Introduction
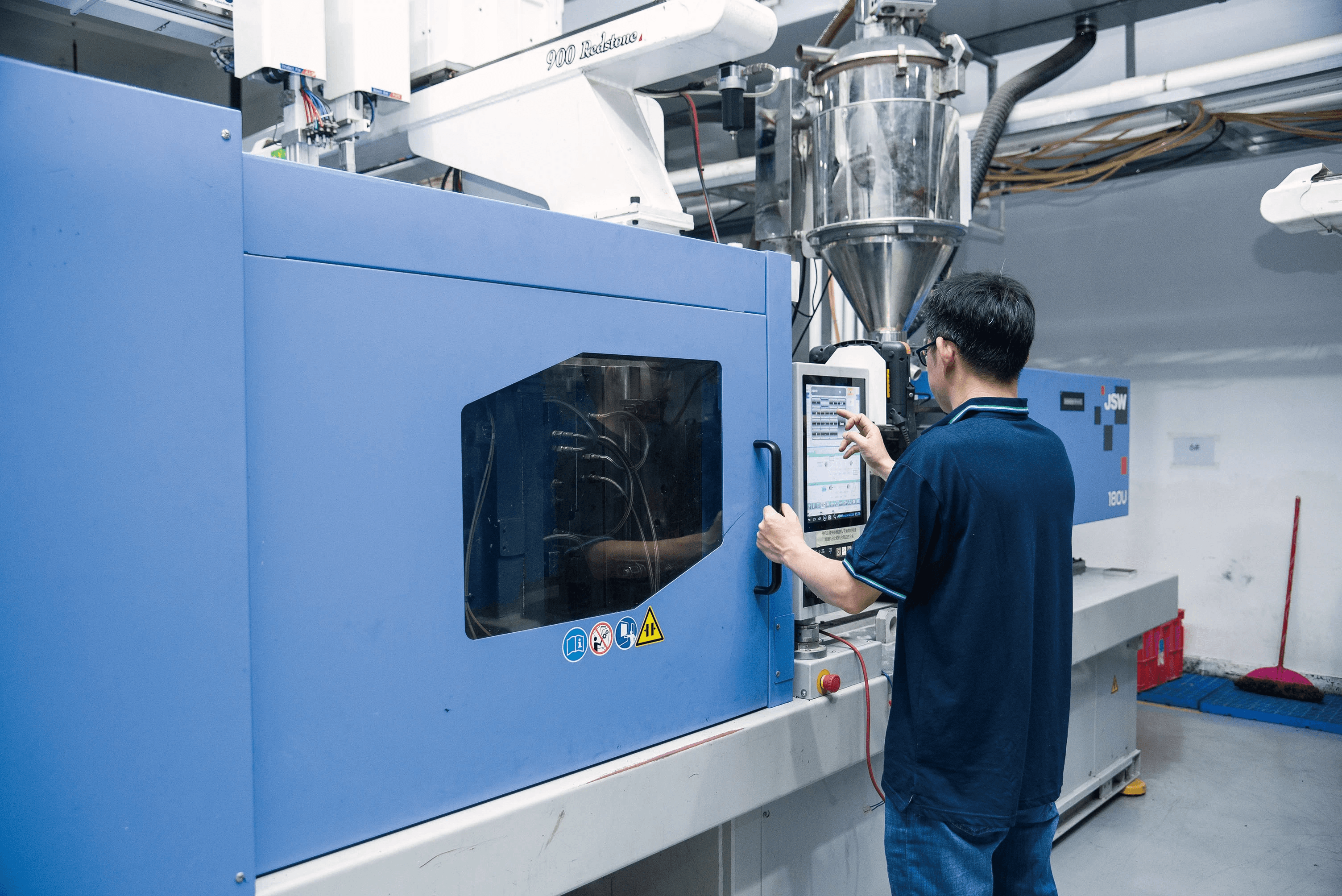
In the ever-evolving landscape of healthcare, medical device moulding stands as a crucial pillar supporting innovation and safety. Medical device moulding refers to the intricate processes involved in creating components that are vital for various medical applications, from simple syringes to complex surgical instruments. Understanding what is medical molding is essential for anyone interested in the intersection of technology and health.
