Introduction
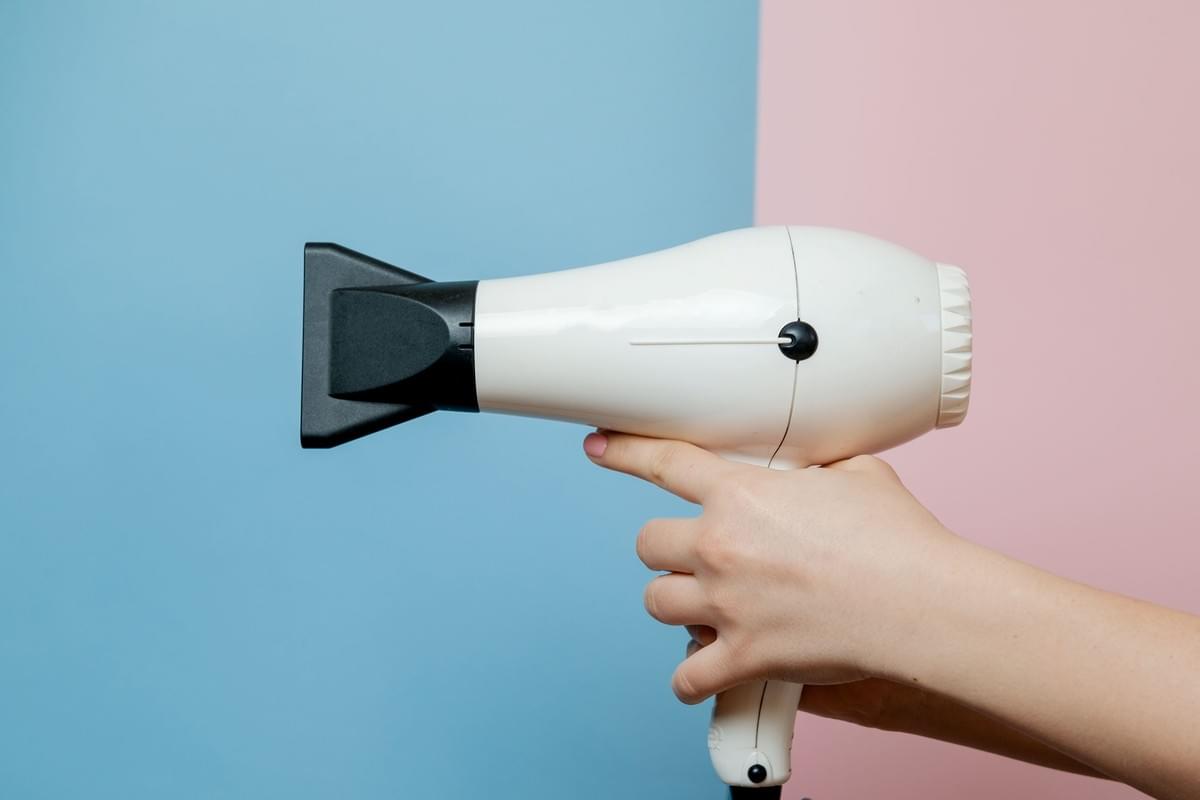
In the world of manufacturing, efficiency and innovation reign supreme, and one technology that stands out is 2 shot injection molding. This advanced process allows for the creation of complex parts with different materials or colors in a single cycle, making it a favorite among manufacturers looking to boost productivity. So, what is 2 shot injection molding? It’s a method where two different materials are injected into a single mold sequentially, resulting in a final product that combines the benefits of both materials.
What is 2 shot injection molding?
At its core, 2 shot injection molding involves using two distinct materials to create one cohesive part. The first material is injected into the mold, followed by the second material which bonds with the first during cooling. This technique not only enhances design possibilities but also improves product functionality by allowing for varying textures and properties within a single component.
Exploring double shot injection molding
What is double shot injection molding? Essentially, it's another term for 2 shot injection molding and emphasizes the dual-material aspect of this innovative process. By employing two-shot technology, manufacturers can produce items like toothbrush handles or automotive components that require both rigidity and flexibility—something traditional methods struggle to achieve efficiently.
