Introduction
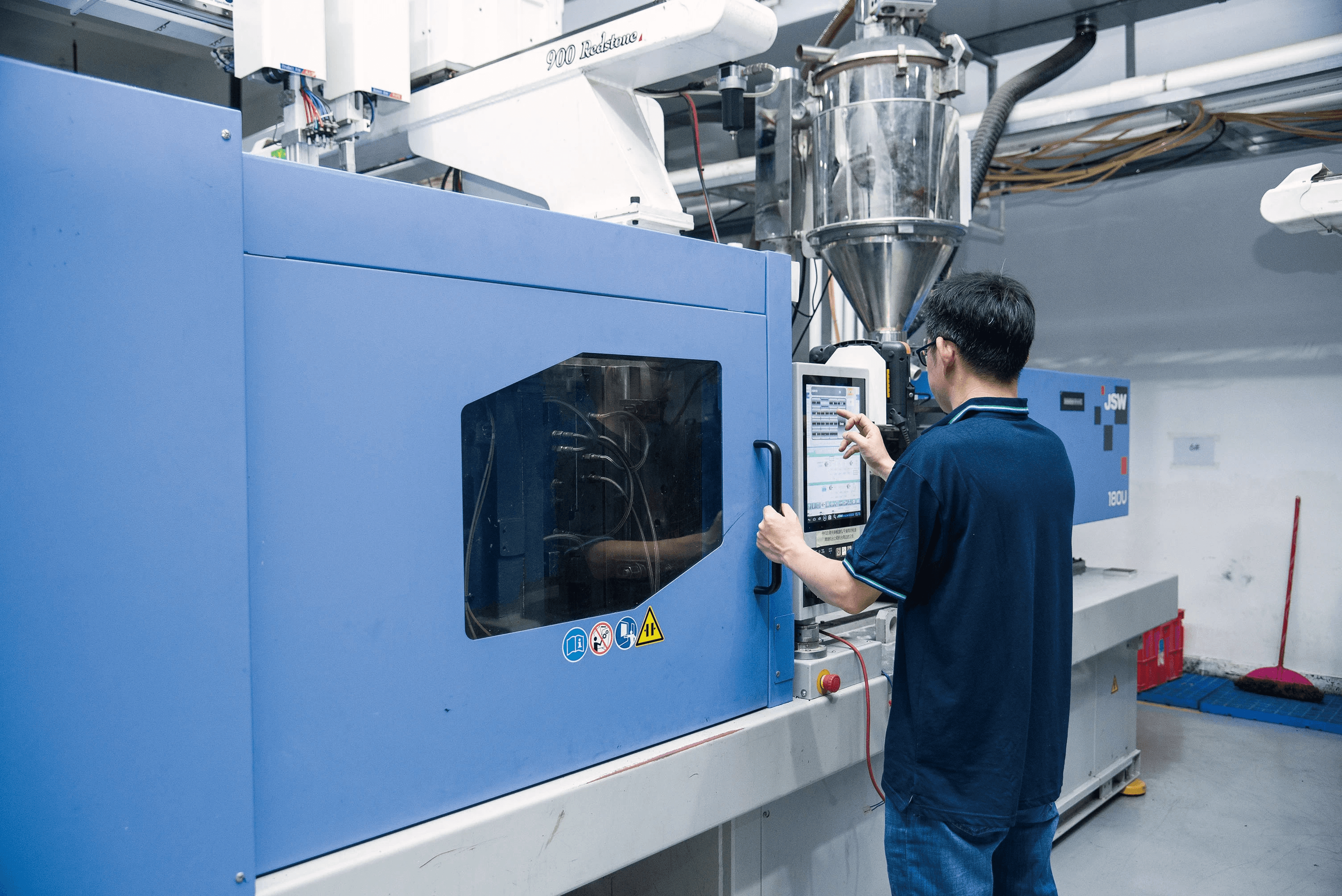
In the world of manufacturing, the injection molding barrel is a crucial component that often doesn’t get the spotlight it deserves. Understanding what a barrel in injection molding is can significantly impact production quality and efficiency. This introduction will explore the importance of barrel efficiency, key factors affecting performance, and how these elements contribute to successful manufacturing processes.
