Introduction
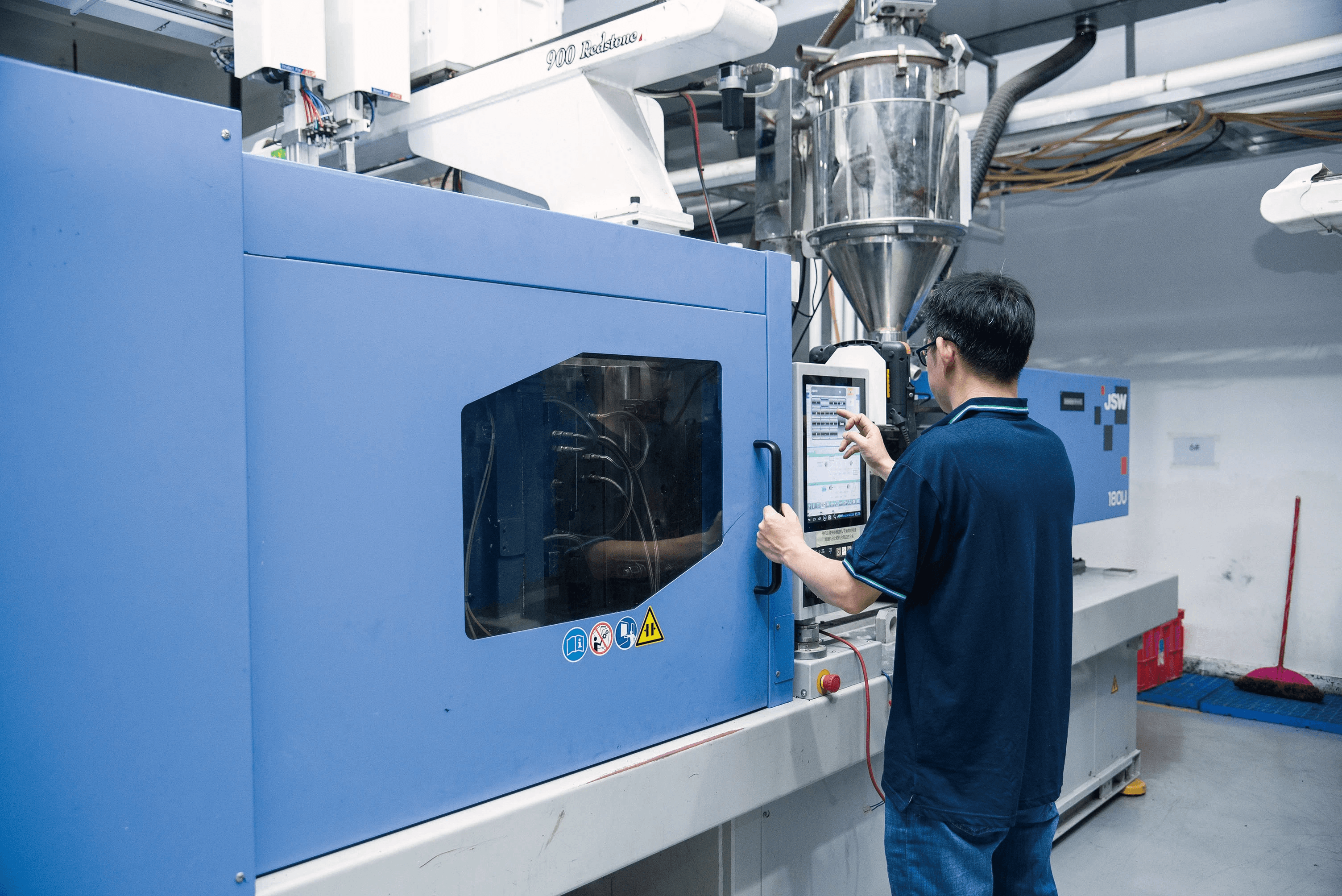
In the fast-paced world of manufacturing, the efficiency of the injection molding mold change procedure can significantly impact production timelines and costs. A well-executed mold change is not just a matter of swapping out parts; it’s about ensuring that the entire plastic injection molding machine operates at peak performance. By understanding the importance of this process, manufacturers can enhance their overall productivity and product quality.
