Introduction
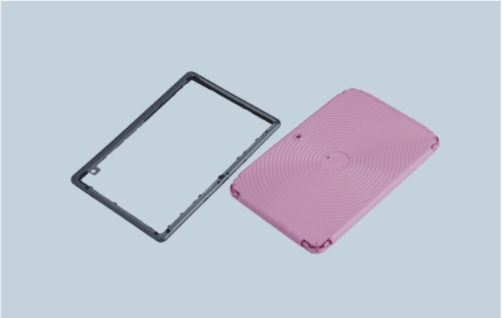
In the world of manufacturing, the terms overmolding and insert molding frequently come up, often leaving many wondering, What does overmolding mean? These techniques are pivotal in creating durable and functional products across various industries. Understanding these processes helps in making informed decisions about material choices and applications.
Understanding Overmolding and Insert Molding
Overmolding refers to a specialized process where one material is molded over another, resulting in a single part that combines different properties. This technique enhances grip, adds color, or provides a softer touch to hard components. On the other hand, insert molding involves placing pre-formed parts into a mold before injecting plastic around them—what is the difference between overmolding and insert molding? Both methods aim to improve product functionality but differ significantly in their processes.
Importance of Material Choices
When considering the overmolding process, selecting the right materials is crucial for achieving desired performance characteristics. Different materials can affect durability, flexibility, and aesthetic appeal—factors that play significant roles in product success. For instance, using silicone for overmolding can enhance grip on tools while also providing resistance against various environmental factors.
Applications in Different Industries
Overmolding examples abound across multiple sectors—from consumer electronics with soft-touch grips to medical devices requiring biocompatible materials. The automotive industry also benefits significantly from these techniques by integrating components that require both strength and comfort—a perfect case of what does it mean to mold over? Ultimately, understanding how these methods apply across different industries can illuminate their importance in modern manufacturing practices.
What is Overmolding?
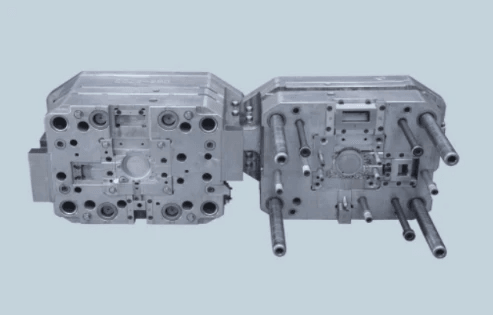
Overmolding is a fascinating manufacturing technique that enhances the functionality and aesthetics of products by combining two different materials into a single component. But what does overmolding mean in practical terms? Essentially, it involves molding one material over another, creating a bond that can improve grip, provide insulation, or add color. The overmolding process typically starts with an initial part being created through injection molding, followed by the application of a second layer of material to achieve the desired properties.
Definition and Process of Overmolding
The definition of overmolding revolves around its ability to layer materials for enhanced performance. In this process, manufacturers first create a base part using injection molding. Once this initial component cools and solidifies, it is placed in the mold again where a second material is injected to form an outer layer—hence the term to mold over. This method not only improves product functionality but also opens up creative avenues for design.
Advantages of Overmolding
One major advantage of overmolding lies in its ability to create durable and ergonomic products that are often more appealing to consumers. By combining materials like hard plastics with softer elastomers, manufacturers can produce items that are both sturdy and comfortable to handle—think smartphone cases or tool grips! Additionally, overmolding allows for better sealing against moisture and dust, making it ideal for applications in various industries such as medical devices or consumer electronics.
Popular Materials Used in Overmolding
When considering what materials are best suited for overmolding, options abound! Commonly used materials include thermoplastics like polycarbonate (PC) for strength and thermoplastic elastomers (TPE) for flexibility and grip. The choice between these materials can significantly affect the final product's performance—this is where understanding what is the difference between 2k molding and overmolding comes into play; 2k molding typically refers to two-component injection processes which may not always involve layering as seen in traditional overmolding examples.
What is Insert Molding?