Understanding Injection Molding Barrels
An injection molding barrel serves as the heart of the injection molding machine, where raw plastic material is heated and melted before being injected into molds. The design of an injection molding barrel directly influences how well materials are processed, making it essential for manufacturers to grasp its functionality fully. By knowing what a barrel in injection molding entails, operators can better appreciate its role in achieving high-quality products.
Importance of Barrel Efficiency
The efficiency of an injection molding barrel cannot be overstated; it determines not only production speed but also energy consumption and material waste. An efficient barrel optimizes heating and cooling zones, ensuring that materials reach their melting points without unnecessary delays or energy expenditure. When manufacturers prioritize barrel efficiency, they pave the way for increased output and reduced costs—two critical factors in today’s competitive market.
Key Factors Affecting Barrel Performance
Several key factors influence the performance of an injection molding barrel, including temperature control, screw design, and material type. Understanding these variables helps manufacturers make informed decisions about their equipment choices—like selecting appropriate injection molding barrel sizes or knowing when it's time for an injection molding barrel replacement with a suitable kit. By focusing on these aspects, companies can enhance their production processes while minimizing downtime and maximizing overall effectiveness.
What is a Barrel in Injection Molding?
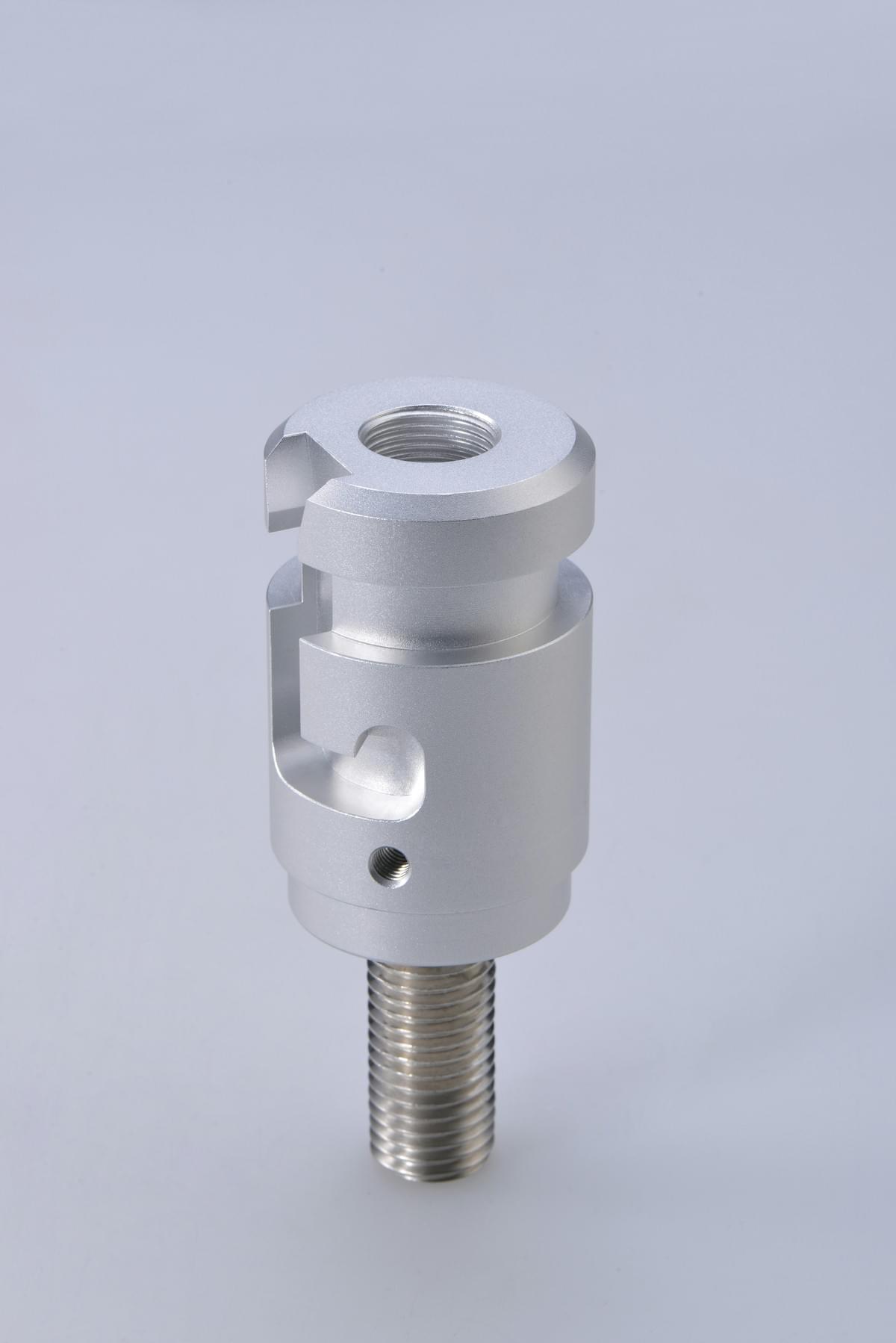
When diving into the world of injection molding, one cannot overlook the pivotal role of the injection molding barrel. It serves as the heart of the machine, where raw plastic pellets are transformed into intricately designed products. Understanding what a barrel in injection molding is and how it functions is essential for anyone involved in this manufacturing process.
Definition and Functionality
