Introduction
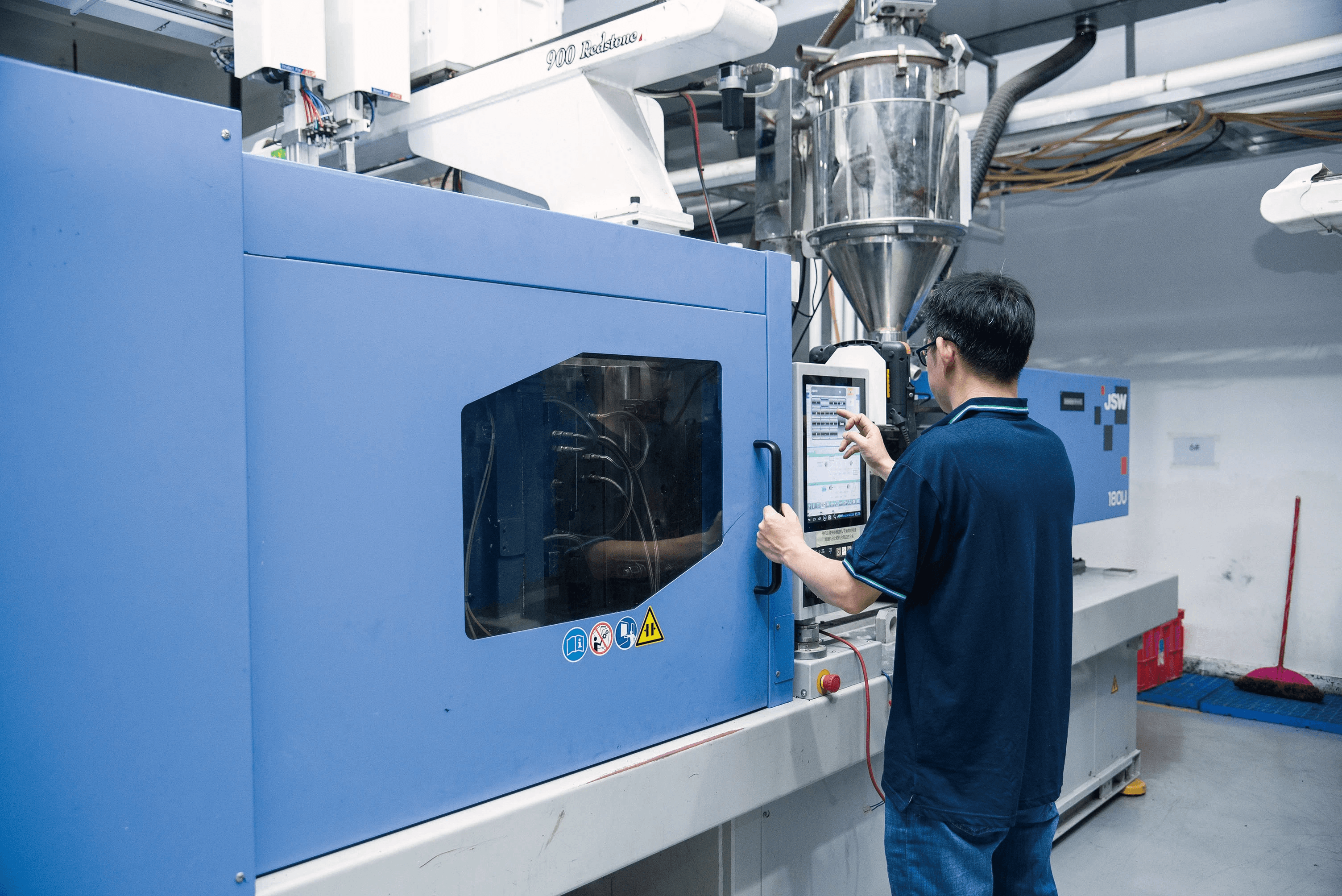
Injection molding is a widely used manufacturing process, but one of its quirks—shrinkage—can leave designers scratching their heads. Understanding injection molding shrinkage is critical for producing accurate and high-quality parts. So, what is the shrinkage of injection molding? This phenomenon occurs when the material cools and contracts after being injected into the mold, and it can significantly affect the final dimensions of a product.