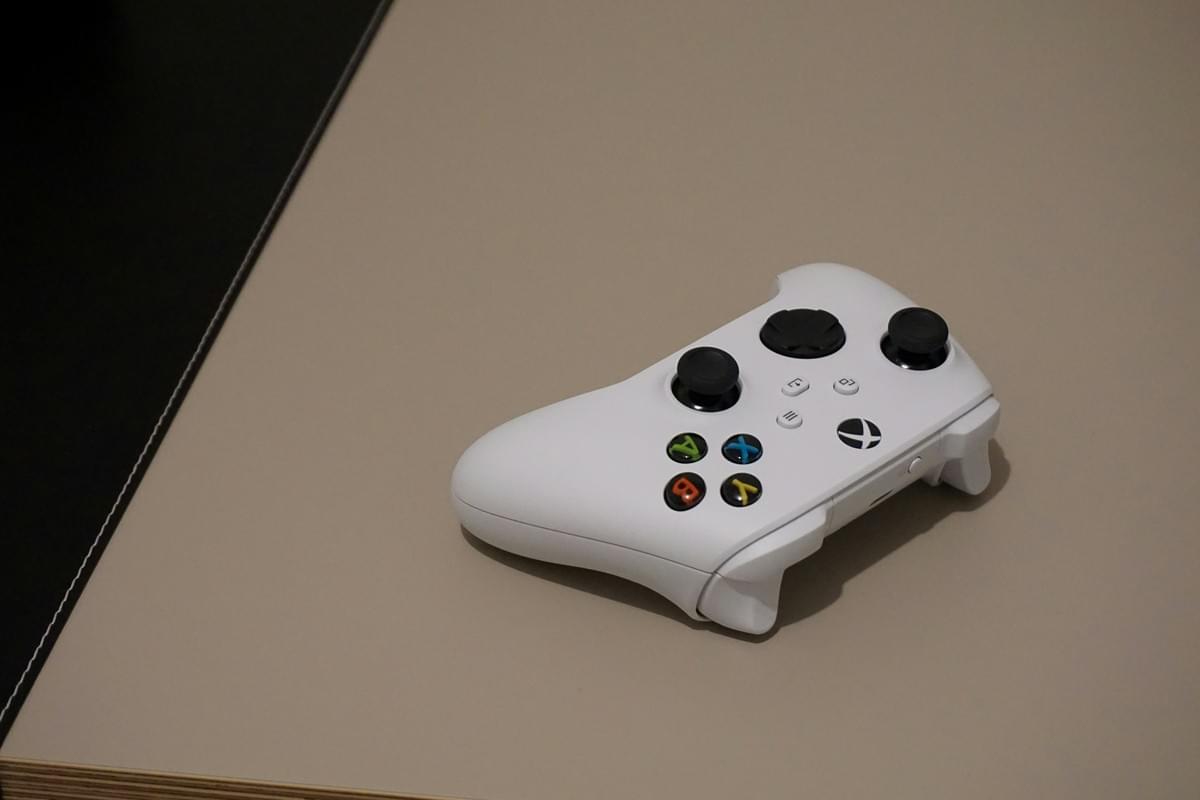
Insert molding is a fascinating manufacturing technique that combines two different materials into a single component. Unlike overmolding, where a softer material is molded over a harder substrate, insert molding involves placing pre-formed inserts—typically made of metal or plastic—into the mold before injecting plastic around them. This method allows for complex designs and enhanced functionality in various applications.
Definition and Process of Insert Molding
So, what does insert molding entail? Essentially, it's about taking an existing part or insert and encasing it with molten plastic during the injection process. The inserts can be anything from metal components to electronic parts, which are strategically placed into the mold cavity before the injection of thermoplastic material occurs. This results in a strong bond between the insert and the surrounding plastic, creating a robust final product.
Key Benefits of Insert Molding
The advantages of insert molding are numerous and quite compelling! For starters, it significantly reduces assembly time since multiple components can be combined in one shot rather than requiring separate assembly steps—talk about efficiency! Additionally, this method enhances durability by ensuring that inserts are securely encapsulated within the molded part, which is crucial for applications where reliability is paramount.
Common Materials Utilized in Insert Molding
Commonly utilized materials include thermoplastics like ABS (Acrylonitrile Butadiene Styrene) and polycarbonate due to their strength and versatility. Furthermore, metals such as aluminum or stainless steel are often used for inserts because they provide excellent structural integrity when encased in plastic—making them ideal for demanding applications.