The efficiency of 2K injection molding
When considering production costs and time constraints, what is 2K injection molding? It refers to the same two-shot process but highlights its effectiveness in reducing overall manufacturing time while maintaining high-quality standards. The efficiency gained from using a two-shot injection molding machine means fewer cycles are needed compared to traditional methods—translating directly into cost savings on labor and materials without compromising on quality.
Understanding 2 Shot Injection Molding
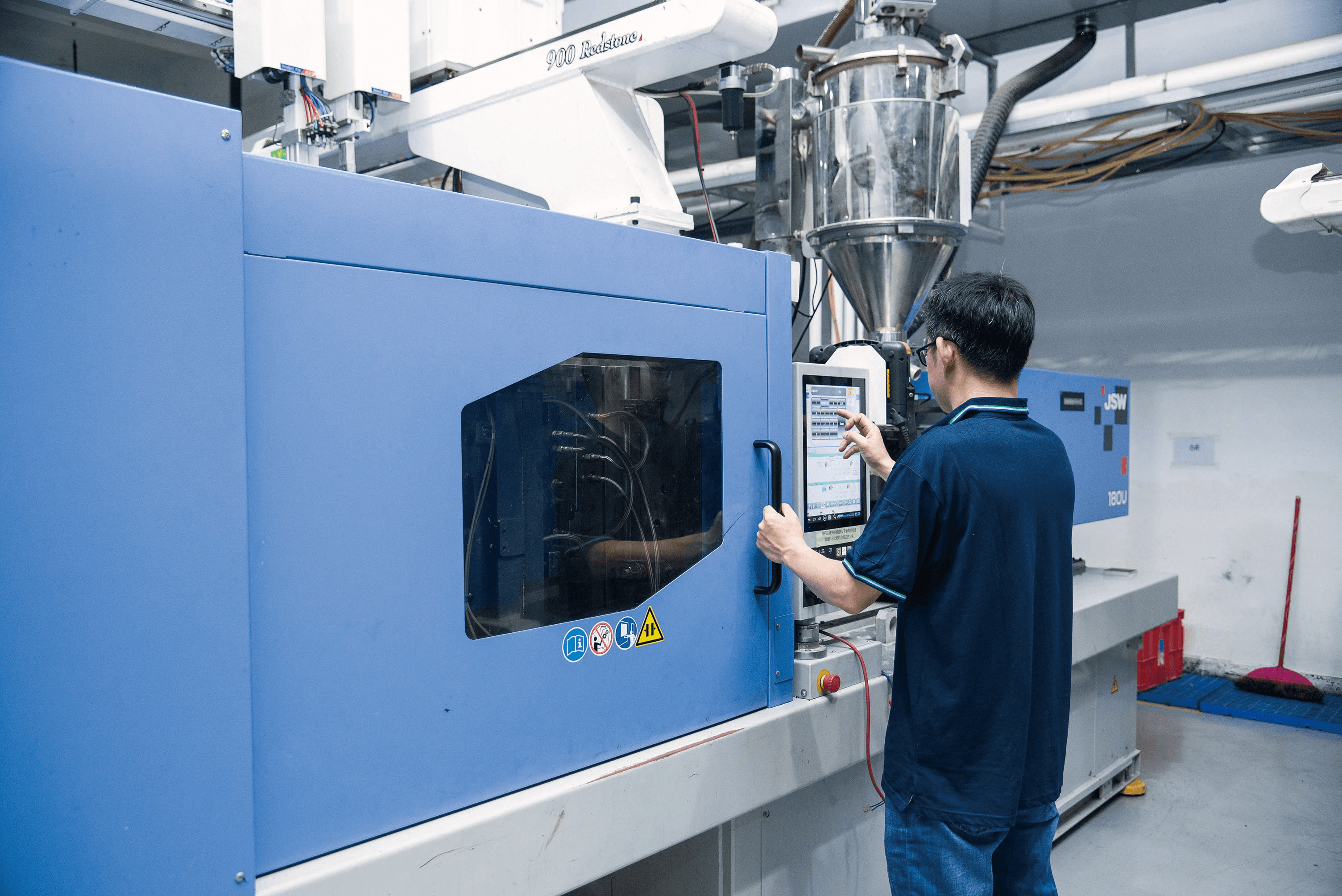
When we dive into the world of 2 shot injection molding, we uncover a fascinating process that blends materials to create complex components with ease. So, what is 2 shot injection molding? It’s a manufacturing technique where two different thermoplastic materials are injected into a single mold in sequence. This method allows for the production of parts that combine varying properties, enhancing both functionality and aesthetics.