Understanding Injection Molding Shrinkage
At its core, injection molding shrinkage refers to the reduction in size that occurs as molten plastic cools and solidifies within a mold. The degree of shrinkage can vary based on several factors, including material type and processing conditions. To navigate this tricky terrain effectively, it's essential to know what is the ISO standard for molding shrinkage, which provides industry benchmarks for measuring these changes.
Key Factors Influencing Shrinkage
Several key factors influence injection molding shrinkage rates—material selection stands out as one of the most significant determinants. Different resins exhibit varying degrees of contraction; for instance, polypropylene (PP) has its unique challenges when it comes to managing shrinkage. Additionally, temperature control during processing plays a crucial role in achieving consistent results; fluctuations can lead to unexpected variations in what is the standard shrinkage rate.
The Importance of Accurate Measurements
Accurate measurements are paramount in mitigating issues related to injection molding shrinkage. Without precise data on how much a part will contract post-molding, manufacturers risk producing components that do not meet specifications or fit together correctly. Utilizing tools like a mold shrinkage chart can help engineers predict and adjust for these changes effectively while also exploring techniques on how to increase shrinkage in injection molding when necessary.
What is Injection Molding Shrinkage?
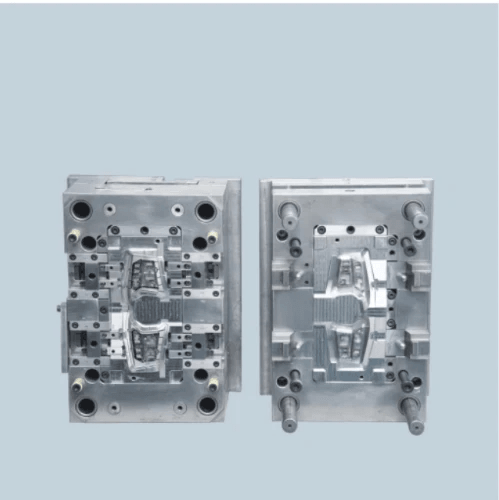
Injection molding shrinkage is a critical concept that every manufacturer should grasp. It refers to the dimensional change that occurs in a plastic part as it cools and solidifies after being injected into a mold. Understanding this phenomenon is essential for achieving precise dimensions and maintaining quality in production.
Defining Injection Molding Shrinkage
At its core, injection molding shrinkage describes how much a molded part decreases in size during the cooling process. When molten plastic fills the mold, it expands to fit; however, as it cools, it contracts—leading to what we term shrinkage. This change can affect both the final product's dimensions and its overall performance, making it vital to account for when designing molds.
Industry Standards and Measurements
In the world of injection molding, there are established industry standards that help quantify shrinkage rates across different materials. These standards provide a baseline for manufacturers to ensure consistency and quality control throughout production runs. Accurate measurements of injection molding shrinkage are crucial for aligning expectations with actual outcomes.
What is the ISO Standard for Molding Shrinkage?
The ISO standard for molding shrinkage serves as an internationally recognized guideline that defines acceptable levels of dimensional change during the cooling phase of injection molded parts. Specifically, this standard provides parameters regarding what constitutes typical shrink rates based on material types and processing conditions. Adhering to these guidelines helps manufacturers answer questions like What is the standard shrinkage rate? while ensuring compliance with global manufacturing norms.
Factors Affecting Shrinkage Rates
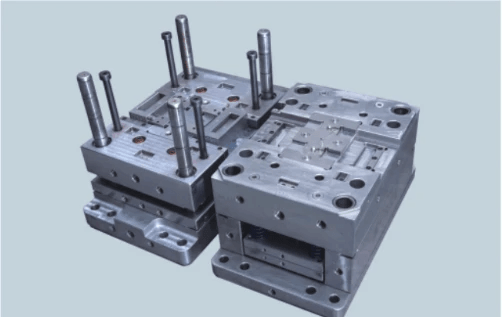
Understanding the factors that affect injection molding shrinkage is crucial for manufacturers aiming to produce high-quality parts. Several elements come into play, including material selection, temperature control during processing, and thoughtful design considerations. Each of these factors can significantly influence the outcome of the molding process and the final product's dimensions.