Comparing Overmolding and Insert Molding

When it comes to molding techniques, overmolding and insert molding often get thrown into the same conversation. But what does overmolding mean, and how does it differ from insert molding? Understanding the nuances of these processes is crucial for choosing the right one for your project.
Key Differences in Processes
The overmolding process involves layering a second material over a pre-formed substrate, creating a part that combines different materials into a single unit. This technique allows for enhanced grip, improved aesthetics, and added functionality. In contrast, insert molding incorporates pre-existing components—like metal or plastic parts—into the mold before the primary material is injected around them, resulting in a strong bond between materials.
What is the difference between overmolding and insert molding? While both methods aim to enhance product performance through multi-material integration, their approaches are distinct. Overmolding focuses on adding soft-touch materials or specialized coatings to an existing part, whereas insert molding embeds functional components within the molded part itself.
Longevity and Durability Considerations
When evaluating longevity and durability, both overmolding and insert molding boast impressive results but shine in different areas. Overmolded products tend to have superior tactile qualities due to their softer outer layers; however, they may be more susceptible to wear if not designed properly. On the other hand, insert molded items benefit from robust structural integrity since they incorporate solid components directly into their design.
What does it mean to mold over? Essentially, it means creating an additional layer that can enhance both function and feel. The durability of an overmolded item largely depends on its material choices; using high-quality elastomers can improve resistance against environmental factors while maintaining flexibility.
Cost Implications for Each Method
Cost implications vary significantly between these two methods based on material choices and complexity of design. The initial setup costs for overmolding might be higher due to specialized molds required for layering processes; however, this investment can pay off by reducing assembly time later on. In contrast, while insert molding may have lower upfront costs due to simpler molds, its production speed might lag behind that of efficient overmolding techniques.
What is the difference between 2k molding and overmolding? 2k (or two-shot) molding is another term often associated with similar processes but typically refers specifically to injecting two different materials sequentially in one mold cycle—this can overlap with traditional overmolding practices but has distinct operational methodologies as well. Overall cost considerations should factor in not only immediate expenses but also long-term benefits like durability and market competitiveness when deciding between these two approaches.
Industry Applications for Overmolding
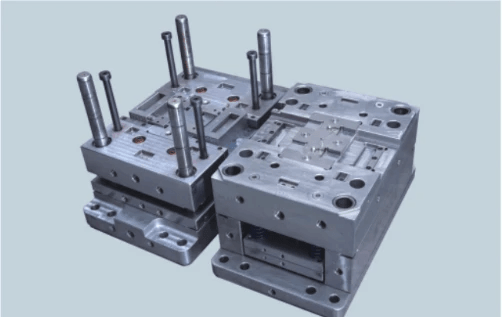
Overmolding is a versatile manufacturing technique that finds its way into various industries, enhancing product performance and user experience. By understanding what overmolding means in the context of different applications, we can see its significant benefits across sectors. In this section, we will explore how overmolding is utilized in consumer electronics, medical devices, and automotive components.
Consumer Electronics
In the world of consumer electronics, overmolding plays a crucial role in improving both aesthetics and functionality. Devices like smartphones and tablets often feature rubberized grips or textured surfaces achieved through the overmolding process. This not only makes products more comfortable to hold but also adds durability against drops and scratches—an essential quality for everyday gadgets.
What does overmolding mean for manufacturers? It signifies an opportunity to create multi-material components that enhance user interaction while reducing assembly time. For example, a common application includes molding soft-touch materials over hard plastic casings to improve grip without compromising structural integrity.
When comparing overmolding vs injection molding, the former offers unique advantages such as reduced part count and increased design flexibility. Overmolding examples in consumer electronics include headphone ear tips and remote control buttons that provide both comfort and functionality.
Medical Devices
The medical device industry benefits immensely from the precision offered by overmolding techniques. Products such as syringes or surgical instruments often require a combination of hard plastics for structure and softer materials for patient comfort—this is where the question What does it mean to mold over? becomes relevant. By using the overmolding process, manufacturers can create devices that are not only effective but also safe and pleasant for users.
