Introduction
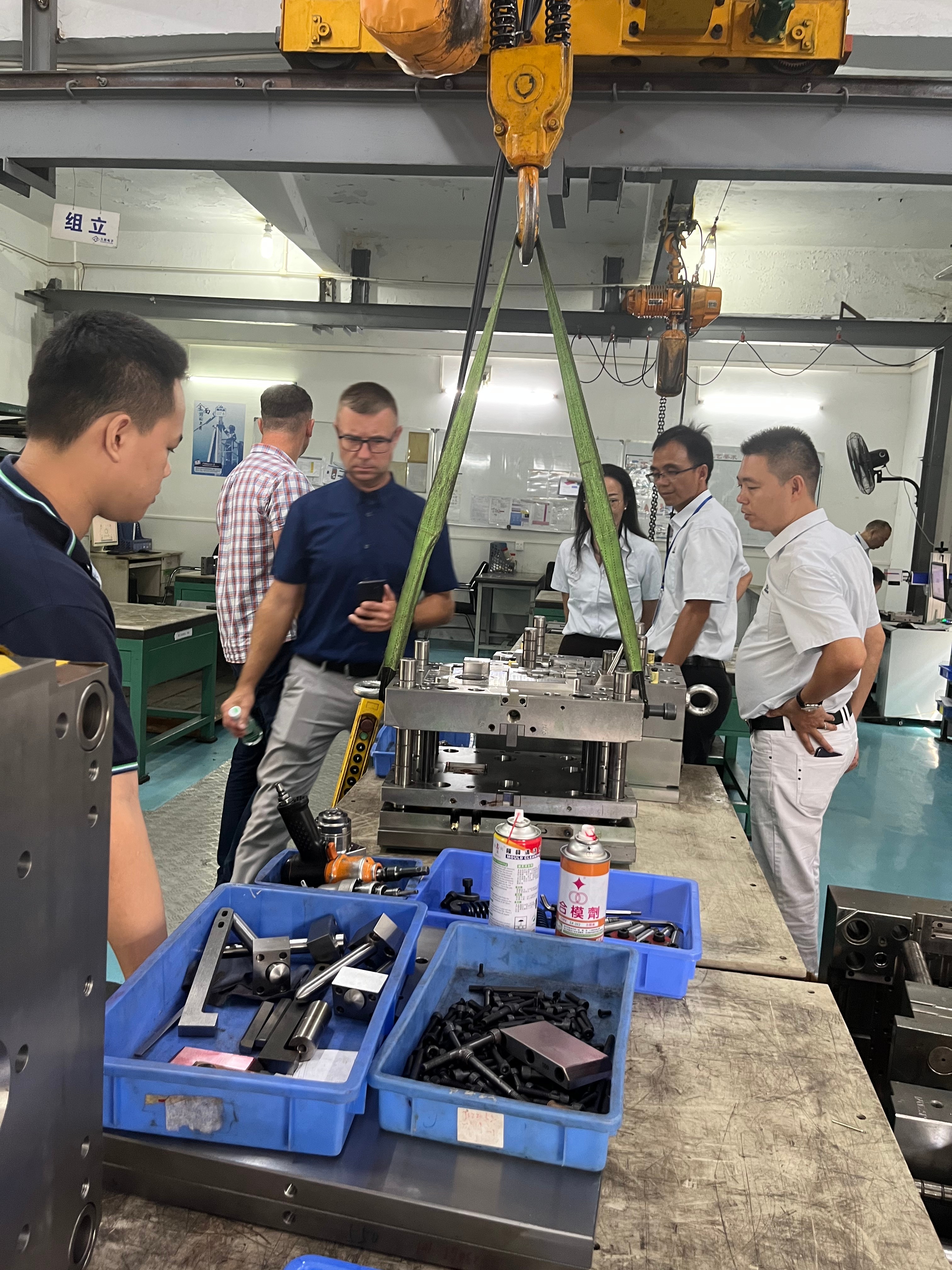
In the world of manufacturing, understanding urethane injection molding is essential for creating high-quality products efficiently. This process involves injecting a liquid urethane mixture into a mold, where it solidifies into the desired shape. With its growing popularity, many ask, Can you injection mold urethane? The answer is a resounding yes, and this guide will explore how this versatile technique works.
Understanding Urethane Injection Molding
So, what is urethane molding? It’s a manufacturing process that utilizes polyurethane materials to create durable and flexible components. The urethane injection molding process allows for intricate designs and precise dimensions, making it ideal for various applications across industries such as automotive, medical devices, and consumer goods.