Material Selection and Its Impact
Different materials exhibit varying shrinkage rates; for instance, polypropylene (PP) has a specific shrinkage profile that must be accounted for in the design phase. Understanding What is the shrinkage of injection molding? involves recognizing how different resins respond to cooling and solidification processes—some materials may expand or contract more than others, leading to potential defects if not managed properly.
Moreover, it's essential to consult a mold shrinkage chart when selecting materials to ensure that you're choosing one with a compatible shrinkage rate for your application. This chart provides valuable insights into standard shrinkage rates across various polymers, helping manufacturers avoid unpleasant surprises down the line. Ultimately, selecting the right material can make all the difference in achieving desired tolerances and minimizing post-processing adjustments.
Temperature Control During Processing
Temperature control during processing plays a critical role in managing injection molding shrinkage effectively. Maintaining optimal temperatures throughout both heating and cooling phases ensures that materials behave predictably as they transition from molten state to solid form. If temperatures fluctuate too much or remain inconsistent, it can lead to uneven cooling rates—resulting in warping or excessive shrinkage.
To address What is the ISO standard for molding shrinkage? it's important to note that industry standards often emphasize maintaining strict temperature controls during production cycles. By adhering to these guidelines, manufacturers can improve consistency in their products while minimizing variations caused by thermal shifts. Properly managing temperature not only aids in reducing unwanted injection molding shrinkage but also enhances overall part quality.
Design Considerations for Minimizing Shrinkage
The design of an injection-molded part greatly influences its susceptibility to shrinkage issues; therefore, careful consideration should be given during this phase of development. Features such as wall thickness uniformity are vital—thicker sections cool slower than thinner ones, leading to differential shrinking and potential defects like sink marks or warping if not designed correctly.
Incorporating rounded corners instead of sharp edges can help reduce stress concentrations that contribute to uneven cooling as well—this is where knowing What is the standard shrinkage rate? becomes essential when designing molds tailored for specific materials like PP or others with known properties on mold shrinkage charts.
Furthermore, employing ribbing strategically within designs can enhance structural integrity while also controlling how parts cool down post-injection; this minimizes unexpected dimensional changes due to differential cooling rates across various sections of a molded part.
What is the Standard Shrinkage Rate?

Understanding the standard shrinkage rate in injection molding is crucial for anyone involved in manufacturing processes. Injection molding shrinkage refers to the reduction in size of a molded part as it cools and solidifies. By knowing what the standard shrinkage rate is, manufacturers can better predict and manage their production outcomes, ensuring high-quality results.
Typical Rates for Various Materials
Different materials exhibit varying rates of injection molding shrinkage, which can significantly impact the final product's dimensions. For instance, thermoplastics like polypropylene (PP) typically have a shrinkage rate ranging from 1% to 2%, while others like ABS may show rates between 0.5% and 1%. Understanding these typical rates helps manufacturers determine how much material will be needed and what adjustments might be necessary during production.
The Impact of Resin Types on Shrinkage
The type of resin used in injection molding plays a pivotal role in determining the overall shrinkage rate of a molded part. For example, crystalline resins often experience higher shrinkage due to their molecular structure compared to amorphous resins, which tend to have more consistent dimensional stability during cooling. This leads us back to our earlier question: What is the shrinkage of injection molding? It's essential to consider resin types when predicting these values.
How to Reference a Mold Shrinkage Chart
To accurately assess and manage injection molding shrinkage, referencing a mold shrinkage chart is invaluable. These charts provide detailed information on expected shrink rates for various materials under specific conditions, allowing engineers and designers to make informed decisions regarding mold design and material selection. When using such charts, it's important to note factors such as temperature control during processing and specific resin properties that could affect outcomes.
Addressing Specific Material Concerns
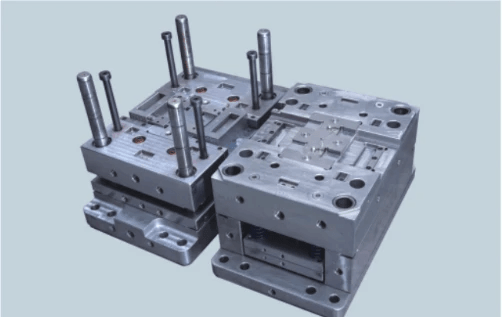
When it comes to injection molding, understanding the specifics of material behavior is crucial. Polypropylene (PP) is a popular thermoplastic that presents unique challenges regarding injection molding shrinkage. Addressing these concerns can help manufacturers optimize their processes and produce high-quality parts.
