Introduction
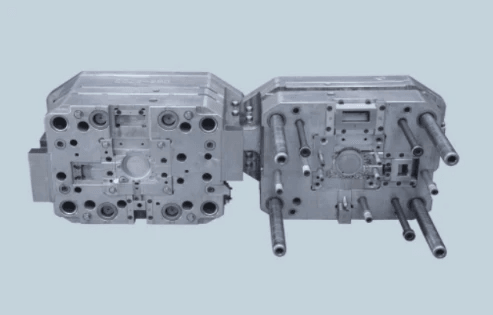
In the world of injection molding, undercuts can be a real game-changer. Understanding injection molding undercuts is crucial for anyone involved in product design and manufacturing, as they can significantly impact both the molding process and the final product's functionality. This introduction will delve into what constitutes an undercut in injection molding, its importance, and some common issues that arise in this context.
Understanding Injection Molding Undercuts
So, what is undercut in injection molding? An undercut refers to a feature on a molded part that prevents it from being easily ejected from the mold due to its geometry. These features can be internal or external and require careful consideration during the design phase to avoid complications later on.
The Importance of Undercut Regions
The importance of undercut regions cannot be overstated; they often play a critical role in how well a part functions within an assembly or system. Properly designed undercuts can enhance product performance by allowing for better fit and function, while poorly managed ones can lead to increased production costs and time delays. Recognizing these regions early on helps streamline the manufacturing process.
Common Issues with Injection Molding Undercuts
Common issues with injection molding undercuts include difficulties during ejection, increased wear and tear on molds, and potential defects in the final product if not handled correctly. Manufacturers often face challenges when trying to balance aesthetic design elements with functional requirements due to these pesky features. Understanding how to deal with undercuts effectively is essential for ensuring quality results without breaking the bank or extending timelines unnecessarily.
What Is Undercut in Injection Molding?
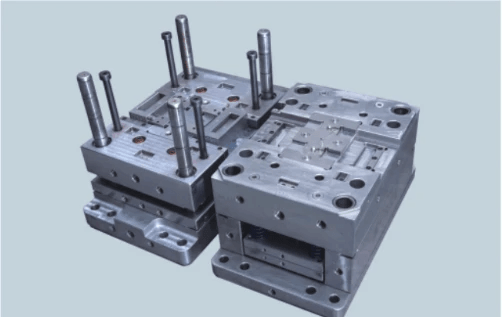
Injection molding undercuts are a critical aspect of the molding process that designers and manufacturers must understand. An undercut occurs when a molded part has features that prevent it from being easily removed from the mold without additional movement or mechanisms. This can complicate production and increase costs, making it vital to grasp what undercuts are and how they impact the overall injection molding process.
Definition and Significance
What is undercut in injection molding? Simply put, an undercut is any feature on a molded part that extends into the mold cavity, creating a geometric obstacle during the ejection phase. The significance of understanding injection molding undercuts lies in their ability to affect both design feasibility and manufacturing efficiency. If not properly accounted for, these features can lead to increased cycle times, higher tooling costs, or even product defects.
Connection to Product Design
The connection between injection molding undercuts and product design cannot be overstated; they often dictate how a product is shaped and manufactured. Designers must consider potential undercut regions early in the design phase to ensure that parts can be produced efficiently without compromising functionality or aesthetics. By integrating knowledge of types of undercut in injection molding into their designs, engineers can create more manufacturable products while minimizing risks associated with complex molds.
Real-World Examples
Real-world examples of injection molding undercuts abound across various industries, showcasing both challenges and innovative solutions. For instance, internal undercut injection molding is commonly found in components like automotive parts or consumer electronics where intricate shapes are essential for fitment or assembly. On the other hand, bump off injection molding may be utilized for decorative elements or ergonomic grips where aesthetics play a crucial role—demonstrating how understanding these concepts can lead to better product outcomes.