Key Applications for Urethane Casting
Urethane casting finds its niche in producing prototypes and low-volume parts with exceptional detail. From custom seals to impact-resistant housings, the versatility of urethane makes it invaluable in sectors like aerospace and electronics. When comparing What is the difference between urethane casting and injection molding?, it's clear that each method serves specific needs based on production volume and design complexity.
The Need for a DFM Guide
Designing for manufacturability (DFM) is crucial when working with urethane injection molding kits or any other production methods involving complex materials like polyurethane. A DFM guide helps streamline the design process to ensure optimal efficiency while minimizing costs associated with the urethane injection molding price. By understanding these principles early on, manufacturers can avoid common pitfalls in production and achieve superior results.
What is Urethane Molding?
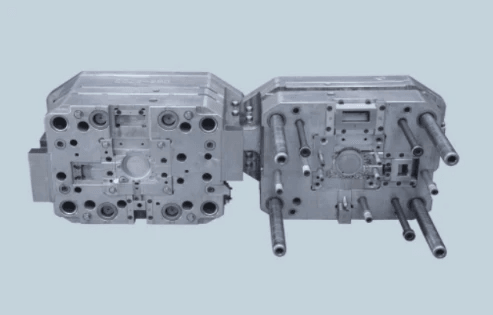
Urethane molding is a versatile manufacturing process that utilizes urethane materials to create durable and precise components. This technique can take various forms, including urethane injection molding and urethane casting, each serving different applications and industries. Understanding what urethane molding entails is crucial for businesses looking to optimize their production methods.
Definition and Overview
So, what is urethane molding? At its core, it involves shaping liquid polyurethane into solid objects through either injection or casting methods. Urethane injection molding uses high pressure to inject the liquid material into molds, while urethane casting typically involves pouring the material into a mold without pressure. Both processes yield strong, lightweight products suitable for a range of applications.
Common Materials Used
In the world of urethane molding, several materials stand out as favorites among manufacturers. Polyurethane elastomers are commonly used due to their excellent flexibility and resilience; they come in various hardness levels to suit specific needs. Additionally, fillers such as fiberglass or carbon black can be added to enhance properties like strength or thermal stability in the final product.
Benefits of Urethane Molding
The benefits of urethane molding are impressive and worth noting for anyone considering this method for their next project. First off, the speed and efficiency of the urethane injection molding process allow for rapid production cycles—perfect for meeting tight deadlines! Moreover, products made from urethane exhibit high durability and resistance to wear, making them ideal for both industrial and consumer applications.
The Urethane Injection Molding Process
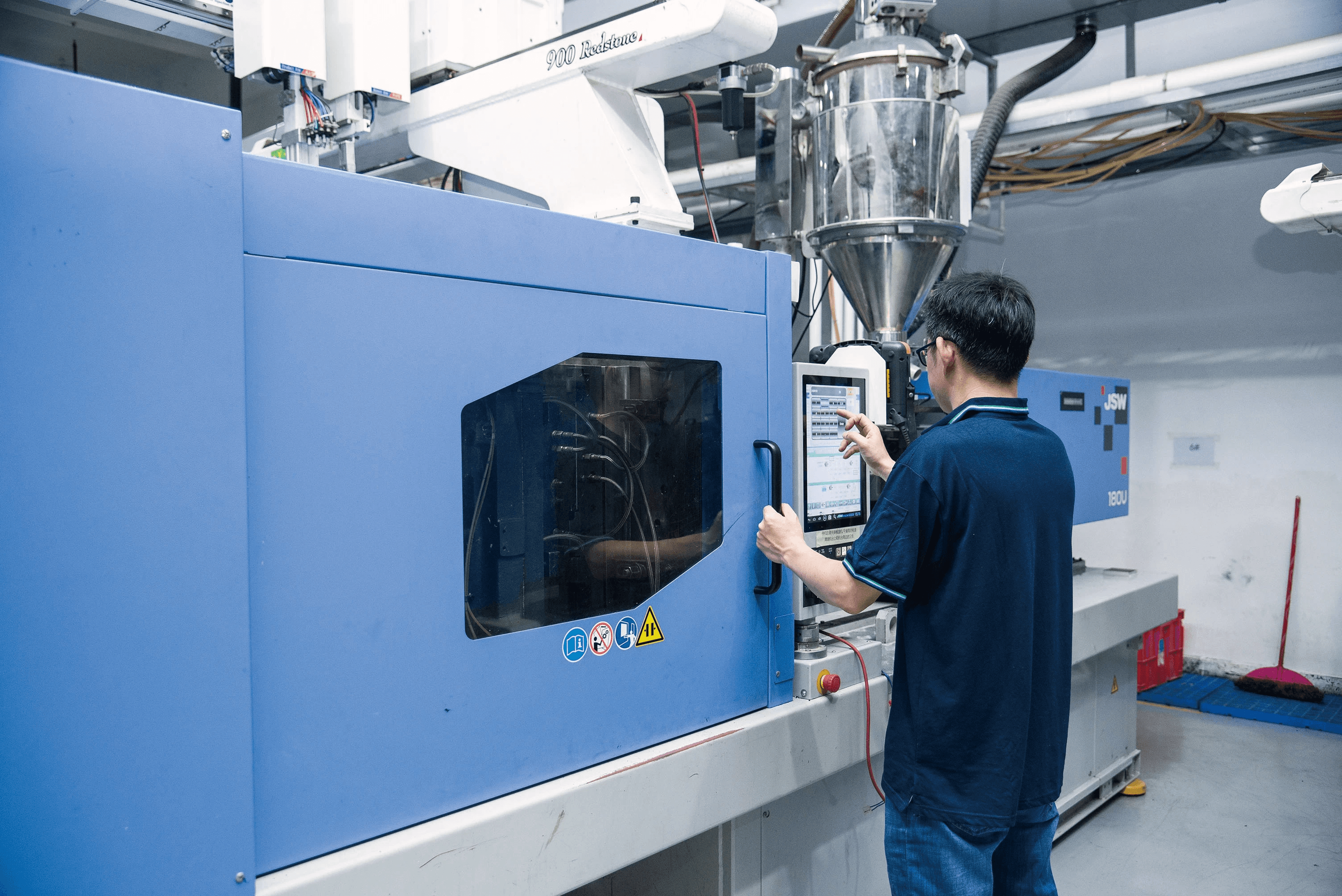
Urethane injection molding is a fascinating blend of science and art, where raw materials transform into intricate designs. Understanding the urethane injection molding process is crucial for anyone looking to harness its potential. From initial preparation to final production, each step plays a vital role in achieving high-quality results.
