on these finishing touches that elevate a product from good to great in terms of market readiness. Manufacturers often employ various methods such as painting or printing logos directly onto molded parts during this stage—adding value through customization options tailored specifically for clients' needs within the realm of plastic manufacturing projects.
Attention paid during post-molding processes ensures that products not only meet functional requirements but also resonate well with end-users’ expectations—a key factor in competitive markets relying heavily on quality assurance practices throughout their production lines.
Quality Assurance in Injection Molding
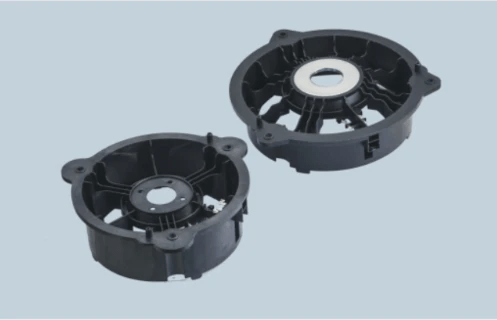
Quality assurance is a critical aspect of the injection molding process, ensuring that every molded part meets the required specifications and standards. By implementing rigorous testing protocols and continuous improvement practices, manufacturers can enhance their production processes and deliver high-quality products consistently. This section explores essential testing methods for molded parts, the importance of ongoing improvements, and how Baoyuan plays a pivotal role in maintaining quality assurance.
Testing Molded Parts for Quality
Testing molded parts for quality is crucial in the injection molding industry to ensure they meet design specifications and performance requirements. Various tests are conducted, including dimensional checks, visual inspections, and functional assessments to determine if the mold plastic injection process produced acceptable results. Additionally, using advanced techniques such as non-destructive testing can help identify internal defects without damaging the molded parts.
In low volume plastic molding scenarios, where precision is paramount due to limited production runs, thorough quality checks become even more vital. The use of injection moldable plastics necessitates stringent testing protocols to confirm that materials perform well under expected conditions. By establishing a robust testing framework, manufacturers can catch issues early on and make necessary adjustments to their processes.
Ultimately, effective quality testing not only ensures product reliability but also enhances customer satisfaction—an essential factor in today's competitive plastic manufacturing landscape. When companies understand how to make an injection mold that produces high-quality parts consistently, they set themselves up for long-term success.
Continuous Improvement Practices
Continuous improvement practices are integral to refining the injection molding process over time. By regularly evaluating production methods and outcomes, manufacturers can identify areas where efficiency can be enhanced or waste reduced—leading to better overall product quality. Techniques such as Six Sigma or Lean Manufacturing principles are often employed in this context to foster a culture of ongoing development.
Incorporating feedback from quality tests into production strategies allows teams to adapt quickly and implement changes that directly address any shortcomings observed during the testing phase of mold plastic injection products. This proactive approach ensures that each iteration of an injected part benefits from lessons learned previously while minimizing defects in future runs of plastic injection molding projects.
Moreover, fostering collaboration among team members involved in various stages—from design through production—can significantly enhance communication regarding potential improvements needed within the process chain itself. As organizations continue refining their practices based on data-driven insights gathered during quality assurance efforts, they will invariably see increased efficiency and reduced costs over time.
Role of Baoyuan in Quality Assurance
Baoyuan has established itself as a leader in ensuring quality assurance within the realm of injection molding by focusing on comprehensive evaluation techniques throughout each stage of production. Their commitment extends beyond just making sure that molded parts meet specifications; it encompasses creating an environment conducive to continual learning and adaptation based on real-world results from customers' experiences with their products.
By leveraging state-of-the-art technology combined with expert knowledge about how to make an injection mold effectively tailored for specific applications using various types of injection moldable plastics available today—Baoyuan stands out among competitors committed solely toward traditional methods without embracing innovation fully! Their proactive involvement helps clients navigate challenges associated with low volume plastic molding while still achieving outstanding results consistently across diverse projects.
Through dedicated efforts aimed at enhancing both product performance and customer satisfaction levels alike—Baoyuan exemplifies what it means when we talk about integrating quality assurance into every facet involved within modern-day plastic manufacturing methodologies!