In medical applications, durability is paramount; thus, choosing appropriate materials during the overmolding process is critical to ensure longevity under rigorous conditions. For instance, creating handles with soft grips enhances usability while maintaining sterility—a vital factor in healthcare settings.
Additionally, many medical devices utilize two-shot (2k) molding techniques alongside traditional overmolding methods to achieve complex geometries with varying material properties within one part. This integration leads to innovative designs that improve overall patient care while streamlining production processes.
Automotive Components
Overmolding has carved out a significant niche within automotive manufacturing by enhancing component performance while reducing weight—a crucial factor in modern vehicle design aimed at improving fuel efficiency. From dashboard controls to exterior trims, what is the difference between 2k molding and overmolding becomes evident as both methods are employed strategically based on design needs.
The automotive sector relies on durable yet lightweight materials; hence using an overmolded soft-touch layer on hard plastic parts helps mitigate vibrations while providing aesthetic appeal. Parts like gear knobs or door handles frequently incorporate this technology to create comfortable interactions between drivers and their vehicles.
Moreover, employing the overmolding process allows manufacturers to reduce assembly time by consolidating multiple components into one cohesive unit—streamlining production without sacrificing quality or performance standards expected from automotive parts.
Industry Applications for Insert Molding
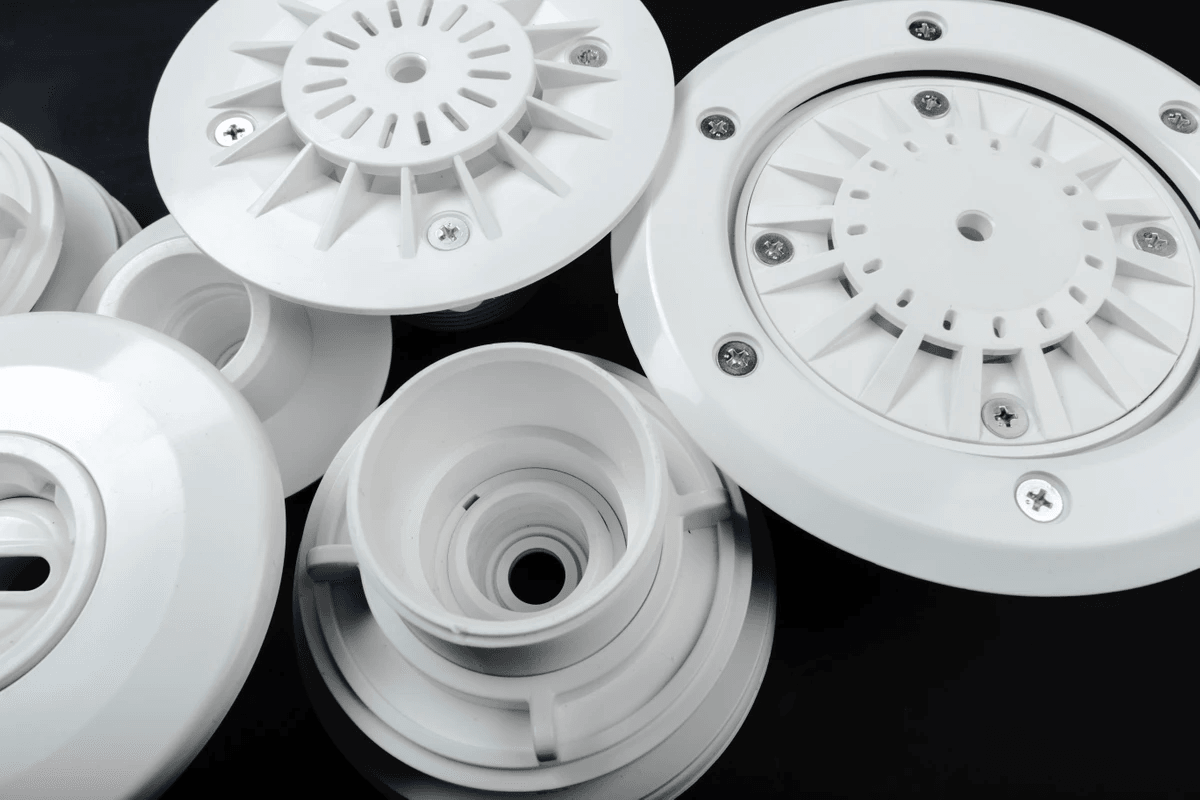
Insert molding is a highly versatile manufacturing technique that finds its way into various industries, proving its worth through durability and efficiency. By integrating metal or other materials into plastic components, insert molding enhances the performance and functionality of end products. Let's explore some key applications where insert molding shines.