Importance of Efficient Mold Change
Efficient mold changes are critical in minimizing downtime during production runs on an injection molding machine. Every minute spent on changing molds is a minute lost in potential output, making it essential to streamline this procedure for optimal results. Moreover, well-managed mold changes contribute to better maintenance practices, ultimately extending the life of both the injection machine mold and the plastic molding machine itself.
Key Components of Injection Molding
The injection molding process relies on several key components that work together harmoniously to produce high-quality products. These include the injection molding machine itself, which houses various mechanisms for heating and injecting plastic, as well as molds that shape the final product. Understanding these components helps operators effectively manage their roles in executing efficient mold changes and maintaining smooth operations.
Benefits of Streamlined Procedures
Implementing streamlined procedures for mold changes brings numerous benefits beyond just reduced downtime; it fosters a culture of continuous improvement within manufacturing environments. Enhanced coordination among team members ensures that everyone knows their responsibilities during an injection molding machine operation, leading to faster transitions between different products. Ultimately, these benefits translate into higher quality standards for injection molding machine products while also reducing operational costs.
Understanding the Injection Molding Process
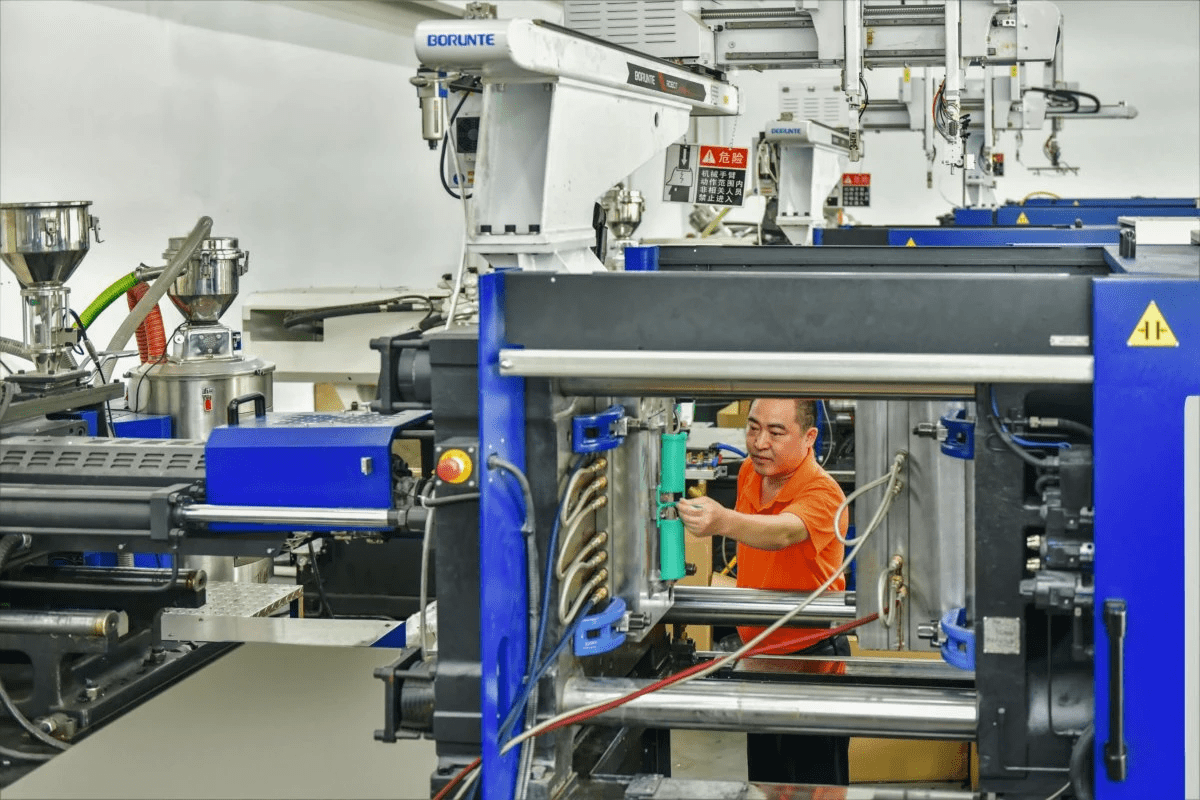
Injection molding is a fascinating process that transforms raw plastic into usable products through a series of well-orchestrated steps. This method relies on high pressure to inject molten plastic into a mold, where it cools and solidifies into the desired shape. Understanding these basic principles is crucial for anyone involved in the injection molding mold change procedure, as it lays the foundation for efficient production.
