Introduction
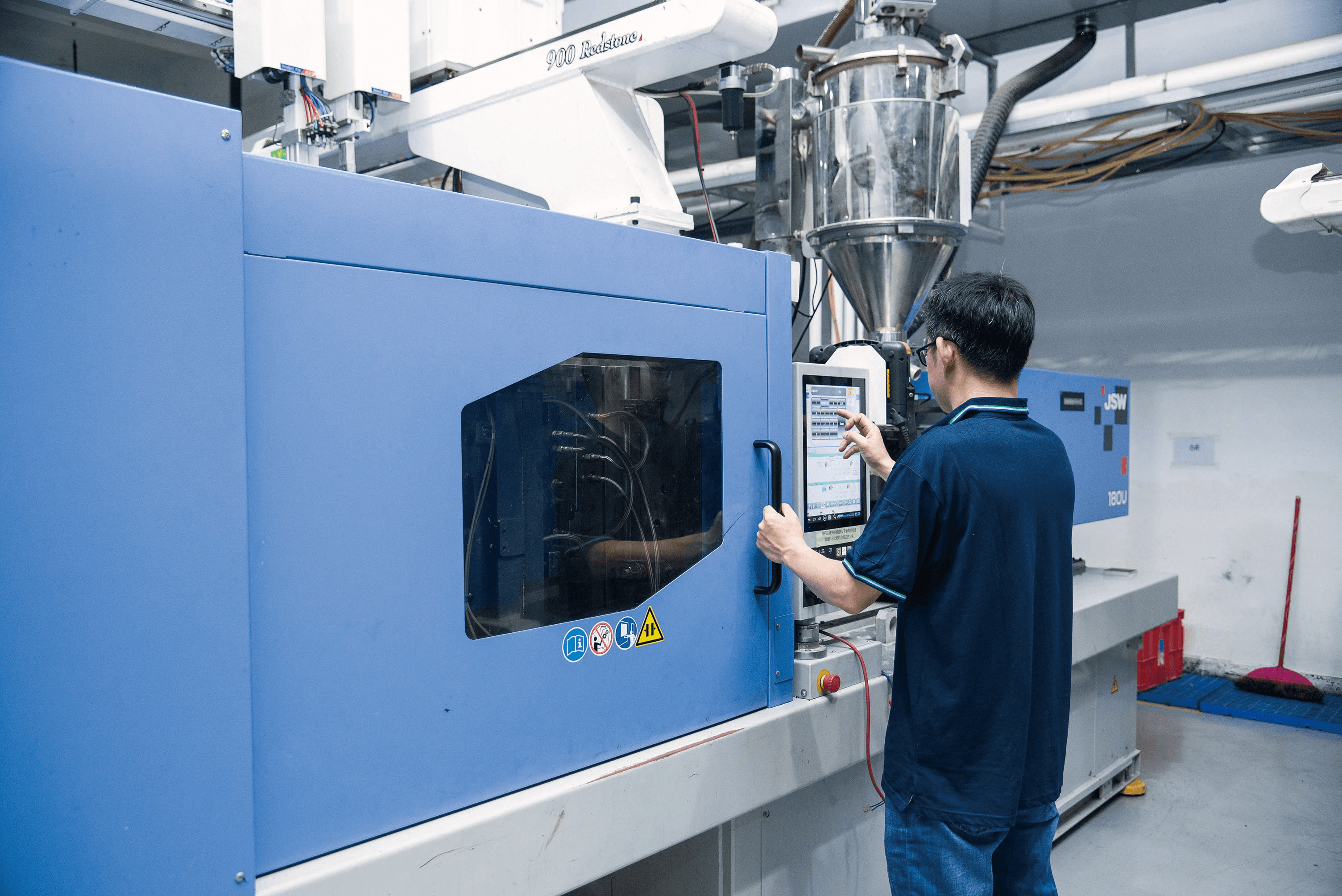
Injection molding is a fascinating process that transforms raw materials into intricate shapes, and at the heart of this operation lies the injection molding lifter. These components play a crucial role in ensuring that complex designs can be manufactured with precision and efficiency. Understanding how lifters function, their differences from slides, and their impact on overall product quality is essential for anyone involved in injection molding.
Understanding Injection Molding Lifters
So, what is a lifter in injection molding? Simply put, it's a mechanism that helps eject parts from molds by lifting them away from the mold surface during the demolding phase. This action prevents potential damage to delicate features of the molded parts and ensures smooth production runs. By grasping the fundamental concept of injection molding lifters, manufacturers can optimize their processes for better results.