The mechanics behind dual injection
The mechanics behind dual injection are quite ingenious. Essentially, a two-shot injection molding machine operates by injecting one material into a mold cavity, allowing it to cool partially before introducing the second material. This sequential process ensures that both materials bond effectively, creating a single cohesive part that exhibits the strengths of each component—something you can't achieve with traditional methods.
Understanding what is double shot injection molding helps clarify its advantages over conventional techniques. The dual-injection approach not only optimizes production efficiency but also minimizes waste and energy consumption—key factors in today’s environmentally-conscious manufacturing landscape. By utilizing advanced technology and precision engineering, manufacturers can produce intricate designs while maintaining high quality.
Applications of 2 shot injection molding
The applications of 2 shot injection molding are vast and varied, spanning numerous industries and product types. From consumer electronics to automotive components, this technology is employed wherever complex geometries and multi-material designs are beneficial. For instance, think about smartphone cases that require both rigidity and flexibility; these often rely on the unique capabilities of 2K injection molding.
Another exciting application lies in medical devices where biocompatibility and durability are paramount. Here, manufacturers leverage this technique to create ergonomic handles or housings that combine soft-touch surfaces with robust structural elements—an ideal blend for user comfort and device longevity. Overall, the versatility of 2 shot injection molding makes it an attractive option across multiple sectors.
Key industries utilizing this technology
Several key industries have embraced 2 shot injection molding as an essential part of their manufacturing processes. The automotive industry frequently utilizes this technology for producing dashboard components or exterior trims that require different textures or colors in one piece—a true game-changer! Similarly, consumer goods manufacturers benefit from its ability to create aesthetically appealing products without compromising on functionality.
In addition to automotive and consumer goods sectors, healthcare has seen substantial advancements thanks to double shot techniques as well. Medical device manufacturers leverage these capabilities for creating intricate assemblies like syringes or inhalers which need precise material properties for optimal performance. Thus, it's clear that understanding what is 2K injection molding reveals its significant role across various industries striving for innovation.
The Process of 2 Shot Injection Molding
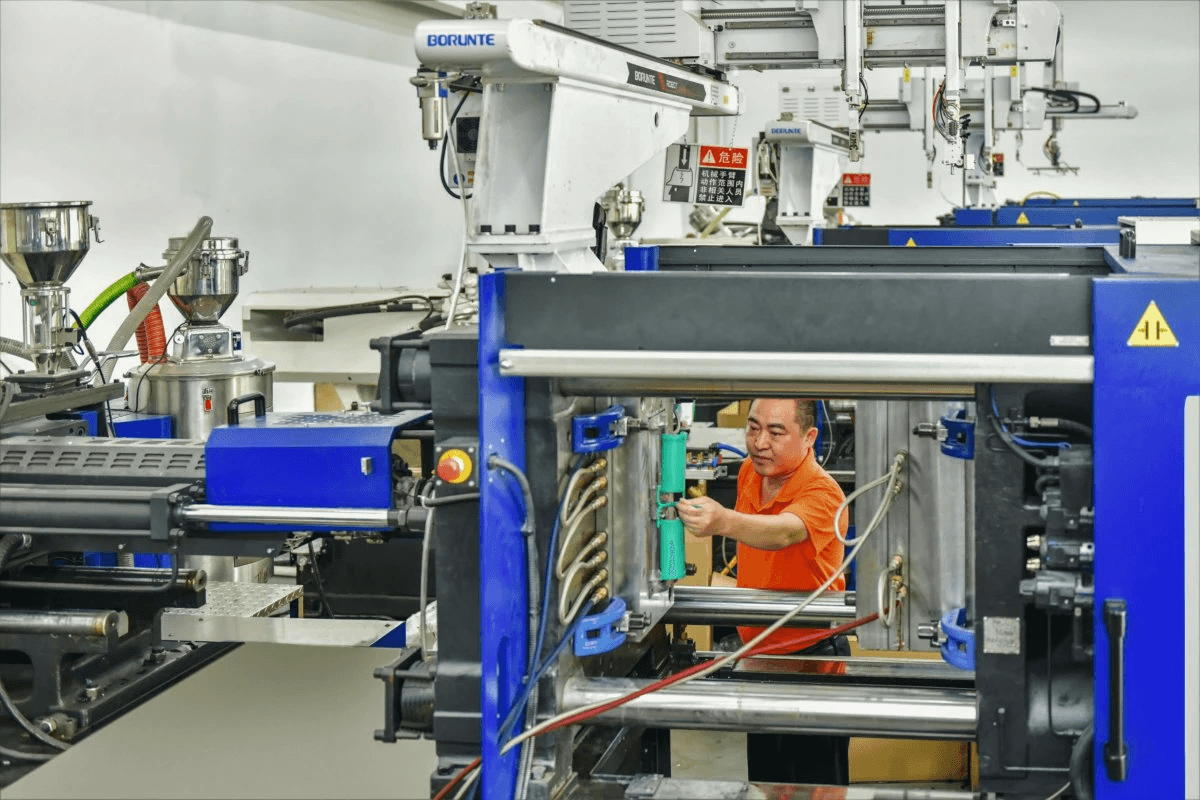
When diving into the world of 2 shot injection molding, one might wonder about the intricacies involved in this fascinating process. What is 2 shot injection molding? It’s a technique that allows manufacturers to create complex parts by injecting two different materials or colors in a single cycle, resulting in enhanced functionality and aesthetics. This method stands out not just for its efficiency but also for its ability to combine materials that would otherwise need separate processes.
Step-by-step breakdown of the process
The journey of 2K injection molding begins with the first material being injected into a mold, where it takes shape and cools slightly. Next, the mold shifts to allow for a second injection without removing the part; this is where double shot injection molding shines as it seamlessly integrates two materials into one cohesive product. Finally, after both injections are complete, the part is ejected from the mold—voilà! You have a finished product that boasts both durability and aesthetic appeal.