Basic Principles of Plastic Injection Molding
At its core, plastic injection molding involves melting plastic pellets and injecting them into a precisely designed injection machine mold under high pressure. The process begins with the heating of plastic resin until it reaches a molten state, followed by its rapid injection into the mold cavity. Once cooled, the solidified product is ejected from the mold, ready for further processing or assembly.
Efficiency in this process hinges on several factors, including temperature control, injection speed, and cooling time—all critical elements that can affect product quality and production rates. By mastering these principles, manufacturers can streamline their operations and minimize downtime during the injection molding machine mold change procedure. Ultimately, understanding these basics not only enhances productivity but also leads to higher quality products.
Anatomy of an Injection Molding Machine
An injection molding machine consists of several key components that work together harmoniously to produce high-quality molded parts. The main parts include the hopper (where raw materials are fed), the barrel (which melts and conveys plastic), and the clamping unit (which holds the mold in place during injection). Each component plays an essential role in ensuring that the entire process runs smoothly.
The clamping unit is particularly important; it applies pressure to keep the two halves of the mold tightly closed while molten plastic is injected inside. If this unit fails or isn't properly calibrated during an injection molding machine mold change procedure, it can lead to defects or even complete production stoppages. Understanding how each part functions helps operators troubleshoot issues quickly and effectively when working with a plastic molding machine.
Roles of Injection Machine Mold in Production
The injection machine mold serves as both a blueprint and a tool for shaping raw materials into finished products during manufacturing processes. It determines not only what shape will be created but also influences aspects like surface finish and dimensional accuracy—key factors that impact customer satisfaction with injection molding machine products. Therefore, investing in high-quality molds pays off significantly in terms of both durability and performance.
Moreover, molds must be maintained meticulously to ensure their longevity; regular inspections can catch wear before it becomes problematic during production runs or after an injection molding mold change procedure. The design complexity of an injection machine mold also affects cycle times—more intricate designs may require longer cooling periods but yield more detailed products overall. Thus, understanding these roles helps manufacturers make informed decisions about their production capabilities and strategies moving forward.