Steps Involved in Injection Molding
The process of injection urethane begins with the preparation of the mold, which must be designed with precision to accommodate the desired final product. Once the mold is ready, liquid urethane is heated and injected under pressure into it, filling every nook and cranny. After allowing sufficient time for curing, the mold opens to reveal perfectly formed parts ready for use or further processing.
Can you injection mold urethane? Absolutely! This method allows for rapid production cycles and can create complex shapes that would be difficult or impossible with traditional methods. The ability to produce high volumes efficiently makes urethane injection molding a popular choice across various industries.
Tools Required for Injection Molding
To execute a successful urethane injection molding process, several tools are essential. First and foremost is the injection molding machine itself, which applies pressure to inject heated urethane into molds. Additionally, you'll need temperature control systems to monitor and maintain optimal conditions during production.
Other vital tools include mixing equipment for combining different components of urethane and molds made from durable materials like aluminum or steel. For those interested in getting hands-on, a urethane injection molding kit can be an excellent way to start experimenting on a smaller scale without diving headfirst into large-scale operations.
Insights from the Baoyuan Team
The Baoyuan team has extensive experience in implementing effective strategies for successful urethane injection molding projects. Their insights emphasize the importance of meticulous planning at every stage of production—from selecting materials to designing molds that ensure minimal waste and maximum efficiency. They also highlight how understanding what is the difference between urethane casting and injection molding can lead businesses toward more informed decisions regarding their manufacturing processes.
With their expertise, they encourage businesses not only to consider cost implications but also quality assurance throughout the entire production cycle—after all, ensuring high standards will save money in rework down the line! By leveraging these insights from seasoned professionals like Baoyuan’s team, companies can navigate challenges effectively while maximizing their return on investment related to urethane injection molding price considerations.
Urethane Casting vs. Injection Molding
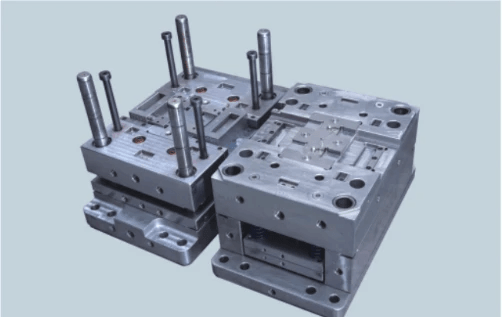
When it comes to choosing between urethane casting and injection molding, the decision often boils down to specific project requirements and production needs. Both methods have their unique advantages, but understanding what is urethane molding can help clarify your options. While urethane casting is often favored for smaller, less complex parts, urethane injection molding shines in high-volume production scenarios.