An injection molding barrel is a cylindrical chamber that holds and melts plastic pellets before they are injected into a mold. The functionality of this barrel lies in its ability to heat, mix, and transport molten plastic through a screw mechanism. Essentially, it’s where the magic happens—transforming solid materials into liquid form ready for shaping.
The efficiency of an injection molding barrel directly influences production speed and quality. A well-designed barrel ensures that the material reaches optimal melting temperatures while maintaining uniformity throughout the mixture. This process not only enhances product integrity but also minimizes waste during production.
Types of Injection Molding Barrels
There are several types of injection molding barrels tailored to different applications and materials used in production. The most common types include single-screw barrels, which are prevalent due to their simplicity and effectiveness; twin-screw barrels, known for their enhanced mixing capabilities; and specialty barrels designed for specific materials like thermoplastics or thermosets.
Each type has its unique features that cater to varying needs within manufacturing processes. For instance, twin-screw barrels often allow for better dispersion of additives, making them ideal for complex formulations. Understanding these differences can help manufacturers choose the right injection molding barrel sizes based on their specific requirements.
How the Barrel Affects Product Quality
The design and condition of an injection molding barrel significantly impact product quality—think about it like baking: if your oven isn’t calibrated correctly, your cake won’t rise! Factors such as temperature control within different zones of the barrel affect how well plastics melt and flow into molds.
Additionally, wear and tear on an aging injection molding barrel can lead to inconsistencies in material processing, resulting in defects or variations in product dimensions. Regular maintenance or timely replacement with an appropriate injection molding barrel kit can prevent such issues from arising. Ultimately, ensuring optimal performance from your equipment translates directly to higher quality end products.