Understanding what is double shot injection molding helps clarify how this process differs from traditional methods. In contrast to single-material approaches, dual injection enables manufacturers to leverage unique properties from each material used—such as rigidity combined with flexibility—creating parts that are more functional than ever before. This innovative approach not only saves time but also reduces waste by minimizing secondary operations.
Comparison with traditional injection molding
In comparing 2-shot injection molding vs overmolding or even traditional injection techniques, it's evident that dual injection offers significant advantages. Traditional methods often require multiple steps and molds for different materials or colors, leading to longer production times and higher costs—what is 2 shot injection molding if not an efficient solution? By utilizing one machine and one cycle for two materials, manufacturers can streamline production processes while achieving impressive results.
Moreover, when examining 2K injection molding's cost-effectiveness compared to conventional methods, it’s clear that fewer machines and less labor translate into reduced operational expenses. Traditional methods may lead to increased scrap rates due to misalignment during assembly; however, two-shot techniques eliminate these concerns by creating parts in one seamless motion. This ultimately means lower costs without sacrificing quality—a win-win situation!
Role of the two-shot injection molding machine
Central to the success of this innovative process is none other than the two-shot injection molding machine itself. These specialized machines are designed specifically for handling multiple materials in a single cycle—what is double shot injection molding without them? With advanced technology at their disposal, these machines ensure precise control over temperature and pressure during each stage of production while maintaining consistent quality across batches.
Equipped with dual barrels and nozzles capable of injecting different materials sequentially or simultaneously, these machines exemplify efficiency at its best within manufacturing environments focused on innovation. Understanding what is 2 shot injection molding requires recognizing how integral these machines are in reducing lead times while enhancing product design possibilities all at once! Their role cannot be overstated; they’re truly at the heart of modern plastic manufacturing.
Advantages of 2 Shot Injection Molding

Cost-effectiveness of 2 shot injection molding cost
One of the primary advantages of 2 shot injection molding is its cost-effectiveness compared to traditional methods. By combining multiple materials and colors in one cycle, manufacturers can significantly reduce production costs associated with separate processes. The overall **2 shot injection molding cost** tends to be lower due to reduced labor, fewer machines required, and less waste generated during manufacturing.
Additionally, the efficiency gained from using a two-shot injection molding machine means that companies can produce more parts in less time without sacrificing quality. This translates to better profit margins and a more competitive edge in the market. Ultimately, businesses looking for cost-effective solutions will find that **what is 2 shot injection molding?** offers considerable financial benefits.