Exploring the Basics of Medical Device Moulding
At its core, medical device moulding encompasses a variety of techniques used to manufacture devices that meet stringent industry standards. These methods ensure that products are not only functional but also safe for patient use. So, what are the three types of molding? Each technique—injection, blow, and compression moulding—offers unique advantages tailored to specific applications within the medical field.
The Importance of Moulding in Healthcare
The significance of moulding in healthcare cannot be overstated; it directly impacts patient outcomes and overall healthcare efficiency. High-quality medical device moulding ensures that devices perform reliably under pressure, which is critical during procedures where lives may depend on them. Furthermore, understanding what is molding in the pharmaceutical industry helps clarify how these processes contribute to drug delivery systems and other essential healthcare products.
Key Players in Medical Device Manufacturing
The landscape of medical device manufacturing features a diverse array of key players ranging from small startups to large multinational corporations. These entities collaborate with engineers and designers specializing in Medical Device Injection Molding to create innovative solutions tailored for their markets. As competition intensifies, companies focusing on Medical Injection Molding for Devices & Parts must prioritize quality and efficiency while navigating regulatory challenges.
What is Medical Moulding?
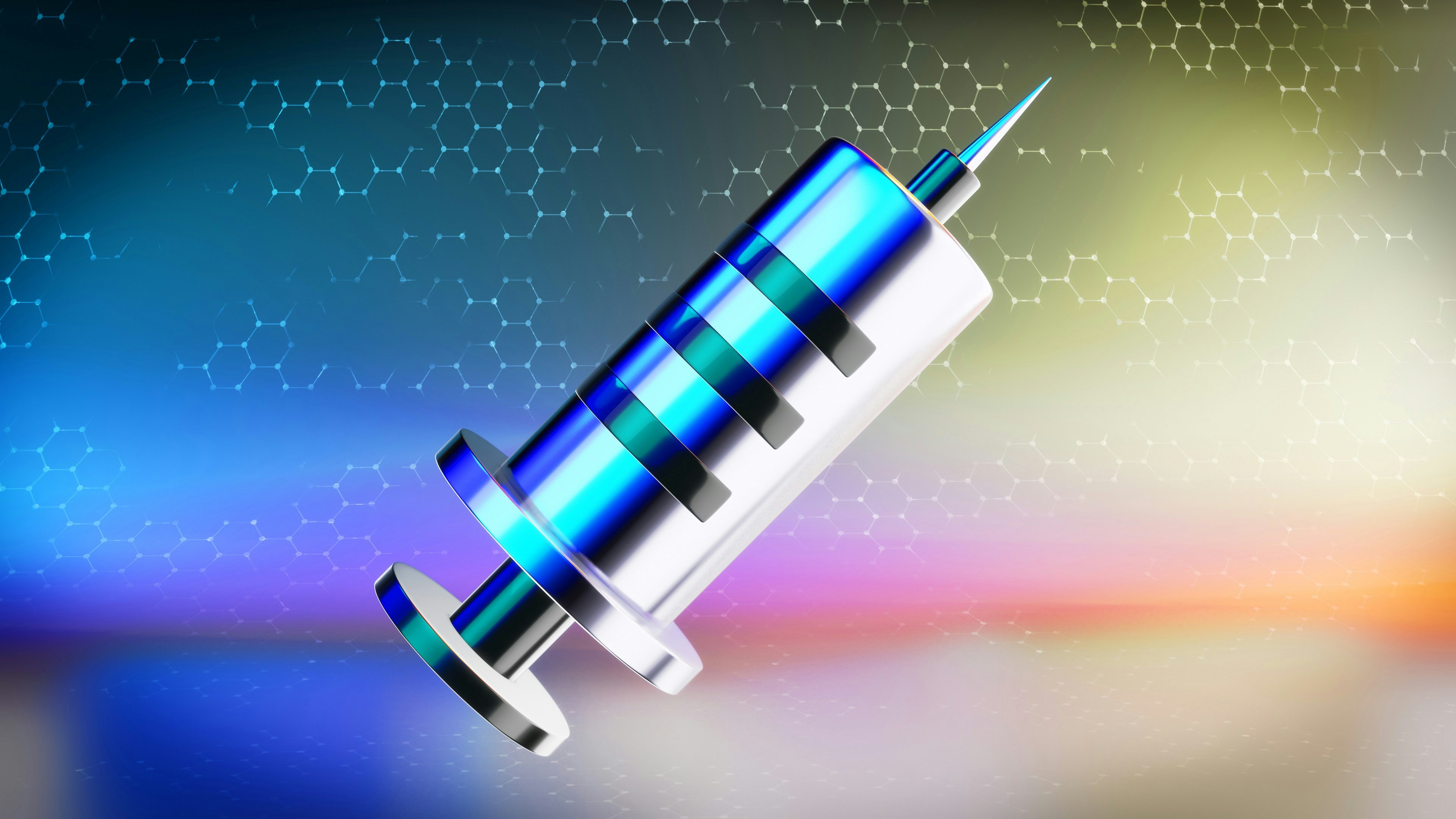
Medical moulding is a specialized process crucial for producing various medical devices and components that play a vital role in healthcare. This technique utilizes advanced manufacturing processes to create precise and reliable products that meet stringent regulatory standards. Understanding what medical moulding entails is essential for grasping its significance in the medical field.