Injection Molding Barrel Sizes
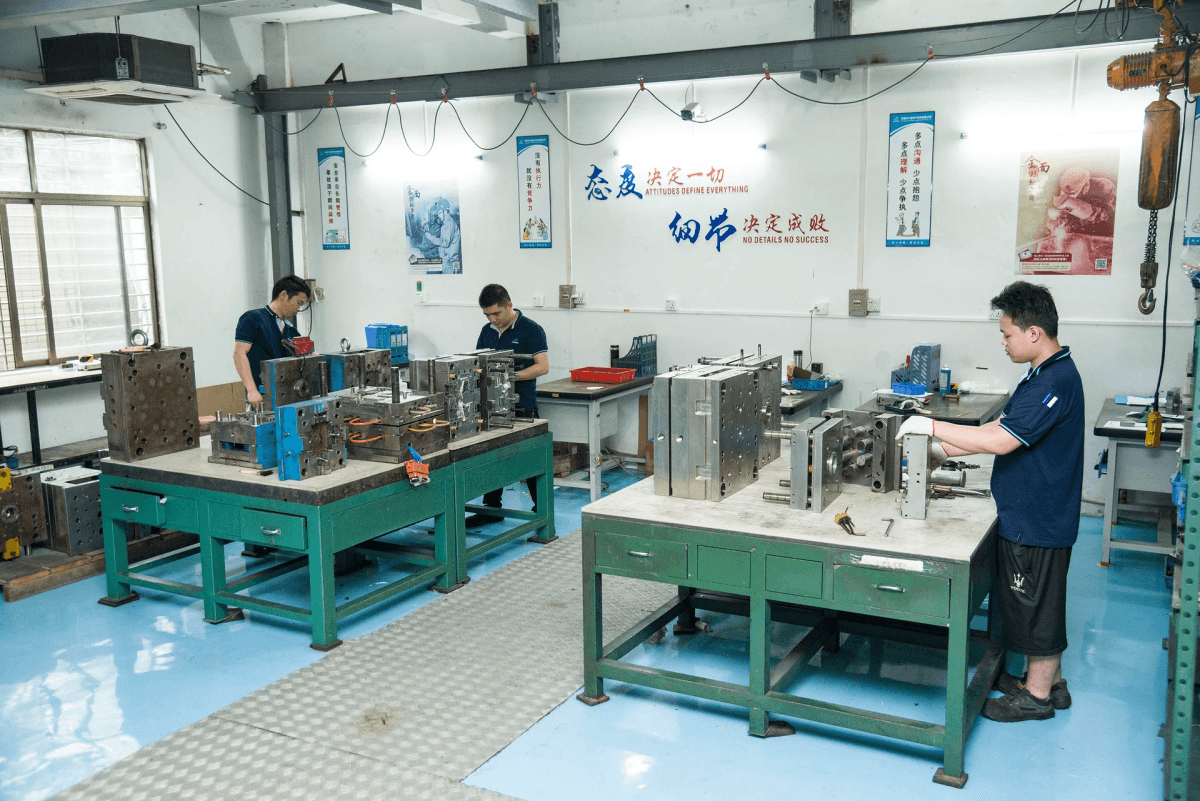
Standard Sizes Explained
Standard sizes for injection molding barrels vary widely based on the type of machine and the materials being processed. Typically, these barrels range from small capacities of about 50cc to larger ones exceeding 1000cc, accommodating different production needs. Knowing what is a barrel in injection molding helps clarify these variations; each size serves specific applications and materials, ensuring optimal performance during operation.
In addition to capacity, standard diameters also differ across machines—common diameters include 25mm, 35mm, and even larger sizes for heavy-duty applications. Each diameter correlates with specific flow rates and pressure capabilities that influence how well a material is injected into molds. Therefore, selecting the appropriate standard size is crucial for achieving desired outcomes in both quality and efficiency.
Choosing the Right Barrel Size
Choosing the right barrel size can be a daunting task if you're not familiar with your production requirements or materials used. Factors such as part complexity, cycle time, and material viscosity all play significant roles in determining which injection molding barrel size will work best for you. It’s also essential to consider what is barrel capacity in injection molding; this knowledge will guide you in selecting a size that not only meets your current needs but also anticipates future growth.
A common mistake many manufacturers make is opting for a larger barrel than necessary due to misconceptions about capacity requirements or potential waste reduction strategies. However, an oversized barrel can lead to inefficient heating and cooling cycles—impacting overall cycle times negatively. Therefore, conducting thorough assessments of your production goals will help ensure that you choose an injection molding barrel kit tailored specifically for your operational demands.
Impact of Size on Efficiency
The impact of size on efficiency cannot be overstated when discussing injection molding barrels; it directly influences cycle times, energy consumption, and material utilization rates. Larger barrels may seem advantageous at first glance but often result in longer heating periods due to increased volume—leading to wasted energy costs over time. Conversely, smaller barrels allow quicker cycle times but might limit flexibility when dealing with various materials or complex parts.