What is the Shrinkage of PP?
What is the shrinkage of PP? The typical shrinkage rate for polypropylene in injection molding ranges from 1% to 2%, although this can vary based on factors like processing conditions and part geometry. Understanding this range is essential for accurately predicting final dimensions and ensuring parts fit together as intended, especially when considering what is the standard shrinkage rate across different materials.
The variability in PP’s shrinkage also highlights the importance of consulting a mold shrinkage chart, which provides valuable insights into how different formulations might behave during cooling and solidification. By keeping these rates in mind, manufacturers can better manage expectations and minimize discrepancies in part production.
Strategies for Polypropylene Shrinkage Management
Managing polypropylene shrinkage effectively requires a multi-faceted approach that considers various aspects of the injection molding process. One effective strategy involves adjusting processing temperatures; optimizing melt temperature and mold temperature can significantly influence how much a part shrinks post-molding. Additionally, maintaining consistent cooling rates throughout the cycle can help reduce unexpected variations in size.
Another strategy includes modifying mold design—incorporating features such as draft angles or using uniform wall thicknesses can mitigate issues related to what is the shrinkage of injection molding? Furthermore, careful selection of gate locations can enhance material flow and reduce localized cooling effects that may lead to uneven shrinkage.
Finally, utilizing simulation software allows engineers to predict potential issues before production begins, helping them make necessary adjustments proactively rather than reactively responding after problems arise.
The Role of Additives in Reducing Shrinkage
Additives play a pivotal role in managing injection molding shrinkage, particularly for materials like polypropylene. Certain additives are designed specifically to enhance dimensional stability by reducing overall shrink rates during cooling phases. For instance, incorporating nucleating agents or fillers can alter crystallization behavior, leading to more uniform properties across molded parts.
Moreover, understanding what is the ISO standard for molding shrinkage helps manufacturers choose suitable additives that comply with industry standards while achieving desired performance characteristics. These additives not only aid in reducing overall shrink but also improve other mechanical properties such as strength and impact resistance.
In summary, leveraging additives strategically offers an effective means to address concerns about how to increase shrinkage in injection molding while maintaining product quality and compliance with industry norms.
How to Increase Shrinkage in Injection Molding
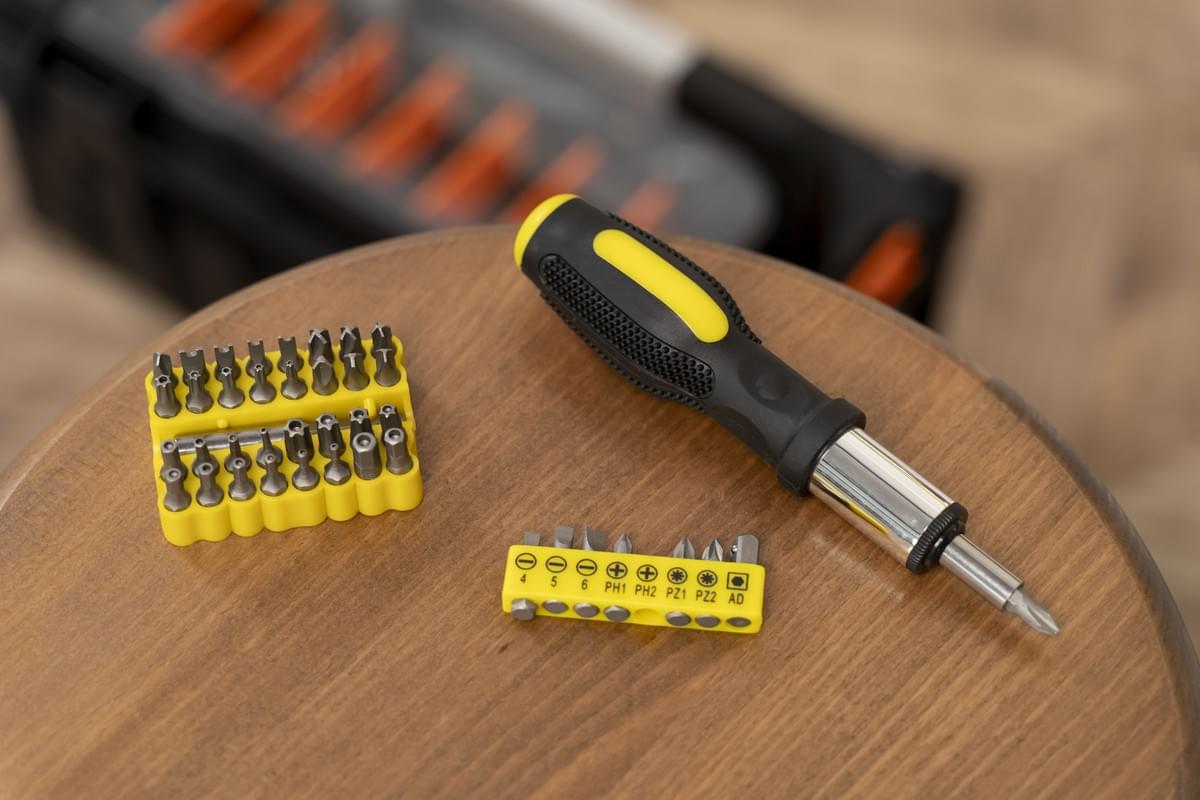
When it comes to injection molding shrinkage, understanding how to effectively manage it can significantly impact the quality of your final product. While most discussions focus on minimizing shrinkage, there are valid scenarios where increasing shrinkage may be beneficial. By implementing specific techniques, adjusting mold design, and leveraging technology, you can achieve the desired results while ensuring adherence to industry standards.