Definition and Essential Concepts
At its core, medical moulding refers to the manufacturing process used to create plastic components specifically designed for medical devices. This involves shaping molten material into specific forms using molds, ensuring each product meets strict quality and safety standards. The essential concepts of medical device moulding include precision engineering, biocompatibility, and adherence to regulatory guidelines, which are fundamental in ensuring patient safety.
Historical Development of Medical Moulding
The evolution of medical moulding can be traced back to the early 20th century when plastic materials began to gain popularity in various industries, including healthcare. Initially limited in scope, the field has expanded significantly with advancements in technology and materials science that have allowed for more complex designs and applications. Today, we see a diverse array of devices produced through innovative techniques like Medical Device Injection Molding that cater to an ever-growing demand for high-quality healthcare solutions.
Applications in the Medical Field
Medical moulding finds applications across numerous sectors within healthcare, from surgical instruments to diagnostic equipment and drug delivery systems. Devices produced through this process include everything from syringes and catheters to intricate components found in imaging machines. With such a wide range of uses, understanding what is molding in the pharmaceutical industry becomes critical as it directly impacts patient care through improved device functionality and reliability.
What are the Three Types of Moulding?
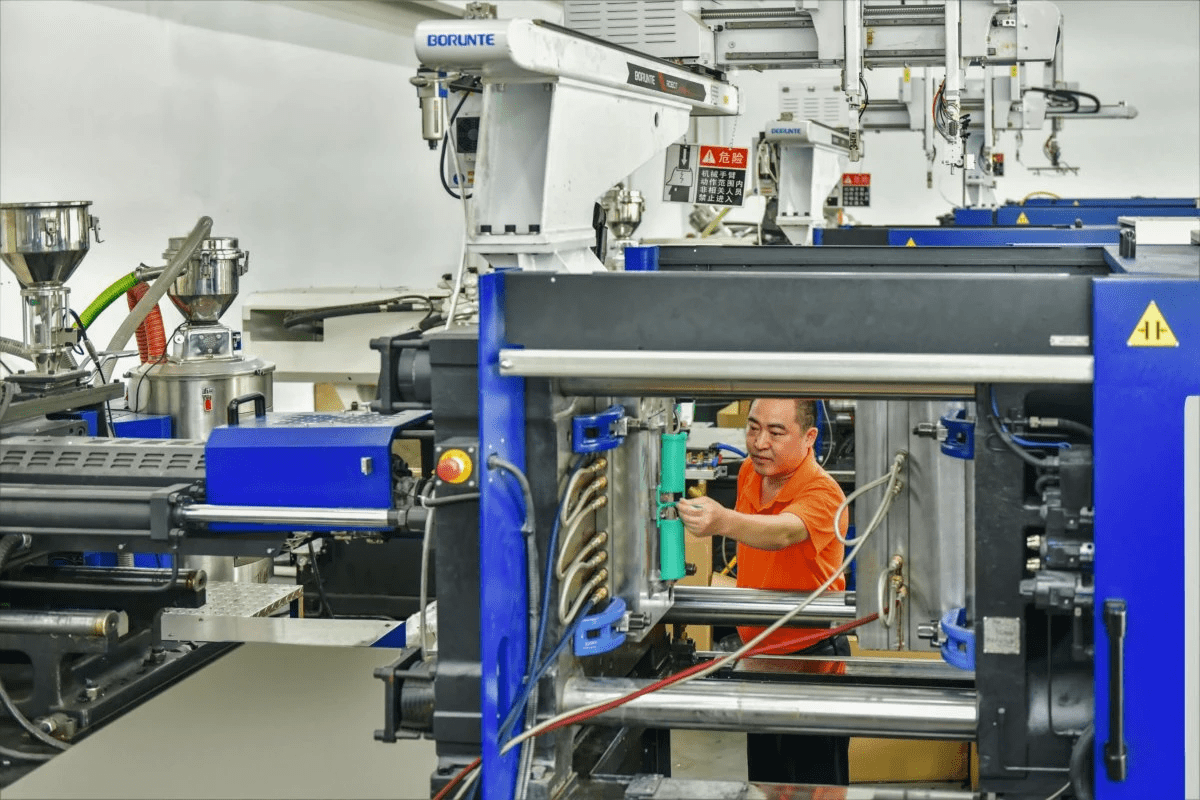
In the realm of medical device moulding, understanding the various types is crucial for manufacturers and healthcare providers alike. Each moulding technique offers unique advantages and applications that cater to different aspects of medical devices and their production processes. Here, we’ll delve into three primary moulding methods: injection moulding, blow moulding, and compression moulding.