Types of Undercut in Injection Molding
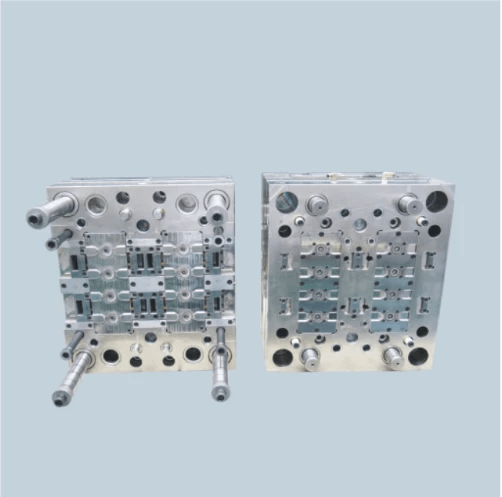
When it comes to injection molding undercuts, understanding the various types is crucial for effective design and manufacturing. Different types of undercuts can significantly impact the molding process, influencing everything from mold design to production efficiency. This section will explore two primary types of undercuts: internal undercut injection molding and bump off injection molding, along with a comparison to highlight their unique characteristics.
Internal Undercut Injection Molding
Internal undercut injection molding refers to scenarios where features are incorporated within the part that create a recess or ledge inside the molded item. These undercuts can complicate the ejection process, as they prevent straightforward removal from the mold without additional mechanisms or complex designs. Understanding what is an undercut in injection molding helps designers anticipate these challenges and implement solutions early in product development.
To manage internal undercuts effectively, engineers often employ specialized molds with sliding cores or lifters that allow for smooth ejection despite the presence of these features. While this adds complexity and cost to mold design, it can be essential for achieving intricate shapes that enhance product functionality. Thus, recognizing how do you prevent undercut in injection molding becomes vital when crafting parts with internal features.
Bump Off Injection Molding
Bump off injection molding is another type of undercut that occurs when a protrusion or bump on a part creates an obstruction during ejection from the mold. This situation typically arises when there are designs with external details that cannot be easily extracted without causing damage to either the part or the mold itself. Understanding what is the undercut region helps designers identify potential problem areas before they become costly issues down the line.
To address bump off issues effectively, manufacturers may incorporate draft angles into their designs or utilize advanced mold technologies like collapsible cores that allow for easier release of parts with complex geometries. By proactively considering how to deal with undercuts during design stages, teams can streamline production processes and minimize defects associated with difficult ejections. Therefore, knowing about bump off injection molding prepares engineers for potential hurdles they might face.
Comparisons Between Various Types
When comparing internal undecuts and bump off scenarios within injection molding processes, several key differences emerge that influence both design decisions and production methods. Internal undecut regions tend to require more sophisticated tooling due to their hidden nature within parts; conversely, bump offs are typically more visible but present their own set of challenges during part removal from molds.
Both types highlight why understanding types of undercut in injection molding is essential—each requires tailored strategies for prevention and management throughout development phases. While both may seem similar at first glance, their implications on overall manufacturing processes differ significantly; hence recognizing these distinctions aids in efficient project planning and execution.
What Is the Undercut Region?
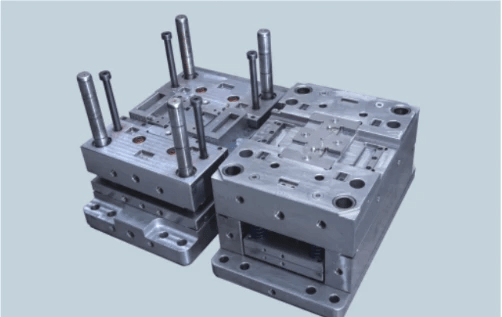
Understanding the undercut region is crucial for anyone involved in injection molding. An undercut in injection molding refers to a feature that prevents a molded part from being easily ejected from the mold without additional mechanisms or modifications. Identifying these areas can significantly impact both the design and manufacturing processes, influencing everything from production efficiency to part quality.
Identifying Undercut Areas
To effectively manage injection molding undercuts, it’s essential first to identify where these problematic areas are located. Common indicators include features like grooves, recesses, or any geometry that creates an obstruction during ejection. For example, internal undercut injection molding may involve shapes that curve inward, while bump off injection molding might showcase protrusions that complicate removal.
Impact on the Molding Process
The presence of undetected undercut regions can have significant repercussions on the overall molding process. They often necessitate specialized mold designs and additional components like slides or lifters to facilitate part ejection, which can increase production costs and lead times. Additionally, if not properly accounted for during design stages, these areas might result in defects such as warping or incomplete filling.
Visualizing Undercut Zones
Visualizing undercut zones is vital for designers and engineers aiming to streamline their workflows and avoid potential pitfalls associated with injection molding undercuts. Utilizing 3D modeling software can help simulate how different geometries will interact within molds, allowing teams to spot trouble spots before they become costly problems on the production floor. By effectively mapping out these regions early in the design process, manufacturers can devise strategies to prevent issues related to how do you prevent undercut in injection molding?