Techniques for Managing Shrinkage
To effectively manage injection molding shrinkage, one must first grasp the underlying principles of material behavior during cooling and solidification. Techniques such as optimizing cooling rates and adjusting injection speeds can lead to better control over how much a part shrinks after ejection from the mold. Additionally, incorporating proper venting and ensuring consistent material flow can help regulate what is the standard shrinkage rate for different materials.
Understanding what is the shrinkage of injection molding requires a deep dive into these techniques as they directly influence how materials behave under varying conditions. For example, if you're working with polypropylene (PP), knowing what is the shrinkage of PP specifically allows for targeted adjustments that can enhance production efficiency while maintaining quality standards. Utilizing resources like a mold shrinkage chart can provide valuable insights into expected rates based on specific materials and conditions.
Adjustments in Mold Design
Mold design plays a critical role in managing injection molding shrinkage effectively. By modifying wall thicknesses or adding features like ribs or fillets, you can influence how heat dissipates throughout the molded part—ultimately affecting its dimensions post-cooling. Moreover, designing molds with appropriate draft angles ensures easier ejection of parts without compromising their integrity or leading to excessive warpage.
When considering what is the ISO standard for molding shrinkage, it's important to align your mold design processes with these benchmarks for consistency across production runs. The incorporation of conformal cooling channels within molds can also drastically improve temperature uniformity during processing—a key factor in controlling what is the standard shrinkage rate for various resins used in manufacturing processes today.
Utilizing Technology for Better Results
In today's fast-paced manufacturing environment, technology has become an indispensable ally in managing injection molding shrinkage efficiently. Advanced simulation software allows engineers to predict potential issues related to shrinkage before production begins by modeling different scenarios based on material properties and processing conditions. This proactive approach not only saves time but also reduces waste associated with trial-and-error methods.
Additionally, real-time monitoring systems provide vital data during production runs that help adjust parameters dynamically—ensuring optimal performance when dealing with complex materials like PP where understanding what is the shrinkage of PP becomes crucial for achieving desired outcomes quickly and accurately. By referencing updated mold shrinkage charts frequently throughout production cycles, teams can maintain awareness about shifts in standards or unexpected variations that may arise due to external factors.