Aerospace Components
In the aerospace industry, precision and reliability are non-negotiable. Insert molding allows manufacturers to achieve these standards by embedding components like metal brackets or connectors into plastic parts, creating lightweight yet robust assemblies. This process not only reduces assembly time but also minimizes potential failure points, which is critical when safety is paramount in aerospace applications.
When discussing the difference between overmolding and insert molding in this context, it’s clear that insert molding focuses on integrating different materials to enhance structural integrity rather than simply adding a layer over an existing part. The ability to mold over specific inserts ensures that each component fits perfectly within complex designs required in aircraft and spacecraft. Overall, the insert molding process proves invaluable in producing reliable aerospace components that meet stringent regulations.
Industrial Equipment
The industrial equipment sector benefits tremendously from the use of insert molding techniques as well. Here, manufacturers often require durable parts that can withstand harsh environments while maintaining operational efficiency. By utilizing insert molding, companies can create equipment housings with embedded metal reinforcements or electrical connectors seamlessly integrated into their design.
What does it mean to mold over? In this case, it refers to how insert molded parts can encapsulate critical elements within a single piece, reducing the need for additional fasteners or assembly steps—this streamlines production processes significantly. The combination of strength from inserted materials and flexibility from plastics makes this method particularly appealing for machinery used in manufacturing settings where durability is key.
Household Appliances
Household appliances are another area where insert molding plays a crucial role in design and functionality. Manufacturers leverage this technique to produce appliance casings that incorporate electrical components securely within their structures—think about how your blender or toaster has both plastic exteriors and functional internal mechanisms all working harmoniously together!
In comparing overmolding vs injection molding here, it's evident that while injection molding creates standalone parts efficiently, insert molding adds value by combining multiple functionalities into one cohesive product without compromising on quality or performance. Overmolding examples abound in kitchen gadgets where ease of use meets advanced engineering—insert molded appliances often feature ergonomic grips made from soft-touch materials alongside sturdy structural elements molded directly into place.
Conclusion
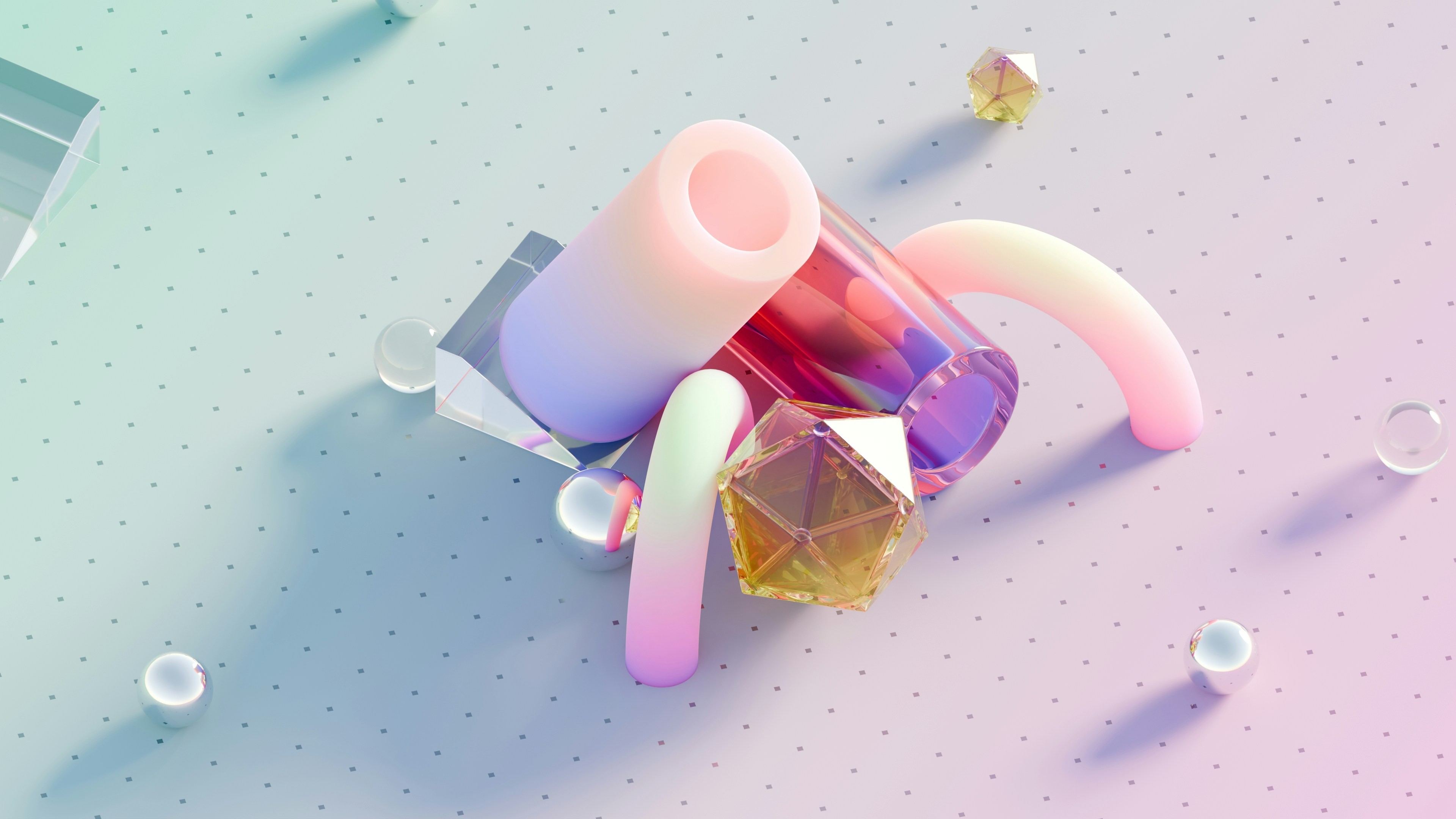