Preparing for Mold Change
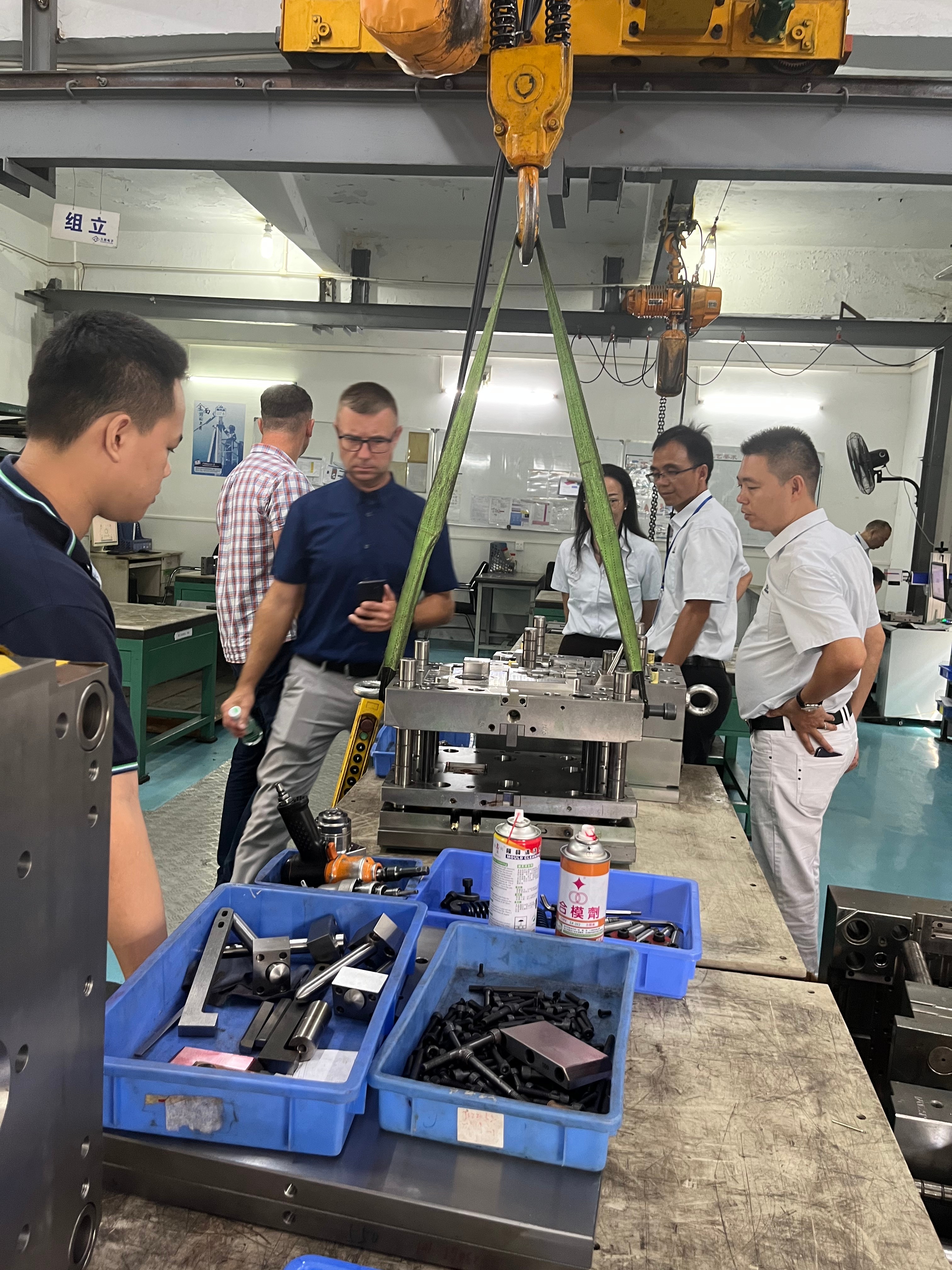
Preparing for an injection molding mold change is crucial to ensure a smooth and efficient process. This phase sets the stage for the entire operation, minimizing downtime and maximizing productivity. By focusing on safety protocols, having the right tools ready, and ensuring seamless team coordination, you can enhance the effectiveness of your plastic injection molding machine.
Safety Protocols and Best Practices
Safety should always be a top priority when performing an injection molding mold change procedure. Before starting, ensure that all team members are familiar with safety protocols, including wearing appropriate personal protective equipment (PPE) such as gloves, goggles, and steel-toed boots. It's also essential to conduct a thorough risk assessment of the injection molding machine area to identify potential hazards associated with handling heavy molds or working with hot components.
Establishing clear communication about safety practices can prevent accidents during the mold change process. Make sure everyone knows emergency shutdown procedures in case something goes awry while dealing with the injection machine mold or other equipment. Regular safety training sessions will help reinforce best practices and keep everyone alert to potential risks involved in operating plastic molding machines.
Tools and Equipment Checklist
Having a comprehensive tools and equipment checklist is vital for any successful injection molding mold change procedure. Essential items may include wrenches, screwdrivers, hoists or cranes for lifting molds safely, alignment tools for proper positioning, and temperature sensors to monitor heating elements on your plastic injection molding machine. Don't forget smaller yet significant items like cleaning rags or lubricants to maintain machinery performance during this transition.
Before starting work on the injection molding machine products, double-check that all necessary tools are in good condition and easily accessible to avoid delays later on. A well-organized workspace not only speeds up the process but also contributes to overall safety by reducing clutter around heavy machinery like plastic molding machines. Ensuring that your team has everything they need at their fingertips will make for a more efficient operation.
Team Coordination and Communication
Effective team coordination is key when executing an efficient injection molding mold change procedure. Assign specific roles based on each member's expertise—this ensures that everyone knows their responsibilities during this critical phase of production involving the injection machine mold. Regular briefings before starting will help clarify tasks while fostering collaboration among team members.