Injection Moulding Overview
Injection moulding stands out as a dominant technique in medical device manufacturing due to its efficiency and precision. This process involves injecting molten plastic into a pre-designed mold, allowing for intricate designs that can meet stringent healthcare standards. With its ability to produce high volumes of uniform parts quickly, Medical Device Injection Molding is particularly beneficial for creating components like syringes, housings for electronic devices, and various surgical instruments.
The versatility of injection moulding also extends to the materials used; it accommodates a wide range of thermoplastics that are crucial in maintaining the integrity and safety of medical devices. As manufacturers explore what is medical molding? they often find that this method enables them to innovate while ensuring compliance with regulatory requirements. The precision offered by injection moulding not only enhances product quality but also reduces waste—an essential factor in today’s environmentally conscious market.
Blow Moulding Explained
Blow moulding serves a distinct purpose within the spectrum of medical device moulding techniques, primarily focused on creating hollow parts such as bottles or containers used in pharmaceutical applications. The process begins with heating a plastic tube (or parison) until it becomes pliable; then air is blown into it to expand into the desired shape within a mold. This method is especially useful for producing large-volume products like IV bags or drug delivery systems where maintaining sterility and functionality is paramount.
While blow moulding may not be as widely recognized as injection moulding in terms of versatility, its role cannot be understated when considering what are the three types of molding? It offers significant advantages in producing lightweight yet durable containers essential for pharmaceuticals. Furthermore, advancements in blow mould technology continue to enhance production efficiency while ensuring that quality standards are met across various applications.
Compression Moulding Insights
Compression moulding may not be as mainstream as its counterparts but holds significant importance within specific niches of the medical industry. This technique involves placing material directly into an open mold cavity before applying heat and pressure to form the desired shape—perfect for larger components or those requiring high-density materials such as silicone rubber used in prosthetics or seals for surgical instruments.
What is molding in the pharmaceutical industry? Compression moulded parts often play vital roles in drug delivery systems where precise dosages must be maintained without contamination risks. Its ability to produce robust components makes it an ideal choice when durability is critical; thus highlighting why understanding what are the three types of molding? can greatly influence material selection and manufacturing strategies.
What is Moulding in the Pharmaceutical Industry?