Additionally, understanding what are the barrel zones in injection molding helps further clarify how different sizes interact with temperature control systems within those zones—affecting both quality and throughput rates significantly. An optimized balance between size selection and zone management leads to enhanced productivity while minimizing defects during manufacturing processes. Ultimately, making informed choices regarding injection molding barrel sizes ensures that you're set up for success now—and down the line!
Barrel Capacity in Injection Molding
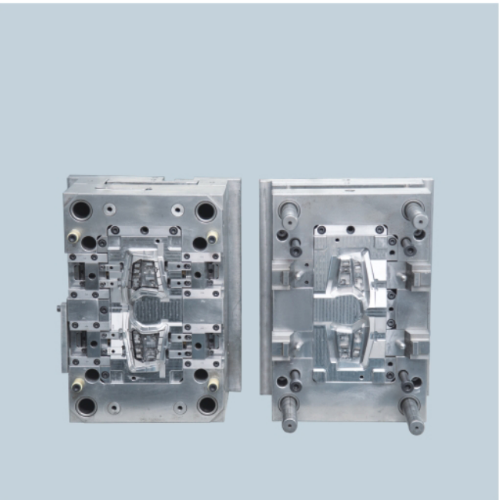
The capacity of an injection molding barrel is a critical factor that influences the overall efficiency and effectiveness of the injection molding process. Understanding what barrel capacity in injection molding truly means can help manufacturers optimize their production lines. It encompasses not only the physical size of the barrel but also its ability to handle different materials and maintain consistent output.
Determining Capacity and Limits
Determining the capacity of an injection molding barrel involves evaluating both its physical dimensions and its operational limits. The total volume a barrel can hold is typically measured in cubic centimeters or ounces, which directly correlates to the amount of material that can be processed at any given time. Additionally, factors such as material type, temperature settings, and pressure levels play pivotal roles in establishing these limits, ensuring that manufacturers don’t push their equipment beyond safe operational thresholds.
Capacity’s Role in Production Efficiency
Capacity plays a significant role in production efficiency because it dictates how much material can be processed during each cycle. An appropriately sized injection molding barrel allows for quicker turnaround times and reduced waste, as materials are melted and injected more effectively without unnecessary delays. Conversely, if a barrel's capacity is too small for the intended production volume, it could lead to frequent refills or longer cycle times, ultimately hampering productivity.
Capacity Calculations and Considerations
When calculating capacity for an injection molding barrel, several considerations must be taken into account to ensure optimal performance. Manufacturers often rely on formulas that incorporate factors like shot volume—how much material is injected per cycle—and density variations among different materials used in production processes. Moreover, understanding how to balance between various barrel sizes will help determine whether an injection molding barrel replacement or an upgrade to a larger model might be necessary for future projects.
What Are the Barrel Zones in Injection Molding?