Conclusion
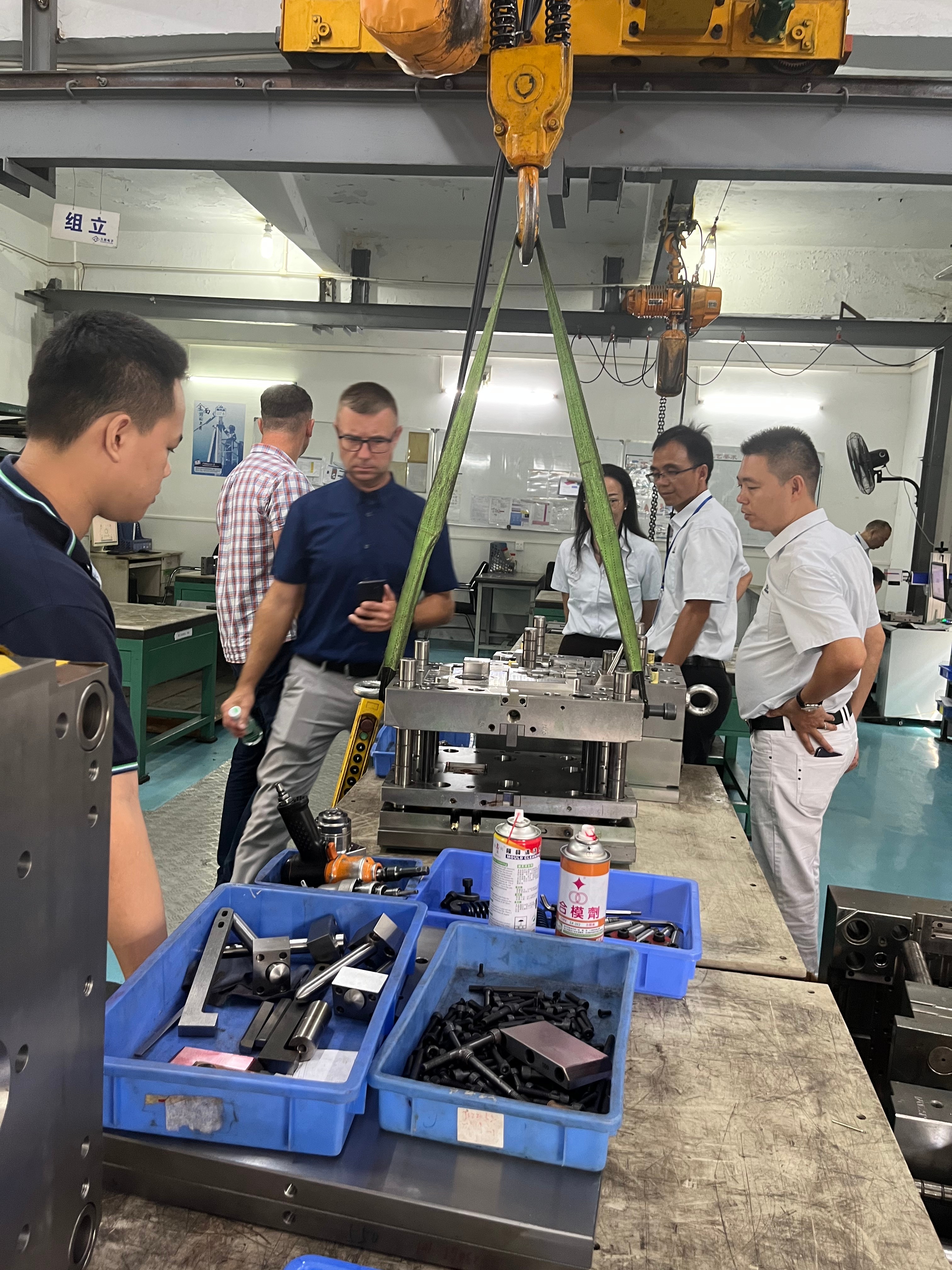
In wrapping up our journey through the world of injection molding, it's clear that mastering how to make an injection mold is essential for successful plastic manufacturing. From the precision needed in mold design to the intricacies of machine setup, each step plays a pivotal role in producing high-quality molded parts. By understanding these fundamental aspects, manufacturers can ensure efficiency and reliability in their injection molding processes.
Key Takeaways on Injection Mold Creation
When it comes to creating an effective injection mold, several key takeaways emerge. First, investing time in designing with CAD software can streamline the process of selecting the right injection moldable plastics, ultimately leading to better product outcomes. Additionally, embracing prototyping allows for valuable testing before full-scale production, ensuring that your plastic injection molding meets both functional and aesthetic standards.
Future Trends in Plastic Manufacturing
The landscape of plastic manufacturing is evolving rapidly, driven by innovations that promise to enhance efficiency and sustainability. One notable trend is the shift towards low volume plastic molding solutions that cater to niche markets while reducing waste. Moreover, advancements in materials science are leading to new types of injection moldable plastics that offer improved performance characteristics and eco-friendliness—an essential consideration for future-proofing any production line.
Getting Started with Injection Molding Projects
For those eager to dive into their own injection molding projects, starting small can be a wise strategy. Begin by familiarizing yourself with the fundamentals of how to make an injection mold and understanding which types of materials work best for your needs. With proper planning and execution using an appropriate injection machine mold, you’ll be well on your way to producing high-quality components tailored specifically for your projects.