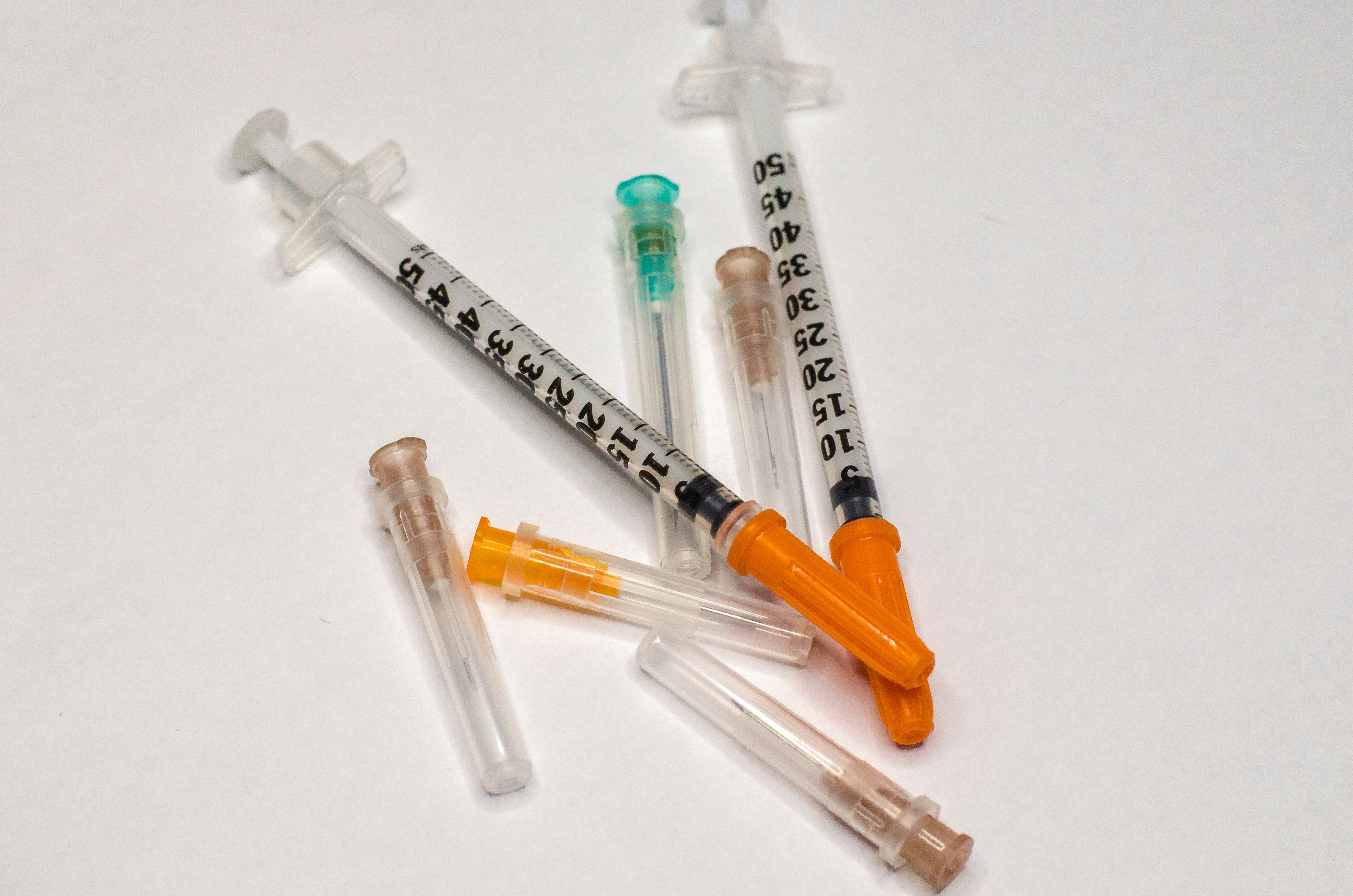
Moulding plays a crucial role in the pharmaceutical industry, particularly in the creation and delivery of medications. By utilizing advanced techniques like Medical Device Injection Molding, manufacturers can produce precise components that ensure effective drug delivery systems. This process not only enhances efficiency but also improves patient outcomes through reliable and consistent product performance.
Role of Moulding in Drug Delivery Systems
When it comes to drug delivery systems, moulding is indispensable. It allows for the production of intricate designs that facilitate controlled release and targeted action of medications within the body. Additionally, what is medical molding? It refers to the specialized processes used to create devices that are safe, effective, and tailored to meet specific therapeutic needs.
The integration of moulding techniques ensures that pharmaceutical devices can accommodate various forms of medication, from solids to liquids. This flexibility is vital in developing innovative solutions like inhalers or infusion pumps that require precision engineering. As we explore what are the three types of molding?, it becomes clear how each type contributes uniquely to enhancing drug delivery mechanisms.
Examples of Pharmaceutical Devices
Several examples illustrate how moulding has revolutionized pharmaceutical devices. For instance, prefilled syringes utilize Medical Injection Molding for Devices & Parts to ensure accuracy in dosage while maintaining sterility and safety for patients. Similarly, inhalers designed through advanced moulding techniques provide users with an efficient means of delivering asthma medications directly into their lungs.
