Introduction
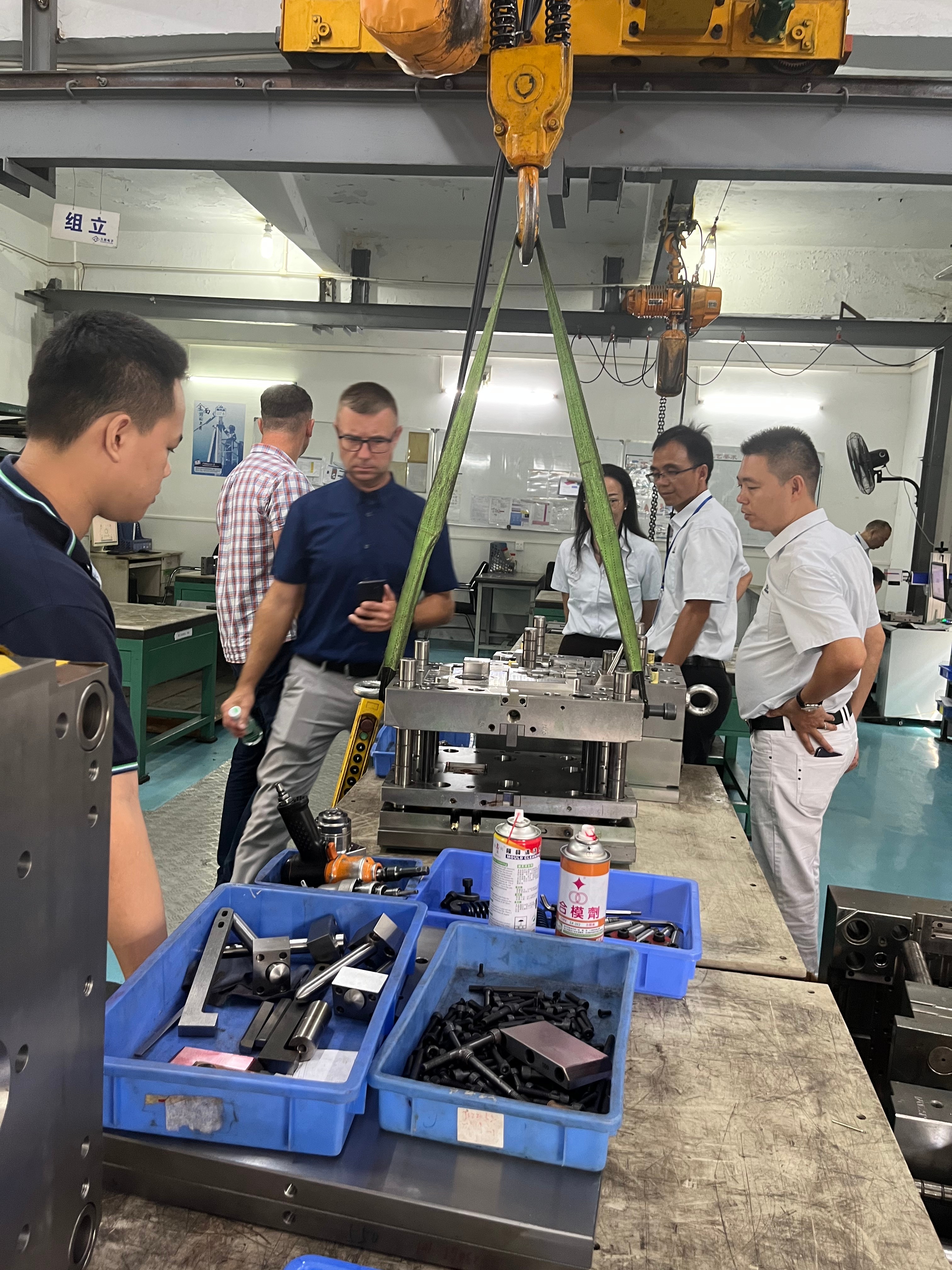
In the world of manufacturing, understanding plastic molding costs is crucial for businesses aiming to optimize their production processes. Plastic injection molding services have gained immense popularity due to their efficiency and versatility, making them a go-to choice for creating intricate designs at scale. However, navigating the landscape of injection molding can be complex, especially when considering the various factors that influence plastic molding price.