Importance of Lifters for Optimal Results
The importance of lifters for optimal results cannot be overstated; they are pivotal in achieving high-quality products while minimizing defects. Without effective lifters, intricate designs may not release properly from the mold, leading to costly reworks or scrap material. Therefore, understanding what is the function of a lifter in casting becomes vital—it's all about ensuring that each piece meets design specifications without compromising integrity.
Key Techniques for Enhanced Performance
To maximize efficiency and quality in production, employing key techniques related to injection molding lifters is essential. This includes understanding what is the clearance of injection molding lifters; proper clearance ensures that parts are ejected smoothly without damaging either the part or the mold itself. Additionally, familiarizing oneself with best practices can significantly enhance performance and lead to more successful manufacturing outcomes.
What is a Lifter in Injection Molding?
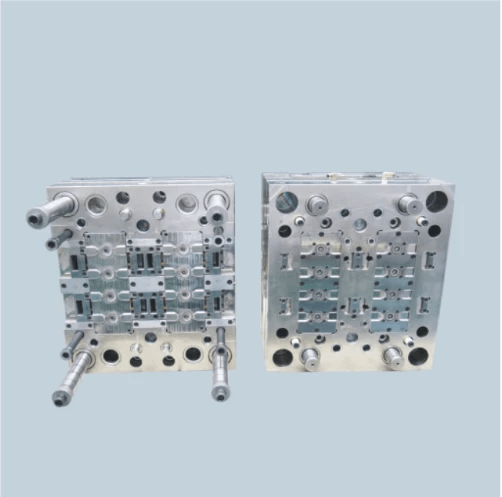
Injection molding lifters are essential components that aid in the production of complex parts with undercuts or intricate geometries. They play a crucial role in the ejection process, ensuring that molded parts can be removed from the mold without damage. Understanding what a lifter in injection molding is and its significance can greatly enhance manufacturing efficiency.
Definition and Purpose of Lifters
A lifter in injection molding is a mechanical device designed to assist in the removal of molded parts from their molds, particularly when dealing with features that would otherwise trap the part inside. Essentially, these lifters pivot or slide to create an upward force on the molded piece, allowing it to clear any obstructions during ejection. This function is vital for maintaining part integrity and achieving high-quality outputs.
Real-World Applications in Manufacturing
In manufacturing, injection molding lifters find applications across various industries, including automotive, consumer goods, and electronics. For instance, they are often used to produce components like gear housings and intricate enclosures which require precise detailing and undercuts. Their ability to facilitate complex designs makes them invaluable for manufacturers looking to push the boundaries of product innovation.
Insights from the Baoyuan Team
The Baoyuan team emphasizes that understanding what is the difference between lifter and slide in injection molding can significantly impact design choices. While both components serve unique functions—lifter primarily assists with vertical motion during ejection while slides facilitate lateral movement—they work together harmoniously for optimal results. The team advocates for careful consideration of both elements during design phases to maximize efficiency and quality.
Difference Between Lifters and Slides
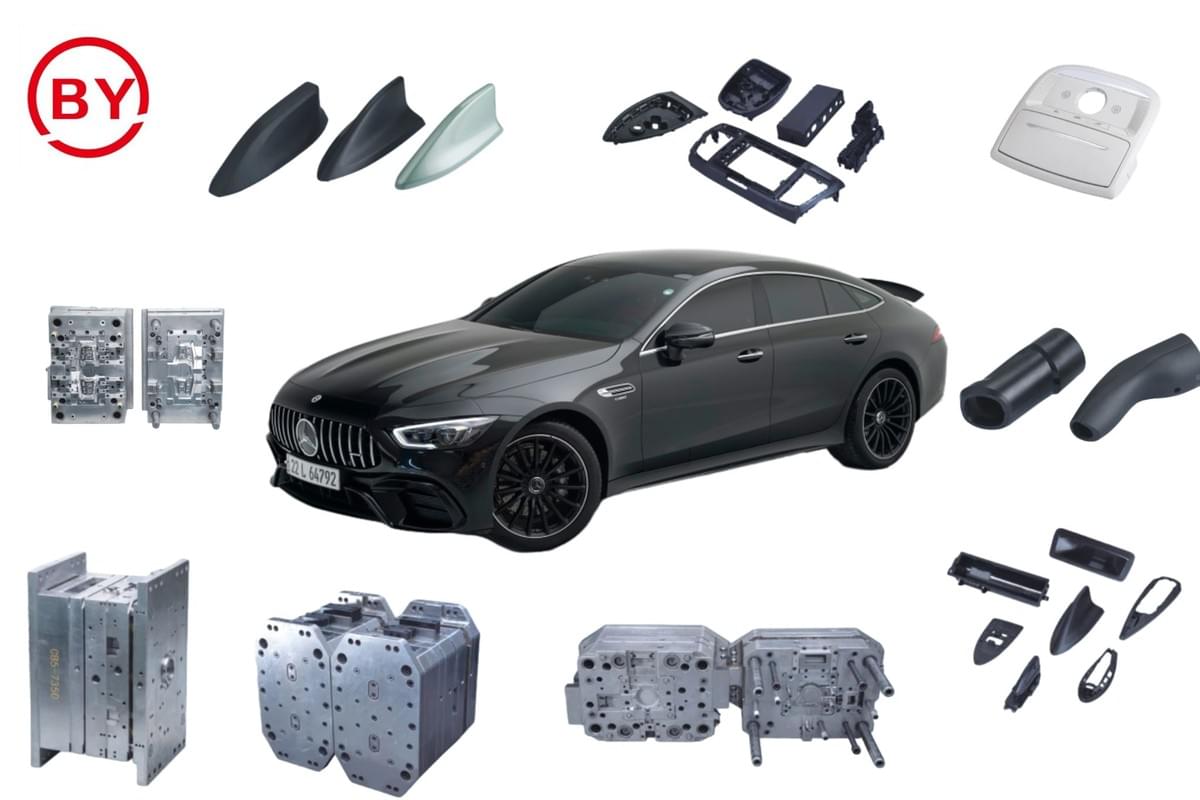
In the world of injection molding, understanding the difference between lifters and slides is crucial for achieving optimal results. Both components serve unique functions that are essential to the molding process, yet they operate quite differently. Recognizing these distinctions can significantly influence product design and manufacturing efficiency.