Open lines of communication are essential throughout the entire process; this means encouraging team members to voice concerns or suggest improvements as they work with the plastic injection molding machine or handle molds directly. Utilizing hand signals or two-way radios can facilitate swift communication in noisy environments where verbal instructions might get lost amidst machinery sounds. Ultimately, strong teamwork leads to quicker adjustments during production runs while enhancing overall quality in your products.
Step-by-Step Injection Molding Mold Change Procedure
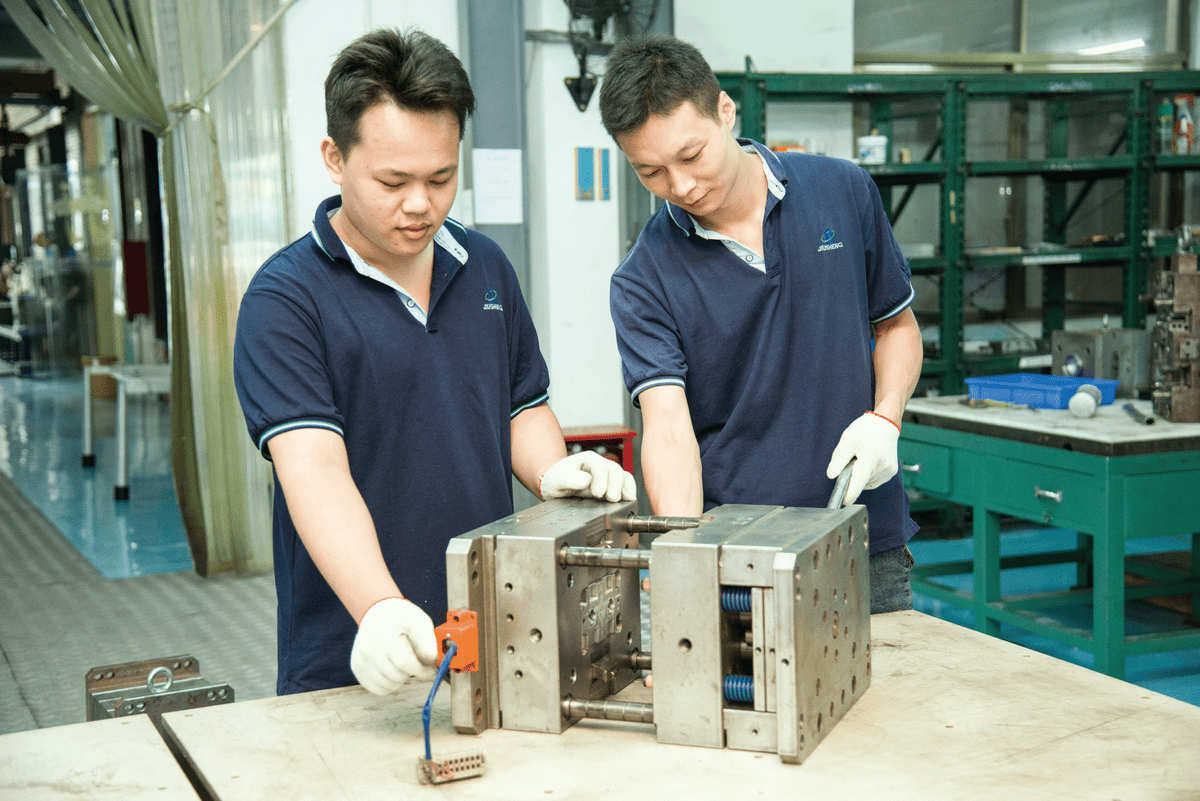
When it comes to the injection molding mold change procedure, precision and efficiency are key. This section will guide you through the essential steps to ensure a smooth transition between molds, thereby minimizing downtime and maximizing productivity on your plastic injection molding machine. Let's dive into the nitty-gritty of this crucial process.
Disengaging the Existing Mold
The first step in the injection molding mold change procedure is to safely disengage the existing mold from the injection molding machine. Begin by turning off the machine and ensuring that all safety protocols are followed; this includes wearing appropriate personal protective equipment (PPE) and checking for any residual pressure in the system. Once it's safe, use your tools to carefully detach the injection machine mold from its mounting points, making sure to keep track of any bolts or components for easy reassembly later.