Other notable examples include blister packs for tablets and capsules, which rely on blow moulding processes for secure packaging that protects against contamination while offering user-friendly access. These devices demonstrate how essential medical device moulding is in ensuring both efficacy and safety across various therapeutic applications. The diversity among these products showcases just how integral what is molding in the pharmaceutical industry? truly is.
Quality Standards in Pharmaceutical Moulding
Quality standards are paramount when it comes to pharmaceutical moulding due to the critical nature of healthcare products involved. Regulatory bodies such as the FDA set stringent guidelines ensuring all medical device moulding processes adhere to best practices for safety and effectiveness. This includes rigorous testing protocols throughout production stages—confirming not only functionality but also compliance with biocompatibility requirements.
Moreover, quality assurance measures extend beyond mere compliance; they foster innovation within Medical Device Injection Molding by encouraging manufacturers to adopt cutting-edge technologies and materials that enhance product performance further. By prioritizing quality standards in pharmaceutical moulding, companies can assure healthcare providers—and ultimately patients—that they receive reliable devices designed with their well-being at heart.
In conclusion, understanding what is molding in the pharmaceutical industry reveals its profound impact on drug delivery systems and overall patient care quality while emphasizing adherence to high standards throughout manufacturing processes.
Medical Device Injection Moulding
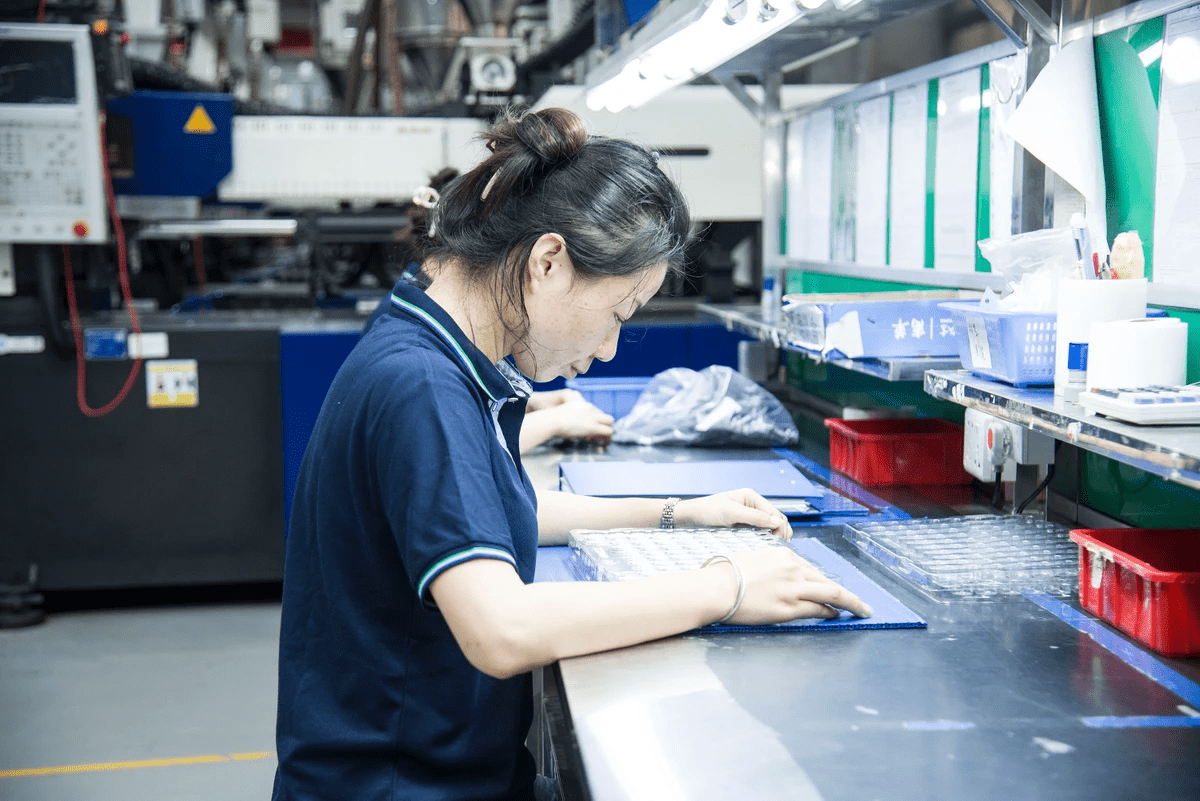
In the realm of medical device manufacturing, injection moulding stands out as a critical process. This technique allows for the mass production of complex components with high precision, making it indispensable in creating reliable medical devices. Understanding how this process works can illuminate its importance in the broader context of medical device moulding.