Understanding Plastic Molding Costs
Plastic molding price can fluctuate significantly based on several key elements, including material selection, design complexity, and production volume. For instance, different types of injection moldable plastics come with varying costs that can dramatically affect your budget. By grasping these nuances in plastic injection and mold plastic injection processes, companies can make more informed decisions about their manufacturing needs.
Factors Influencing Plastic Molding Price
These include the choice of materials used in production and the intricacy of design features that may require specialized tooling or molds. Additionally, market dynamics such as vendor expertise and regional pricing variations also play a vital role in shaping overall plastic molding price.
Benefits of Investment in Injection Molding
Investing in high-quality plastic injection services offers numerous advantages that go beyond mere cost savings. The efficiency and precision achieved through advanced injection casting techniques can lead to superior product quality and faster time-to-market for new designs. Furthermore, embracing this technology often results in long-term financial benefits by reducing waste and optimizing resource use throughout the production cycle.
Material Selection and Its Impact
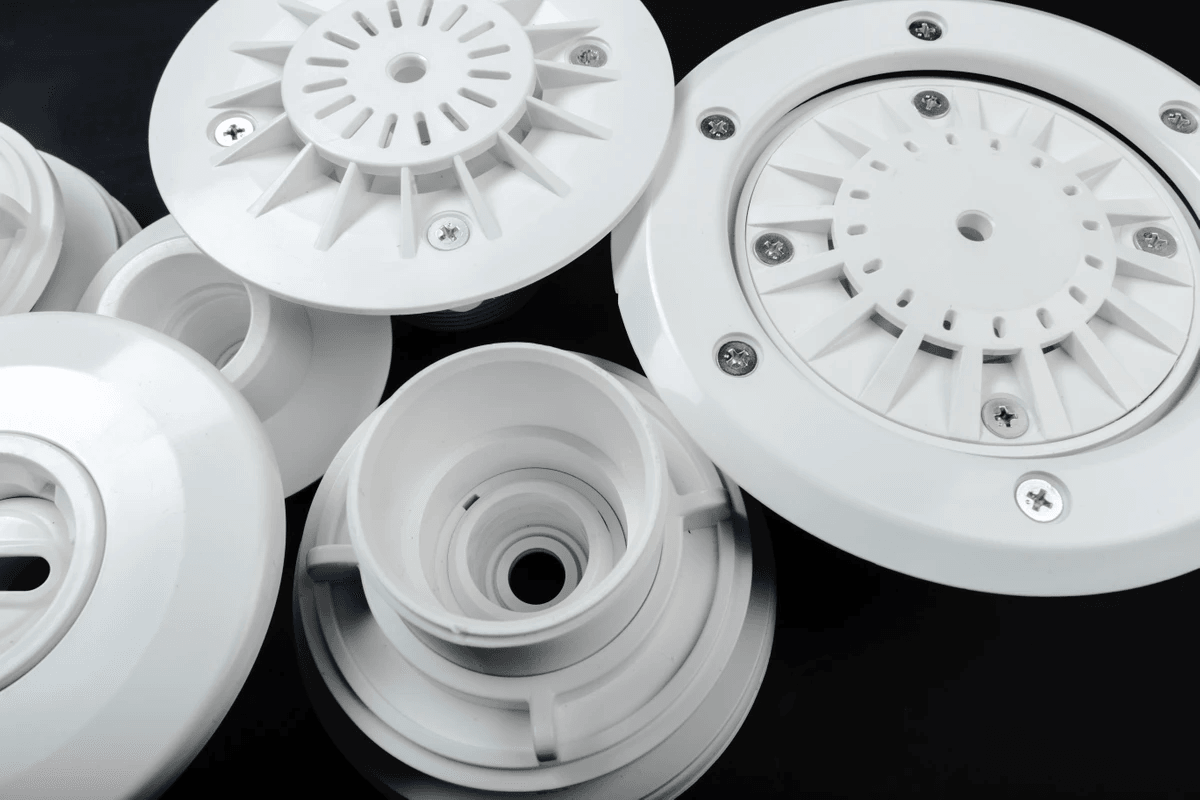
Comparing Injection Moldable Plastics
There’s a vast array of injection moldable plastics available, each with its own set of characteristics that can impact your project. For instance, thermoplastics like ABS and polycarbonate offer versatility and strength, while thermosetting plastics provide durability at higher temperatures but can be more expensive to process. Selecting the right type of plastic for your specific application is essential to balance functionality with budget constraints, ensuring you don’t overspend on unnecessary features.