After disengaging, inspect both the mold and machine for any signs of wear or damage that could affect future production runs. This not only helps maintain quality assurance but also allows you to address potential issues before they escalate into costly problems during subsequent cycles of plastic molding machine operations. Remember: a little preventive maintenance goes a long way in keeping your injection molding process efficient.
Installing the New Injection Molding Machine Mold
With the old mold safely removed, it’s time to install your new injection molding machine mold. Start by cleaning both surfaces where the new mold will be mounted; this ensures a proper fit and reduces contamination risks during production cycles. Carefully align your new mold with its mounting points on the plastic injection molding machine, securing it with bolts while maintaining even pressure across all contact points.
Once installed, double-check all connections and ensure that everything is tightly secured before proceeding further—loose fittings can lead to misalignment issues down the line! It’s also wise to consult any specific guidelines provided by your equipment manufacturer regarding installation practices for their particular model of plastic molding machine. Trust us; following these details can save you headaches later!
Adjusting Settings for Optimal Performance
Now that you've successfully installed your new injection machine mold, it’s time to adjust settings for optimal performance in your upcoming production runs. Begin by setting parameters such as temperature, pressure, and cycle times according to specifications suitable for both your new mold and material being used in production processes—these factors are critical in achieving high-quality outputs from your injection molding process.
Don’t forget about calibrating ejection settings as well! Properly adjusted ejection mechanisms will ensure smooth removal of finished products without damaging either them or their molds—a key aspect of maintaining quality assurance throughout manufacturing operations on plastic injection machines. Lastly, run a few test cycles with lower volumes before ramping up full-scale production; this allows you to identify any adjustments needed while still keeping waste minimal.
Common Challenges and Solutions
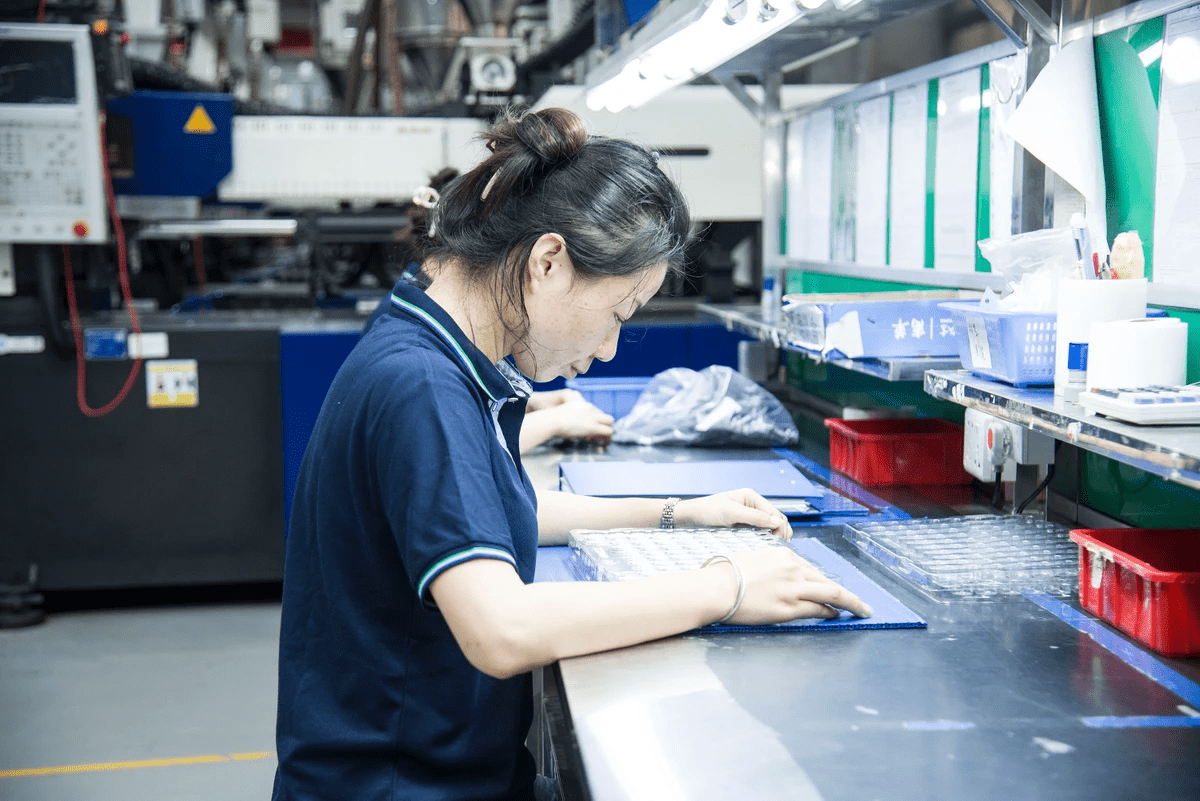
Navigating the complexities of the injection molding mold change procedure can be daunting, particularly when faced with common challenges. From alignment issues to troubleshooting machine products, understanding these potential setbacks is crucial for maintaining efficiency and quality in production. Let’s explore some of these challenges and their solutions to keep your plastic injection molding machine running smoothly.