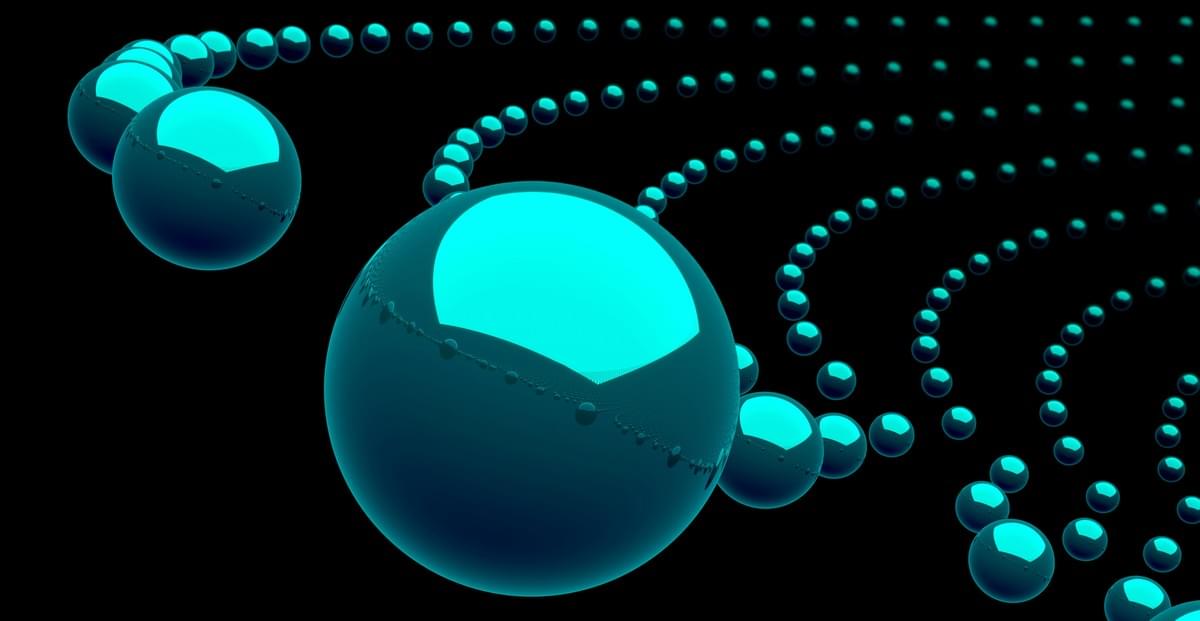
In the world of injection molding, understanding the barrel zones is crucial for achieving optimal performance and product quality. The barrel is segmented into different zones, each designed to perform specific functions during the molding process. By mastering these zones, manufacturers can significantly enhance the efficiency of their injection molding barrels.
Understanding the Heating Zones
Heating zones in an injection molding barrel are responsible for melting plastic pellets before they enter the mold cavity. Typically, there are multiple heating elements along the length of the barrel that control temperature variations essential for different types of materials. Properly calibrated heating zones ensure that plastic reaches its ideal processing temperature, which directly influences product quality and cycle times.
When discussing what a barrel is in injection molding, it’s important to note that these heating zones play a pivotal role in maintaining consistent melt flow rates. If temperatures are too low or too high, it can lead to issues like incomplete melting or degradation of materials. Therefore, understanding how to manage these heating zones is vital for anyone involved in injection molding processes.
Cooling Zones and Their Importance
Cooling zones follow heating zones in an injection molding barrel and serve a critical function: they help solidify molten plastic after it has been injected into a mold. This cooling phase ensures that products maintain their shape and integrity as they transition from liquid back to solid form. Without effective cooling mechanisms within an injection molding barrel, you risk warping or dimensional inconsistencies in your final products.
The importance of cooling cannot be overstated; improper cooling leads not only to defective parts but also extends cycle times—negatively impacting production efficiency. Moreover, understanding what is barrel capacity in injection molding also relates back to how effectively you can manage both heating and cooling processes within those designated zones. Efficiently balanced temperatures across these areas contribute significantly to overall productivity.
Optimizing Barrel Zones for Efficiency
Optimizing barrel zones involves fine-tuning both heating and cooling mechanisms to maximize operational efficiency while minimizing waste and defects during production runs. One way to achieve this optimization is by employing advanced temperature control systems that provide real-time data on zone performance throughout each cycle of your injection molding process. This allows operators to make necessary adjustments on-the-fly—enhancing both product quality and machine longevity.
Additionally, when considering an injection molding barrel replacement or investing in a new injection molding barrel kit, it's wise to examine how well those components handle thermal dynamics across all designated zones. Selecting equipment designed with efficient zone management capabilities can dramatically improve your overall output while reducing energy consumption—a win-win scenario! Furthermore, understanding what are the barrel sizes in injection molding can also play a role here; larger barrels may require more complex zone configurations compared to smaller ones.