In the realm of manufacturing, selecting the right molding technique can significantly impact product quality, cost, and functionality. Understanding the nuances of overmolding and insert molding is essential for businesses aiming to optimize their production processes. By evaluating factors like application requirements and material compatibility, companies can make informed decisions that align with their specific needs.
Choosing the Right Molding Technique
When deciding between overmolding and insert molding, it's crucial to consider what each technique offers in terms of performance and application suitability. Overmolding involves layering materials to enhance grip or aesthetics, while insert molding integrates components into a single piece for added strength. Understanding what does overmolding mean in your context will help clarify whether this method or its counterpart is more appropriate for your project.
Additionally, one must ponder: what is the difference between overmolding and insert molding? Overmolding typically focuses on adding a second material onto an existing substrate for improved functionality or design appeal. On the other hand, insert molding embeds parts within a molded component—each has its unique advantages depending on specific project requirements.
The Role of Baoyuan in the Molding Process
Baoyuan stands out as a pivotal player in advancing both overmolding and insert molding techniques within various industries. With expertise in optimizing the overmolding process, Baoyuan ensures that clients receive high-quality products tailored to their specifications. Their commitment to innovation means they are constantly exploring new materials and methods to enhance production efficiency while maintaining exceptional standards.
Moreover, by leveraging Baoyuan's capabilities, businesses can gain insights into practical applications of overmolding examples across different sectors—from consumer electronics to automotive components. The company’s proficiency also extends into understanding what it means to mold over existing structures effectively—ensuring seamless integration with minimal waste or defects during production.
Future Trends in Overmolding and Insert Molding
Looking ahead, we can expect exciting advancements in both overmolding and insert molding techniques driven by technological innovations and evolving market demands. As industries increasingly prioritize sustainability, there will likely be a shift toward eco-friendly materials that still deliver optimal performance through methods like 2k molding compared to traditional approaches such as injection molding.
Furthermore, as automation technology continues to develop at an unprecedented pace, we may see significant improvements in speed and precision during the overmolding process—ultimately lowering costs while enhancing product quality. Keeping an eye on these trends will be essential for manufacturers seeking competitive advantages through effective use of both overmolding vs injection molding strategies.