Cost Variability Among Different Materials
Cost variability among different materials can be quite staggering in the world of injection molding. For example, high-performance polymers such as PEEK or PTFE may come with a hefty price tag compared to standard options like polypropylene or polyethylene. However, investing in pricier materials might save you money in the long run if they enhance durability or reduce maintenance costs—so it's all about weighing immediate expenses against future savings.
Recycling Options and Their Influence
Recycling options play an increasingly important role in determining plastic molding price today. Many manufacturers are now opting for recycled plastics due to their lower cost and reduced environmental impact—this not only helps in cutting down expenses but also aligns with sustainability goals. Additionally, using recycled materials can influence consumer perception positively, making your product more appealing without compromising quality or increasing production costs significantly.
Complexity of Design Features
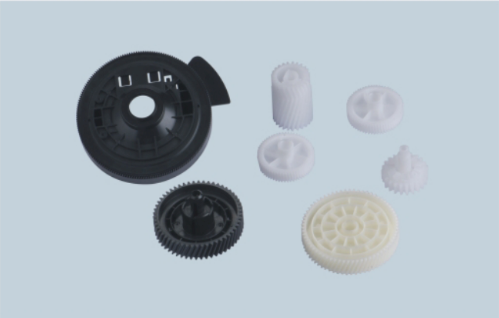
Role of Design in Plastic Injection Pricing
The design phase is often where many overlook the potential impact on plastic molding price. Every detail, from wall thickness to surface finish, can significantly affect the cost of mold plastic injection. A simple yet effective design will not only cut down on production time but also minimize material waste, leading to more economical outcomes.
How Intricate Designs Affect Costs
Intricate designs may seem appealing but can substantially inflate costs in the realm of injection molding. Complex features require specialized molds and additional setup time, which directly contributes to increased plastic injection molding prices. Moreover, these designs often necessitate advanced techniques like multi-cavity molds or secondary operations that add layers of expense.
Balancing Functionality and Budget
Finding the sweet spot between functionality and budget can be quite the juggling act when it comes to plastic injection projects. While it's tempting to go all out with intricate designs that showcase innovation, it's crucial to keep an eye on how these choices impact your overall investment in injection casting services. By prioritizing essential features while maintaining simplicity where possible, you can achieve a balance that keeps both functionality intact and costs manageable.
Production Volume Considerations
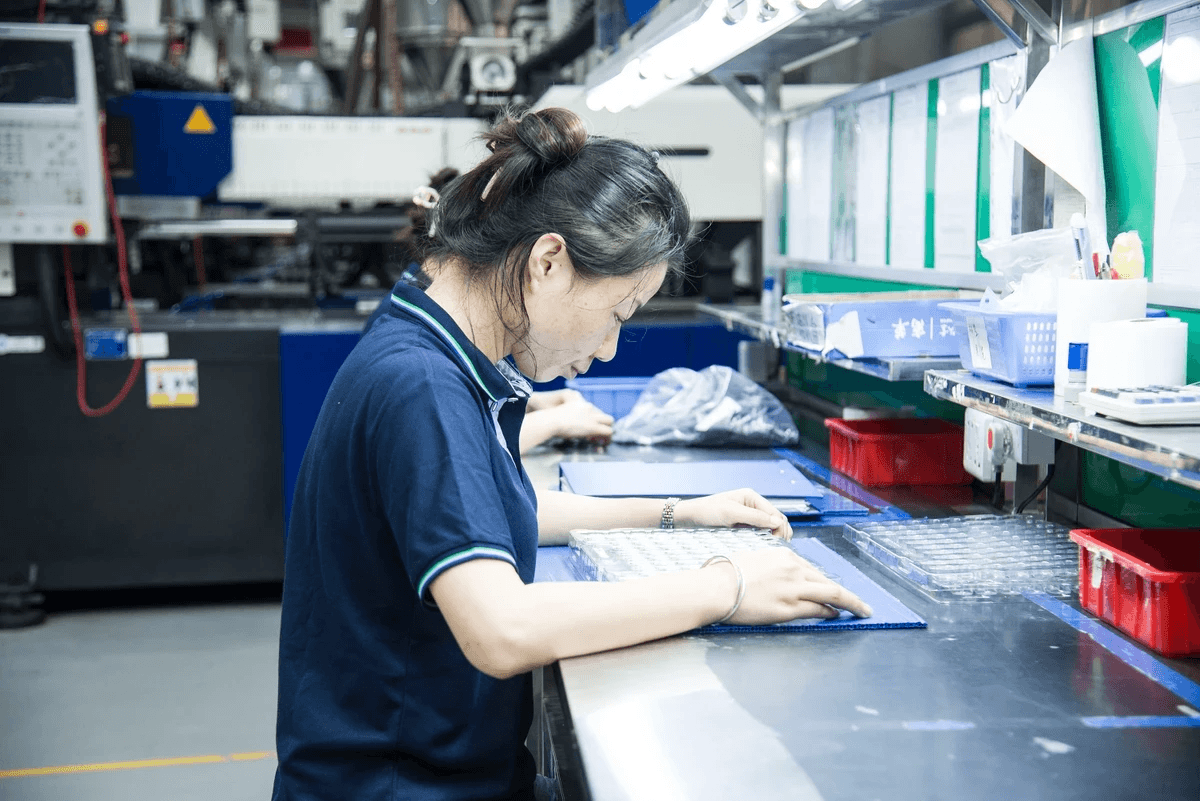
Economies of Scale in Injection Molding