Process of Injection Moulding Explained
At its core, Medical Device Injection Molding involves injecting molten material into a pre-designed mold to create specific shapes and components. The process begins with heating plastic pellets until they melt and then injecting this material under pressure into a mold cavity where it cools and solidifies. This method ensures that each part produced is consistent in quality and dimension, which is crucial when considering what is medical molding?
The precision offered by injection moulding allows manufacturers to create intricate designs that are often required for modern medical devices. It also enables the use of various materials tailored to specific applications in healthcare, enhancing performance and safety standards. This versatility makes injection moulding a preferred choice among manufacturers when addressing what are the three types of molding?
Advantages for Medical Devices
Medical Device Injection Molding offers numerous advantages that make it particularly suitable for the healthcare sector. First and foremost, it provides exceptional accuracy and repeatability, ensuring that each component meets stringent regulatory requirements essential for patient safety. Additionally, this method supports high-volume production runs, allowing manufacturers to meet demand without sacrificing quality.
Another key advantage is the ability to use advanced materials that can withstand sterilization processes while maintaining their integrity over time—critical factors when considering what is molding in the pharmaceutical industry? Furthermore, innovations in injection moulding technology have led to faster cycle times and reduced waste, making it an environmentally friendly option as well.
Case Studies from Leading Firms
Several leading firms have successfully harnessed Medical Device Injection Molding to revolutionize their product lines. For instance, Company A developed an innovative drug delivery system using advanced injection-moulded components that improved patient compliance through user-friendly design features. Their case exemplifies how effective medical device moulding can lead to better health outcomes.
Similarly, Company B utilized injection moulding techniques to produce surgical instruments with enhanced ergonomic designs while ensuring each piece conformed precisely to regulatory standards—showcasing how critical this process is within the industry landscape today. These examples illustrate not only what is medical molding but also highlight its transformative impact on healthcare innovation.
Medical Injection Moulding for Devices & Parts
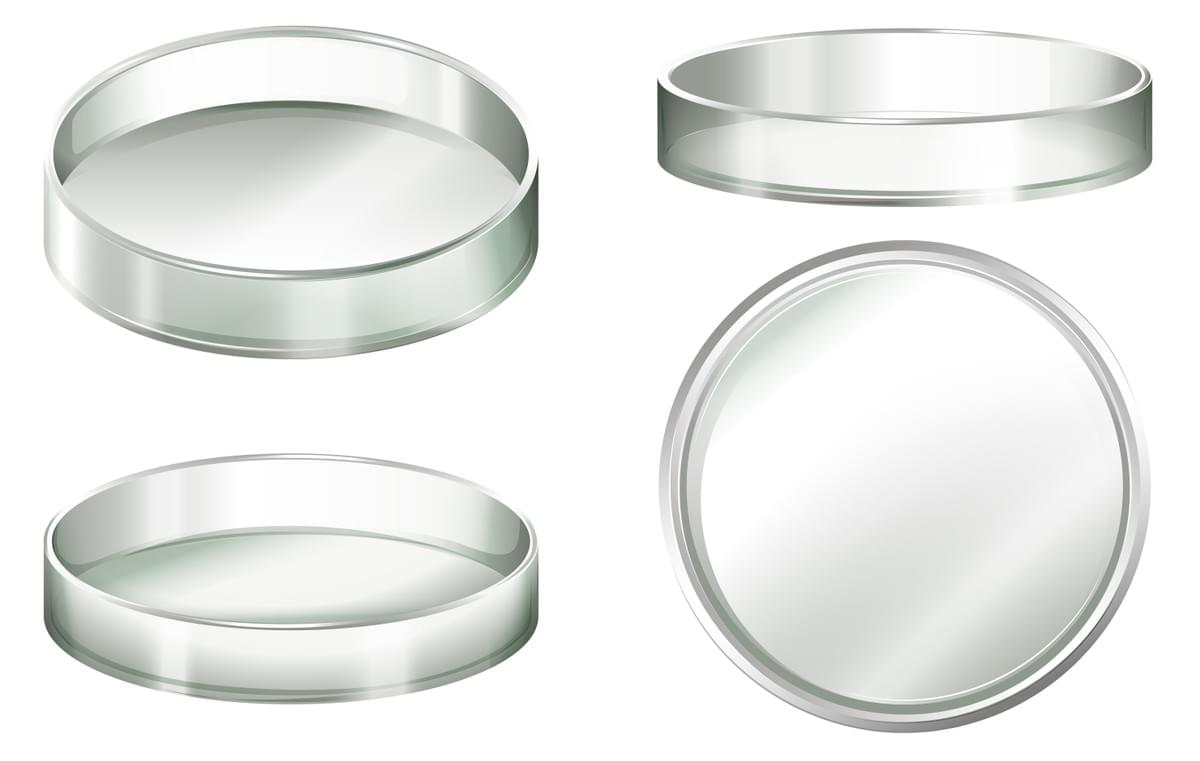
Medical injection moulding is a critical process in the production of various medical devices and parts, ensuring precision and reliability. This method allows manufacturers to create complex shapes and designs that meet stringent healthcare standards. With advancements in technology, medical device moulding continues to evolve, offering innovative solutions for the healthcare industry.