Conclusion
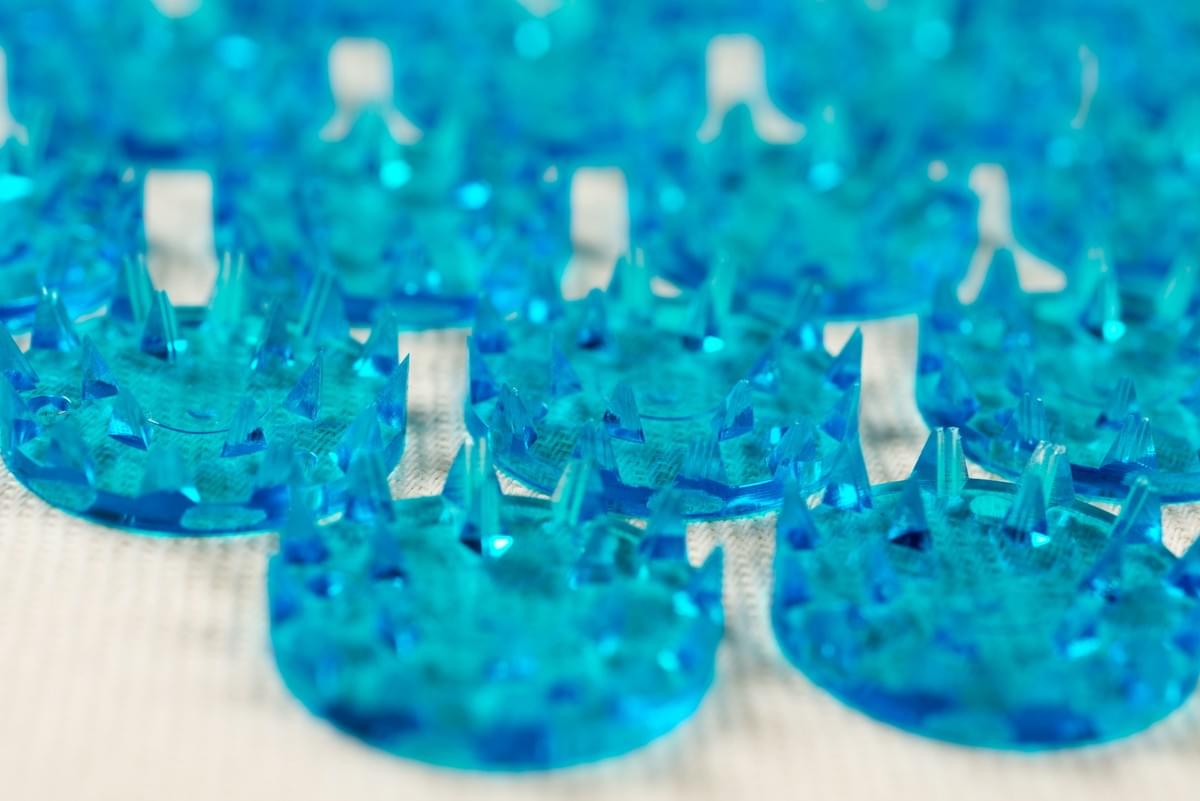
In conclusion, understanding injection molding shrinkage is crucial for anyone involved in the manufacturing process. From defining what injection molding shrinkage is to recognizing the importance of industry standards like the ISO standard for molding shrinkage, we’ve covered a lot of ground. By grasping the nuances of shrinkage rates and how they vary across different materials, you can make informed decisions that enhance product quality.
Key Takeaways on Injection Molding Shrinkage
One critical takeaway is that the standard shrinkage rate varies depending on material choice and processing conditions. For instance, if you're wondering what is the shrinkage of PP (polypropylene), you'll find it has specific characteristics that differ from other resins. Additionally, utilizing a mold shrinkage chart can help you visualize these differences and aid in making adjustments to minimize unwanted outcomes.
Best Practices for Quality Assurance
To ensure quality assurance in your injection molding projects, consistently monitor temperature control during processing and select materials wisely based on their known shrinkage rates. Implementing best practices involves not only understanding what is the standard shrinkage rate but also knowing how to increase shrinkage in injection molding when necessary through design modifications or technology enhancements. Regularly consulting with mold design experts can also help mitigate risks associated with unexpected changes in dimensions.
Collaborating with Experts like Baoyuan Team
Finally, collaborating with experts like the Baoyuan Team can provide invaluable insights into managing injection molding shrinkage effectively. Their expertise can guide you through specific material concerns such as what is the shrinkage of PP and how additives might play a role in reducing it. By leveraging their knowledge, you’ll be better equipped to tackle challenges associated with mold design and processing techniques while ensuring compliance with industry standards.