Economies of scale are a game-changer in the world of plastic injection molding services. Essentially, as production volume increases, the cost per unit decreases due to fixed costs being spread over more items. This means that larger runs can significantly reduce the plastic molding price compared to smaller batches, making mass production an attractive option for businesses looking to save money.
Moreover, when manufacturers invest in high-volume production, they often benefit from lower material costs and more efficient use of machinery. This efficiency translates into reduced labor costs and quicker turnaround times, enhancing overall productivity. In a competitive market where margins matter, leveraging economies of scale through injection molding can be a strategic advantage.
Impact of Short Runs vs. Mass Production
The choice between short runs and mass production has significant implications for plastic injection pricing. Short runs might seem appealing for prototyping or small projects but often come with higher per-unit costs due to setup expenses that don’t get diluted across many pieces. In contrast, mass production allows companies to take full advantage of cost savings associated with larger quantities while also benefiting from streamlined processes.
However, it’s essential to consider the specific needs of your project before jumping into mass production; sometimes flexibility is more valuable than sheer volume. If your product requires frequent design changes or quick iterations, short runs could be the way to go despite higher costs per unit. Ultimately, understanding this balance is crucial for managing your budget effectively while still meeting market demands.
Cost Savings Strategies for Different Volumes
To navigate the complexities of plastic injection molding pricing across various volumes, businesses should employ targeted cost-saving strategies tailored to their needs. For high-volume productions, investing upfront in quality molds can yield long-term savings by reducing maintenance and replacement costs down the line—after all, quality tools lead to fewer defects and waste during manufacturing.
On the other hand, companies focusing on lower volumes might explore options like shared tooling or using less complex designs that require simpler molds—this approach helps mitigate initial expenses without sacrificing product quality too much. Additionally, considering partnerships with established vendors who offer flexible pricing models based on volume can provide further opportunities for cost reduction while ensuring access to reliable plastic injection services.
In summary, understanding how production volume affects plastic mold injection prices is vital for any business looking to optimize its manufacturing strategy effectively.