Injection Molding Barrel Replacement
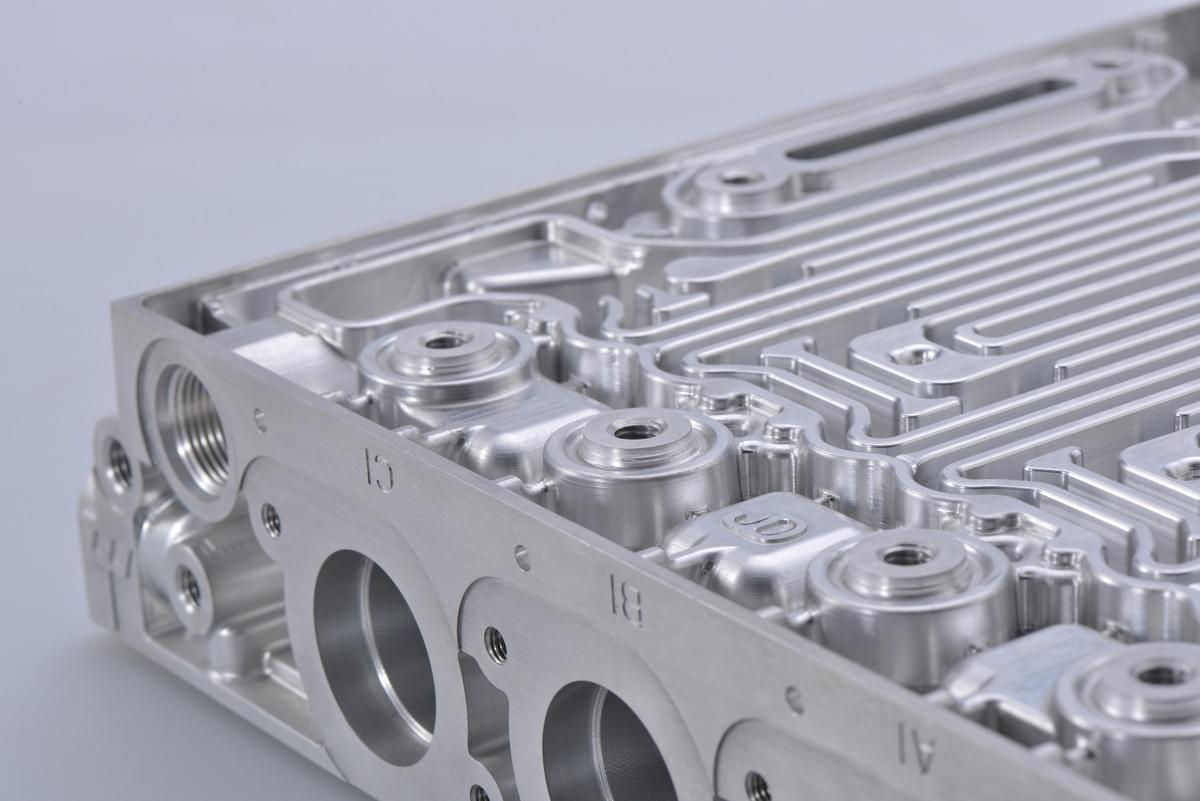
When it comes to maintaining optimal performance in injection molding, understanding when to replace your injection molding barrel is crucial. A worn-out barrel can lead to inefficiencies, product defects, and increased downtime during production. Recognizing the signs that indicate a need for replacement can save time and money in the long run.
Signs You Need a Replacement
Several telltale signs suggest it's time for an injection molding barrel replacement. First, if you notice inconsistent melt quality or fluctuating temperatures during production, this could point to issues within the barrel itself. Additionally, if there are visible signs of wear such as scratches or grooves on the internal surface of the barrel, it's time to consider whether a new injection molding barrel is necessary.
Another indicator is excessive material degradation; if your products are showing signs of burning or discoloration, it may be due to insufficient heat control in the barrel zones. Finally, frequent clogging or jamming during operation can signal that your current setup isn’t functioning efficiently anymore—an unmistakable sign that an upgrade might be in order.
Choosing the Right Barrel Kit
Selecting the right injection molding barrel kit is essential for ensuring compatibility with your existing machinery and maximizing efficiency. Start by identifying what type of materials you will be processing; different barrels cater to various polymers and resins based on their thermal properties and required capacities.