Unique Functions of Each Component
When we ask, What is a lifter in injection molding? we find that lifters are primarily designed to assist in ejecting parts from the mold by lifting them out of undercuts or complex geometries. In contrast, slides are used to create side actions, allowing for features like grooves or slots on the part without compromising its integrity during ejection. While both components facilitate part removal, their specific roles highlight how they contribute uniquely to the overall efficiency of the injection molding process.
How They Impact Product Design
The question of What is the difference between lifter and slide in injection molding? revolves around their impact on product design flexibility and complexity. Lifters often allow for more intricate designs by enabling undercuts that would otherwise be impossible with just standard ejection methods. Conversely, slides can introduce additional challenges such as increased cycle times and potential wear issues; thus, designers must carefully consider which component best fits their needs when crafting a product.
Industry Examples for Clarity
To illustrate these differences further, let's look at some industry examples where lifters and slides play pivotal roles in production. In automotive manufacturing, lifters might be used to create complex interior components with undercuts that enhance aesthetics while maintaining functionality. On the other hand, slides could be employed in consumer electronics to create sleek designs with precise grooves or openings required for assembly—showcasing how each component fulfills distinct needs within various sectors.
Function of Lifters in Casting

Injection molding lifters play a pivotal role in ensuring the smooth flow of materials during the casting process. These components are designed to provide necessary support and guidance for the molten material as it fills the mold cavity, facilitating an even distribution that is crucial for achieving precise shapes and dimensions. Without effective lifters, manufacturers could encounter significant issues, such as incomplete filling or uneven cooling, leading to defects in the final product.
Lifter Roles in Material Flow
When we ask, What is the function of lifter in casting? we're really delving into how these tools manage material flow throughout the injection molding process. Lifters actively assist in directing molten plastic into complex mold geometries, ensuring that every nook and cranny is filled efficiently. By optimizing this flow, injection molding lifters help reduce cycle times and improve overall production efficiency.
Ensuring Quality in Final Products
Quality assurance is a top priority for manufacturers utilizing injection molding lifters. By enabling proper material flow and minimizing defects during the casting stage, lifters contribute significantly to maintaining high standards in product quality. When considering What is a lifter in injection molding?, one must acknowledge its critical function: not only does it shape products but also enhances their durability and performance.