Tooling and Setup Expenses
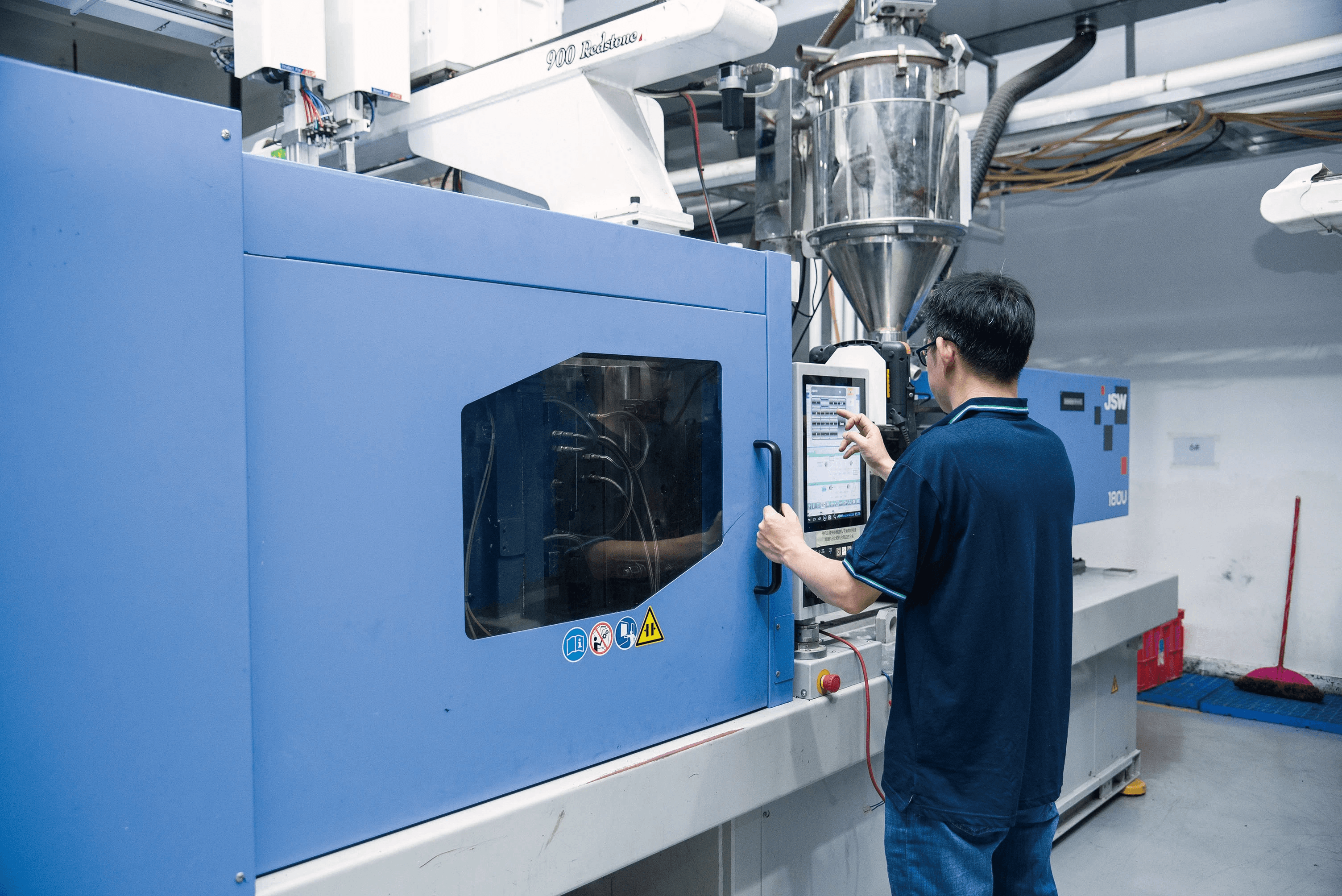
When diving into the world of plastic molding, understanding tooling and setup expenses is crucial for grasping the overall plastic molding price. Tooling costs can make or break your budget, especially in injection molding, where precision and quality are paramount. A well-planned investment in tooling not only ensures better product quality but also enhances production efficiency in the long run.
Understanding Initial Tooling Costs
Initial tooling costs are typically one of the most significant expenses when starting a new injection molding project. These costs encompass everything from designing and fabricating molds to setting up machinery for production. Depending on the complexity of your design and the type of injection moldable plastics used, initial tooling can vary greatly, impacting your overall plastic injection molding price.
It's essential to remember that while high-quality tools may seem like a hefty upfront cost, they often pay off through increased durability and reduced downtime during production runs. The initial investment sets the foundation for future production efficiency; thus, it’s wise to consider both short-term budgets and long-term goals when selecting your tools. Ultimately, understanding these initial costs helps businesses make informed decisions about their injection molding projects.