Comparing Production Methods
The first thing to note is how these two processes differ fundamentally. Urethane casting typically involves pouring liquid urethane into a mold, allowing it to cure before removal, which can be great for prototyping or low-volume runs. In contrast, the urethane injection molding process uses high pressure to inject heated liquid urethane into a mold cavity, making it ideal for mass production where consistency and speed are crucial.
Can you injection mold urethane? Absolutely! This technique allows for intricate designs and tight tolerances that might be challenging with casting methods. The choice between these two production methods ultimately hinges on factors like volume, complexity, and material properties desired in the final product.
Cost Implications: Urethane Injection Molding Price
Cost is often a significant factor when deciding between urethane casting and injection molding. Generally speaking, the initial investment for a urethane injection molding kit can be higher due to the tooling costs associated with creating molds that withstand high pressures and temperatures. However, this upfront cost can pay off quickly in large-scale production runs where per-unit costs drop significantly as volume increases.
It's essential to evaluate not just the immediate expenses but also long-term savings when considering the price of urethane injection molding versus casting methods. While you might spend more initially on equipment and molds for injection molding, those costs could be offset by reduced labor time and increased efficiency down the line.
Quality Considerations
Quality considerations are paramount when selecting between these two processes as well. Urethane injection molding tends to produce parts with superior surface finishes and dimensional accuracy compared to traditional casting methods due to its ability to control pressure during the process effectively. This precision makes it easier to meet stringent quality standards required in industries like automotive or aerospace.
On the flip side, while urethanes cast using traditional techniques may not achieve quite the same level of detail or finish quality as their molded counterparts, they still offer excellent mechanical properties suitable for various applications. Ultimately, your choice should align with your project's specific quality requirements—knowing what is the difference between urethane casting and injection molding will guide you toward making an informed decision.
Advantages of Urethane Injection Molding
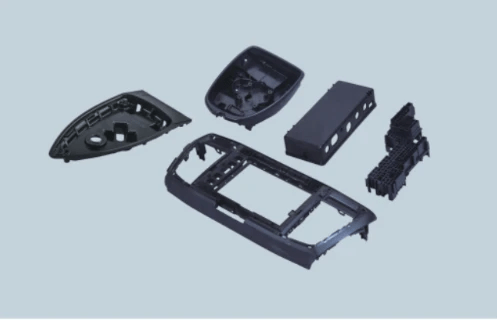
Urethane injection molding offers a plethora of advantages that make it a go-to choice for manufacturers across various industries. From its remarkable speed and efficiency to the precision it can achieve, this process stands out in the world of manufacturing. Moreover, the versatility in applications makes urethane injection molding a reliable option for diverse projects.
Speed and Efficiency
One of the standout features of urethane injection molding is its speed and efficiency. The urethane injection molding process allows for rapid production runs, meaning you can get your products to market faster than with many other methods. When considering how quickly you can scale up production, it's no wonder businesses often ask, Can you injection mold urethane? The answer is a resounding yes!
Efficiency doesn't just stop at production speed; it also encompasses resource management. With the right urethane injection molding kit, manufacturers can minimize waste while maximizing output, making it an economically savvy choice. In an era where time is money, investing in urethane injection molding can provide substantial returns.
Precision in Production
Precision is crucial when creating components that must fit perfectly or perform reliably under stress. Urethane injection molding excels in this area by providing tight tolerances that ensure consistency across batches. This high level of precision answers the question: What is the process of injecting urethane? It involves carefully controlled parameters that yield parts with exact specifications every time.
Moreover, advancements in technology have further enhanced precision capabilities within the urethane injection molding process. Manufacturers now have access to sophisticated machinery and software that fine-tune each step for optimal results. This means less rework and fewer defects—an essential factor when considering quality assurance.
Versatility in Applications
The versatility offered by urethane injection molding is another significant advantage worth noting. Whether you're producing automotive parts, medical devices, or consumer goods, this method adapts well to numerous industries and applications. Many people often wonder about What is the difference between urethane casting and injection molding? While both processes utilize similar materials, their applications vary widely based on desired outcomes.
Urethane's inherent properties allow it to be formulated for specific performance characteristics such as flexibility or hardness—ideal for customized solutions tailored to unique project needs. This adaptability ensures that whether you're looking at high-volume production or intricate designs requiring finesse, urethane injection molding has got you covered!
In conclusion, choosing urethane injection molding not only enhances your production capabilities but also opens doors to innovative possibilities across various sectors.