Case Studies on Successful Implementations
Looking at industry examples can shed light on how effective injection molding lifters can transform production outcomes. For instance, a leading automotive parts manufacturer implemented advanced lifter designs that improved their casting efficiency by 30%. This change not only optimized their workflow but also reduced waste—demonstrating how understanding What is the difference between lifter and slide in injection molding? can lead to smarter design choices that enhance overall manufacturing processes.
Clearance in Injection Molding Lifters
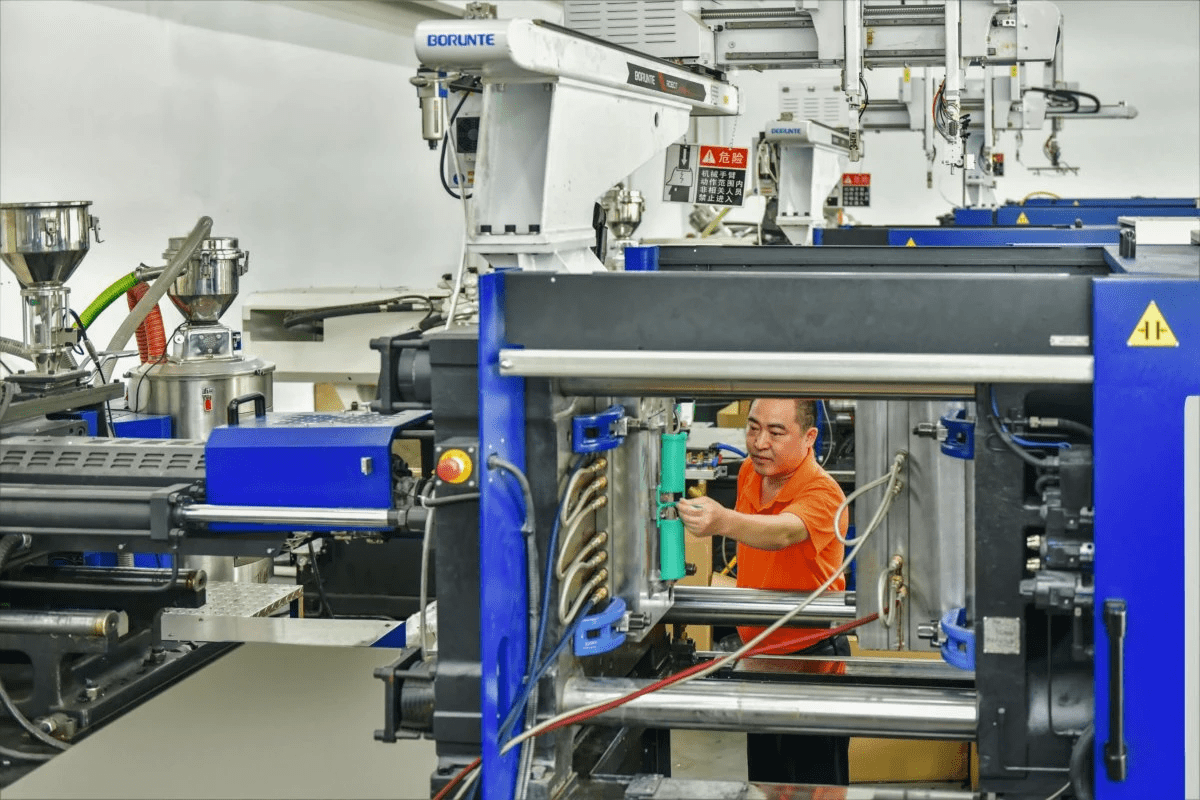
When it comes to injection molding lifters, clearance is a crucial factor that can significantly impact the efficiency and quality of the molding process. Understanding what is the clearance of injection molding lifters helps manufacturers design components that work seamlessly together. Proper clearance ensures that lifters can operate without obstruction, allowing for smooth ejection of parts and reducing wear on machinery.
Defining Clearance Needs
Defining clearance needs in injection molding lifters involves understanding the specific requirements based on part geometry and material properties. The term clearance refers to the space between moving parts, which must be meticulously calculated to avoid interference during operation. If you’re asking yourself, “What is a lifter in injection molding?” remember that these components need just the right amount of space to function effectively without compromising part integrity.
Effects on Part Quality and Performance
The effects of improper clearance on part quality and performance can be detrimental, leading to defects such as warping or incomplete fills. When considering what is the function of a lifter in casting, one must recognize that insufficient clearance can hinder material flow and affect surface finish negatively. Achieving optimal clearance not only enhances product quality but also contributes to overall efficiency in production processes involving injection molding lifters.