Maintenance and Replacement of Molds
Once you've navigated through initial tooling expenses, maintenance becomes a critical factor in sustaining efficient production processes. Regular maintenance of molds not only extends their lifespan but also ensures consistent quality in every batch produced with those molds. Neglecting mold upkeep can lead to defects that may compromise product integrity, resulting in increased waste—and we all know how that affects plastic molding price!
Moreover, as molds wear down over time due to repeated use with various injection moldable plastics, replacement becomes inevitable. Planning for this eventuality is crucial; having a strategy for mold replacement can help you avoid costly downtime during production cycles. In essence, investing time and resources into maintaining your molds pays dividends by keeping your operations smooth and cost-effective.
Long-Term Investment in Quality Tools
Investing in quality tools is not just an expense—it's a strategic move towards long-term success in plastic injection molding services. High-quality tools provide more than just reliability; they also enhance precision during manufacturing processes which ultimately leads to superior end products at competitive plastic molding prices. This means fewer errors during production runs and less need for costly rework or scrapped materials.
Additionally, premium tools tend to offer better performance across various types of injection casting applications—making them versatile assets for any manufacturing operation focused on growth and innovation within their industry niche. While it might be tempting to cut corners with cheaper options initially, those savings could evaporate quickly if you face frequent repairs or replacements down the line.
In conclusion, when contemplating costs associated with mold plastic injection projects, consider how much you’re willing to invest upfront versus potential long-term gains from high-quality tools that enhance productivity and product consistency over time.
Vendor Expertise and Location
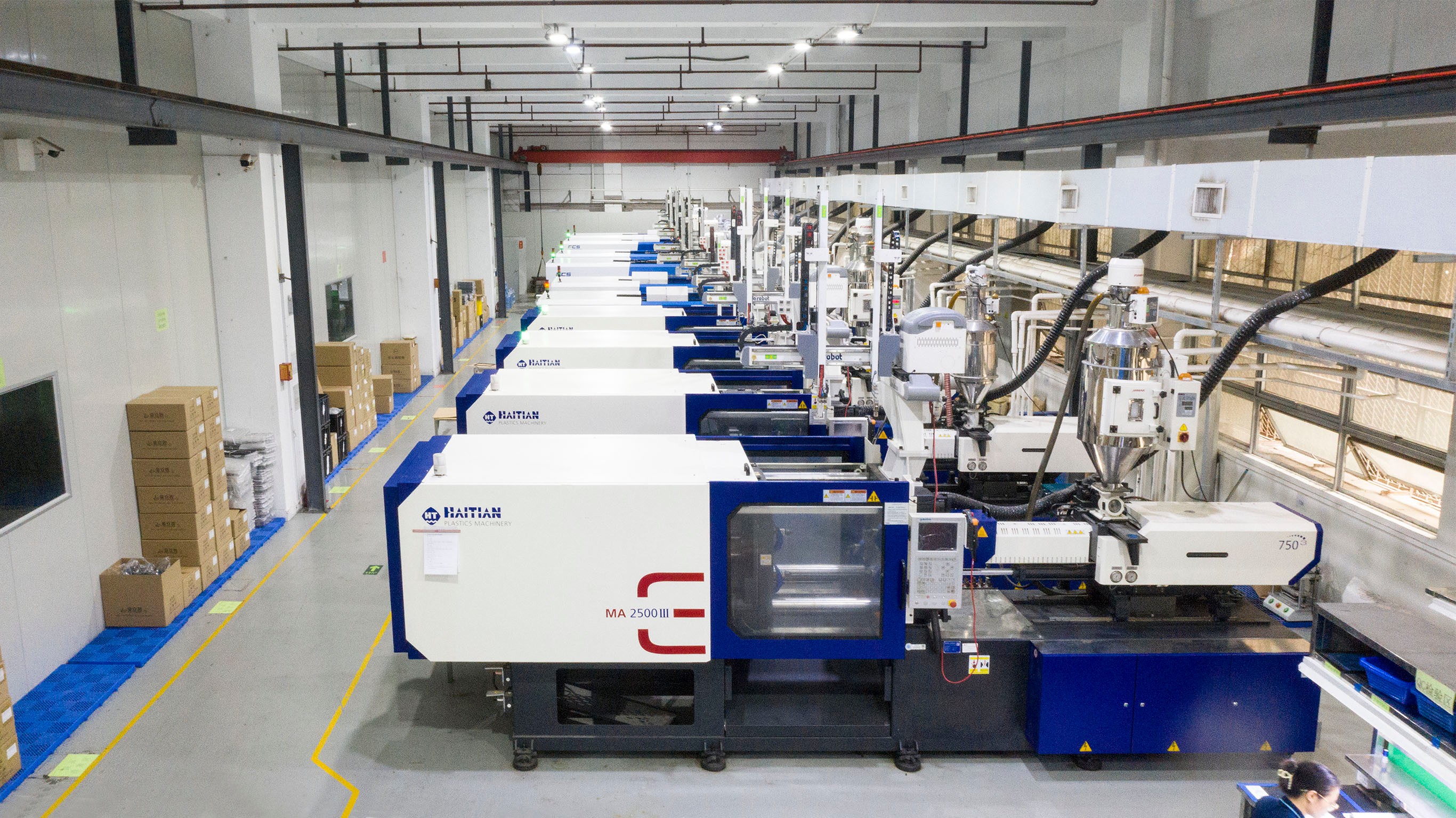
When it comes to plastic molding price, selecting the right plastic injection molding services can make all the difference. Not all vendors are created equal; their expertise, technology, and experience can significantly impact the quality of your product and its overall cost. A well-chosen vendor not only helps in optimizing production processes but also ensures adherence to industry standards, which is crucial for maintaining competitive pricing.
Selecting the Right Plastic Injection Molding Services
Choosing a reliable provider for your injection molding needs involves more than just comparing prices; it's about assessing their capabilities and reputation in the market. Look for companies that specialize in injection moldable plastics relevant to your project requirements, as their specific knowledge can lead to better material selection and design optimization. Additionally, vendor reviews and case studies offer insights into their past performance and reliability—key factors that can influence your final plastic molding price.