How Do You Prevent Undercut in Injection Molding?
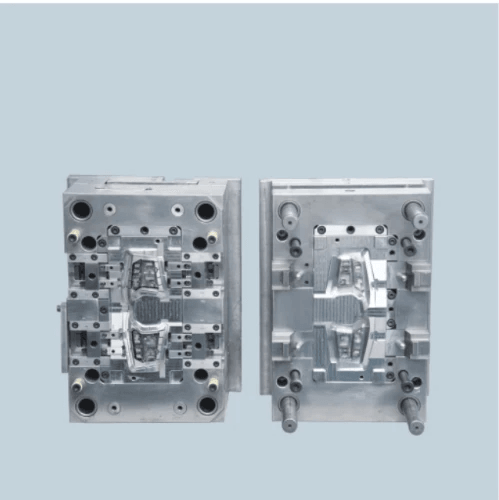
Preventing injection molding undercuts is crucial for ensuring a smooth production process and high-quality end products. Understanding the strategies and tools available can significantly reduce the occurrence of these design challenges. With the right approach, manufacturers can avoid costly delays and improve overall efficiency.
Design Strategies to Avoid Undercuts
When considering how to prevent undercut in injection molding, design strategies play a pivotal role. One effective approach is to simplify part geometries by eliminating complex shapes that may lead to internal undercut injection molding issues. Additionally, incorporating draft angles can help facilitate easier ejection from molds, reducing the risk of bump off injection molding problems.
Another strategy involves using symmetrical designs whenever possible. Symmetry not only enhances aesthetic appeal but also minimizes potential undercut regions that complicate mold creation. Finally, collaborating with experienced designers early in the product development phase ensures that all aspects of the design are optimized to avoid unnecessary undercuts.
Tools and Software Utilization
In today’s digital age, utilizing advanced tools and software is essential for managing undercuts effectively. CAD (Computer-Aided Design) programs allow engineers to visualize potential undercut regions during the design process, making it easier to identify problematic areas before they become costly mistakes. These tools often include simulation features that predict how materials will behave during injection molding, allowing for adjustments before physical prototypes are created.
Moreover, specialized software can analyze different types of undercut in injection molding scenarios and suggest modifications based on industry best practices. By leveraging technology, manufacturers can streamline their processes and enhance productivity while minimizing errors related to undercuts. Ultimately, investing in these tools leads to faster turnaround times and higher-quality products.
Expertise of the Baoyuan Team
With years of experience in tackling common challenges associated with what is an undercut in injection molding, their professionals provide invaluable insights into best practices for mold design and production strategies. Their knowledge extends beyond basic prevention techniques; they understand how various types of undercut in injection molding affect overall project timelines and costs.
Baoyuan's team also collaborates closely with clients throughout every stage of product development—from initial concept through final production—to ensure all potential pitfalls are addressed proactively. This holistic approach not only helps prevent issues but also fosters innovation within the industry by introducing new solutions tailored specifically for each client’s needs. By partnering with experts like Baoyuan, companies can confidently navigate complex projects while avoiding setbacks related to how do you prevent an undercut in injection molding?
How to Deal with Undercuts?
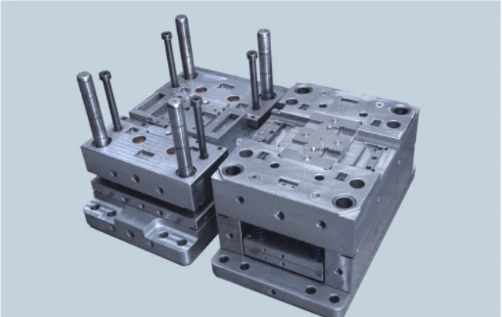
Dealing with injection molding undercuts can be a challenging endeavor, but it's not insurmountable. Understanding what is undercut in injection molding and the various types of undercut in injection molding is crucial for effective management. With the right techniques and considerations, manufacturers can navigate these complexities while achieving high-quality results.
Techniques for Managing Undercuts
When it comes to managing injection molding undercuts, several techniques can be employed to mitigate their impact. One effective method is the use of side actions or lifters that can retract during the ejection phase, allowing for the removal of parts that have internal undercut features. Additionally, utilizing a two-shot or multi-material molding process can help create complex geometries without compromising part integrity while effectively addressing how do you prevent undercut in injection molding.