Addressing Potential Mold Alignment Issues
One of the most frequent challenges during an injection molding mold change procedure is achieving proper mold alignment. Misalignment can lead to defects in the final product, including uneven surfaces or incomplete fills, which can be costly to rectify. To avoid this, ensure that your injection molding machine is calibrated correctly before installation; using alignment tools can significantly enhance precision during the setup process.
Another effective strategy is to conduct a thorough inspection of both the injection machine mold and the mounting plates prior to installation. Any debris or residue could interfere with proper alignment, so cleanliness should be a priority. Additionally, involving experienced team members familiar with the intricacies of the plastic molding machine can further mitigate risks associated with misalignment.
Finally, consider implementing a checklist for each mold change that includes steps specifically focused on alignment verification. This systematic approach not only streamlines procedures but also fosters a culture of accountability within your team—ensuring everyone knows their role in achieving optimal results during each injection molding process.
Troubleshooting Injection Molding Machine Products
When dealing with issues related to finished products from your plastic injection molding machine, early detection is key. Common problems such as surface blemishes or dimensional inaccuracies often stem from incorrect settings on the injection machine mold or inadequate material quality. Regularly reviewing production parameters and conducting sample tests after each mold change can help identify these issues before they escalate into larger problems.
If you encounter defects in your products, it’s essential to trace back through your recent changes—checking everything from temperature settings to cycle times on your plastic molding machine. Sometimes even small adjustments can have significant impacts on product quality; thus, meticulous attention to detail pays off over time. Don’t hesitate to involve cross-functional teams for insights; collaboration often leads to innovative solutions that you might not have considered alone.
Lastly, document all troubleshooting steps taken during production runs as part of an ongoing improvement strategy for future reference. Creating a knowledge base around common issues encountered during different stages of the injection molding process will empower your team and streamline responses when similar challenges arise again.
Learning from Baoyuan's Expertise
Baoyuan has long been recognized as a leader in overcoming challenges associated with the injection molding mold change procedure through innovation and expertise. Their experience highlights how investing in continuous training for operators can drastically reduce errors related to both equipment handling and product output quality from an injection molding machine. By fostering a learning environment where team members share insights gained from hands-on experiences, organizations can enhance their overall operational efficiency.
Moreover, Baoyuan emphasizes proactive maintenance practices as vital for minimizing downtime caused by unforeseen issues during production runs on plastic molding machines. Regular inspections not only extend equipment lifespan but also ensure that all components are functioning optimally—ultimately leading to better performance across all aspects of the injection process.
Incorporating lessons learned from industry leaders like Baoyuan into everyday practices not only mitigates risks but also promotes a culture of excellence within teams engaged in complex tasks like changing molds on an injection machine mold setup—transforming potential pitfalls into opportunities for growth and improvement.
Maintenance Tips for Long-Lasting Molds
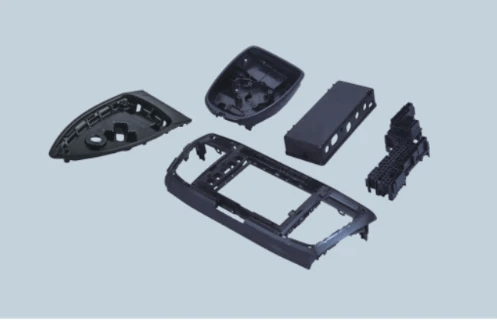
Maintaining your molds is crucial for ensuring the longevity and efficiency of your injection molding machine. Regular care not only extends the life of the injection machine mold but also enhances the overall quality of plastic injection molding machine products. By implementing a proactive maintenance routine, you can avoid costly downtime and ensure that your injection molding process remains smooth.