Tips from Experts on Optimizing Clearance
To optimize clearance in injection molding lifters, experts recommend conducting thorough simulations during the design phase to identify potential issues before they arise in production. Adjusting tolerances based on real-world testing can provide valuable insights into what works best for your specific application—after all, what is the difference between a successful mold and one riddled with flaws? Regular maintenance checks are also essential; ensuring that your equipment remains calibrated will help maintain those critical clearances needed for flawless operation.
Best Practices for Injection Molding Lifters
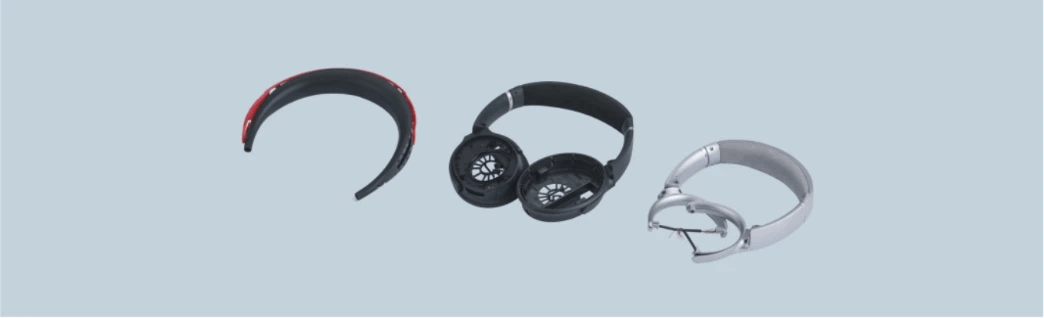
When it comes to optimizing injection molding lifters, understanding the nuances can make all the difference. The design of an injection molding lifter is critical not only for functionality but also for ensuring the final product meets quality standards. By adhering to best practices, manufacturers can enhance performance and reduce defects in their molded parts.
Design Considerations for Lifters
Designing effective injection molding lifters requires careful consideration of several factors. First, it’s crucial to determine what is a lifter in injection molding and how its geometry will affect material flow and ejection. Additionally, incorporating adequate clearance of injection molding lifters is vital; insufficient clearance can lead to sticking or damage during operation, while excessive clearance may compromise precision.
Another key design consideration involves the materials used for the lifter itself. Selecting durable materials that withstand wear and tear ensures longevity and consistent performance over time. Ultimately, a well-thought-out design that incorporates these elements will help achieve optimal results in production.
Common Mistakes to Avoid
Despite their importance, many manufacturers fall prey to common mistakes when working with injection molding lifters. One frequent error is neglecting the difference between lifter and slide in injection molding; while both assist in part ejection, they serve distinct roles that should not be confused during design or implementation phases. Understanding these differences can significantly impact overall product design efficiency.
Another mistake is overlooking the function of a lifter in casting processes; failing to account for how it influences material flow can lead to defects or inconsistencies in molded parts. Additionally, improper clearance settings are often ignored until problems arise—this oversight can be costly both in terms of time and resources.
Pro Tips from the Baoyuan Team
The Baoyuan team has gathered valuable insights over years of experience with injection molding lifters that can help streamline your processes. For starters, always conduct thorough simulations before finalizing your designs; this allows you to visualize how your lifting mechanisms interact with other components under various conditions. Remember: what is the clearance of injection molding lifters matters greatly—aim for just enough space to avoid friction without compromising structural integrity.
Moreover, consider regular maintenance checks as part of your production schedule; preventative measures can save you from unexpected downtimes caused by worn-out components or misalignments over time. Lastly, keep an open line of communication with your engineering team; sharing knowledge about what works best will foster continuous improvement across all stages of production.