Another approach involves modifying existing designs to reduce or eliminate the need for undercuts altogether. This might include redesigning features that would typically require bump off injection molding or adjusting dimensions to allow for smoother ejection paths. By strategically planning designs with these techniques in mind, manufacturers can significantly reduce issues associated with undercuts.
Lastly, embracing advanced technology such as 3D printing for prototyping allows designers to visualize potential issues before they become costly problems on the production floor. By testing designs early on, teams can identify what is the undercut region and make necessary adjustments before moving into full-scale production.
Mold Design Considerations
Mold design plays a pivotal role in effectively managing injection molding undercuts. Incorporating features such as draft angles and rounded edges can minimize friction during part ejection and help avoid complications related to what is an undercut in injection molding processes. Designing molds with sufficient clearance also ensures that parts are released smoothly without damaging intricate details.
Moreover, considering the flow of material during filling is crucial when dealing with types of undercut in injection molding. Ensuring that melt flow paths are optimized will not only improve cycle times but also enhance overall part quality by reducing potential defects caused by trapped air or material flow interruptions.
Collaboration between design engineers and mold makers is essential for creating effective solutions tailored specifically for each project’s unique requirements related to internal undecut injection molding or bump off techniques. This synergy helps ensure that all aspects of mold design are aligned with production goals while addressing any potential challenges posed by complex geometries.
Case Studies and Solutions
Examining real-world case studies provides valuable insights into how companies have successfully dealt with injection molding undercuts. For instance, one manufacturer faced significant challenges due to intricate internal features requiring extensive bump off injection molding methods, leading to increased costs and extended lead times. By re-evaluating their product design using advanced simulation software alongside expert consultation from teams like Baoyuan, they were able to streamline their process significantly.
In another example, a company producing automotive components encountered difficulties due to multiple internal undercuts within their parts’ designs which were causing frequent production delays and quality issues. They implemented innovative mold designs featuring collapsible cores that allowed them to efficiently manage these regions without sacrificing performance—showcasing how understanding what is the undercut region can lead directly to impactful solutions.
Ultimately, these case studies highlight not only the importance of proactive measures when considering how do you prevent undecut in injection molding but also emphasize collaboration among skilled professionals who understand both design intricacies and manufacturing capabilities.
Conclusion
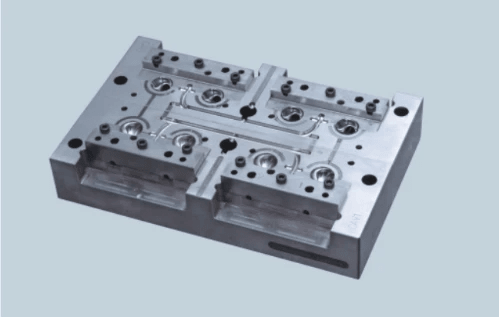
In the world of injection molding, understanding and managing undercuts is crucial for producing high-quality parts. The challenges associated with injection molding undercuts can be significant, but with the right strategies and insights, they can be effectively addressed. Whether it’s through innovative design approaches or advanced technologies, tackling the question of What is undercut in injection molding? becomes a manageable task.
Addressing Common Undercut Challenges
Common challenges related to injection molding undercuts often stem from their impact on mold design and part release. Identifying what is the undercut region early in the design phase allows engineers to develop solutions that minimize complications during production. By proactively addressing these issues, manufacturers can enhance efficiency and reduce costs associated with rework or redesign.
Innovative Techniques in Injection Molding
The landscape of injection molding is continually evolving, with innovative techniques emerging to mitigate issues related to types of undercut in injection molding. For instance, advancements in mold technology allow for better handling of internal undercut injection molding and bump off injection molding scenarios. These innovations not only simplify the manufacturing process but also improve product quality and precision.
The Role of Expert Teams like Baoyuan
Navigating the complexities of how to deal with undercuts requires expertise that many teams possess—like Baoyuan's skilled professionals who specialize in this field. Their deep understanding of how do you prevent undercut in injection molding empowers clients to achieve optimal results while minimizing risks associated with design flaws. With a collaborative approach, expert teams ensure that every project benefits from tailored solutions that address unique challenges effectively.