Challenges in Urethane Molding
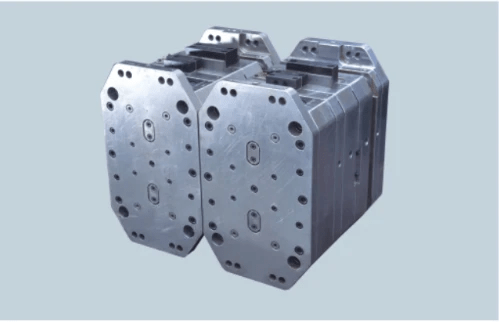
While urethane injection molding offers many benefits, it isn't without its challenges. Understanding these pitfalls is crucial for achieving high-quality results. By addressing common issues and implementing effective solutions, manufacturers can optimize the urethane injection molding process and enhance product quality.
Common Pitfalls in the Process
One of the most frequent questions is, Can you injection mold urethane? The answer is a resounding yes, but not without some hurdles along the way. Common pitfalls include improper material selection, which can lead to defects or compromised performance; inadequate mold design that affects part quality; and insufficient temperature control during the urethane injection molding process that may cause incomplete curing or warping.
Another common issue arises from insufficient knowledge about what is urethane molding? This lack of understanding can result in poor execution of the process and ultimately lead to unsatisfactory products. Additionally, failing to conduct thorough testing before production can expose manufacturers to costly errors down the line.
Addressing Quality Assurance
Quality assurance is paramount when it comes to urethane injection molding. Manufacturers need to establish rigorous testing protocols throughout the production cycle to ensure that each component meets stringent standards. This includes evaluating both raw materials and finished products for consistency in performance and appearance.
Understanding what is the difference between urethane casting and injection molding also plays a role in quality assurance; different methods necessitate different checks for defects or inconsistencies. Implementing a comprehensive quality management system helps identify potential problems early on, allowing for timely intervention before they escalate into larger issues.
Moreover, regular training for staff involved in the process ensures everyone understands best practices related to both quality assurance and product specifications. This proactive approach minimizes risks associated with human error while enhancing overall production efficiency.
Solutions for Effective Implementation
To successfully navigate challenges in urethane molding, manufacturers should invest in a reliable urethane injection molding kit tailored to their specific needs. These kits often come with detailed instructions that guide users through each step of what is the process of injection urethane? From material preparation to final inspection, having a structured approach greatly reduces errors.
Additionally, leveraging technology such as computer-aided design (CAD) software helps streamline mold design and enhances precision during production processes—this not only saves time but also reduces costs associated with rework due to defects caused by poor designs or miscalculations.
Finally, keeping an eye on market trends regarding urethane injection molding price will help businesses make informed decisions about their investments while ensuring they remain competitive within their industry landscape. By addressing these challenges head-on with effective solutions, companies can achieve remarkable success with their projects involving this versatile manufacturing technique.
Conclusion
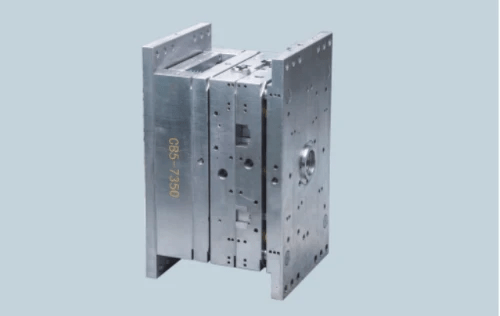
In wrapping up our exploration of urethane injection molding, it's clear that this process offers significant advantages for various applications. Whether you’re looking to create durable parts or intricate designs, understanding the nuances of urethane molding can be pivotal for your project's success. So, is urethane injection molding the right fit for you? Let’s dive into some key considerations.
The Right Choice for Your Project
When deciding if urethane injection molding is suitable for your project, consider the specific requirements of your application. Urethane molding provides remarkable flexibility in design and material properties, making it ideal for both prototypes and high-volume production runs. If you're pondering Can you injection mold urethane? the answer is a resounding yes; this method allows for precise control over product characteristics while maintaining cost-effectiveness.
Evaluating Cost vs. Benefit
Cost considerations are always at the forefront when choosing a manufacturing method. While the initial investment in a urethane injection molding kit may seem steep, it’s essential to evaluate long-term benefits against upfront costs. Understanding What is the difference between urethane casting and injection molding? can help clarify why many industries lean towards injection molding despite potentially higher prices—it's all about efficiency and quality assurance over time.
Future Trends in Urethane Molding
Looking ahead, we can expect exciting developments in the field of urethane injection molding that will further enhance its capabilities. Innovations in materials and processes will likely lead to even faster production times and improved precision in complex designs. As industries continue to evolve, staying informed about these trends will be crucial for those invested in maximizing their use of urethane molding techniques.