Next, consider the size of your current setup; understanding standard injection molding barrel sizes will help you find a kit that fits seamlessly into your production line without requiring extensive modifications. Lastly, consult with manufacturers or suppliers about any specific features or enhancements they offer—such as improved heating zones—that could elevate performance above what you're currently experiencing.
Steps for a Successful Replacement
To ensure a smooth transition during injection molding barrel replacement, follow these carefully laid steps. Begin by shutting down your machine completely and allowing it to cool down; safety should always come first! Next, detach any components connected to the existing barrel—this includes heaters and sensors—before removing it from its housing.
Once you've installed your new injection molding barrel kit into place, double-check all connections before powering up again; this ensures everything is secure and ready for action! Finally, run test cycles with monitoring equipment in place to observe how well the new system performs under operating conditions—paying close attention to temperature regulation across different zones ensures optimal function right from day one.
Conclusion
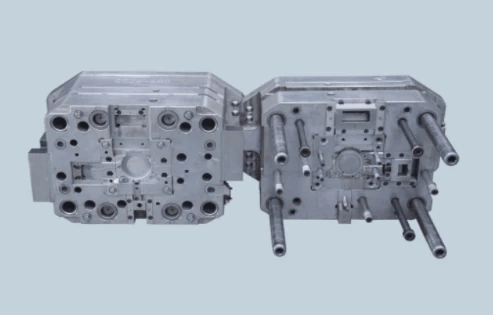
In the world of manufacturing, understanding the intricacies of the injection molding barrel can significantly enhance production efficiency and product quality. By maximizing the performance of this essential component, manufacturers can achieve higher output rates, reduce waste, and maintain consistency in their products. Whether it’s about selecting the right barrel size or optimizing barrel zones, every aspect plays a pivotal role in streamlining operations.
Maximizing Production with Efficient Barrels
To truly maximize production with efficient barrels, one must first grasp what is a barrel in injection molding? It serves as a crucial chamber where plastic is melted and injected into molds. The efficiency of an injection molding barrel directly influences cycle times and overall productivity; thus, understanding factors like barrel capacity in injection molding becomes vital for any operation aiming to boost output.
Efficiency isn’t just about speed; it also encompasses energy consumption and material usage. An optimized injection molding barrel ensures that materials are heated evenly across various zones—this leads to better melting processes and ultimately higher-quality products. By addressing potential inefficiencies within these systems, manufacturers can significantly cut costs while improving their bottom line.
The Role of Baoyuan in Barrel Efficiency
Baoyuan has established itself as a leader in providing high-quality solutions for injection molding barrels that cater to diverse industrial needs. Their innovative designs focus on enhancing performance while ensuring durability—two critical factors when considering an injection molding barrel replacement or evaluating an injection molding barrel kit. With Baoyuan's expertise, companies can navigate the complexities of choosing the right components tailored to their specific requirements.
The brand's commitment to research and development allows them to stay ahead of industry trends and continually improve their offerings. This proactive approach not only benefits manufacturers looking for reliable equipment but also contributes to advancements in technology related to what are the barrel zones in injection molding? Understanding these zones is essential for optimizing temperature control and processing efficiency.
Future Trends in Injection Molding Barrels
Looking ahead, several trends are shaping the future landscape of injection molding barrels that every manufacturer should keep an eye on. One such trend is the increasing demand for smaller yet more efficient barrels that optimize space without compromising performance—a response to modern manufacturing's lean principles. Furthermore, advancements in materials science could lead to stronger yet lighter barrels that enhance overall operational efficiency.
Another exciting development revolves around smart technology integration within barrels themselves! Imagine having sensors embedded within your system that provide real-time data on temperature fluctuations across different zones—what are the implications for quality control? This kind of innovation will redefine how we perceive what is barrel capacity in injection molding by allowing more precise adjustments based on live feedback.
As we move forward into this evolving industry landscape, staying informed about emerging technologies will be crucial for maintaining competitive advantage while ensuring sustainable practices remain at the forefront of manufacturing strategies.