Conclusion
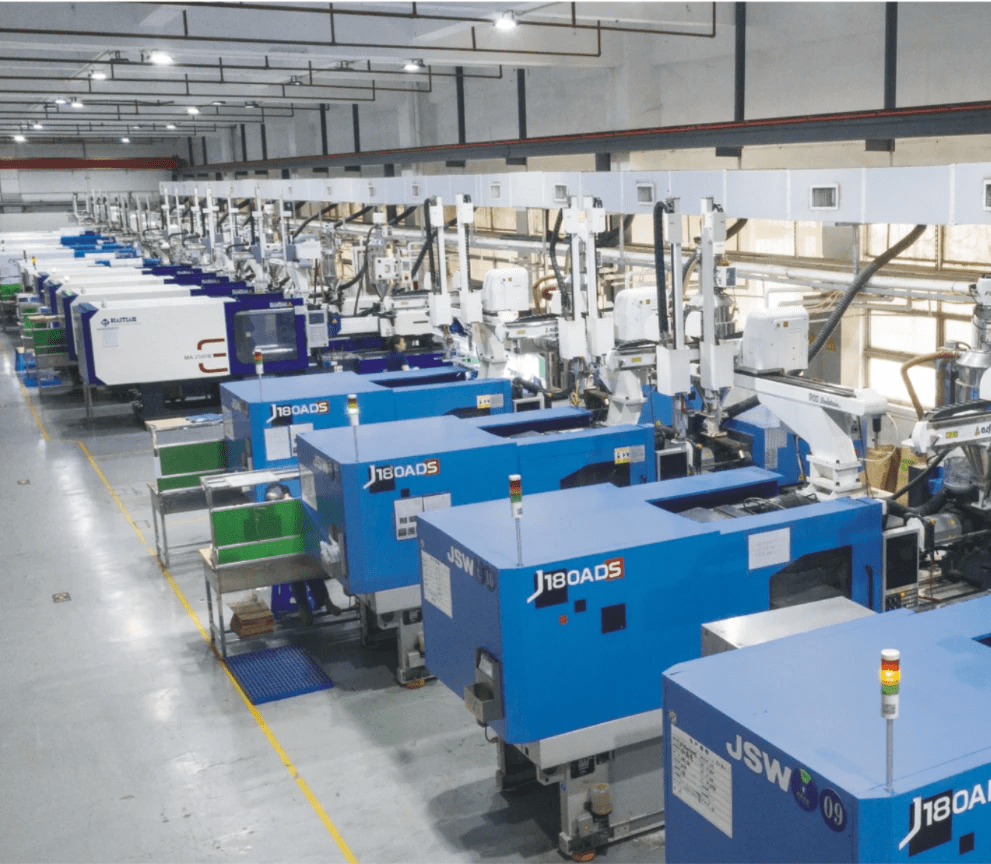
In the fast-paced world of manufacturing, mastering injection molding lifters is crucial for achieving optimal results. Understanding their role and functionality can be the difference between a mediocre product and one that stands out in quality and precision. By leveraging the insights shared throughout this guide, manufacturers can enhance their processes and achieve greater efficiency.
Mastering Lifter Techniques for Success
To truly master lifter techniques in injection molding, one must first grasp what a lifter in injection molding is designed to do. Lifters play a vital role in ensuring that complex geometries are produced accurately while facilitating the removal of parts from molds without damage. Implementing best practices such as proper clearance adjustments and thoughtful design considerations can significantly improve production outcomes, making it essential for manufacturers to refine their approach continually.
The difference between lifters and slides in injection molding also plays into mastering these techniques; while both components assist with part ejection, understanding their unique functions allows for better integration into product designs. Lifters are primarily used to create undercuts or intricate features, whereas slides provide lateral movement during ejection. By recognizing these distinctions, manufacturers can optimize their designs for enhanced performance and efficiency.
Future Trends in Lifter Technology
Looking ahead, future trends in lifter technology promise exciting advancements that could revolutionize injection molding practices. Innovations such as smart lifters equipped with sensors may soon enable real-time monitoring of performance metrics like clearance levels and material flow dynamics—essentially answering the question: what is the clearance of injection molding lifters? This data-driven approach will empower manufacturers to make informed decisions that elevate product quality.
Moreover, advancements in materials used for lifters may lead to increased durability while reducing friction during operation—addressing concerns about wear over time. As industries continue to demand more complex shapes and higher precision, new technologies will likely emerge that further blur the lines between traditional lifting mechanisms and cutting-edge automation solutions.
Final Thoughts on Injection Molding Efficiency
In conclusion, enhancing injection molding efficiency hinges on a comprehensive understanding of all components involved—including injection molding lifters. By addressing questions like what is the function of a lifter in casting? or what is the difference between a lifter and slide in injection molding?, professionals can create products that not only meet specifications but exceed expectations.
Ultimately, investing time into mastering these techniques will yield significant returns through improved quality control and streamlined processes—ensuring your place at the forefront of manufacturing innovation.