Enhanced product functionality and aesthetics
Another significant advantage lies in the enhanced functionality and aesthetics that **double shot injection molding** provides. By utilizing different materials simultaneously, manufacturers can create products with varied textures, colors, and even properties like softness or hardness—all within one seamless component. This capability allows designers greater freedom when conceptualizing products that are not only visually appealing but also functionally superior.
For instance, think about grips on tools or ergonomic handles; they often require both durability and comfort—qualities easily achieved through **2K injection molding** techniques. As consumers increasingly demand innovative designs coupled with high performance, companies leveraging these advantages stand out in a crowded marketplace by delivering products that meet these expectations head-on.
Reduction in manufacturing time and resources
Time is money—especially in manufacturing—and **two-shot injection molding** excels at minimizing both through its streamlined process. Unlike traditional methods where multiple steps are needed for assembly or finishing touches after initial production, this technique allows for everything to be done at once: injecting different materials into a single mold saves substantial time without compromising on quality or precision.
Moreover, by reducing the number of processes involved—from material handling to assembly—companies can conserve resources such as energy and raw materials while also decreasing their carbon footprint over time. In essence, adopting **2-shot injection molding vs overmolding** not only enhances productivity but also aligns well with sustainable practices sought by many modern businesses today.
Comparing 2 Shot Injection Molding and Overmolding
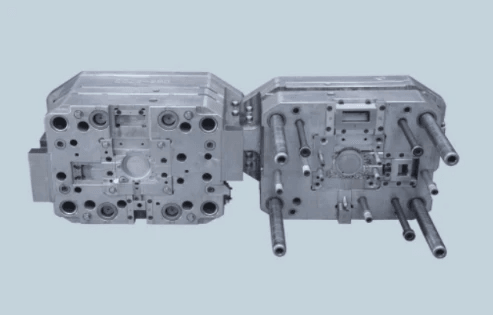
When diving into the world of plastic manufacturing, it’s crucial to distinguish between two shot injection molding and overmolding. So, what is 2 shot injection molding? Essentially, it involves injecting two different materials or colors into a single mold to create a single part with enhanced characteristics. On the other hand, overmolding is a process where one material is molded over another, typically combining hard and soft plastics for functional or aesthetic benefits. Understanding these differences helps manufacturers choose the right technique for their specific needs.
What is the difference between two shot and overmolding?
The primary difference between two shot injection molding and overmolding lies in their processes and outcomes. Two shot injection molding utilizes a specialized machine that allows for simultaneous or sequential injections of different materials into one mold cavity, resulting in a cohesive part with varied properties in one go. In contrast, overmolding involves first creating a base component which then gets coated or enveloped by another material in a separate step—ideal for adding grips or seals to existing parts.
Pros and cons of both techniques
Both techniques have their merits and drawbacks worth considering when deciding between 2-shot injection molding vs overmolding. The advantages of 2K injection molding include reduced assembly time since multiple materials are combined in one step, leading to lower labor costs overall—this can significantly impact your 2 shot injection molding cost efficiency! However, it requires more sophisticated machinery and tooling upfront compared to simpler overmolding setups that can be less expensive but may involve additional assembly steps later on.
On the flip side, while overmolding offers flexibility with material combinations (like soft-touch finishes), it might not provide the same level of integration as dual-shot methods do. Each approach has its unique applications; hence understanding these pros and cons can guide manufacturers in selecting the appropriate method based on project requirements.
Real-world applications and case studies
In practice, both techniques find their niche across various industries—from automotive components needing durability to consumer electronics seeking user-friendly designs. For instance, using 2 shot injection molding allows companies like Apple to create seamless products that combine aesthetics with function—think of those sleek phone cases that feel great in hand! Alternatively, companies often use overmolding for items like toothbrushes where comfort grips are essential.
Case studies reveal how manufacturers strategically choose between these methods based on desired outcomes; an automotive supplier might opt for dual-shot processes for intricate dashboard components requiring multiple textures while opting for traditional overmolding when creating ergonomic handles on tools—a perfect blend showcasing each technique's strengths!