Regular Inspection and Care
Regular inspection of your molds is essential to identify any wear or damage that could affect performance during the injection molding mold change procedure. This includes checking for surface imperfections, alignment issues, and any signs of corrosion or rust on the injection molding machine components. By scheduling periodic maintenance checks, you can address potential problems before they escalate into major issues that disrupt production.
Additionally, proper cleaning after each use is vital to maintain the integrity of your molds. Residual plastic or contaminants can lead to defects in future runs, affecting the quality of your injection molding machine products. Using appropriate cleaning agents and techniques ensures that both the plastic molding machine and its components remain in top condition.
Importance of Quality Assurance
Quality assurance plays a pivotal role in maintaining high standards throughout the injection molding process. Implementing rigorous testing protocols helps ensure that every product produced meets specifications and customer expectations, directly impacting business reputation and profitability. Regular audits of both molds and processes contribute to identifying areas for improvement in mold design and functionality.
Moreover, consistent monitoring allows for quick adjustments during production runs if issues arise with an injection machine mold's performance. This proactive approach not only minimizes waste but also enhances overall productivity by reducing cycle times associated with troubleshooting defects in injected parts. Quality assurance becomes a part of your culture when everyone understands its significance in achieving excellence.
Benefits of Proficient Mold Design
Proficient mold design is fundamental to maximizing efficiency within any plastic molding machine operation. Well-designed molds facilitate smoother transitions during the injection molding mold change procedure while minimizing cycle times significantly — a win-win scenario! Additionally, investing time upfront into designing robust molds pays dividends by reducing maintenance needs over time.
A carefully crafted mold will also enhance product consistency by ensuring uniformity across all injected parts produced by an injection molding machine. This not only improves customer satisfaction but also reduces rework costs associated with defective products due to poor mold performance or design flaws. Ultimately, proficient mold design leads to greater profitability as it streamlines operations while enhancing product quality.
Conclusion
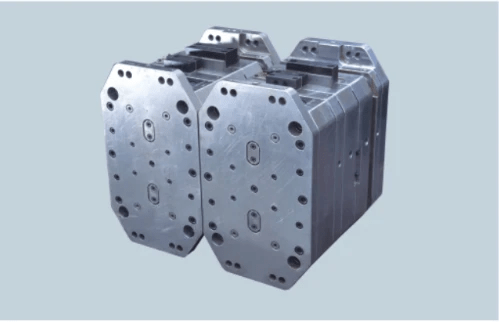
In wrapping up our exploration of the injection molding mold change procedure, it’s clear that efficiency and quality are paramount in the world of plastic manufacturing. By mastering the steps involved in this intricate process, businesses can significantly reduce downtime and enhance productivity. A well-executed mold change not only optimizes the operation of the injection molding machine but also leads to superior output in terms of product quality.
Boosting Efficiency with Proper Procedures
The injection molding process thrives on efficiency, and proper procedures play a crucial role in achieving that goal. Streamlining the injection molding mold change procedure minimizes interruptions, allowing for quicker transitions between different production runs. When teams are well-coordinated and equipped with the right tools for their plastic molding machines, they can achieve remarkable gains in productivity without sacrificing quality.
Enhancing Quality in Plastic Products
Quality assurance is vital when it comes to injection molding machine products; even minor errors during a mold change can lead to defects that compromise the entire batch. By adhering to best practices during the installation and adjustment of an injection machine mold, manufacturers can ensure that each product meets stringent quality standards. Ultimately, a focus on enhancing quality through meticulous procedures fosters customer satisfaction and strengthens brand reputation.
Continuous Improvement in Mold Change Techniques
The landscape of manufacturing is ever-evolving, making continuous improvement essential for staying competitive within the industry. Regularly revisiting and refining your injection molding mold change procedure not only helps identify areas for enhancement but also encourages innovation among team members. Embracing new technologies and methodologies will ensure that your plastic injection molding machine remains at the forefront of efficiency and effectiveness.