Materials Commonly Used
In medical device moulding, the choice of materials is paramount to ensure safety and efficacy. Commonly used materials include thermoplastics like polycarbonate, polypropylene, and polyethylene due to their durability and biocompatibility. Additionally, silicone rubber is favored for its flexibility and resistance to extreme temperatures, making it ideal for various applications in the pharmaceutical industry.
When considering what is medical molding?, it's essential to understand that these materials must comply with rigorous regulatory standards. They should not only be effective in their application but also safe for patient use. The right material selection can significantly influence the performance of devices produced through Medical Injection Moulding for Devices & Parts.
Design Considerations
Design considerations play a pivotal role when it comes to medical injection moulding processes. Factors such as ergonomics, functionality, and manufacturability must be taken into account during the design phase. When addressing what are the three types of molding?, it's important to note that each type may require different design approaches tailored to specific applications within the healthcare field.
Moreover, intricate designs often necessitate advanced tooling techniques that enhance precision while minimizing production costs. Designers must also consider ease of assembly and disassembly since many medical devices require regular maintenance or replacement parts over time. Ultimately, successful design integration leads to improved user experience and better patient outcomes.
Innovations in Injection Moulding
The landscape of Medical Device Injection Molding is continuously being reshaped by technological innovations aimed at improving efficiency and quality. Recent advances include 3D printing technologies that allow rapid prototyping before full-scale production begins—this helps streamline processes while reducing waste associated with traditional methods.
Furthermore, smart manufacturing techniques are being integrated into injection moulding operations—enabling real-time monitoring of production parameters which enhances quality control measures significantly. These innovations not only improve manufacturing capabilities but also contribute positively towards meeting what is molding in the pharmaceutical industry? by ensuring high-quality standards throughout production cycles.
Conclusion
In the ever-evolving world of healthcare, the significance of medical device moulding cannot be overstated. As we look to the future, advancements in technology and materials will continue to shape how we approach medical device manufacturing. The integration of innovative processes will not only enhance product quality but also improve patient outcomes.
The Future of Medical Device Moulding
The future of medical device moulding is poised for exciting developments, particularly with the advent of smart materials and 3D printing technologies. These innovations promise to revolutionize what is medical molding by enabling more complex designs and customized solutions tailored to individual patient needs. Moreover, as regulatory standards evolve, manufacturers will need to adapt their practices to ensure compliance while maintaining efficiency in production.
Best Practices for Quality Assurance
Quality assurance in medical device moulding is paramount; it’s not just about meeting standards but exceeding them. Implementing robust testing protocols at every stage— from design through production—ensures that all products are safe and effective. Additionally, fostering a culture of continuous improvement among teams can significantly enhance overall quality, ensuring that what are the three types of molding are applied effectively in every project.
How Baoyuan Enhances Medical Moulding Expertise
Baoyuan stands out as a leader in enhancing expertise within the realm of medical injection molding for devices & parts. Their commitment to innovation and quality assurance ensures that they stay ahead in a competitive market, providing clients with state-of-the-art solutions tailored specifically for their needs. By leveraging advanced technologies and skilled craftsmanship, Baoyuan exemplifies how dedication can elevate standards in medical device moulding.