Influence of Regional Costs on Price
The geographical location of your chosen plastic injection molding services can greatly affect production costs due to variances in labor rates and operational expenses. For instance, vendors located in regions with a lower cost of living may offer more competitive pricing than those situated in high-cost areas. However, it’s essential to balance cost with logistics; sometimes higher shipping fees from distant vendors could negate any savings on initial pricing.
The Role of Established Companies Like Schmidt
Established companies like Schmidt have built a reputation over decades through consistent quality and service excellence in plastic injection molding. Their experience often translates into more efficient production processes, which can help reduce overall plastic molding price without compromising quality or timelines. Furthermore, established firms typically have access to advanced technologies that enhance precision in injection casting—resulting in superior products tailored to client specifications.
Conclusion
As we wrap up our exploration of plastic molding costs, it’s clear that understanding the various factors influencing plastic molding price is essential for making informed decisions. From material selection to production volume, each aspect plays a critical role in determining overall expenses. By grasping these elements, businesses can navigate the complexities of injection molding with confidence and clarity.
Key Takeaways on Plastic Molding Price
The pricing landscape of plastic injection molding is multifaceted, influenced by everything from the choice of injection moldable plastics to the intricacies of design features. It's vital to remember that while initial costs may seem daunting, effective planning and strategic decision-making can lead to significant long-term savings. Ultimately, knowledge is power; understanding how each factor affects plastic molding price empowers you to optimize your investment.
Making Informed Decisions for Injection Molding
When considering plastic injection molding services, it’s crucial to weigh all options carefully—from selecting the right materials to choosing an experienced vendor who understands your unique needs. Engaging with established companies can provide insights into best practices and innovative solutions that might not be immediately apparent. By prioritizing communication and collaboration with your service provider, you can ensure that your project aligns well with both functionality and budget constraints.
Future Considerations for Mold Plastic Injection Costs
Looking ahead, staying abreast of advancements in technology and material science will be key in managing mold plastic injection costs effectively. Innovations such as improved recycling methods or alternative materials could reshape cost structures in unexpected ways. As industries evolve and demand fluctuates, being adaptable and proactive will help businesses remain competitive while keeping a close eye on their plastic molding price.