Baoyuan's Expertise in Injection Molding
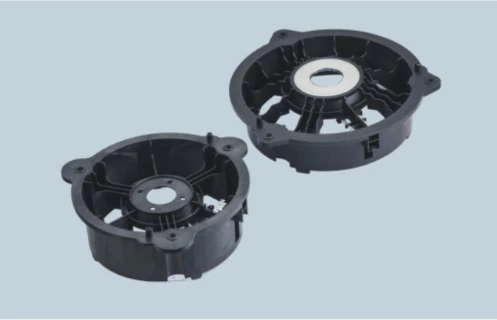
When it comes to mastering the art of 2 shot injection molding, Baoyuan stands out as a beacon of innovation and reliability. With years of experience under its belt, Baoyuan has carved a niche in the field, specializing in what is double shot injection molding and leveraging cutting-edge technology to produce high-quality plastic products. This expertise not only encompasses traditional methods but also embraces modern techniques like 2K injection molding, ensuring they remain at the forefront of the industry.
History of Baoyuan in the industry
Baoyuan's journey in the injection molding industry began several decades ago, with a commitment to excellence that has only grown stronger over time. Initially focusing on standard injection processes, they quickly recognized the potential of 2 shot injection molding and expanded their offerings to include this advanced technique. Today, Baoyuan is synonymous with quality and innovation, becoming a trusted partner for many businesses looking to enhance their product lines through efficient manufacturing solutions.
Technical proficiency and software utilization
In an era where technology reigns supreme, Baoyuan leverages state-of-the-art software tools and technical know-how to optimize their two-shot injection molding machine operations. Their team is trained extensively in both design and production aspects of 2K injection molding, ensuring every project meets rigorous standards for quality and efficiency. By utilizing advanced simulation software during the design phase, they can predict outcomes accurately and reduce potential waste—making 2 shot injection molding cost-effective for clients.
Commitment to quality in plastic product production
Quality assurance is at the heart of Baoyuan’s manufacturing philosophy when it comes to plastic products produced via dual injection techniques. Their rigorous testing protocols ensure that every item made through 2 shot injection molding adheres to international standards for durability and performance. This unwavering commitment not only bolsters customer satisfaction but also reinforces their reputation as leaders in understanding what is the difference between two shot and overmolding technologies.
Conclusion
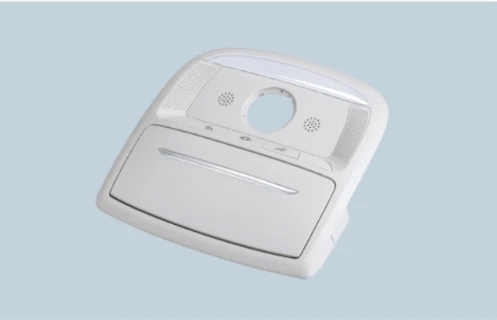
In wrapping up our exploration of 2 shot injection molding, it's clear that this innovative process offers numerous advantages over traditional methods. Not only does it enhance product functionality and aesthetics, but it also streamlines manufacturing processes, ultimately leading to cost savings. With its ability to combine different materials and colors in one seamless operation, what is double shot injection molding if not a game changer in the industry?
Summary of advantages in dual injection molding
The primary benefits of 2K injection molding are efficiency and versatility. By allowing manufacturers to create complex parts with varying properties in a single cycle, the 2-shot injection molding process significantly reduces production time and resources. Additionally, the finished products often boast improved durability and aesthetic appeal—qualities that are increasingly important in today's competitive market.
Key differences in 2-shot injection molding vs overmolding
When considering what is the difference between two shot and overmolding, it's essential to note that while both techniques involve combining materials, their approaches differ significantly. Two-shot injection molding utilizes a specialized two-shot injection molding machine to inject two different materials sequentially into a single mold for a cohesive final product. In contrast, overmolding involves applying a second layer of material onto an existing part—usually for added grip or cushioning—allowing for distinct applications depending on project requirements.
Future trends in injection molding technology
Looking ahead, the future trends in injection molding technology suggest an exciting evolution driven by advancements such as automation and smart manufacturing solutions. Innovations like real-time monitoring systems will likely enhance the precision of 2 shot injection molding processes while reducing waste and improving quality control further. As industries continue to seek more sustainable practices, we can expect increased interest in eco-friendly materials within both 2K injection molding and traditional methods alike.